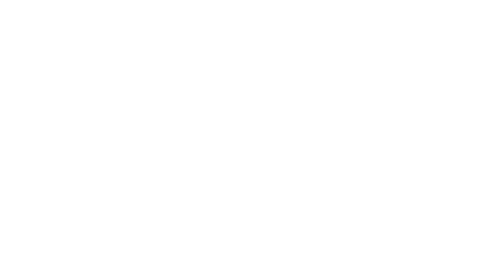
APS (Advanced Planning and Scheduling) – особенности и преимущества
- 09.11.2021
Планирование – основное звено в системе управления производством. От того, насколько оно будет точным, зависит эффективность работы предприятия, его финансовые показатели и положение на рынке. При этом планирование производства должно быть одновременно гибким по отношению к меняющимся потребностям рынка и адаптированным под реальные возможности конкретного производства.
APS-системы – это программное обеспечение для производственных предприятий, в основу которого заложена концепция усовершенствованного планирования. Оно позволяет осуществлять сквозное планирование от клиентского заказа до конкретных сменно-суточных заданий, синхронизируя производственные планы с мощностями, ресурсами, существующими ограничениями и сроками поставок.
APS выполняют две главные функции:
- Составление производственного плана. Это долгосрочное и среднесрочное планирование, основанное на удовлетворении внешних потребностей с учетом внутренних возможностей предприятия. Внешние потребности – это имеющиеся или прогнозируемые заказы. К внутренним возможностям относятся производственные мощности и ресурсы – люди, сырье и материалы. В результате формируются основной производственный план, план загрузки мощностей и график закупок.
- Диспетчеризация. Это функция оперативного планирования, цель которого – составление производственных графиков, расписаний и сменно-суточных заданий. При этом в планировании учитывается текущее положение дел в цехе, текущая доступность ресурсов и имеющиеся ограничения. Кроме этого, используется принцип оптимизации: построение графиков происходит таким образом, чтобы справиться с задачей с минимальными затратами и в максимально короткие сроки.
Особенности APS
Системы APS имеют ряд особенностей:
- Высокая скорость создания планов. В APS используются алгоритмы современной математики, позволяющие быстро проводить сложные расчеты. Поэтому планирование занимает несколько минут в отличие от транзакционных систем, в которых расчет плана может происходить в течение нескольких часов.
- Оперативная реакция на отклонения. В традиционных системах планирование происходит последовательно, в результате производство основывается на плане, который устарел из-за поступления новых заказов и других изменений. APS проводят расчеты одновременно и в реальном времени, создавая синхронизированные, оптимальные планы, основанные на оперативных данных. В любой момент планы можно актуализировать – внести изменения, соответствующие новым обстоятельствам.
- Точность и детализация. APS точно прогнозирует сроки и создает реалистичные планы, учитывающие множество критериев: пропускную способность, проблемные места, особенности технологического процесса, характеристики оборудования, заказы, распределенные по приоритетам, и т.д.
- Визуализация сложных процессов. В системах APS предусмотрены удобные инструменты для анализа и изменения планов: различные графики, отчеты, а также диаграмма Ганта, в которой наглядно отображаются все производственные процессы.
- Создание сценариев «что, если». Эта функция позволяет создавать альтернативные копии производственного плана, чтобы протестировать различные изменения. Таким образом можно определить, какой производственный график принесет наибольшую прибыль и будет иметь наименьшее количество просроченных заказов, стоит ли запускать дополнительное оборудование с точки зрения прибыли и эффективности и т.д.
Преимущества внедрения APS
Ключевое преимущество APS заключается в том, что внедрение системы позволяет производственным предприятиям выйти на качественно новый уровень:
- Автоматизировать планирование. Система генерирует максимально реалистичные планы без участия человека. Таким образом, планирование не требует значительных трудовых ресурсов и исключает негативное влияние человеческого фактора.
- Глобально оптимизировать производство. APS ищет оптимальные решения не для отдельных процессов и подпроцессов, а для всей производственной цепочки.
- Достигнуть максимальной прозрачности. Функциональность APS позволяет полностью контролировать производственный процесс и эффективно им управлять.
- Увеличить эффективность. APS помогает сократить время производственного цикла, увеличить пропускную способность, повысить производительность труда и эффективно использовать ресурсы.
- Снизить затраты. С помощью APS предприятие получает возможность снизить производственные расходы, сократить брак, запасы незавершенного производства и готовой продукции.
К российским разработкам этого класса систем для производственного планирования относится СНАРЯД | APS компании «Адептик». При создании программного обеспечения учитывались мировой опыт и особенности работы российских промышленных предприятий. В ПО применена собственная технология, основанная на передовых методах искусственного интеллекта. Одна из ее особенностей заключается в оптимизации обмена данными для увеличения надежности системы и повышения скорости работы. СНАРЯД | APS интегрируется с ERP или внедряется как отдельное решение, поскольку предусмотрена возможность заведения справочников.
Сегодня вряд ли найдется такой IT-ишник, которому при слове «планирование» не приходит на ум аббревиатура ERP, APS, MES. Хотя эти системы обладают разными функциональными возможностями и предназначены для решения задач планирования различного уровня, они могут не только прекрасно уживаться, но и дополнять друг друга. Иногда слышатся со стороны максималистов призывы повысить функциональность APS или MES до уровня ERP. Можно ли это сделать? В принципе, можно. Как можно раскормить кота до размеров кавказской сторожевой. Но кто тогда будет ловить мышей и охранять дом? …
В настоящее время, взамен устаревшим стандартам систем планирования классов MRP (Material Requirements Planning) и MRP-II (Manufacturing Resource Planning), пришли системы нового поколения – ERP (Enterprise resource planning), APS (Advanced Planning & Scheduling Systems) и MES (Manufacturing Execution Systems). Эти системные решения, апробированные за последние 15-20 лет на различных предприятиях машиностроительного комплекса, имеют различное назначение, функциональность и могут быть использованы как в отдельности, так и вместе.
Несмотря на имеющуюся полемику приверженцев различных платформ, указанных выше, надо отметить, что все они, несмотря на то, что имеют в своем составе функцию планирования на том или ином уровне детализации, могут являться отдельными частями общей системы – АСУП.
Вспомним, с чего же все началось…
История систем планирования
Древняя история
Идея планирования работ на предприятии, будь оно фабрикой, заводом или процессом возведения пирамиды, стара, как мир. Как только люди научились более-менее сносно обращаться с числами, сразу возникло желание подчинить себе с помощью этих чисел производственные процессы. Также давно люди поняли, что экстремальное значение – не всегда самое лучшее, поскольку ему в нашем мире всегда противостоят всевозможные ограничения. Комбинаторика в природе вещей, событий, была всегда. И всегда было желание убрать хаос, упорядочить работы во времени и этот порядок, пусть даже найденный эмпирическим путем, зафиксировать. Еще в начале 20-го века известный специалист по организации производства Генри Лоуренс Гантт впервые сформулировал, применительно к компании «Банкрофт», производящей хлопчатобумажные ткани, следующие три простых правила организации работы:
- Порядок, в котором должна выполняться работа, теперь определяется в офисе «белым воротничком», а не красильщиком.
- Точная запись лучшего метода крашения в любой оттенок хранится в офисе, соблюдается мастером и более не зависит от записной книжки красильщика или его памяти.
- Все красильщики и машинисты поощряются материально, когда следуют инструкциям или, наоборот, наказываются, когда они не делают этого.
Генри Л.Гантт (1861-1924)
И закрепил Г. Гантт этот порядок работ графически в известной диаграмме, которую теперь мы называем его именем. Начало было положено. Осталось только найти способ, как рассчитать ту оптимальную последовательность работ, которую нельзя нарушать. После внедрения указанных принципов организации производства на текстильной фабрике при значительном сокращении рабочего дня на 25-30% увеличился выход продукции, а заработная плата выросла на 20-60%. [1].
Новая история
«Новую» историю решения задач по оптимальному планированию в производстве принято исчислять от 1939 г. Именно тогда в издательстве Ленинградского университета вышла небольшая по объему книжка молодого профессора Л.В. Канторовича «Математические методы организации и планирования производства». Эта монография положила начало научным методам в планировании и организации производства на основе зарождающегося тогда направления экономической математики впоследствии оформившейся в математическое программирование.
Л.В.Канторович (1912-1986)
Не только «железный занавес» в какой-то мере помешал ознакомиться с этой работой зарубежным ученым, в частности, Дж. Б. Данцигу, который в 1947 г. пришел к аналогичным результатам идеи численного решения задач оптимизации, позже названного симплекс-методом.
Дж.Б.Данциг (1914-2005)
Причиной «невостребованности» служило отсутствие возможности реализации предложенных моделей и алгоритмов, т.к. ЭВМ еще не было и до появления первого прообраза языка программирования было еще долгих десять лет.
Появление первых вычислительных машин значительно стимулировало развитие работ в области математической экономики, организации и планирования производства. Были разработаны эффективный метод решения целочисленных задач (Р. Гомори), метод ветвей и границ (А. Лэнд, В. Дойг и Дж. Литтл), метод динамического программирования (Р. Беллман) и др. Все эти методы отыскания оптимума в окружающем нас комбинаторном мире находили применение в различных областях экономики и производства. Одна из таких прикладных областей математики под названием Теория расписаний как раз и «взялась» за решение многочисленного класса задач планирования работ на производстве.
Задача планирования технологических операций на станках, опубликованная С.М. Джонсоном в 1954 г., которая показала, что составление расписания уже для трех станков относится к классу задач, трудноразрешимых за приемлемое время (так называемый, класс NP-сложных задач) ничуть не обескуражила заводских специалистов первых отделов АСУ. Если первыми благами компьютеризации могли пользоваться только государственные структуры, перемалывая многомерные балансовые модели Леонтьева или составляя пятилетние планы, то с удешевлением вычислительной техники и появлением первых серийных ЭВМ появилась возможность решать задачи планирования на уровне предприятий и даже для цехов и отдельных участков. Предприятие считалось передовым, если оно разрабатывало собственную АСУП, если пыталось построить расписания работ для своего станочного парка с помощью систем оперативно-календарного планирования собственного же изготовления.
Развитие новых прикладных разделов математики и доступная вычислительная техника класса IBM 360/370, ЕС ЭВМ 1020 – 1060 сделали свое дело в 70-80-х годах – они явились катализатором появления первых АСУП и позволили хотя бы в каком-то приближении решать задачи избавления от хаоса комбинаторики «в мире станков и деталей» [2].
Новейшая история
Какие бы новые сюжеты обращения со временем не придумывали писатели-фантасты, оно, это время, бежит почти по экспоненциальной зависимости. За какие-то двадцать лет человечество «обогнало» закон Мура и взамен мэйнфреймам и доморощенным АСУП, на рынке IT теперь бродят новые «звери» зоопарка, который все также называется системы управления предприятиями и процессами. Основные разновидности этих систем, которые в настоящее время отвечают за составление планов работ на производстве – это системы классов ERP, MRPII, APS и MES. Если их предки – системы АСУП довольствовались возможностью составления объемно-календарных планов (реже – план-графиков работы оборудования), обсчетом финансовых перспектив на ближайшую пятилетку при стабильном спросе и расчетом заработной платы, то новые системы включают в себя все новые и новые функции автоматизации деятельности предприятий в условиях динамично развивающегося рынка товаров новейшего общества потребления. Но основной функцией, как и прежде, считается возможность составления плана работ. Именно эта функция, в конечном итоге, позволяет понять – кто, когда и что должен делать. Как же происходит планирование в этих системах и какая из них для каких случаев предназначена?
Планирование в ERP
Мы не будем подробно останавливаться на описании функциональных возможностей ERP-систем не только по причине того, что об этом написано достаточно много, сколько по причине того, что ERP-системы, по сути, не являются прямым инструментом планирования работ на предприятии. По прошествии десяти лет консультанты и пользователи наконец-то поверили в то, что ERP – это, прежде всего, корпоративная информационная система, система управления предприятием, своего рода кровеносная и нервная система промышленного организма, соединяющая островки логистики многочисленных органов, выполняющих определенные функции (документооборот, управление закупками, поставками, складскими запасами и пр.). О характере планирования работ, технологических операций на станки и другие единицы технологического оборудования в ERP-системах можно сказать одной фразой – планирование в большинстве систем ведется на основе старого стандарта MRPII [3] без учета текущей загрузки данного оборудования и состояния обработки изделий. Т.е. по сути, любой детальный ERP-план будет практически невыполнимым.
Рис.1. ERP: Формирование плана выпуска продукции (производственной программы)
Любое планирование на уровне ERP ограничивается лишь формированием объемного месячного (декадного) плана. Корректировать такие планы оперативно не удается, вот почему их реализация предполагает строгую исполнительскую дисциплину во всех вовлеченных в производственную цепочку подразделениях предприятия. Т.е. можно говорить об организации производства, контролируемого ERP, как производства с определенным запасом «устойчивости» по отношению к возникающим отклонениям от составленного объемного плана. Вся тяжесть при этом ложится на исполнителей: «как хочешь, но плановое задание к рассчитанному сроку выполни!» И, что особенно важно, ERP, выдав задание всем подразделениям, при возникновении потребности в корректировке планов, не в состоянии с этим справиться, т.к. любой пересчет даст ту же картину общего задания – задания в объемах, но не в детальных сроках по изделиям и операциям, что требуется для управления на уровне цехов.
Планирование в APS
С точки зрения точного планирования работ на предприятиях интерес представляют системы классов APS (Advanced Planning & Scheduling Systems) и MES (Manufacturing Execution Systems).
APS-системы, появившиеся на рынке в середине 90-х годов, являются уже непосредственным инструментом планирования работ на предприятии. Несмотря на однозначное обозначение, многие авторы и даже разработчики трактуют это название по-разному: «оптимизированное производственное планирование», «усовершенствованное планирование», «улучшенное планирование», «расширенное планирование», «оптимизированное и синхронное планирование», «точное планирование», «оперативное планирование» и даже «аккуратное планирование»!
Согласитесь, толкований столь много, что возникает вопрос – в чем, собственно, дело? По сравнению с чем расширенное, усовершенствованное, насколько точное, с чем синхронное, что оптимизируется и насколько оперативное?
Расширенное и усовершенствованное.
В начале 90-х годов после первых опытов внедрения ERP, осмысления преимуществ и недостатков планирования по стандарту MRPII предприятия столкнулись с основной проблемой – достоверность планирования. Достоверность и точность во времени. Динамика рынка, веяния концепции JIT потребовали от предприятий более точных сроков поставок, полноценного участия в управлении цепочкой поставок. Несовершенство методов планирования с помощью MRPII потребовали пересмотра «ценностей» – что важно при планировании? Скорость, противоречащая ей точность, и для чего нужны эти показатели? Выяснилось, что без решения задачи управления поставками, без возможности прогнозирования точных дат выпуска продукции предприятие представляет собой вещь в себе. Поэтому основной целью для систем планирования нового поколения – APS являлось решение задач автоматизации управления цепочками поставок (SCM – Supply Chain Management), причем этот функционал APS, реализуемый за счет возможности планирования всех работ во времени с учетом загрузки мощностей, имеет двойное назначение – он реализуется как для предприятия, выступающего объектом всей цепочки на динамичном рынке товаров, так и для объектов самого предприятия – цехов, участков и подразделений. Таким образом, возможности планирования в APS расширены и усовершенствованы относительно стандарта MRPII.
Синхронность.
Понятие синхронности нужно понимать в APS, с одной стороны, как возможность планирования материалов, ресурсов и одновременно построение расписания с учетом реальной загрузки оборудования во времени. С другой стороны, синхронность выражается еще и в том, что расписания строятся для всех подразделений предприятия, с учетом сроков поставок партнеров и расписания для всех этих производственных структур являются всегда взаимоувязанными во времени, поскольку они получаются из общего расписания работы всего предприятия.
Оперативность.
Оперативность для APS – это возможность за кратчайшее время определить по тому или иному заказу срок его изготовления. Оперативность в плане диспетчерского контроля и оперативного пересчета расписаний к APS, как правило, никакого отношения не имеет, поскольку, если не меняются внешние ограничения (нарушение сроков поставок со стороны партнеров, другие непредвиденные задержки) и в портфель заказов каждые пять минут не вносится новое изделие, то пересчет расписаний ничего не даст. Учет же внутренних возмущений со стороны многочисленных подразделений (поломки оборудования, брак на операциях и т.п.) может привести у существенному утяжелению контура диспетчирования при существующей размерности задачи.
Точность и оптимизация.
Точность и оптимальность формируемых расписаний – прерогатива алгоритмов любой системы планирования.
По сравнению с алгоритмами MRPII, алгоритмы APS при составлении расписаний одновременно учитывают как потребности материалов, так и мощности предприятия с учетом их текущей и спланированной загрузки. В алгоритмах APS учитываются переналадки и некоторые другие параметры технологической среды, которые пессимисты почему-то называют «ограничениями».
В адрес алгоритмов APS встречается немало заслуженных эпитетов, но в ряде случаев в порыве восторга этим системам приписываются особенности, которые ставят в тупик даже специалистов. В частности, говорится, что в основе алгоритмов APS-систем лежат имитационные модели, нейросетевые модели, планирование на основе базы знаний, модные ныне эвристические методы типа генетических алгоритмов, моделирования отжига и даже линейное программирование (!).
Рис.2. APS: Расчет укрупненного расписания работ для производственных подразделений.
На самом деле алгоритм построения расписаний в APS достаточно прост [4]. Есть множество операций для всего множества выпускаемых изделий, множество станков и на каждые изделия есть ограничения – по срокам выпуска, по наличию материала и т.п. Ограничения разделяются на важные и не очень. Вначале, на первом проходе алгоритма составляется расписание с учетом выполнимости важных ограничений, например, отсутствие нарушение сроков поставок. Если расписание получено, то оно считается допустимым и принимается в качестве базового для дальнейшей «оптимизации» – на последующих проходах алгоритма проводится попытка учесть оставшиеся менее важные ограничения. На самом деле это не оптимизация. Это не что иное, как итерационный процесс получения допустимого расписания с учетом новых ограничений, вносимых на новой итерации, т.е. весьма несложная эвристика. В ряде случаев процесс планирования упрощают еще сильнее – сначала планируют одну деталь, потом другую, до тех пор, пока все множество деталей не будет спланировано. Оценка полученных расписаний относительно действительного оптимума при этом может быть достаточно низкой, но надо отметить, что если мы составляем расписание для нескольких тысяч единиц оборудования из сотен тысяч операций на месяц или полгода, то с этим фактом можно смириться. Особенно если учесть, что на последующем этапе за фактическую реализацию производственного расписания будут отвечать MES-системы. Таким образом, упростив алгоритм построения расписания, разработчики APS дали возможность в пределах существующих вычислительных мощностей получать допустимые расписания и более-менее точно прогнозировать сроки поставок. При этом APS-системы не ставят себе более сложных задач вроде минимизации в построенных расписаниях времен переналадок, транспортных операций, уменьшения количества задействованного оборудования и т.п., поскольку учет этих требований неминуемо приведет к утяжелению алгоритмов и невозможности за кратчайшее время получать расписания для больших размерностей. В связи с этим APS-системы имеют на своем вооружении крайне ограниченный состав критериев планирования. Надо отметить, что и эта существующая возможность получения хотя бы допустимых расписаний (в пределах получаса) не зря появилась в середине 90-х годов. Увеличение производительности вычислительных машин с одновременным снижением их стоимости, в очередной раз, явилось катализатором прогресса в области управления производством.
Другие особенности.
Хотя и говорится, что APS может перепланировать, но во-первых контур диспетчирования есть не у всех APS-систем, во-вторых, частота перепланирования в APS обусловлена частотой появления новых заказов (обратная связь в режиме реального времени для APS считается избыточной), в отличии от MES, которые делают эту операцию гораздо чаще (для задачи значительно меньшей размерности, корректируя планы лишь отдельных цехов), поскольку реагируют на любое изменение хода технологического процесса. Постоянные коррекции планов производства – это типичное явлений для производств мелкосерийного и единичного типов; их часто именуют в литературе «позаказными». Заметим, что для создания более точного контура обратной связи с «позаказным» производством поставщики APS-систем в некоторых случаях используют интеграцию с MES-системами.
Горизонт планирования в APS редко указывают однозначным – смена, неделя, месяц, до полугода. Но как бы ни гадали относительно «средней величины» горизонта планирования, для APS-систем он определяется предельно просто, – исходя из основной задачи, функционала системы, которым является управление цепочками поставок. Длительность горизонта планирования в APS-системах – это всегда разница во времени между моментами выдачи наиболее дальних заказов из всего портфеля заказов предприятия и текущей датой, поскольку при появлении нового заказа и соответствующем пересчете всего расписания, надо определить не только сроки его изготовления, но и возможность ненарушения сроков выполнения уже запущенных заказов.
Итак, именно эти новые возможности, обусловленные необходимостью управления цепочками поставок, явились причиной того, что темпы роста APS-систем стали значительно опережать темпы роста решений в сегменте ERP. Наряду с зарубежными системами (Berclain, Chesapeake Decision Sciences, CSC, Fygir, i2 Technologies, Manugistics, Numetrix, Optimax, Ortems, Preactor, Pritsker, Paragon Management Systems, ProMIRA, Red Pepper Software, Thru-Put Technologies и др.) в последние годы стали появляться и отечественные продукты (infor:APS, Adexa eGPS и др.). Опасения в том, что APS вырастут до новых ERP были, пожалуй, только у журналистов, поскольку изначально было ясно, что APS-системы не отвечают за финансы, закупки, документооборот и другие транзакционные функции ERP, но ведущие производители ERP-систем (People Soft, SAP, Oracle, SSA Global, JD Edwards, Marcam и др.) среагировали достаточно быстро и отметились в желании совместного использования своих решений с продуктами APS. Постепенно это сотрудничество переросло в естественную потребность интеграции на уровне ядра планирования ERP, которое может быть заменено APS-системой. В то же время APS может поставляться как отдельный продукт.
Укрупненная схема взаимодействия ERP и APS приведена на рис. 3.
Рис.3. Укрупненная схема взаимодействия ERP и APS.
Пример производственной программы с сроками запуска-выпуска изделий.
Организующим элементом на приведенной схеме является ERP-система, исполняющая роль как учетно-информационной системы, так и системы управления. В ее задачи входит формирование портфеля заказов из востребованной рынком продукции.
Необходимым этапом при формировании портфеля заказов является оценка возможности выполнения того или иного заказа, обладающего такими свойствами, как стоимость, сроки изготовления, объемы, параметры качества, соответствие требуемым техническим условиям и пр. Данная оценка проводится как с помощью несложных логистических инструментов, позволяющих определить возможность выполнения заказа с точки зрения существующего на предприятии уровня технологии (или – технологического уклада), возможности приобретения материалов и комплектующих, так и силами APS-систем, задача которых – определить возможность выполнения заказа во времени с учетом занятости производственных мощностей. При этом составляется расписание работ, необходимых для изготовления анализируемой продукции, для различных цехов предприятия. Расписание для вновь поступающей в портфель заказов продукции составляется с учетом того, что для ранее запланированных к производству заказов не пересматриваются моменты запуска и выпуска, т.е. при планировании используются либо существующие резервы времени, либо планирование изготовления предполагается на момент освобождения требуемых ОЦ от ранее запущенных в производство заказов. Если полученные в результате планирования предполагаемые сроки изготовления устраивают заказчика, то данная продукция поступает в портфель заказов, а затем включается в производственную программу. В противном случае рассматриваемая продукция не может быть принята в состав портфеля заказов.
В итоге соответствующие производственные подразделения получают от APS-системы в качестве плана определенный объем продукции, которую надо изготовить в указанные сроки. APS-система составляет планы, как правило, в момент поступления нового заказа. План по выпуску принятого к производству изделия спускается в те цехи, в которых должны быть изготовлены те или иные детали и сборочные единицы (ДСЕ) данного изделия.
В результате тандем ERP+APS позволяет сформировать не только производственную программу (план выпуска продукции), но и построить укрупненное расписание работ для всего предприятия. За счет более точного пооперационного планирования, т.е. расчета производственного расписания, APS, опираясь на информацию о состоянии поставок, запасов и наличия производственных мощностей, уточняет плановые сроки запуска-выпуска изделий. Возникающие рассогласования этих сроков с требованиями текущей производственной программы приводит к необходимости коррекции плановых сроков на уровне ERP.
Планирование в MES
Говорят, что MES-системы появились более 30 лет назад. К сожалению, авторы статьи, общий стаж работы которых в области планирования и автоматизации производства составляет 45 лет, еще двадцать лет назад не встречали в литературе эту аббревиатуру. Как бы то ни было, с MES-системами все более-менее предельно ясно, кроме одного – их постоянно путают с APS-системами. Чтобы разобраться, что же такое на самом деле MES-системы, еще раз взглянем на регламентированный состав функций MES, число которых ровно одиннадцать (www.mesa.org, www.mesa.ru, www.mesforum.ru):
- Контроль состояния и распределение ресурсов (RAS).
- Оперативное/Детальное планирование (ODS).
- Диспетчеризация производства (DPU).
- Управление документами (DOC).
- Сбор и хранение данных (DCA).
- Управление персоналом (LM).
- Управление качеством продукции (QM).
- Управление производственными процессами (PM).
- Управление техобслуживанием и ремонтом (MM).
- Отслеживание истории продукта (PTG).
- Анализ производительности (PA).
Как мы видим, в данном списке нет функции SCM, которая является главной в APS-системах. Несмотря на кажущееся, на первый взгляд, многообразие функций MES, надо понимать, что все эти функции имеют оперативный характер и регламентируют соответствующие требования не к предприятию в целом, а к той его единице (цеху, участку, подразделению), для которой ведется планирование работ. При этом надо также понимать, что такие функции, как управление документами, персоналом – это управление цеховыми документами (наряд-заказами, отчетными ведомостями и пр.) и персоналом цеха. Основными функциями MES-систем из перечисленных выше являются – оперативно-календарное планирование (детальное планирование) и диспетчеризация производственных процессов в цеху. Именно эти две функции определяют MES-систему как систему оперативного характера, нацеленную на формирование расписаний работы оборудования и оперативное управление производственными процессами в цеху.
MES-система получает объем работ, который либо представлен ERP на этапе объемно-календарного планирования, либо выдается APS-системой в виде допустимого для предприятия план-графика работы цеха, и в дальнейшем сама не только строит более точные расписания для оборудования, но и в оперативном режиме отслеживает их выполнение. В этом смысле цель MES-системы – не только выполнить заданный объем с указанными сроками выполнения тех или иных заказов, но выполнить как можно лучше с точки зрения экономических показателей цеха. Мы уже говорили, что APS-системы формируют некие исходные расписания работы первой степени приближения еще до начала реализации производственных планов. При этом ввиду большой размерности задачи, не учитываются многие технологические и организационные факторы. MES‑система уже на этапе выполнения, получая такой предварительный план, оптимизирует его по ряду критериев. При этом после оптимизации и построения нового план-графика работы цеха, очень часто, за счет уплотнения работы оборудования, отыскиваются дополнительные резервы, появляется возможность в рамках планируемого периода выполнить дополнительные заказы. Тем самым достигается эффект увеличения пропускной способности производственных структур.
В отличие от APS-систем, MES-системы оперируют меньшими размерностями назначения – до 200 станков и 10000 операций на горизонте планирования, который обычно составляет не более трех-десяти смен. Уменьшение размерности связано с тем, что в MES учитывается гораздо большее количество ограничений технологического характера. Еще одним отличием является то, что MES-системы обычно оперируют не одним или двумя критериями построения расписания, а зачастую несколькими десятками, что дает возможность диспетчеру цеха строить расписание с учетом различных производственных ситуаций. И только MES-системы оперируют так называемыми векторными, интегральными критериями построения расписаний, когда в один критерий собираются несколько частных критериев. При этом диспетчер, составляя расписание, может указать, что он хочет видеть в конкретном расписании – уменьшение календарной длительности выполнения всего задания, уменьшение длительности операций переналадок, высвобождение станков, имеющих небольшую загрузку и т.п. Оперативность составления и пересчета расписания является также прерогативой MES, поскольку пересчет может вестись с дискретой в одну минуту. Это не означает, конечно же, что каждую минуту рабочему будут выдаваться новые задания, но это означает, что все процессы в цеху контролируются в режиме real time и это позволяет заранее предвидеть все возможные нарушения расписаний и вовремя принимать соответствующие меры.
Рис.4. MES: Расчет детальных производственных расписаний на уровне цеха..
Алгоритмы MES-систем, хотя и базируются, в большинстве случаев, на эвристике, но, как правило, значительно сложнее и «умнее» алгоритмов APS. Вначале алгоритм MES находит допустимое решение с учетом всех ограничений и выбранного критерия (частного или интегрального). В дальнейшем, на этапе оптимизации, происходит поиск лучшего расписания. Конечно, полученное расписание также не является оптимальным в полном смысле слова, поскольку поиск оптимум в таких задачах всегда сопровождается со значительными временными затратами (MES-системы строят расписания за 0.1 – 5 минут на современной технике), но полученные при этом расписания, как правило, уже намного ближе к оптимуму, нежели расписания, построенные APS-системами.
В ряде случаев MES-системы могут составлять расписания не только для станков, но также для транспортных средств, бригад наладчиков и других обслуживающих устройств. Не по силу каким-либо другим системам такие особенности планирования, как формирование технологических сборов, планирование выпуска изделий с параллельным планированием изготовления требуемого комплекта оснастки (приспособлений, уникального инструмента).
Важным свойством MES-систем является выполнимость расписаний. Встроенные в планирующий контур ERP, APS-системы составляют производственные расписания только в случае внесения в портфель заказов новых изделий или работ, корректировать их в режиме реального времени крайне сложно, что приводит к серьезным проблемам использования APS-систем в мелкосерийном производстве. MES-системы в таких случаях работают более гибко и оперативно, пересчитывая и корректируя расписания при любых отклонениях производственных процессов, что повышает гибкость и динамичность производства. Если расписания APS-системы больше подходят для производств с крупносерийным характером выпуска продукции, где резких отклонений от производственной программы, как правило, не бывает (устойчивый характер производства), то MES-системы являются незаменимыми в мелкосерийном и позаказном производстве. При этом, если для APS-систем цех с большим объемом технологической и оперативной информации является в какой-то мере «черным ящиком», то MES-системы при выполнении заданий опираются на принцип расчета и коррекции производственных расписаний по фактическому состоянию производства. Эти системы достаточно чутко реагируют на отклонения во времени выполнения технологических операций, на непредвиденный выход из строя оборудования, на появление брака в процессе обработки изделий и другие возмущения внутреннего характера.
В отличие от систем классов ERP и APS, MES-системы являются предметно ориентированными – для машиностроения, деревообработки, полиграфии и пр. Поэтому они максимально полно отражают особенности технологии конкретных производственных процессов и зачастую включают в себя развитые средства поддержки технологической подготовки того или иного типа производства. Очень часто MES-системы имеют средства интеграции с системами САПР ТП/АСТПП.
На рис.5 представлена схема процедуры планирования производственных процессов, включающая в себя кроме MES-системы, еще и системы уровня SCADA (Supervisory Control And Data Acquisition), или в традиционной аббревиатуре АСУТП – автоматизированные системы управления технологическими процессами.
Как мы говорили выше, точность расписания напрямую зависит от длительности горизонта планирования и количества рабочих мест, на которых составляется это расписание. Если директивные расписания от APS-системы могут поступать раз в неделю (при поступлении нового заказа), то для цеха актуально расписание на текущую смену или сутки. Каждый такой оперативный интервал времени характеризуется своими особенностями, как уже говорилось выше – комплектация обслуживающего персонала, временные неполадки оборудования и пр., т.е. каждый цех на текущий момент времени характеризуется собственными производственным условиями, которые могут препятствовать строгому выполнению расписания, выданного APS-системой. Например, при временном дефиците наладчиков оборудования, расписание для того или иного цеха целесообразно построить по критерию минимума количества времени, затрачиваемого на переналадку. При дефиците транспортных средств, — по критерию минимума времени, затрачиваемого на транспортные операции.
Поэтому поступившие от APS-системы в тот или иной цех задания пересматриваются MES-системой. Задача MES-системы – коррекция нового план-графика работы оборудования в соответствии с частными условиями цеха. MES-система на оперативном интервале времени корректирует расписание работ, полученное от APS, с учетом того критерия, который является наиболее актуальным для данного цеха в текущий момент времени. При этом моменты выпуска вновь поступивших в обработку ДСЕ, определенные ранее APS-системой, для MES-системы являются директивными. Можно выпустить эти ДСЕ раньше, пересмотрев расписание цеха, но нельзя выпускать позже срока, рассчитанного APS-системой. Причина этого директивного начала со стороны APS кроется в том, что сроки сдачи, рассчитанные APS, согласованы с заказчиком и, в ряде случаев, присутствуют в договоре. Нарушение этих сроков выпуска может повлечь нарушение внешних, по отношению к предприятию, сроков поставок продукции со стороны заказчика, т.е. может нарушиться временная составляющая цепочки поставок. Для предприятия это может обернуться штрафными санкциями. Кроме ограничений временного характера APS-система может сформулировать (на основании построенного расписания) и ограничения стоимостного характера – могут присутствовать ограничения на общую стоимость выполнения расписания по изготовлению планируемых заказов.
В результате коррекции производственного расписания в MES формируются подробные сменно-суточные задания на рабочие места (ОЦ), а также составляются для всех ДСЕ оперативные маршрутные карты с указанием сроков начала и завершения каждой технологической операции с ее привязкой к конкретному инвентарному номеру станка.
Рис.5. MES: Схема процедуры планирования производственных процессов, включая SCADA.
Пример сменно-суточного задания на рабочее место.
Итак, MES-система в контуре планирования АСУП составляет расписание для цеха или производственного участка на оперативном горизонте планирования исходя из ограничений внешнего и внутреннего характера по критерию, который наиболее полно отражает особенности цеха в текущий момент времени. К задачам MES-систем можно отнести не только единовременное составление расписания работы оборудования в течение краткосрочного горизонта планирования, но также постоянную его коррекцию во времени. В случае выхода из строя какого-либо ОЦ или другого объекта, участвующего в ходе технологического процесса, MES-система оценивает, в зависимости от времени восстановления отказавшей единицы оборудования и директивных сроков сдачи ДСЕ, как возможность сдвига по времени выполнения зависимых ДСЕ (при наличии резервов времени), так и пересчета как всего расписания, так и его части. Таким образом, MES-система обеспечивает наличия контура автоматического регулирования функции производства с учетом динамически меняющихся частных производственных условий производственных подразделений.
Необходимости внеплановой остановки оборудования не всегда связана с сообщениями операторов или наладчиков, получающих визуальную информацию общего характера. В ряде случаев брак изготовления или состояние оборудования не диагностируемы визуально, поэтому с целью сбора, анализа информации о качестве технологических процессов в общем контуре планирования АСУП должны использоваться SCADA-системы. Задача этих аппаратно-программных комплексов – сбор и информации о ходе технологического процесса (ТП) в реальном режиме времени, аварийное оповещение в случае выхода параметров ТП за пределы допустимых значений и поломки оборудования, а также – формирование журнала событий и связь с MES-системой. Таким образом, через взаимодействие систем MES и SCADA обеспечивается контроль качества протекания ТП и в дальнейшем – своевременное принятие решение об остановке оборудования, пересчете расписания.
Строгая функциональность систем, «устойчивость» реализуемых производственных планов и расписаний
Время на прочтение
8 мин
Количество просмотров 11K
Особенности коммерческих APS-алгоритмов
Питеркин С.В.
«Продвинутые» коммерческие APS состоят, как правило, из 2 частей. Первую условно можно назвать APS–synchronizer’ы, их задача – рассчитать (синхронизированные и оптимизированные) планы по всему «дереву» изделия (далее – СИ — Состав Изделия) или заказа, и/или для всего производства-снабжения-цепочки поставок. Вторая — APS-scheduler’ы, задача которых – оптимизация по какому-либо критерию прохождения производственных, несвязанных между собой заданий через группу оборудования. Первые, как правило, при планировании рассматривают все ресурсы (материалы, производственные ресурсы,…), вторые, как правило (есть исключения), – только производственные. APS-scheduler’ы под разными названиями выступают в качестве «планировщиков» в MES-системах.
APS–synchronizer, «классический» подход
Что есть сущность APS-synchronizer’ов? Это – могучие «калькуляторы», которые могут, с теми или иными допущениями, быстро составить детализированный и точный (на момент расчета!) производственный план. Во многих случаях — и с элементами оптимизации по различным критериям. В этом — их большой плюс и возможность их легкой продажи: «вот она, та самая волшебная кнопка, которая будет мне считать реальный (реально выполнимый) план»! Но будет ли?..
Возьмем очередные плюсы APS: не планирует в прошлое, планирует с учетом загрузки ресурсов (люди, машины, инструменты, …), каждый раз создает реально выполнимый план, и т.п.
А теперь «темная сторона силы». И прежде всего: да, планирует, но какой ценой? Цена:
- наличие точного пооперационного техпроцесса и точная ресурсная (люди, машины, …);
- организация точного и оперативного учета (точность – не хуже, чем «до смены»);
- мощная аппаратная платформа;
- цена (деньги и трудозатраты на администрирование)…
- работающая «взрослая» (на базе MRP-II) общая система/методология планирования (SOP -> MPS (DP)-> “MRP”(APS) -> “Scheduler”)
На последнее условие у нас редко кто обращает внимание (а вообще-то, мало кто даже и подозревает, что нет «в природе» «производственного планирования», состоящего из одного (супер) плана… А это условие – определяющее и: не-решение задач планирования верхних уровней ведет к GIGO (Garbage-In-Garbage-Out).
Далее. Недостатки алгоритма при использовании в реальных условиях:
- при несоблюдении п.1 выше — неточный план, не попадающий в «окно запуска» — рабочие стоят…
- при несоблюдении п.2 выше — план сдвигается вправо. И так — каждый день…
- многономенклатурное производство сложной продукции и проблемы по п.3. выше – большое время отклика системы.
п5 – опускаем: прежде чем бегать, надо научиться ходить…
Плюс, еще интересные APS особенности:
- избыточная сложность и «тяжесть» алгоритмов, многократный overkill для большинства прикладных «наших» производственных задач, и при этом, почти полная невозможность решить следующие, «маловажные» задачи;
- «заточенность» APS на западную индустриальную модель, модель абсолютно зрелого и абсолютно рыночного завода, и «западной» размерности;
- невозможность APS жестко резервировать запасы и производственные задания (ожидаемые приходы) за каким-либо головным заказом. При каждом перепланировании APS будет «отнимать» резервы как мощности, так и запасов под заказы, ставшие более приоритетными. Отсюда – чрезвычайно «нервный», постоянно меняющийся план. Более того, в сложном машиностроении/приборостроении, в производстве любят (и это действительно надо, почему – отдельный разговор) жестко резервировать запасы НзП и материалов под конкретные головные изделия (под серийный номер выпускаемой «машины»). Но APS про это не хочет ничего знать;
- несмотря на то, что большинство дискретных APS — позаказные, при каждом перепланировании они «забывают» про планы прошлого заказа, и строят новый. В жестком позаказном производстве, где нужны жесткие связки заказа от головного изделия до материала это неприменимо;
- APS строят Мега-точные и оптимизированные планы. Каждый раз – новые. Каждый раз – с «крайней», сдвинутой вправо новой датой выполнения заказа. И если еще ничего не запущено, даже будут показывать отклонения первоначального плана от нового. Но, если многое уже запущено, т.е. есть производственные задания, и среди них есть отстающие, APS почти никак на это не среагирует – даст сигнал запустить новое или сдвинет всю сеть заказа. Не показав, какие и на сколько ПЗ отстают. Для наших «традиционно-ориентированных» и даже уходящих от «традиционности» производств, имеющих склонность выполнять заказ под конец периода это неприемлемо;
- есть и еще особенности, например: крайне трудно, если вообще возможно с APS реализовать «TOC MTA» управление, со скользящим расчетом «прогноза» достижения «красного» уровня общих, «НзП+ готовые изделия» запасов;
- цитируя близко к тексту Голдратта («Необходимо, но недостаточно»): «… из своей жесткости в точности и детализации планирования APS «классно» распространяют локальные «возмущения» на все производство, всю «сеть заказов»…»
- …и еще короткое замечание: в коммерческих APS не предусмотрено «обвязки», т.е. транзакционной системы, предназначенной для сбора информации и запасах, ходе производства, для автоматизации и управлении (электронным) производственным документооборотом и объектами (наверное единственная «классическая» APS форма «простого» анализа – диаграмма Ганта. У многих «околопроизводственников» вызывает восхищение, в жизни же практически неприменима). На западе подразумевается интеграция APS с ERP системами (и, внимание, повтор! Обязательная логическая интеграция с общей системой планов), но у нас их практически ни у кого в производстве (корректно внедренных и правильно используемых) — нет. Да и сама идея применимости устаревшей ERP модели сейчас — весьма сомнительна.
Постановка же с нуля системы «сбора» и «обработки» информации – это, как минимум, половина всего объема усилий по построению правильной производственной системы.
Совсем ли APS безнадежны? Нет, также, как и ERP. С тем условием, что вы будете подходить к APS как к «простому» калькулятору, или, что лучше — почти прямая аналогия, — как к процессору. Если вам нужно собрать компьютер, под определенные условия, вам нужен процессор. Но еще много-много-много чего… та самая «обвязка», п.7 выше. И при этом — будьте готовы – потребуется «слегка влезть» в процессор, подправить некоторые особенности алгоритмов под вас… А это, в случае процессора и даже весьма квалифицированного сборщика,– практически невозможно. С APS – теоретически возможно, практически — … Но, если знаете, как это сделать (и собрать и «подпилить»), тогда — удачи (и это без шуток). Если нет – готовьте себе прокрустово ложе APS. А это будет пострашнее, чем «холодная и костлявая рука ERP» «из коробки»…
Если альтернатива? Для «наших» производств?
Созданный нами на основе вот уже 20и летней практики построения методологии и внедрения ИТ систем, в т.ч. (давно это было…) тех самых ERP и APS. Чем наш подход отличается? Простотой… Реализовав практически все возможности «сетевого» APS (сетевое позаказное планирование, загрузку мощностей (по ресурсной модели), и некоторые другие) и устранив указанные выше недостатки, мы, в СПМ (SCMo), строим концепцию планирования на одновременном существовании в системе двух видов планов: «директивного» («идеальный» «точно вовремя» план) и «расчетного».
Которые постоянно сравниваются между собой, с учетом и ситуации в производстве в т.ч., с запущенными производственными заданиями. Таким образом давая производственным руководителям то, чего им больше всего не хватает: не супер-точного плана (он, возможно (!) нужен на коротком промежутке времени…), но отклонений — «узкие места» как в производстве, так и в «сети» заказа. Правильное определение «правильного» плана производства: «План не должен быть точным, он должен быть достоверным!» И рабочим. Что еще особенного у нас? Интерфейсная часть (экранные формы мониторинга. В самой системе – не BI) и обязательная «подгонка» (иногда и с подгонкой «ядра») алгоритмов расчета под особенности параллельно определяемой производственной системы предприятия (мы никогда не автоматизируем заводы со слов сотрудников…); бОльшая, по сравнению с равнозначными APS, скорость вычисления и пр.
Что с таким подходом мы потеряли? Ничего. (мега) Оптимизация, т.е. составление плана с учетом всех и всяческих, разных-преразных ограничений – не используется в начале работы системы по нашей методологии. Но не потому, что не может система, а потому, что производство — не готово. Ощутимо это? Пока, и в ближайшей перспективе — нет, т.к. все эти «мелочи» – суть внутрицехового управления. И потом — зачем нам «ловить блох» в «пооперационном планировании станочного парка», если выпуск цеха/участка слабо синхронизирован с выпуском остальных «партнеров»? (это, кстати, типичный подход многих «горе-продавцов» MES: MES–оптимизация внутрицеховой работы, без оглядки на остальных). А если планы по производственной цепочке синхронизированы, не проще ли управлять «внутри-цеха» Lean-инструментарием?
А если все-же кто-то захочет оптимизацию уже на уровне межцехового/участкового планирования? Без вопросов! Причем в рамках той же самой модели (необходимо будет детализировать ресурсы…)
APS– scheduler
Они-же — «калькуляторы» планирования MES. Их место – внутрицеховое/участковое планирование. Оно возможно и оправдано тогда и только тогда, когда производственная цепочка синхронизована. А если «по серьезному» — тогда и только тогда, когда реализован п5 выше (выстроена общая система планов). В этом случае, при наличии явно выраженных и сложно-планируемых вручную «узких мест» они могут применяться. Прежде всего, для определения последовательности в очереди на обработку перед конкретным участком/станком или последовательными группами оборудования. В силу этого APS–scheduler’ы «начинали свою жизнь» как sequencer’ы, как правило, в системах имитационного моделирования.
Если у вас позаказное производство, каждый заказ – существенно отличается по параметрам наладки и обработки оборудования, заказов/вариантов прохождения и обработки – много, нельзя заранее задать правила их размещения – да, в этом случае эта часть APS может вам помочь. С учетом того, что вы готовы заплатить указанную выше цену (не все «особенности» APS–scheduler’ов указаны). И с учетом следующего комментария: если «муда», генерируемая этой частью APS меньше, чем «муда» без его использования. Первая муда – это неизбежное нормативное увеличение циклов выполнения заказа, необходимое для задания «окна оптимизации», в котором scheduler будет по своему усмотрению «тасовать» производственные задания, и, связанный с эти рост НзП; вторая – потери на переналадках, потери пропускной способности узкого места, риск срыва сроков выполнения заказа. В моей практике, в дискретных производствах, крайне редко APS–scheduler необходим. Многие задачи внутрицехового управления решаются «примитивными» Lean и/или ТОС инструментами, а так-же, «простой», через ИТ-методы, визуализацией происходящего с элементами полу автоматизированного управления очередями.
«Непрерывка»
Использование «правильных» APS/MES в «непрерывке» («где все течет»), металлургии, пищёвке, и для решения некоторых других узко-специфических задач в производствах, где оборудование (его использование) – критично для процесса – не обсуждается. Они (системы) там просто должны быть.
Сокращения
SCM, SCMo: Supply Chain Management и Supply Chain (Planning) and Monitoring – управление производственными цепочками, Планирование и Мониторинг Производственных цепочек. Набор базирующихся на классической MRP-II концепции методов и автоматизированных систем, позволяющий планировать производство и закупки синхронно, с учетом существующих и будущих материальных и производственных ресурсов. Как в рамках отдельного предприятия, так и для распределенных систем (производственно-логистических цепочек).
APS — Advanced Planning and Scheduling, «Продвинутое» Планирование или, ближе к смыслу, синхронное планирование и оптимизация. Класс информационных систем – планировщиков производства и запасов, в которых, вычисляющих планы производства и/или уровни запасов с использованием оптимизационных алгоритмов. В классической системе планов предприятия могут соответствовать (зависит от конкретной системы конкретного производителя) уровням планирования от DP до Scheduling.
MES — Manufacturing Execution System, система производственного управления (исполнения!). Класс информационных систем, предназначенных для детального планирования и управления производством, как правило, на уровне оборудования и операций. В ряде случаев с использованием интеграции с оборудованием. Принципиально отличаются для разных типов производства.
ERP — Enterprise Resource Planning – планирование ресурсов предприятия. Маркетинговый термин и широко определенный класс информационных систем позволяющих интегрировано автоматизировать некоторые области деятельности предприятия, как правило, без областей планирования, бюджетирования, ведения состава изделия и некоторых других.
MRP-II — Manufacturing Resource Planning, Планирование Производственных Ресурсов – западная 1970х гг прошлого века концепция управления производством и операциями. Планирование производства и запасов в которой выполняется по MRP (Material Requirements Planning) и CRP (Capacity Requirements Planning) алгоритмам.
Мы начинаем цикл статей, которые посвящены автоматизации планирования производства. В современных условиях организация планирования принципиально важна для жизнеспособности производственного предприятия. В первой части цикла мы поговорим об основных подходах и концепциях планирования производства, которые важны именно в плане их автоматизации. Существует множество различных методологий планирования производства с точки зрения расчета потребностей в выпуске изделий и их компонент. В первой статье цикла кратко описываются наиболее употребительные концепции планирования производства, связанные с автоматизацией.
Производственное планирование — это часть системы планирования деятельности предприятия, элемент среднесрочного и краткосрочного бизнес-планирования. Производственные планы могут строится отталкиваясь от долгосрочных и среднесрочных планов маркетинга и продаж, а также на основании текущих заказов клиентов.
Ключевые цели автоматизации производственного планирования:
- повышение качества выполнения заказов клиентов:
- быстрое определение возможного срока изготовления продукции по запросу клиента;
- формирование выполнимого и оптимального графика производства исходя из доступных мощностей и ресурсов;
- обеспечение выполнения обязательств перед клиентом по срокам и ассортименту и прослеживаемость выполнения заказов на всех этапах изготовления продукции;
- оперативная реакция на отклонения в выполнении графика и на изменения заказов и, соответственно, перестраивание графика производства;
- эффективное использование производственных ресурсов и снижение себестоимости;
- минимизация замораживания капитала в НЗП, исключение невостребованных работ;
- обеспечение ритмичности производства и исключение авралов;
- обеспечение контроля выполнения нормативов и использования замен и аналогов;
- снижение влияния «человеческого фактора» и эффективное использование человеческих ресурсов.
В современных условиях эти характеристики принципиально важны для жизнеспособности производственного предприятия.
В рамках образовательного проекта PlanFact2.ru эксперты компании «Институт типовых решений — Производство» совместно с партнерами регулярно готовят и публикуют обучающие материалы, в том числе по производственному планированию — методички, записи вебинаров, примеры документов с проектов автоматизации, видеоуроки, полные курсы по освоению предметной области в решениях 1С. Часть материалов доступна для скачивания бесплатно.
Двухуровневая модель планирования
Одна из важных концепций в области производственного планирования ç— двухуровневая модель планирования. На многих предприятиях, особенно в дискретных отраслях производства, можно выделить два уровня управления.
- Верхний уровень — межцеховое планирование. Планирование и управление выполнением графика производства, исполнителями которого являются отдельные производственные подразделения. Функцию межцехового управления обычно исполняет производственно-диспетчерский отдел предприятия (ПДО). При таком планировании формируется график выполнения этапов производства подразделениями без детализации операций внутри этапа. Ведется координация процессов передачи результатов этапов между подразделениями. При отклонении от графика выполняется перепланирование графика, потребители оповещаются о срыве сроков.
- Нижний уровень — внутрицеховое планирование. На этом уровне организуется исполнение графика производства в отдельном подразделении — обособленной зоне ответственности диспетчера подразделения, которой может быть цех или участок. Функцию внутрицехового планирования выполняет диспетчер подразделения. Для исполнения графика диспетчер формирует маршрутные листы для конкретных рабочих центров, они отображают исполнение запланированного этапа производства. Диспетчер формирует расписание выполнения маршрутных листов на рабочих центрах, организует и контролирует выполнение этого расписания.
В дальнейшем верхний уровень управления (функции диспетчера предприятия) будем называть уровнем «диспетчера предприятия1, нижний уровень (функции диспетчера подразделения) — уровнем «локального диспетчера».
«Проталкивающая» и «вытягивающая» системы управления
Независимо от того, два уровня планирования на предприятия или один, план производства рассчитывается исходя из определенных подходов. Прежде всего, необходимо разделять системы планирования производства «проталкивающего» (push) и «вытягивающего» (pull) типа. Данная классификация определяется принципиальными различиями двух подходов к координации многоэтапного производственного процесса.
При изготовлении изделия в многоэтапных (в том числе и многопередельных) производствах возникает потребность в компонентах — в других изготавливаемых изделиях или исходных материалах. Потребность в компонентах приводит, в свою очередь, к потребности в других компонентах. И так вниз по иерархической структуре продукта до исходных материалов. Соответственно, чтобы получить готовую продукцию к требуемой дате, необходимо обеспечить своевременный выпуск компонент. Обеспечить это можно двумя основными подходами.
- «Проталкивающий» подход. В системе «проталкивающего» типа график производства, как график передачи результатов работ между подразделениями, рассчитывается заранее и увязывает все производство. Источником плана выпуска изделий для каждого подразделения является график производства по предприятию в целом. Диспетчер предприятия как бы поэтапно «проталкивает» изготовление каждой компоненты в назначенный срок: от первого до последнего этапа производства, от подразделения к подразделению. Каждое подразделение при этом вправе полагать, что, выполняя свои этапы по глобальному графику, оно своевременно обеспечит своими компонентами другие подразделения. Связываться напрямую с потребителями и поставщиками ç— смежными подразделениями ç— в общем случае ему не требуется. К проталкивающему типу относятся такие методологии планирования, как MRP, APS, TOC («буфер—барабан—веревка»), о которых мы расскажем ниже.
- «Вытягивающий» подход. В системе «вытягивающего» типа потребности в выпуске определяются в режиме онлайн непосредственно подразделениями и рабочими местами, которые используют эти компоненты. Диспетчер подразделения сам определяет, когда и какие компоненты-материалы ему понадобятся, и сообщает о своей потребности подразделениям-поставщикам. Можно сказать, что выпуск «вытягивается» подразделениями — потребителями компонент из подразделений-поставщиков (которые в свою очередь будут потребителями компонент предшествующих этапов ç— и так до исходных материалов).
При таком подходе потребность в компонентах фиксируется в сигналах, передаваемых между подразделениями. В роли сигналов, например, могут быть карточки. Типичный пример использования сигнальных карточек ç— система «Канбан». В соответствии с сигналами о потребностях, как по командам, подразделения-поставщики передают результаты своей работы подразделениям-потребителям, от которых получены сигналы. Диспетчер подразделения постоянно держит связь с диспетчерами-смежниками.
Такие системы часто называют «точно в срок» (Just-In-Time), поскольку:
- сроки всех поставок по предприятию определяются не графиком, рассчитанным заранее, а реальными текущими потребностями, определенными в режиме онлайн;
- если точно в срок, в соответствии с сигналом, необходимые компоненты для производства не будут получены, работа подразделения ç— потребителя компонент остановится. Поэтому работа такой системы возможна лишь при поставке компонент точно в срок, по сигналу потребителя.
Надо сказать, что в существующих на большинстве производств условиях столь высокие требования к времени поставки компонент практически недостижимы и это делает «вытягивающую» концепцию трудно применимой в российских условиях. Например, алгоритмы планирования этапов в системе «1С:ERP Управление предприятием 2.0» базируются преимущественно на «проталкивающих» методиках. Опишем подробнее системы этого типа.
MRP (Manufacturing Resourse Planning2)
Это самый известный и один из самых старых методов планирования. В нем используется простой алгоритм расчета графика производства, который заключается в следующем. На вход алгоритма подается график выпуска готовой продукции3. По каждому плановому выпуску продукции (количеству на определенную дату) по спецификации определяется потребность в компонентах и их количестве, дата (время) потребности. Определяется также подразделение ç— изготовитель компонент4.
Далее для подразделения — изготовителя компонента в график записывается выпуск и подача компонента подразделению-потребителю в необходимом количестве в требуемую дату. Для каждой компоненты в цехе-изготовителе, в свою очередь, определяются по ее спецификации необходимые для ее изготовления компоненты более нижнего уровня. Аналогично планируется выпуск и подача компонент более нижнего уровня (рис. 1).
Рис. 1. Связь компонент и готового изделия на графике производства.
Данный процесс называется «разузлование спецификаций изделия» и выполняется до тех пор, пока дерево изделия не развернется до закупаемых компонент-материалов. В процессе разузлования строится график потребностей во времени работы оборудования и персонала. Этот график опирается на данные об операциях по каждой спецификации и о необходимом времени работы оборудования и персонала.
Затем график потребностей во времени работы оборудования и персонала можно сравнить с доступным временем и определить, выполним график производства или нет. Если график выпуска продукции не выполним, то он «прореживается», то есть заказы клиентов смещаются на более поздние даты и расчет графика производства выполняется заново. После этого график производства опять проверяется на выполнимость. Такие итерации повторяются несколько раз, пока график производства не будет выполнимым.
Очевидно, что для исключения большого количества итераций расчета необходимо, чтобы график выпуска продукции изначально соответствовал мощностям производства.
Преимущество алгоритма MRP — простота и понятность результатов.
Недостатки MRP:
- обычно для получения выполнимого графика требуется выполнить несколько итераций (зачастую — множество);
- возможна неполная загрузка мощностей, в том числе рабочих центров — «узких мест», ограничивающих пропускную способность производства.
Заметим, что, несмотря на недостатки и ограниченность алгоритма MRP, именно с него началась эволюция многих алгоритмов и концепций планирования производства.
APS (Advanced Planning & Scheduling), или «синхронное планирование»
В отличие от алгоритма MRP при APS-планировании сразу учитываются те или иные производственные мощности — оборудование либо оборудование и рабочий персонал. График производства в общем случае содержит расписание работы и переналадок рабочих центров на всех этапах производства. Операции в расписании сразу планируются с учетом фонда доступного времени рабочих центров.
В APS-алгоритме расчета могут быть использованы различные критерии оптимизации ç— например, минимизация времени переналадки, минимизация времени пролеживания деталей и пр. Кроме того, APS-алгоритмы поддерживают планирование не только «назад» во времени, но и планирование «вперед». Например, если в процессе расчета расписания выявляется отсутствие доступного времени оборудования для какой-либо операции, алгоритм находит ближайшее незанятое время в будущем и выстраивает расписание операций «вперед» от этого времени, тем самым определяется дата выпуска готовой продукции по заказу. Таким образом рассчитывается минимально возможная реальная дата выполнения заказа.
На рис. 2 показан пример, когда одна из операций для изготовления промежуточного компонента изделия MRP-алгоритмом была бы назначена на вторник, чтобы выпустить готовую продукцию к намеченному сроку. Однако APS-алгоритм обнаружил, что необходимое для этой операции оборудование до конца вторника уже занято. Он сдвигает эту операцию вперед по времени туда, где рабочий центр освободится. И затем сдвинет вперед все последующие операции, включая и дату выпуска конечного изделия (если это необходимо).
Рис. 1. Связь компонент и готового изделия на графике производства.
Данный процесс называется «разузлование спецификаций изделия» и выполняется до тех пор, пока дерево изделия не развернется до закупаемых компонент-материалов. В процессе разузлования строится график потребностей во времени работы оборудования и персонала. Этот график опирается на данные об операциях по каждой спецификации и о необходимом времени работы оборудования и персонала.
Затем график потребностей во времени работы оборудования и персонала можно сравнить с доступным временем и определить, выполним график производства или нет. Если график выпуска продукции не выполним, то он «прореживается», то есть заказы клиентов смещаются на более поздние даты и расчет графика производства выполняется заново. После этого график производства опять проверяется на выполнимость. Такие итерации повторяются несколько раз, пока график производства не будет выполнимым.
Очевидно, что для исключения большого количества итераций расчета необходимо, чтобы график выпуска продукции изначально соответствовал мощностям производства.
Преимущество алгоритма MRP — простота и понятность результатов.
Недостатки MRP:
- обычно для получения выполнимого графика требуется выполнить несколько итераций (зачастую — множество);
- возможна неполная загрузка мощностей, в том числе рабочих центров — «узких мест», ограничивающих пропускную способность производства.
Заметим, что, несмотря на недостатки и ограниченность алгоритма MRP, именно с него началась эволюция многих алгоритмов и концепций планирования производства.
APS (Advanced Planning & Scheduling), или «синхронное планирование»
В отличие от алгоритма MRP при APS-планировании сразу учитываются те или иные производственные мощности — оборудование либо оборудование и рабочий персонал. График производства в общем случае содержит расписание работы и переналадок рабочих центров на всех этапах производства. Операции в расписании сразу планируются с учетом фонда доступного времени рабочих центров.
В APS-алгоритме расчета могут быть использованы различные критерии оптимизации ç— например, минимизация времени переналадки, минимизация времени пролеживания деталей и пр. Кроме того, APS-алгоритмы поддерживают планирование не только «назад» во времени, но и планирование «вперед». Например, если в процессе расчета расписания выявляется отсутствие доступного времени оборудования для какой-либо операции, алгоритм находит ближайшее незанятое время в будущем и выстраивает расписание операций «вперед» от этого времени, тем самым определяется дата выпуска готовой продукции по заказу. Таким образом рассчитывается минимально возможная реальная дата выполнения заказа.
На рис. 2 показан пример, когда одна из операций для изготовления промежуточного компонента изделия MRP-алгоритмом была бы назначена на вторник, чтобы выпустить готовую продукцию к намеченному сроку. Однако APS-алгоритм обнаружил, что необходимое для этой операции оборудование до конца вторника уже занято. Он сдвигает эту операцию вперед по времени туда, где рабочий центр освободится. И затем сдвинет вперед все последующие операции, включая и дату выпуска конечного изделия (если это необходимо).
Рис. 2. Сдвиг операции на свободное время рабочего центра APS-алгоритмом.
При APS-планировании все заказы клиентов могут обрабатываться последовательно в соответствии с приоритетом заказов. Более приоритетные заказы, вставляемые в график производства в первую очередь, в результате первыми захватывают доступные мощности. Таким образом уменьшается вероятность, что система передвинет время их выполнения на более поздний срок, чем того требует заказ.
Преимущества APS-алгоритма:
- планирование в соответствии с мощностями производства, что позволяет сразу получить выполнимые планы;
- возможность определить реальную дату выполнения заказа;
- скорость перепланирования графика производства, актуализации в соответствии с отклонениями в ходе производства или изменениями в заказах;
- максимальное использование пропускной способности производства, что очень важно, когда именно производство является ограничением бизнеса, а не рыночный спрос.
Недостатки APS-алгоритма:
- необходимость ввода в систему большого количества производственных параметров, в противном случае построенный график производства потребует постоянной корректировки и перепланирования;
- возможные отклонения от графика в производстве требуют периодического (например, ежесуточного) перепланирования, что приводит к нестабильности графика («нервозности» производства) и периодическому изменению плановых дат выпуска по заказам.
«Буфер — барабан — веревка» (ББВ)
Метод планирования, названный «буфер — барабан — веревка», базируется на теории ограничений систем (Theory of Constraints, ТОС5). В его основе лежит допущение, что производство не может быть полностью синхронным. То есть всегда есть рабочие центры — так называемые «узкие места», которые ограничивают пропускную способность. Поэтому необходима концентрация на управлении этим «узким местом», а остальным рабочим центрам не стоит уделять внимание в той мере, как это делают алгоритмы MRP и APS.
Рабочий центр, который является «узким местом», называется барабаном6. Как и в примере Голдрата, барабан «отбивает такт» всего производства и все остальные рабочие центры подчинены этому ритму и должны обеспечивать наиболее эффективную загрузку барабана. Логика этого проста: простаивание барабана — это простаивание всего предприятия, а излишки продукции при максимально работающем барабане — это увеличение НЗП. Перед барабаном следует поддерживать очередь работ (и запас необходимых для обработки на барабане материалов или полуфабрикатов), чтобы этот рабочий центр был всегда загружен. Однако при этом необходимо следить, чтобы перед барабаном не скапливалось много полуфабрикатов.
Чтобы обеспечить упомянутую выше очередь работ перед барабаном, используются два инструмента:
- буфер, задающий запас времени на выполнение работы до барабана;
- веревка «связывает» ритм работы барабана и ритм отпуска материалов в производство (рис. 3). Ее задача — ограничить накопление НЗП в цепочке, не выдав материалы в работу раньше времени7.
Рис. 3. Основные понятия метода «буфер — барабан — веревка».
Важный момент: длина веревки не равна, а больше, чем общее время предшествующих барабану операций! Это необходимо для защиты барабана (узкого места) от простоев вследствие возможных непредвиденных отклонений на операциях перед ним. Иными словами, параметр «буфер» задает время, за который должны пройти все операции, предшествующие барабану. И при этом буферное время обязательно превышает суммарное время операций до барабана. Чем больше разница между буфером и суммарным временем операций, тем длительнее процесс производства, но тем меньше риск простоя барабана из-за «обнуления» очереди перед барабаном8.
Для каждого заказа или партии деталей, которые еще не поступили в очередь к барабану, в любой момент времени можно определить «цвет зоны» буфера, в которой находится заказ, партия:
- «зеленая зона» — партия еще не выбрала время, равное суммарному времени операций9. Эта партия не требует внимания;
- «желтая зона» — партия выбрала суммарное время операций, например, это может быть 1/3 буфера. Такая партия уже требует внимания, так как ее операции запаздывают;
- «красная зона» — партия выбрала некоторую критичную долю буфера, например 2/3. Такая партия требует немедленного вмешательства, в противном случае есть риск, что партия не выйдет к «барабану» вовремя согласно расписанию, то есть риск простоя барабана.
Организация контроля по зонам позволяет сконцентрироваться на проблемах и не обращать внимание на нормально выполняющиеся процессы. На рис. 4 показано распределение зон в буфере, когда длина буфера равна утроенному суммарному времени операций.
Рис. 3. Основные понятия метода «буфер — барабан — веревка».
Важный момент: длина веревки не равна, а больше, чем общее время предшествующих барабану операций! Это необходимо для защиты барабана (узкого места) от простоев вследствие возможных непредвиденных отклонений на операциях перед ним. Иными словами, параметр «буфер» задает время, за который должны пройти все операции, предшествующие барабану. И при этом буферное время обязательно превышает суммарное время операций до барабана. Чем больше разница между буфером и суммарным временем операций, тем длительнее процесс производства, но тем меньше риск простоя барабана из-за «обнуления» очереди перед барабаном8.
Для каждого заказа или партии деталей, которые еще не поступили в очередь к барабану, в любой момент времени можно определить «цвет зоны» буфера, в которой находится заказ, партия:
- «зеленая зона» — партия еще не выбрала время, равное суммарному времени операций9. Эта партия не требует внимания;
- «желтая зона» — партия выбрала суммарное время операций, например, это может быть 1/3 буфера. Такая партия уже требует внимания, так как ее операции запаздывают;
- «красная зона» — партия выбрала некоторую критичную долю буфера, например 2/3. Такая партия требует немедленного вмешательства, в противном случае есть риск, что партия не выйдет к «барабану» вовремя согласно расписанию, то есть риск простоя барабана.
Организация контроля по зонам позволяет сконцентрироваться на проблемах и не обращать внимание на нормально выполняющиеся процессы. На рис. 4 показано распределение зон в буфере, когда длина буфера равна утроенному суммарному времени операций.
Рис. 4. «Зеленая», «желтая» и «красная» зоны в буфере.
«Упрощенный «буфер — барабан — веревка» (УББВ)
Методику «буфер — барабан — веревка» можно сильно упростить, если заметить, что подход цветных зон может использоваться без барабана. Организация контроля производства по зонам очень удобна, поскольку позволяет сконцентрироваться над проблемами и не обращать внимания на процессы, проходящие в нормальном режиме. И можно использовать идею «зеленой», «желтой» и «красной» зон, но не выявлять узкое место (барабан). В этом случае буфером считается весь производственный цикл, то есть по зонам ведется контроль прохождения партии (заказа) в рамках всего производственного цикла. Эту методику называют «упрощенный «буфер — барабан — веревка» (УББВ).
Фактически методика УББВ исходит из допущения, что ограничением является потребитель, а мощности производства превышают потребительский спрос. В этом случае основной такт производства задают плановые операции передачи продукции потребителю.
***
В следующей статье цикла мы расскажем об общих принципах формирования графика производства: интервалах планирования и расчете графика на верхнем и нижнем уровнях.