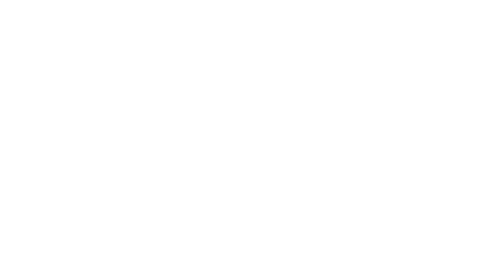
Поверхностная обработка заготовок методом фрезерования может проводиться исключительно после разработки технологической карты, в которой указываются основные режимы обработки. Подобной работой, как правило, занимается специалист, прошедший специальную подготовку.
Режимы резания при фрезеровании могут зависеть от самых различных показателей, к примеру, типа материала и используемого инструмента. Основные показатели на фрезерном станке могут устанавливаться вручную, также проводится указание показателей на блоке числового программного управления. Особое внимание заслуживает резьбофрезерование, так как получаемые изделия характеризуются довольно большим количеством различных параметров. Рассмотрим особенности выбора режимов резания при фрезеровании подробно.
Скорость резания
Наиболее важным режимом при фрезеровании можно назвать скорость резания. Он определяет то, за какой период времени будет снят определенный слой материала с поверхности. На большинстве станков устанавливается постоянная скорость резания. При выборе подходящего показателя учитывается тип материала заготовки:
- При работе с нержавейкой скорость резания 45-95 м/мин. За счет добавления в состав различных химических элементов твердость и другие показатели меняются, снижается степень обрабатываемости.
- Бронза считается более мягким составом, поэтому подобный режим при фрезеровании может выбираться в диапазоне от 90-150 м/мин. Она применяется при изготовлении самых различных изделий.
- Довольно большое распространение получила латунь. Она применяется при изготовлении запорных элементов и различных клапанов. Мягкость сплава позволяет повысить скорость резания до 130-320 м/мин. Латуни склонны к повышению пластичности при сильном нагреве.
- Алюминиевые сплавы сегодня весьма распространены. При этом встречается несколько вариантов исполнения, которые обладают различными эксплуатационными характеристиками. Именно поэтому режим фрезерования варьирует в пределе от 200 до 420 м/мин. Стоит учитывать, что алюминий относится к сплавам с низкой температурой плавления. Именно поэтому при высокой скорости обработки есть вероятность существенного повышения показателя пластичности.
Скорость резания
Наиболее важным режимом при фрезеровании можно назвать скорость резания. Он определяет то, за какой период времени будет снят определенный слой материала с поверхности. На большинстве станков устанавливается постоянная скорость резания. При выборе подходящего показателя учитывается тип материала заготовки:
- При работе с нержавейкой скорость резания 45-95 м/мин. За счет добавления в состав различных химических элементов твердость и другие показатели меняются, снижается степень обрабатываемости.
- Бронза считается более мягким составом, поэтому подобный режим при фрезеровании может выбираться в диапазоне от 90-150 м/мин. Она применяется при изготовлении самых различных изделий.
- Довольно большое распространение получила латунь. Она применяется при изготовлении запорных элементов и различных клапанов. Мягкость сплава позволяет повысить скорость резания до 130-320 м/мин. Латуни склонны к повышению пластичности при сильном нагреве.
- Алюминиевые сплавы сегодня весьма распространены. При этом встречается несколько вариантов исполнения, которые обладают различными эксплуатационными характеристиками. Именно поэтому режим фрезерования варьирует в пределе от 200 до 420 м/мин. Стоит учитывать, что алюминий относится к сплавам с низкой температурой плавления. Именно поэтому при высокой скорости обработки есть вероятность существенного повышения показателя пластичности.
Встречается довольно большое количество таблиц, которые применяются для определения основных режимов работы. Формула для определения оборотов скорости резания выглядит следующим образом: n=1000 V/D, где учитывается рекомендуемая скорость резания и диаметр применяемой фрезы. Подобная формула позволяет определить количество оборотов для всех видов обрабатываемых материалов.
Рассматриваемый режим фрезерования измеряется в метрах в минуту режущие части. Стоит учитывать, что специалисты не рекомендуют гонять шпиндель на максимальных оборотах, так как существенно повышается износ и есть вероятность повреждения инструмента. Поэтому полученный результат уменьшается примерно на 10-15%. С учетом этого параметра проводится выбор наиболее подходящего инструмента.
Скорость вращения инструмента определяет следующее:
- Качество получаемой поверхности. Для финишной технологической операции выбирается наибольший параметр. За счет осевого вращения с большим количеством оборотов стружка получается слишком мелкой. Для черновой технологической операции, наоборот, выбираются низкие значения, фреза вращается с меньшей скоростью, и размер стружки увеличивается. За счет быстрого вращения достигается низкий показатель шероховатости поверхности. Современные установки и оснастка позволяют получить поверхность зеркального типа.
- Производительность труда. При наладке производства уделяется внимание и тому, какова производительность применяемого оборудования. Примером можно назвать цех машиностроительного завода, где налаживается массовое производство. Существенное снижение показателя режимов обработки становится причиной уменьшения производительности. Наиболее оптимальный показатель существенно повышает эффективность труда.
- Степень износа устанавливаемого инструмента. Не стоит забывать о том, что при трении режущей кромки об обрабатываемую поверхность происходит ее сильный износ. При сильном изнашивании происходит изменение показателей точности изделия, снижается эффективность труда. Как правило, износ связан с сильным нагревом поверхности. Именно поэтому на производственной линии с высокой производительностью применяется оборудование, способное подавать СОЖ в зону снятия материала.
При этом данный параметр выбирается с учетом других показателей, к примеру, глубины подачи. Поэтому технологическая карта составляется с одновременным выбором всех параметров.
Глубина резания
Другим наиболее важным параметром является глубина фрезерования. Она характеризуется следующими особенностями:
- Глубина врезания выбирается в зависимости от материала заготовки.
- При выборе уделяется внимание тому, проводится черновая или чистовая обработка. При черновой выбирается большая глубина врезания, так как устанавливается меньшая скорость. При чистовой снимается небольшой слой металла за счет установки большой скорости вращения инструмента.
- Ограничивается показатель также конструктивными особенностями инструмента. Это связано с тем, что режущая часть может иметь различные размеры.
Глубина резания во многом определяет производительность оборудования. Кроме этого, подобный показатель в некоторых случаях выбирается в зависимости от того, какую нужно получить поверхность.
Мощность силы резания при фрезеровании зависит от типа применяемой фрезы и вида оборудования. Кроме этого, черновое фрезерование плоской поверхности проводится в несколько проходов в случае, когда нужно снять большой слой материала.
При этом данный параметр выбирается с учетом других показателей, к примеру, глубины подачи. Поэтому технологическая карта составляется с одновременным выбором всех параметров.
Глубина резания
Другим наиболее важным параметром является глубина фрезерования. Она характеризуется следующими особенностями:
- Глубина врезания выбирается в зависимости от материала заготовки.
- При выборе уделяется внимание тому, проводится черновая или чистовая обработка. При черновой выбирается большая глубина врезания, так как устанавливается меньшая скорость. При чистовой снимается небольшой слой металла за счет установки большой скорости вращения инструмента.
- Ограничивается показатель также конструктивными особенностями инструмента. Это связано с тем, что режущая часть может иметь различные размеры.
Глубина резания во многом определяет производительность оборудования. Кроме этого, подобный показатель в некоторых случаях выбирается в зависимости от того, какую нужно получить поверхность.
Мощность силы резания при фрезеровании зависит от типа применяемой фрезы и вида оборудования. Кроме этого, черновое фрезерование плоской поверхности проводится в несколько проходов в случае, когда нужно снять большой слой материала.
Особым технологическим процессом можно назвать работу по получению пазов. Это связано с тем, что их глубина может быть довольно большой, а образование подобных технологических выемок проводится исключительно после чистовой обработки поверхности. Фрезерование т-образных пазов проводится при применении специального инструмента.
Подача
Понятие подачи напоминает глубину врезания. Подача при фрезеровании, как и при проведении любой другой операции по механической обработке металлических заготовок, считается наиболее важным параметром. Долговечность применяемого инструмента во многом зависит от подачи. К особенностям этой характеристики можно отнести нижеприведенные моменты:
- Какой толщины материал снимается за один проход.
- Производительность применяемого оборудования.
- Возможность проведения черновой или чистовой обработки.
Довольно распространенным понятием можно назвать подачу на зуб. Этот показатель указывается производителем инструмента, зависит от глубины резания и конструктивных особенностей изделия.
Как ранее было отмечено, многие показатели режимом резания связаны между собой. Примером можно назвать скорость резания и подачу:
- При увеличении значения подачи скорость резания снижается. Это связано с тем, что при снятии большого количества металла за один проход существенно повышается осевая нагрузка. Если выбрать высокую скорость и подачу, то инструмент будет быстро изнашиваться или попросту поломается.
- За счет снижения показателя подачи повышается и допустимая скорость обработки. При быстром вращении фрезы возможно существенно повысить качество поверхности. На момент чистового фрезерования выбирается минимальное значение подачи и максимальная скорость, при применении определенного оборудования можно получить практически зеркальную поверхность.
Довольно распространенным значением подачи можно назвать 0,1-0,25. Его вполне достаточно для обработки самых распространенных материалов в различных отраслях промышленности.
Ширина фрезерования
Еще одним параметром, который учитывается при механической обработки заготовок считается ширина фрезерования. Она может варьировать в достаточно большом диапазоне. Ширина выбирается при фрезеровке на станке Have или другом оборудовании. Среди особенностей отметим следующие моменты:
- Ширина фрезерования зависит от диаметра фрезы. Подобные параметры, которые зависят от геометрических особенностей режущей части, не могут регулироваться, учитываются при непосредственном выборе инструмента.
- Ширина фрезерования также оказывает влияние на выбор других параметров. Это связано с тем, что при увеличении значения также увеличивается количество материала, который снимается за один проход.
В некоторых случаях ширина фрезерования позволяет получить требуемую поверхность за один проход. Примером можно назвать случай получения неглубоких канавок. Если проводится резание плоской поверхности большой ширины, то число проходов может несколько отличаться, рассчитывается в зависимости от ширины фрезерования.
Как выбрать режим на практике?
Как ранее было отмечено, в большинстве случаев технологические карты разработаны специалистом и мастеру остается лишь выбрать подходящий инструмент и задать указанные параметры. Кроме этого, мастер должен учитывать то, в каком состоянии находится оборудование, так как предельные значения могут привести к возникновению поломок. При отсутствии технологической карты приходится проводить выбор режимов фрезерования самостоятельно. Расчет режимов резания при фрезеровании проводится с учетом следующих моментов:
- Типа применяемого оборудования. Примером можно назвать случай резания при фрезеровании на станках ЧПУ, когда могут выбираться более высокие параметры обработки по причине высоких технологических возможностей устройства. На старых станках, которые были введены в эксплуатацию несколько десятков лет назад, выбираются более низкие параметры. На момент определения подходящих параметров уделяется внимание и техническому состоянию оборудования.
- Следующий критерий выбора заключается в типе применяемого инструмента. При изготовлении фрезы могут применяться различные материалы. К примеру, вариант исполнения из быстрорежущей качественной стали подходит для обработки металла с высокой скоростью резания, фреза с тугоплавкими напайками предпочтительно выбирается в случае, когда нужно проводить фрезерование твердого сплава с высоким показателем подачи при фрезеровании. Имеет значение и угол заточки режущей кромки, а также диаметральные размер. К примеру, с увеличением диаметра режущего инструмента снижается подача и скорость резания.
- Тип обрабатываемого материала можно назвать одним из наиболее важных критериев, по которым проводится выбор режима резания. Все сплавы характеризуются определенной твердостью и степенью обрабатываемости. К примеру, при работе с мягкими цветными сплавами могут выбираться более высокие показатели скорости и подачи, в случае с каленной сталью или титаном все параметры снижаются. Немаловажным моментом назовем то, что фреза подбирается не только с учетом режимов резания, но и типа материала, из которого изготовлена заготовка.
- Режим резания выбирается в зависимости от поставленной задачи. Примером можно назвать черновое и чистовое резание. Для черного свойственна большая подача и небольшой показатель скорости обработки, для чистовой все наоборот. Для получения канавок и других технологических отверстий и вовсе показатели подбираются индивидуально.
Как показывает практика, глубина резания в большинстве случаев делится на несколько проходов при черновой обработке, при чистовой он только один. Для различных изделий может применяться таблица режимов, которая существенно упрощает поставленную задачу. Встречаются и специальные калькуляторы, проводящие вычисление требуемых значений в автоматическом режиме по введенным данным.
Выбор режима в зависимости от типа фрезы
Для получения одного и того же изделия могут применяться самые различные виды фрез. Выбор основных режимов фрезерования проводится в зависимости от конструктивных и других особенностей изделия. Режимы резания при фрезеровании дисковыми фрезами или другими вариантами исполнения выбираются в зависимости от нижеприведенных моментов:
- Жесткости применяемой системы. Примером можно назвать особенности станка и различной оснастки. Новое оборудование характеризуется повышенной жесткостью, за счет чего появляется возможность применения более высоких параметров обработки. На старых станках жесткость применяемой системы снижается.
- Уделяется внимание и процессу охлаждения. Довольно большое количество оборудования предусматривает подачу СОЖ в зону обработки. За счет подобного вещества существенно снижается температура режущей кромки. СОЖ должна подаваться в зону снятия материала постоянно. При этом также удаляется и образующаяся стружка, что существенно повышает качество резания.
- Стратегия обработки также имеет значение. Примером можно назвать то, что получение одной и той же поверхности может проводится при чередовании различных технологических операций.
- Высота слоя, который может сниматься за один проход инструмента. Ограничение может зависеть от размера инструмента и многих других геометрических особенностей.
- Размер обрабатываемых заготовок. Для больших заготовок требуется инструмент с износостойкими свойствами, который при определенных режимах резания сможет не нагреваться.
В некоторых случаях ширина фрезерования позволяет получить требуемую поверхность за один проход. Примером можно назвать случай получения неглубоких канавок. Если проводится резание плоской поверхности большой ширины, то число проходов может несколько отличаться, рассчитывается в зависимости от ширины фрезерования.
Как выбрать режим на практике?
Как ранее было отмечено, в большинстве случаев технологические карты разработаны специалистом и мастеру остается лишь выбрать подходящий инструмент и задать указанные параметры. Кроме этого, мастер должен учитывать то, в каком состоянии находится оборудование, так как предельные значения могут привести к возникновению поломок. При отсутствии технологической карты приходится проводить выбор режимов фрезерования самостоятельно. Расчет режимов резания при фрезеровании проводится с учетом следующих моментов:
- Типа применяемого оборудования. Примером можно назвать случай резания при фрезеровании на станках ЧПУ, когда могут выбираться более высокие параметры обработки по причине высоких технологических возможностей устройства. На старых станках, которые были введены в эксплуатацию несколько десятков лет назад, выбираются более низкие параметры. На момент определения подходящих параметров уделяется внимание и техническому состоянию оборудования.
- Следующий критерий выбора заключается в типе применяемого инструмента. При изготовлении фрезы могут применяться различные материалы. К примеру, вариант исполнения из быстрорежущей качественной стали подходит для обработки металла с высокой скоростью резания, фреза с тугоплавкими напайками предпочтительно выбирается в случае, когда нужно проводить фрезерование твердого сплава с высоким показателем подачи при фрезеровании. Имеет значение и угол заточки режущей кромки, а также диаметральные размер. К примеру, с увеличением диаметра режущего инструмента снижается подача и скорость резания.
- Тип обрабатываемого материала можно назвать одним из наиболее важных критериев, по которым проводится выбор режима резания. Все сплавы характеризуются определенной твердостью и степенью обрабатываемости. К примеру, при работе с мягкими цветными сплавами могут выбираться более высокие показатели скорости и подачи, в случае с каленной сталью или титаном все параметры снижаются. Немаловажным моментом назовем то, что фреза подбирается не только с учетом режимов резания, но и типа материала, из которого изготовлена заготовка.
- Режим резания выбирается в зависимости от поставленной задачи. Примером можно назвать черновое и чистовое резание. Для черного свойственна большая подача и небольшой показатель скорости обработки, для чистовой все наоборот. Для получения канавок и других технологических отверстий и вовсе показатели подбираются индивидуально.
Как показывает практика, глубина резания в большинстве случаев делится на несколько проходов при черновой обработке, при чистовой он только один. Для различных изделий может применяться таблица режимов, которая существенно упрощает поставленную задачу. Встречаются и специальные калькуляторы, проводящие вычисление требуемых значений в автоматическом режиме по введенным данным.
Выбор режима в зависимости от типа фрезы
Для получения одного и того же изделия могут применяться самые различные виды фрез. Выбор основных режимов фрезерования проводится в зависимости от конструктивных и других особенностей изделия. Режимы резания при фрезеровании дисковыми фрезами или другими вариантами исполнения выбираются в зависимости от нижеприведенных моментов:
- Жесткости применяемой системы. Примером можно назвать особенности станка и различной оснастки. Новое оборудование характеризуется повышенной жесткостью, за счет чего появляется возможность применения более высоких параметров обработки. На старых станках жесткость применяемой системы снижается.
- Уделяется внимание и процессу охлаждения. Довольно большое количество оборудования предусматривает подачу СОЖ в зону обработки. За счет подобного вещества существенно снижается температура режущей кромки. СОЖ должна подаваться в зону снятия материала постоянно. При этом также удаляется и образующаяся стружка, что существенно повышает качество резания.
- Стратегия обработки также имеет значение. Примером можно назвать то, что получение одной и той же поверхности может проводится при чередовании различных технологических операций.
- Высота слоя, который может сниматься за один проход инструмента. Ограничение может зависеть от размера инструмента и многих других геометрических особенностей.
- Размер обрабатываемых заготовок. Для больших заготовок требуется инструмент с износостойкими свойствами, который при определенных режимах резания сможет не нагреваться.
Учет всех этих параметров позволяет подобрать наиболее подходящие параметры фрезерования. При этом учитывается распределение припуска при фрезеровании сферическими фрезами, а также особенности обработки концевой фрезой.
Классификация рассматриваемого инструмента проводится по достаточно большому количеству признаков. Основным можно назвать тип применяемого материала при изготовлении режущей кромки. К примеру, фреза ВК8 предназначена для работы с заготовками из твердых сплавов и закаленной стали. Рекомендуется применять подобный вариант исполнения при невысокой скорости резания и достаточной подаче. В тоже время скоростные фрезы могут применяться для обработки с высоким показателем резания.
Как правило, выбор проводится с учетом распространенных таблиц. Основными свойствами можно назвать:
- Скорость резания.
- Тип обрабатываемого материала.
- Тип фрезы.
- Частота оборотов.
- Подача.
- Тип проведенной работы.
- Рекомендуемая подача на зуб в зависимости от диаметра фрезы.
Использование нормативной документации позволяет подобрать наиболее подходящие режимы. Как ранее было отмечено, разрабатывать технологический процесс должен исключительно специалист. Допущенные ошибки могут привести к поломке инструмента, снижению качества поверхности заготовки и допущению погрешностей в инструментах, в некоторых случаях, поломке оборудования. Именно поэтому нужно уделять много внимания выбору наиболее подходящего режима резания.
Выбор режима в зависимости от материала
Все материалы характеризуются определенными эксплуатационными характеристиками, которые также должны учитываться. Примером можно назвать фрезерование бронзы, которое проводится при скорости резания от 90 до 150 м/мин. В зависимости от этого значения выбирается величина подачи. Сталь ПШ15 и изделия из нержавейки обрабатываются при применении других показателей.
При рассмотрении типа обрабатываемого материала уделяется внимание также нижеприведенным моментам:
- Твердости. Наиболее важной характеристикой материалов можно назвать именно твердость. Она может варьировать в большом диапазоне. Слишком большая твердость делает деталь прочной и износостойкой, но при этом усложняется процесс обработки.
- Степени обрабатываемости. Все материалы характеризуются определенной степенью обрабатываемостью, зависящая также от пластичности и других показателей.
- Применение технологии улучшения свойств.
Довольно распространенным примером можно назвать проведение закалки. Подобная технология предусматривает нагрев материала с последующим охлаждением, после чего показатель твердости существенно повышается. Также часто проводится ковка, отпуск и другие процедуры изменения химического состава поверхностного слоя.
В заключение отметим, что сегодня можно встретить просто огромное количество различных технологических карт, которые достаточно скачать и использовать для получения требуемых деталей. При их рассмотрении уделяется внимание типу материала заготовки, виду инструмента, рекомендуемому оборудованию. Самостоятельно разработать режимы резания достаточно сложно, при этом нужно делать предварительную проверку выбранных параметров. В противном случае может пострадать как инструмент, так и применяемое оборудование.
Работы, выполняемые на фрезерных станках
На
фрезерных станках обрабатывают
горизонтальные, вертикальные и
наклонные плоскости, фасонные поверхности,
фрезеруют пазы, шпоночные канавки, зубья
прямозубых и винтовых цилиндрических
зубчатых колес, обрабатывают сложные
поверхности набором фрез, нарезают
резьбу. Рассмотрим основные работы,
выполняемые на горизонтально и
вертикально-фрезерных станках.
Горизонтальные
плоскости обрабатывают
цилиндрическими фрезами (рис. 11
a)
на
горизонтально-фрезерных станках либо
торцевыми фрезами (рис. 11
в)
на
вертикально-фрезерных и продольно-фрезерных
станках.
В
большинстве случаев более производительна
обработка торцевыми фрезами, крепление
которых в шпинделе более жестко, число
одновременно работающих зубьев больше,
чем у цилиндрических фрез, и благодаря
этому они работают более плавно. Наиболее
производительна обработка плоскостей
торцевыми фрезами со вставными
ножами, оснащенными твердыми сплавами.
Вертикальные
плоскости обрабатывают
на горизонтально-фрезерных станках
торцевыми или дисковыми фрезами, на
продольно-фрезерных — торцевыми и на
вертикально-фрезерных — концевыми
фрезами (рис. 11в,
г, д).
Наклонные
плоскости и
скосы
обрабатывают
на горизонтально-фрезерных станках
угловыми фрезами (рис. 11e)
или
на вертикально-фрезерных станках с
поворотной головкой — торцевыми (рис.
11
ж).
При
этом шпиндельную головку поворачивают
на необходимый угол.
Прямоугольные
пазы и
уступы
фрезеруют
дисковыми фрезами на горизонтально-фрезерных
или концевыми — на вертикально-фрезерных
станках (рис. 11з,и).
Пазы
Т-образные и
типа «ласточкин
хвост» фрезеруют
на вертикально-фрезерном станке в два
прохода. Ранее прорезают прямоугольный
паз цилиндрической концевой фрезой, а
затем окончательно обрабатывают паз
фрезой соответствующего профиля
(рис. 11 к, л).
Шпоночные
пазы открытые обрабатывают
на горизонтально-фрезерных станках
дисковыми фрезами (рис. 11о), а закрытые
— на
вертикально-фрезерных станках концевыми
(рис. 11м)
или
специальными шпоночными фрезами.
Фасонные
поверхности обрабатывают
фасонными фрезами соответствующего
профиля (рис. 11л, р)
преимущественно
на горизонтально-
фрезерных
станках, а сложные пространственные
фасонные поверхности — на специальных
копировально-фрезерных станках.
Сложные
поверхности, представляющие
собой сочетание горизонтальных,
вертикальных и наклонных плоскостей,
а иногда и криволинейных поверхностей,
часто фрезеруют набором фрез на
горизонтально- и продольно-фрезерных
станках (рис. 11с).
Фрезерные
станки имеют весьма широкую область
применения
и разделяются на две основные группы:
станки общего назначения
и специализированные. К первой группе
относятся станки консольные и
бесконсольные, продольно-фрезерные,
станки непрерывного фрезерования
(карусельные и барабанные). Ко второй
группе относятся станки копировально-фрезерные,
зубофре-зерные,
резьбофрезерные, шпоночно-фрезерные
шлицефрезер-ные
и др. Типоразмеры станков характеризуются
площадью рабочей
(крепежной) поверхности стола или
размерами обрабатываемой
заготовки (при зубо- и резьбообработке).
Приспособления
для установки и
закрепления
заготовок на фрезерных
станках —
это различные прихваты, подставки,
угловые плиты,
призмы, машинные тиски, столы и
вспомогательные инструменты, механизирующие
и автоматизирующие закрепление заготовок
и тем самым сокращающие вспомогательное
время.
Прихваты
(рис. 5.10, а)
используют
для закрепления заготовок или
каких-либо приспособлений непосредственно
на столе станка
с помощью болтов. Нередко один из концов
прихвата Попирается
на подставку 1
(рис.
5.10, б).
Если
при обработке заготовок необходимо
получить плоскости,
расположенные под углом одна к другой,
то применяют угловые.
Рис.
5.8. Установка торцовых
насадных фрез на шпиндель станка: 1
—
фреза; 2
—
шпонка; 3
—
винт;
4
—
шпиндель
Р
Использование нормативной документации позволяет подобрать наиболее подходящие режимы. Как ранее было отмечено, разрабатывать технологический процесс должен исключительно специалист. Допущенные ошибки могут привести к поломке инструмента, снижению качества поверхности заготовки и допущению погрешностей в инструментах, в некоторых случаях, поломке оборудования. Именно поэтому нужно уделять много внимания выбору наиболее подходящего режима резания.
Выбор режима в зависимости от материала
Все материалы характеризуются определенными эксплуатационными характеристиками, которые также должны учитываться. Примером можно назвать фрезерование бронзы, которое проводится при скорости резания от 90 до 150 м/мин. В зависимости от этого значения выбирается величина подачи. Сталь ПШ15 и изделия из нержавейки обрабатываются при применении других показателей.
При рассмотрении типа обрабатываемого материала уделяется внимание также нижеприведенным моментам:
- Твердости. Наиболее важной характеристикой материалов можно назвать именно твердость. Она может варьировать в большом диапазоне. Слишком большая твердость делает деталь прочной и износостойкой, но при этом усложняется процесс обработки.
- Степени обрабатываемости. Все материалы характеризуются определенной степенью обрабатываемостью, зависящая также от пластичности и других показателей.
- Применение технологии улучшения свойств.
Довольно распространенным примером можно назвать проведение закалки. Подобная технология предусматривает нагрев материала с последующим охлаждением, после чего показатель твердости существенно повышается. Также часто проводится ковка, отпуск и другие процедуры изменения химического состава поверхностного слоя.
В заключение отметим, что сегодня можно встретить просто огромное количество различных технологических карт, которые достаточно скачать и использовать для получения требуемых деталей. При их рассмотрении уделяется внимание типу материала заготовки, виду инструмента, рекомендуемому оборудованию. Самостоятельно разработать режимы резания достаточно сложно, при этом нужно делать предварительную проверку выбранных параметров. В противном случае может пострадать как инструмент, так и применяемое оборудование.
Работы, выполняемые на фрезерных станках
На
фрезерных станках обрабатывают
горизонтальные, вертикальные и
наклонные плоскости, фасонные поверхности,
фрезеруют пазы, шпоночные канавки, зубья
прямозубых и винтовых цилиндрических
зубчатых колес, обрабатывают сложные
поверхности набором фрез, нарезают
резьбу. Рассмотрим основные работы,
выполняемые на горизонтально и
вертикально-фрезерных станках.
Горизонтальные
плоскости обрабатывают
цилиндрическими фрезами (рис. 11
a)
на
горизонтально-фрезерных станках либо
торцевыми фрезами (рис. 11
в)
на
вертикально-фрезерных и продольно-фрезерных
станках.
В
большинстве случаев более производительна
обработка торцевыми фрезами, крепление
которых в шпинделе более жестко, число
одновременно работающих зубьев больше,
чем у цилиндрических фрез, и благодаря
этому они работают более плавно. Наиболее
производительна обработка плоскостей
торцевыми фрезами со вставными
ножами, оснащенными твердыми сплавами.
Вертикальные
плоскости обрабатывают
на горизонтально-фрезерных станках
торцевыми или дисковыми фрезами, на
продольно-фрезерных — торцевыми и на
вертикально-фрезерных — концевыми
фрезами (рис. 11в,
г, д).
Наклонные
плоскости и
скосы
обрабатывают
на горизонтально-фрезерных станках
угловыми фрезами (рис. 11e)
или
на вертикально-фрезерных станках с
поворотной головкой — торцевыми (рис.
11
ж).
При
этом шпиндельную головку поворачивают
на необходимый угол.
Прямоугольные
пазы и
уступы
фрезеруют
дисковыми фрезами на горизонтально-фрезерных
или концевыми — на вертикально-фрезерных
станках (рис. 11з,и).
Пазы
Т-образные и
типа «ласточкин
хвост» фрезеруют
на вертикально-фрезерном станке в два
прохода. Ранее прорезают прямоугольный
паз цилиндрической концевой фрезой, а
затем окончательно обрабатывают паз
фрезой соответствующего профиля
(рис. 11 к, л).
Шпоночные
пазы открытые обрабатывают
на горизонтально-фрезерных станках
дисковыми фрезами (рис. 11о), а закрытые
— на
вертикально-фрезерных станках концевыми
(рис. 11м)
или
специальными шпоночными фрезами.
Фасонные
поверхности обрабатывают
фасонными фрезами соответствующего
профиля (рис. 11л, р)
преимущественно
на горизонтально-
фрезерных
станках, а сложные пространственные
фасонные поверхности — на специальных
копировально-фрезерных станках.
Сложные
поверхности, представляющие
собой сочетание горизонтальных,
вертикальных и наклонных плоскостей,
а иногда и криволинейных поверхностей,
часто фрезеруют набором фрез на
горизонтально- и продольно-фрезерных
станках (рис. 11с).
Фрезерные
станки имеют весьма широкую область
применения
и разделяются на две основные группы:
станки общего назначения
и специализированные. К первой группе
относятся станки консольные и
бесконсольные, продольно-фрезерные,
станки непрерывного фрезерования
(карусельные и барабанные). Ко второй
группе относятся станки копировально-фрезерные,
зубофре-зерные,
резьбофрезерные, шпоночно-фрезерные
шлицефрезер-ные
и др. Типоразмеры станков характеризуются
площадью рабочей
(крепежной) поверхности стола или
размерами обрабатываемой
заготовки (при зубо- и резьбообработке).
Приспособления
для установки и
закрепления
заготовок на фрезерных
станках —
это различные прихваты, подставки,
угловые плиты,
призмы, машинные тиски, столы и
вспомогательные инструменты, механизирующие
и автоматизирующие закрепление заготовок
и тем самым сокращающие вспомогательное
время.
Прихваты
(рис. 5.10, а)
используют
для закрепления заготовок или
каких-либо приспособлений непосредственно
на столе станка
с помощью болтов. Нередко один из концов
прихвата Попирается
на подставку 1
(рис.
5.10, б).
Если
при обработке заготовок необходимо
получить плоскости,
расположенные под углом одна к другой,
то применяют угловые.
Рис.
5.8. Установка торцовых
насадных фрез на шпиндель станка: 1
—
фреза; 2
—
шпонка; 3
—
винт;
4
—
шпиндель
Рис.
5.9. Установка концевых фрез с цилиндрическим
хвостовиком в патроне:
1— фреза;2
— цанга;
3
—
гайка; 4
—
патрон
Машинные
тиски могут быть простыми неповоротными
(рис.
5.12, а),
поворотными
(поворот вокруг вертикальной оси, рис.
5.12, б),
универсальными
(поворот вокруг двух осей, рис. 5.12, в)
и
специальными (например, для закрепления
валов, рис. 5.12, г):
с
ручным, пневматическим, гидравлическим
или пневмогидравлическим
приводом.
Столы
для установки и закрепления заготовок
бывают неповоротными
(рис. 5.13, а)
и
поворотными (рис. 5.13, б)
с
ручным, пневматическим,
гидравлическим или электрическим
приводом. Поворотные
столы позволяют обрабатывать на станке
фасонные поверхности заготовки, а также
применять метод непрерывного фрезерования,
когда во время обработки одной заготовки
уже готовые
детали снимают и на их место устанавливают
новые заготовки. Непрерывное вращение
стола обеспечивает отдельный привод
или привод станка.
2
3 4
Рис.
5.10. Прихваты и подставка:
а
—
прихваты для крепления детали
непосредственно на столе станка; б
—
прихват,
опирающийся на подставку: 1 — подставка;
2
—
прихват; 3
—
болт; 4
—заготовка
Рис.
5.11. Угловые плиты: а
—
обычные; б
— универсальные,
допускающие поворот вокруг одной оси;
в
универсальные,
допускающие поворот вокруг двух осей
Рис.
5.12. Машинные тиски: а
—
неповоротные; б
—
поворотные; в
—
универсальные; г
—
специальные
Р
ис.
5.13. Столы:
а
— неповоротный;
б
—
поворотный: / — кронштейн для крепления
стола на станке;
2
—
стопор; 3
—
шкала отсчета угла поворота; 4
—
рукоятка ручного попорота
Нередко
на фрезерных станках (как и на токарных)
для закрепления заготовок, имеющих
цилиндрические поверхности, используют
кулачковые поводковые и цанговые патроны
(рис. 5.14).
Значительного
сокращения вспомогательного времени
и повышения
производительности труда при фрезеровании
достигают благодаря
применению механизированных и
автоматизированных зажимных
приспособлений, которые в условиях
крупносерийного
производства нередко используют вместе
с загрузочными устройствами.
При
работе на фрезерных станках для
закрепления заготовок широко
применяют универсально-сборные
приспособления (УСП), которые
собирают из готовых нормализованных
взаимозаменяемых
деталей (рис. 5.15). После обработки на
станке партии заготовок
такое приспособление разбирают и из
его деталей конструируют
новые приспособления. Универсально-сборные
приспособления
позволяют значительно сократить сроки
на проектирование
и изготовление устройств, необходимых
для закрепления заготовок,
что особенно важно в условиях единичного
и мелкосерийного
производства.
Рис.
5.14. Патроны:
а
—
кулачковый: / — кулачки; 2—
корпус; 3—
коническая шестерня с отверстием под
ключ; 4
—
зубчатая рейка для перемещения кулачков;
б
—
поводковый: / — поводок;
2
—
винт крепления поводка; 3
—
скоба для крепления поводка; 4
—
задний
центр; 5 — винт крепления заготовки; 6
—
заготовка; в
—
цанговый: / — винт
крепления патрона; 2
—
хвостовик; 3
—
цанга; 4
—
заготовка
Какие бывают режимы резания при фрезеровании?
Содержание
- Скорость резания
- Глубина резания
- Виды подачи
- Ширина
- Рекомендации по выбору режима
- Для алюминия
- Для дерева
Фрезерование — это способ обработки различных поверхностей фрезой. Во время работы станка режущий инструмент с зубьями совершает вращение вокруг своей оси, в то время как материал заготовки поступает на него. В результате происходит отделение слоя металла, сплава или древесины в виде стружки и обработка поверхности. Сегодня большинство станков для фрезерной обработки снабжены числовым программным управлением, что позволяет работать оборудованию бесперебойно в автоматическом режиме. Рассмотрим основные характеристики, влияющие на работу фрезерного станка.
Скорость резания
Основной тип движения при фрезеровании — вращение режущего элемента. Оно оценивается показателем скорости. Для фрезы это путь в метрах (м), который преодолевают по окружности режущие кромки её зубьев за 1 минуту. Параметр характеризует быстроту работы фрезерного станка, а также скорость снятия слоя материала с обрабатываемой поверхности, измеряется в м/мин.
На практике скорость фрезеровки вычисляется по справочным таблицам или с помощью специально разработанных калькуляторов. Технически фрезеровщик не может управлять этим параметром, он может регулировать другой показатель, от которого зависит скорость — частоту вращения шпинделя.
Сегодня среднестатистическое оборудование рассчитано на работу от 12 до 24 тыс. об/мин, что, к примеру, соответствует скорости резания 100-400 м/мин для пятимиллиметровой фрезы.
Перед работой на станке мастер составляет схему, где учитывает все параметры рабочего оборудования. Скорость резания выбирается с учётом эксплуатационных характеристик станка, глубины резания, вида обрабатываемого материала и скорости его подачи на станок. Отличия в скорости обработки различных материалов определяются степенью их прочности, упругости и пластичности.
- Нержавеющая сталь. Оптимальная скорость резания — 45-100 м/мин. Добавление в состав различных элементов повышает твёрдость сплава, что может отрицательно сказаться на состоянии высокоскоростного оборудования. В таком случае придётся пожертвовать качеством обрабатываемой поверхности взамен за сохранность фрезы.
- Бронза и латунь. Оптимальная скорость обработки — 90-170 м/мин и 130-320 м/мин соответственно. Это относительно мягкие сплавы, состав которых позволяет обрабатывать их быстрее, получая гладкую поверхность. При нагревании они частично размягчаются, что рекомендуется учитывать при обработке бронзовых и латунных заготовок.
- Алюминий. Оптимальная скорость резания — 200-430 м/мин. Это очень мягкий металл, который обладает низкой температурой плавления. Обработка его не составляет трудностей, однако, на высоких скоростях из-за повышенного размягчения металла можно случайно повредить заготовку.
- Полимерные материалы. Оптимальная скорость резания — 100-200 м/мин. Акрил и другие пластмассы обладают средними показателями твёрдости. Температура их плавления ещё ниже, чем у металлов и сплавов, поэтому не стоит злоупотреблять высокими скоростями вращения при их обработке.
- Древесина. Оптимальная скорость резания — 230-310 м/мин. Материал по свойствам абсолютно не похож на предыдущие. Дерево обладает хорошими параметрами упругости и пластичности, но даже самые твёрдые породы, такие как лиственница и дуб, имеют свойства растрескиваться от механических воздействий. При обработке древесины выбирается высокая скорость, а слои удаляются постепенно. При этом стоит учитывать возможность её самовоспламенения из-за сильного нагрева, что усложняет процесс обработки.
Скорость резания всегда требует точных расчётов. Незначительные отклонения как от минимальной, так и максимально допустимой величины могут привести к поломке фрезы, изнашиванию частей станка и, соответственно, к порче обрабатываемой заготовки. Специалисты рекомендуют занижать фактическую скорость на 10-15% от максимально допустимой. Это позволит сохранить качество обрабатываемой поверхности, а также производительность труда без механического износа оборудования.
При работе с любым материалом рекомендуется учитывать обязательный нагрев фрезы вследствие длительной работы оборудования. Это явление отрицательно сказывается на состоянии режущего инструмента и обрабатываемого материала, поэтому сегодня большинство фрезерных станков оборудуются системой подачи смазочно-охлаждающей жидкости.
Глубина резания
В процессе обработки детали на фрезерном станке режущий инструмент, сталкиваясь с поверхностью заготовки, снимает с неё слой материала в виде стружки. Величина снятого слоя за один проход фрезы и есть глубина резания. Параметр измеряется в мм и рассчитывается как разность между исходной и снятой в ходе фрезерования поверхностью.
Рабочий процесс фрезерной обработки обычно включает несколько проходов по заготовке и проводится в два этапа: черновой и чистовой. Первый предполагает максимальное снятие припуска детали, т. е. утилизируемой части материала, и проводится в 2-3 прохода. При этом выбираются наиболее допустимые значения глубины фрезерования при как можно меньшей скорости. Такой режим позволяет снять достаточное количество материала при незначительных нагрузках на оборудование.
Поверхностный слой заготовки получается негладким, шероховатым, поэтому далее следует чистовой этап, который обычно проводится в 1 проход. В ходе него фреза работает на максимально возможной скорости при незначительной глубине резания и как бы шлифует обрабатываемую поверхность, снимая незначительный слой материала.
На заметку! Если величина припуска детали минимальная и составляет несколько миллиметров, достаточно всего одного чистового прохода.
Стоит отметить, что глубина фрезерования выбирается по используемому материалу заготовки. К тому же параметр зависит от производительности станка и ограничивается его конструктивными особенностями. При использовании маломощного оборудования с небольшим режущим элементом требуется несколько проходов по заготовке, т. к. силы такого устройства иногда недостаточно, чтобы снять весь припуск сразу.
Регулировку фрезы по металлу можно сравнить с таковой у мотоблока. Плуг вспашет землю на такой глубине, которую вы заранее ему обеспечите, приложив собственные усилия. В противном случае культивировать он будет неглубоко, а без усилий вообще останется рыть землю на месте.
Виды подачи
Заготовка при обработке перемещается относительно оси станка, т. е. фрезы, по одной из трёх осей: продольной (x), поперечной (y) или вертикальной (z). Величина проходимого деталью расстояния называется подачей. Теоретически выделяют 3 вида подачи заготовки.
- На зуб, Sz — это величина перемещения детали при вращении режущего элемента на расстояние между кромками двух зубьев. Единицы измерения: мм/зуб.
- На оборот, So — это величина перемещения заготовки при одном полном обороте фрезы. Рассчитывается по формуле: So = Sz • z, где z — число зубьев режущего элемента. Единицы измерения: мм/об.
- Минутная, Sm — это расстояние, на которое перемещается обрабатываемая заготовка относительно фрезы за одну минуту. Рассчитывается по формуле: Sm = So • n = Sz • n • z, где n — частота вращения режущего элемента (об/мин); z — число зубьев режущего элемента. Единицы измерения: мм/мин.
На практике используется только минутная подача, которая является важной характеристикой режима резания при обработке деталей на фрезерном станке. Она регулируется в зависимости от материала заготовки, вида фрезы, режима резания и мощности оборудования. Параметр обратно пропорционален скорости резания. Так, высокая скорость требует уменьшения величины подачи. В противном случае будет возрастать осевая нагрузка на станок и степень сопротивления фрезы заготовке, что приведёт к быстрому механическому износу или поломке режущего элемента, шпинделя и других деталей установки.
При снижении величины подачи допускается увеличение скорости фрезерования, что в сочетании с небольшой глубиной резания используется для чистовой обработки поверхностей.
Ширина
Фрезерный станок, как правило, технически не способен обработать всю деталь сразу. Фрезеровке подвергается определённая поверхность, которая и является шириной фрезерования. Показатель измеряется в мм и определяет ширину снимаемого слоя материала, которая перпендикулярна его подаче. Фактически это расстояние, на котором кромки зубьев режущего элемента соприкасаются с поверхностью заготовки. Параметр указывается в технологической схеме перед началом обработки детали. Зная значение ширины фрезерования, а также величину заготовки, мастер может заранее определить необходимое количество проходов.
Параметр варьируется в широком диапазоне и зависит от диаметра фрезы. Для каждого режущего элемента ширина фрезерования является константой, так как изменить геометрические показатели невозможно. При большом количестве обрабатываемого материала рекомендуется использовать режущие элементы соответствующих размеров. Это необходимо для того, чтобы снизить время работы на станке, затраты на эксплуатацию оборудования, а также уменьшить показатели нагрузки.
Рекомендации по выбору режима
Выбор правильного режима работы фрезеровочного станка играет важную роль в процессе обработки материалов и изготовления деталей. Точное соотношение рекомендуемых параметров позволит мастеру добиться лучшей производительности при тех же рабочих затратах, уменьшит износ деталей станка и сохранит заготовку в хорошем состоянии. Сегодня специалисты-фрезеровщики разработали большое количество таблиц и технологических карт. Их можно использовать в качестве примера при выборе оптимального режима.
Если готовые схемы для работы отсутствуют, специальные онлайн-калькуляторы или компьютерные программы помогут с расчётом параметров процесса. В них заранее внесены все формулы, мастеру необходимо лишь указать базовые характеристики станка и фрезы.
При выборе технологического режима мастера руководствуются следующими критериями.
- Параметры станка. Технические характеристики оборудования оказывают наиболее значимое влияние на процесс. При работе следует принимать во внимание его возраст. На современных станках с ЧПУ результаты работы будут лучше, чем на оборудовании возрастом 10-15 лет. Связано это и с меняющимися технологиями разработки, и с механическим износом отдельных частей. Именно поэтому следует периодически проверять техническое состояние оборудования, вовремя ремонтировать неисправности и утилизировать брак.
- Также от возраста системы зависит её прочность. Новое оборудование без особых усилий выдержит высокие нагрузки и качественно обработает любые твёрдые сплавы. Более старые модели, в свою очередь, чаще подвержены поломке, поэтому непригодны для работы с такими материалами.
- Другая часть результатов процесса зависит от предустановленных параметров в зависимости от используемого материала. Это касается скорости, которая варьируется в пределах 50-400 м/мин. Рекомендуется начинать работу со средним значением, а в процессе фрезеровки менять его в необходимую сторону. В противном случае высокая частота вращения шпинделя может привести к его поломке, а низкая — испортить материал.
- Станок не должен испытывать сопротивление при работе, поэтому необходимо постоянно регулировать величину нагрузки на ось. Для этого можно менять параметры глубины резания и подачи. Оптимальное значение последнего в начале работы составляет 0,15 мм/зуб.
- Последней особенностью работы фрезеровочного станка является необходимость в его постоянном охлаждении. Для этого современные устройства оборудованы системой подачи смазочно-охлаждающей жидкости в зону обработки. Это существенно снижает нагревание режущих кромок зубьев, что лучше сказывается на состоянии заготовки. Также СОЖ удаляет с материала постоянно образующуюся стружку и пыль.
- Особенности режущей части. Свойства фрезы оказывают существенное влияние на качество процесса. При выборе инструмента обратите внимание на его состав. Для обработки большинства металлов, пластмасс, древесины достаточно обычной фрезы из быстрорежущей нержавейки. При работе с твёрдыми сплавами рекомендуется использовать режущие элементы с тугоплавкими напайками на зубьях. Так инструмент не сломается после нескольких минут работы и не испортит заготовку.
- Имеет значение также диаметр режущего элемента, с увеличением которого пропорционально снижаются скорость фрезерования и подачи, при этом увеличивается ширина резания. Рекомендуется выбирать диаметр, соответствующий глубине обработки и виду используемого материала. Тогда для работы достаточно будет всего нескольких проходов. Качество фрезерованной поверхности зависит от длины режущего элемента, количества зубьев и угла заточки их режущей кромки. Большинство фрез изготавливается с 4-мя зубьями, что позволяет добиться лучшего соотношения между скоростью процесса и состоянием заготовки.
- Особенности материала – самый важный критерий во всем процессе. Именно от свойств заготовки зависит большинство настраиваемых параметров. Среди особенностей материала важны степень твёрдости, пластичности и упругости. Первый параметр прямо влияет на прочности детали и её износостойкость. С другой стороны, обработка таких материалов существенно усложняется. Всегда есть риск износа или поломки оборудования. Иногда это приводит к порче заготовки.
Поэтому для обработки твёрдых металлов и их сплавов, например, калёной стали или титана, следует снижать глубину и скорость резания станка, а также использовать фрезы с тугоплавкими напайками. Показатели пластичности и упругости существенно зависят от величины нагрева материала. При работе с такими сплавами, как бронза или латунь, эти свойства могут оказаться полезными, в то время как для других металлов они окажутся причиной порчи заготовки.
Для алюминия
Среди всех использующихся металлов при изготовлении деталей этот самый мягкий. В сочетании с высокой степенью пластичности алюминий легко подвергается обработке. В то же время стоит учесть его относительно низкую температуру плавления — 660 C, что может привести к размягчению заготовки при сильном нагревании фрезы.
Обработку алюминия рекомендуется начинать со скорости 250-300 м/мин и постепенно повышать её до 400-420, если станок оборудован системой подачи СОЖ. Глубина резания при этом должна быть минимальной. В таком режиме фреза будет быстро снимать несколько миллиметров слоя поверхности, что позволит сохранить структуру и свойства металла.
Для дерева
Древесина, в зависимости от породы, характеризуется различными параметрами твёрдости. Большинство видов при этом обладает хорошей упругостью и пластичностью, которые, к сожалению, пропадают при полном высушивании. Такой материал необходимо обрабатывать на высоких скоростях, чтобы избежать появления трещин и дефектов. Оптимальный режим — 250 м/мин при небольшой глубине.
Независимо от материала, любой режим резания считается оптимальным, если все параметры сочетаются между собой разумно, обеспечивают максимальную производительность и точность работы. Сегодня практически любой человек, воспользовавшись справочными пособиями и калькуляторами, способен за несколько дней овладеть навыками фрезерования. Однако одних таблиц для выбора правильного режима недостаточно: необходимы многолетний опыт и знания всех особенностей работы.
Время чтения: 15 мин.
Фрезерование – это операция по обработке металла методом резания. Режущим инструментом выступает вращающаяся фреза, заготовка подается линейно. Фреза может работать торцевой стороной или периферией, заготовка перемещается продольно, поперечно или вертикально – это движение подачи.
На фрезерном станке можно производить разные виды обработки заготовок — профилировать торцевые поверхности, наносить узоры и гравировку, сверлить отверстия под резьбу, нарезать шлицы, пазы, выбирать канавки и многое другое. Для разных операций предназначены разные виды фрез. Расширяет функционал станков возможность обработки не только металлов, а также композитных материалов и даже дерева, пластика, стекла и других твердых материалов.
Процесс производства пресс-формы на современном фрезерном станке с ЧПУ. Источник https://www.123rf.com/
Принцип обработки на фрезерных станках предполагает прерывистую обработку заготовки: каждый зуб фрезы погружается в металл на разную глубину и удаляет стружку разной толщины.
Фрезерование бывает:
- цилиндрическим – в процесс резки вовлечены периферийные зубья фрезы, обрабатывается плоская поверхность, которая расположена параллельно оси вращения режущего инструмента;
- торцевым – резка производится торцевой и периферийной частями фрезы, глубина реза увеличивается к центру и уменьшается в точках выхода из взаимодействия с заготовкой, так создаются канавки, пазы, срезаются торцы, черновая обработка габаритов заготовок.
а) цилиндрическое фрезерование, б) торцевое фрезерование
Все виды работ, выполняемых на фрезерных станках, представляют собой сочетание этих двух методов обработки.
Встречное и попутное фрезерование
Самые распространенные методы фрезерования – встречное и попутное.
Встречное, или «против подачи», – когда фреза (ее режущие кромки) и обрабатываемая заготовка двигаются навстречу друг другу.
Плюсы:
- мягкая резка с невысокой нагрузкой на узлы станка;
- минимальная деформация металла;
- высокая производительность обработки.
Минусы:
- требуется обращать особое внимание на надежную фиксацию заготовки, встречное движение подачи противодействует силам резания и деталь буквально “отрывает” от стола, зоны крепления;
- при работе на высоких режимах возможен скорый износ инструмента — важно правильно подобрать режимы резания;
- образующаяся стружка нередко попадает, застревает прямо в точках соприкосновения режущей кромки и снимаемого слоя металла.
Попутное, или «по подаче», – когда режущий инструмент вращается в том же направлении, в котором двигается заготовка.
Плюсы:
- в условиях отсутствия противохода нет необходимости сильно закреплять заготовку к столу, достаточно прижимной силы в процессе резания, силы резания обеспечат жесткость сопряжения;
- режущие кромки фрезы при перемещении вдоль движения затупляются меньше;
- стружка не попадает под режущую кромку;
- съем металла производится плавно, удается добиться оптимального уровня шероховатости.
Минусы:
- метод не подходит для обработки грубых поверхностей, обдирочных операций, в основном это чистовые операции;
- твердые вкрапления, неоднородность слоя металла, заготовки после поверхностного упрочнения ( например Термообработки) может приводить к скорому износу режущей кромки;
- станина станка должна быть очень жесткая во избежание вибраций.
Выбор метода обработки зависит от поставленных задач и типа материала, из которого изготавливают изделие на фрезерном станке. Обдирочные работы выполняются исключительно против подачи, этот же метод выбирают при наличии в материале твердых включений. Мягкие сплавы лучше обрабатывать по подаче.
Виды и назначение фрез
Фреза, лезвийный инструмент, который представляет собой тело вращения, на поверхности которого расположены режущие элементы — зубья. Наибольшее распространение имеют фрезы с неперетачиваемыми пластинками (СМП) из твердосплавных материалов. Вид фрезы выбирают в зависимости от того, какие работы будут выполняться на фрезерном станке ЧПУ.
Конструктивно выделяют следующие виды фрез:
- кольцевые, корончатые сверла – для высокоточного скоростного сверления;
- цилиндрические – могут быть прямозубными или иметь винтовые зубья, первые используются для обработки прямых поверхностей, вторые – разных;
- фасонные – имеют острые или затылованные зубья и используются для фасонной обработки поверхностей;
- червячные – спрофилированный червяк с режущими зубьями, применяемый для создания цилиндрических и шлицевых зубчатых колес;
- концевые – предназначены для создания пазов и уступов;
- угловые – специально разработаны для обработки углов, криволинейных поверхностей;
- дисковые – режущие диски, главным образом применяемые для резки заготовок и создания канавок;
- торцевые – разновидность дисковых с большим количеством монолитных или сменных режущих пластин, используются для чистовой обработки.
Разные виды режущего инструмента для обработки заготовок на фрезерном станке.
Зубья фрезы могут быть остроконечными и затылованными. Первые считаются универсальными, могут исполняться в форме трапеции, параболы, с двойной спинкой. Вторые в основном применяются для фасонной обработки изделий, задняя поверхность таких зубьев имеет вид архимедовой спирали.
На рисунке отмечены основные конструктивные элементы зуба фрезы и углы, влияющие на выбор инструмента
Какие параметры определяют режим работы
- Скорость резания – путь, который проходит в минуту или секунду максимально удаленная от оси вращения точка режущей кромки.
- Подача: на зуб – время перемещения детали/фрезы за один шаг, то есть угол между зубьями; на 1 оборот – перемещение за время полного оборота фрезы; минутная подача – перемещение за минуту.
- Глубина резания – расстояние между поверхностями до и после обработки.
- Ширина обработки – ширина зоны, обработанной за один ход фрезы.
С увеличением диаметра фрезы скорость резания возрастает, зубья лучше охлаждаются, так как удлиняется промежуток времени их пребывания вне зоны резки. Возможности увеличения диаметра инструмента ограничены мощностью, жесткостью станка и размером посадочного отверстия в шпинделе.
Образование стружки при фрезеровании
Процесс образования стружки при фрезеровании сопровождается теми же явлениями, что и при точении. Например, деформации, теплообразование, образование нароста, вибрации, износ инструмента и пр. Но при обработке методом фрезерования имеются свои особенности. Резец при точении находится под постоянным действием стружки вдоль всей длины обработки. При фрезеровании зуб за один оборот фрезы находится под действием стружки незначительное время. Большую часть оборота зуб не участвует в резании, за это время он охлаждается, что положительно отражается на его стойкости. Вход зуба в контакт с обрабатываемой заготовкой сопровождается ударом о его режущую кромку; ударная нагрузка снижает стойкость зуб; фрезы.
Процесс образования стружки фрезой со сменными пластинами
Что влияет на качество обработки
- Попадание стружки в зону резки – возможно появление брака, повреждение фрезы, потеря качества шероховатости уже обработанной поверхности.
- Чрезмерное повышение температуры в зоне резки – появляются наклепы, края режущих кромок инструмента становятся более твердыми и менее прочными.
- Вибрации – затрудняют нормальное течение процесса резания, снижают итоговое качество — исполнение размеров, шероховатости и др. технических требований.
Для изготовления качественного изделия на фрезерном станке нужно правильно подобрать режимы резания и исключить влияние негативных факторов: обеспечить отвод стружки, подачу СОЖ в зону резания, обеспечить надежное крепление приспособлений и заготовки, жесткость СПИД.
Основные этапы настройки станка с ЧПУ
Наладчик получает сменное задание. Необходимую сопроводительную документацию по заготовке, технологию обработки и сам чертеж изделия. Отсюда он понимает, какие будут применены технологии, программы обработки, карты наладки. Далее он получает необходимый режущий и мерительный инструмент, если тот отсутствует на рабочем месте. Как правило, часть инструментов находятся в распоряжении наладчика у станка постоянно.
На фотографии изображен фрезерный станок ЧПУ и наладчик станков с программным управлением в процессе наладки
Следующим этапом он обмеряет заготовку и подготавливает к установке на рабочий стол станка, или в универсальное специальное приспособление, зажимное устройство.
После подбора необходимого инструмента согласно карте наладки, наладчик загружает инструмент в магазин станка, и каждая фреза или сверло должны пройти этап определения их положения относительно координат станка и обрабатываемых поверхностей заготовки. Заполняет параметры – диаметр фрез ( для дальнейшей коррекции), потом их привязывает или вручную методом касания, или через эталонные образцы, или через измерительные устройства – датчики через присвоенные параметры – номера позиций и их корректора в системе ЧПУ. (Статья об этом тут.)
В зависимости от этапа технологии обработки заготовки – это может быть черновая или уже чистовая операции – выбирают необходимую программу обработки. Если она не сложная, то ее можно написать прямо на стойке ЧПУ. Затем производят первую обработку. Вообще, рекомендуют сперва отвести инструмент от заготовки и пройтись по программе вне детали (по воздуху) для исключения аварийных ситуаций, чтобы понять, что с программой все хорошо. И уже после можно запускать обработку уже «по детали».
В процессе обработки 1-ой годной детали необходимо внимательно – «покадрово» – контролировать управляющую программу и производить контрольные замеры исполнения полученных на данном этапе размеров. Для дальнейшего нормального течения процесса обработки по необходимости корректируют режимы резания, частоту вращения инструмента, величину подач, как рабочих, так и холостых, точки подхода инструмента к заготовке, изменяют глубину резания, корректируют положение инструмента в осях перемещений по УП (износ или геометрические параметры).
Если все хорошо – мы получаем годную деталь. И далее по накатанной – снимаем готовую, крепим следующую.
Детально об устройстве фрезерного станка читайте в отдельном материале нашего блога.
Самые востребованные станки для фрезерной обработки:
- вертикально-фрезерные;
- горизонтально-фрезерные;
- горизонтально-расточные.
Подробная информация, как правильно выбрать станок с разбором основных ошибок представлен в этой статье.
Возможно, вы уже задавались вопросом расчёта режимов резания, но при этом продолжали ломать фрезы и не понимать, что происходит? Почему так? Почему, например, вы уменьшаете подачу, а фреза всё равно работает в неправильном режиме? Звенит, издает нехарактерный звук и, как результат, быстро тупится и ломается. В этой статье вы найдете ответы на интересующие вас вопросы:
- Почему не стоит полагаться на режимы резания из каталогов
- Какие параметры входят в расчёт режимов резания
- Как назначать обороты и подачу по внешнему виду инструмента
- Как работать с различными материалами
- Какой методики расчёта режимов резания придерживаться
Сразу оговорюсь, что в начале статьи будет некоторая вводная информация, предназначенная для общего понимания. Рекомендую читать все по порядку, чтобы не только пользоваться методикой расчёта режимов резания, но и понимать, что откуда берется, и почему именно так. Данная статья в первую очередь рассказывает о расчёте режимов резания для ЧПУ станков, так как на них нет возможности «пощупать» усилие в процессе работы, как это делают на универсальных станках. На ЧПУ оборудовании нужно изначально назначать правильный режим, и только потом вносить небольшие коррективы в пределах ±20%.
Режимы резания из каталогов.
Мы часто слышим вопрос от наших клиентов: «Какие обороты и подачу поставить на ту или иную фрезу?» Можно ответить кратко: «Посмотрите по каталогу производителя!» Но к сожалению, это не является правильной рекомендацией по нескольким причинам:
- Продавец зачастую завышает режимы резания на свою продукцию на 20-40%, чтобы иметь конкурентное преимущество перед другими поставщиками.
- Продавец в большинстве случаев не имеет практического опыта работы с режущим инструментом и различными материалами.
- И самое главное – когда вы соберетесь фрезеровать, каталога под рукой не окажется, а интернет предательским образом отключится!
На что тогда полагаться? На методику расчёта режимов резания, которую мы для вас подготовили! Она является результатом личного опыта работы на фрезерных ЧПУ станках с различными материалами. Возможно, что полученные режимы будут не самыми выигрышными в плане времени обработки, но они точно сохранят ваш инструмент и позволят работать в безопасном для него режиме, что наиболее важно для начинающих операторов ЧПУ!
Параметры режимов резания.
Как видно из рисунка, в режимы резания для фрезы входит 3 параметра:
- S – обороты (частота вращения шпинделя)
- F – подача (скорость, с которой движется инструмент)
- P – величина съема (слой материала, срезаемый фрезой)
Это именно та последовательность, с которой мы производим расчёт режимов резания для фрезы – далее будем её придерживаться. Данные буквенные обозначения используются в том числе и в самой программе на ЧПУ станок. Например, чтобы включить шпиндель на 1500 об/мин по часовой стрелке, мы записываем в программу «S1500 M3». Или, чтобы сделать проход вправо на 50 мм с подачей 300 мм/мин, мы пишем в программе «G1 X50 F300».
Внешний вид инструмента.
Дадим краткую характеристику фрез по внешнему виду, которую следует учитывать при расчёте режимов резания. Рассмотрим три примера:
Данная фреза имеет острые режущие кромки, большой угол завивки винтовой канавки, она 2-х зубая и не имеет покрытия. Все эти факторы свидетельствуют о том, что перед нами инструмент, идеально подходящий для фрезерования цветных металлов, а также вязких материалов (меди, пластиков), которые подвержены сильному нагреву и оплавлению в процессе резания. Такая фреза хорошо подходит для чистовых обработок с небольшими усилиями резания, но не подходит для сталей и черновых обдирок заготовок с большими съёмами.
Данные фрезы имеют более тупые углы заточки режущих кромок, они 4-х зубые (более жесткие) и имеют слой покрытия, уменьшающего трение и увеличивающего твёрдость поверхностного слоя. Всё это свидетельствует о том, что этот инструмент идеально подходит для обработки сталей, они достаточно прочные для работы с большими подачами, подходят в том числе и для черновых обдирок, при этом позволяют достичь хорошей чистоты поверхности.
На этом рисунке мы видим составную фрезу, состоящую из корпуса и твердосплавных пластинок. Как правило, такие фрезы имеют диаметр от 20 мм и более, так как цельный твердосплавный инструмент такого размера становится экономически не выгодным. Предназначение и поведение данных фрез зависит от установленных на них пластинок. Если пластинки без покрытия (блестящие) и имеют остро заточенные режущие кромки, значит, они предназначены для обработки цветных металлов. Если пластинки имеют покрытие и на ощупь кажутся тупыми, то они предназначены для сталей. По опыту использования, покрытие «золотистого» цвета хорошо подходит под нержавеющие стали, а покрытие черного цвета — под обычные конструкционные стали. Фрезы с твердосплавными пластинками «любят» большие подачи.
Вывод: не обязательно заглядывать в каталог или на сайт производителя режущего инструмента и искать у них калькулятор расчёта режимов резания – учитесь идентифицировать фрезы по их внешнему виду. Разновидностей не так много.
Особенности работы с различными материалами.
Здесь мы не будем вдаваться в подробности, а просто дадим список распространённых материалов и опишем особенности работы с ними. Список составлен по принципу от легкообрабатываемых (некапризных) материалов к более сложным.
- Пластики (модулан, капролон, фторопласт) – наиболее легкообрабатываемые материалы. Можно обрабатывать как на высоких, так и на низких оборотах, как с высокими, так и с низкими подачами. На инструмент действуют небольшие силы резания, можно давать большое заглубление. Обращать внимание нужно только на оплавление материала и в случае нагрева снижать обороты.
- Цветные металлы (дюраль, латунь, бронза) – также очень легко обрабатываемые материалы. Обрабатываются на высоких скоростях, стружка сходит легко, не перегреваются, на инструмент действуют небольшие силы резания. Можно обрабатывать без СОЖ (смазочно-охлаждающая жидкость). Режимы резания можно корректировать в большом диапазоне без боязни повредить инструмент.
- Медь, алюминий (мягкие алюминиевые сплавы типа АМГ) – всё то же самое, что и для цветных металлов, но с одной особенностью. В случае превышения скорости происходит резкий нагрев и оплавление материала, что моментально забивает фрезу – она перестаёт резать и сразу ломается. Для предотвращения этого явления нужно применять СОЖ.
- Конструкционные стали – для них обязательно применение фрез именно под стали с 3/4-мя зубьями и желательно с покрытием. Обработка ведется легко, если станок имеет достаточную жёсткость. Для сталей не стоит применять большие обороты, а также не стоит сильно снижать подачу, так как в этом случае фреза не режет материал, а «зализывает», что приводит к нагреву и ухудшению качества обрабатываемой поверхности. Величина снимаемого материала одним зубом (подача на зуб фрезы) должна быть достаточной.
- Нержавеющая сталь, титановые сплавы – наиболее капризные материалы в обработке. Требуют применения специального инструмента, подходящего для обработки этих материалов. Не «любят» большие обороты и подачу, требуют интенсивного охлаждения СОЖ. Не стоит усердствовать с глубиной врезания и снимать более чем 1/3 от диаметра фрезы.
Методика расчётов режимов резания при фрезеровании.
1. Определяемся с первым параметром – оборотами фрезы (S).
Обороты рассчитываются исходя из оптимальной скорости резания для того или иного материала. Скорость резания – это не обороты! Это скорость, с которой режущая кромка движется относительно материала в метрах в минуту. Скорость резания – это отправная величина для расчёта, но не конечное знание оборотов, которое нам нужно. Условно разделим материалы на цветные металлы и стали, а фрезы на монолитные и с пластинками. Привожу рекомендуемые (подобранные опытным путем) скорости резания.
Монолитные:
- Цветные металлы 120-160 м/мин
- Стали 60-100 м/мин
С пластинками:
- Цветные металлы 180-220 м/мин
- Стали 120-160 м/мин
Формула расчёта скорости резания выглядит так:
Но нас всё-таки интересуют обороты, поэтому выразим S и получим формулу расчёта оборотов шпинделя:
где:
- S – обороты шпинделя (об/мин)
- V – скорость резания (м/мин)
- D – диаметр фрезы (мм)
Точности тут не требуется, полученные обороты можно округлять в любую сторону. Также стоит оговориться, что если Ваш станок не выдает высокие обороты, то не стоит беспокоиться – ставьте те, которые выдает, и работайте. Просто это будет немного медленнее, чем могло бы быть, так как подача будет напрямую зависеть от оборотов – чем меньше обороты, тем меньше будет подача.
Исходя из этих параметров, можно составить таблицу с рекомендациями оборотов для наиболее распространённых диаметров фрез.
2. Определяемся со вторым параметром – подачей (F).
В первую очередь это актуально для концевых монолитных фрез, так как они наиболее подвержены поломке в случае завышения или занижения скорости подачи. Для фрез с твердосплавными пластинками подачу можно брать исходя из расчёта 0.1-0.2 мм на зуб. При этом подача 0.1 мм на зуб будет идеальна для инструмента небольшого диаметра (20-30 мм), а 0.2 мм стоит применять только для более крупных фрез (от 40 мм в диаметре и более).
Для определения скорости подачи воспользуемся простой формулой:
F = D * k * N * S
где:
- F – подача (мм/мин)
- D – диаметр фрезы (мм)
- K – коэффициент 0.006-0.008
- N – количество зубьев фрезы
- S – обороты (об/мин)
Поясняю:
Умножая диаметр инструмента на коэффициент k, мы получаем допустимую подачу на один зуб фрезы. Например, возьмем инструмент диаметром 8 мм – у нас получится 8*0.007 = 0.056 мм/зуб. Если один зуб фрезы будет снимать меньше, то может произойти «зализывание» материала, нагрев и поломка. Если на один зуб будет приходиться больше, то возможна поломка фрезы из-за значительного увеличения сил резания. Далее, подачу на один зуб фрезы мы умножаем на количество зубьев (например, 3 зуба), получаем: 0.056*3 = 0.168 мм/об. Это тот путь фрезы, который она будет проходить за один оборот. Нам остаётся только умножить это значение на ранее выбранные исходя из обрабатываемого материала обороты, и готово! 0.168*5600 = 940 мм/мин.
Таким образом, для обработки цветных металлов 3-х зубой фрезой диаметром 8 мм нам необходимо поставить на нее 5600 об/мин и подачу около 900 мм/мин. Вот и весь расчёт!
3. Определяемся с третьим параметром – величиной съёма (P).
Или, другими словами, глубиной фрезерования. Тут всё просто, достаточно придерживаться правила: 1/3 от диаметра инструмента. Например, для фрезы диаметром 6 мм мы выберем величину съёма 2 мм, а для инструмента диаметром 12 мм допустимая глубина фрезерования составит уже 4 мм.
Но есть и нюансы:
- Если вы работаете только краем фрезы, то глубину фрезерования можно значительно увеличивать. Например, при использовании новомодного высокоскоростного фрезерования инструмент входит в материал на всю глубину режущей кромки, при этом величина перекрытия составляет всего около 5%.
- Если вы работаете с труднообрабатываемыми материалами, то правило 1/3 от диаметра может быть губительным для инструмента, возможно величину съёма придется значительно уменьшить.
- Если у вас скоростной шпиндель и нет возможности поставить на инструмент малые (расчётные) обороты, то ставьте больше, которые станок в состоянии выдать. Но при этом значительно уменьшайте глубину резания – это убережет фрезу от поломки, а шпиндель от перегрузки.
- Если у вас недостаточно жёсткий станок, то забудьте про большие съёмы по глубине в принципе. Самым оптимальным будет съём по 0.5-1 мм при рабочем диаметре фрезы не более 6 мм.
Заключение:
Для расчёта режимов резания при фрезеровании действуйте следующим образом:
- Определитесь с обрабатываемым материалом и внимательно осмотрите фрезу.
- Выберите из таблицы подходящие для нее обороты исходя из материала, типа фрезы и её диаметра.
- По формуле расчёта режимов резания посчитайте необходимую подачу. Для труднообрабатываемых материалов выбирайте коэффициент 0.006, а для легкообрабатываемых – 0.008.
- Определитесь с глубиной фрезерования, учитывая наши рекомендации.
Задача для закрепления:
— необходимо фрезеровать паз шириной 10 мм на глубину 6 мм
— концевой 3-х зубой фрезой диаметром 10 мм
— обрабатываемый материал: сталь
Ответ:
S (обороты) = 2500 об/мин
Кол-во проходов = 2
P (съём) = 3 мм
F (подача) = 525 мм/мин
Скорость и режимы резания при фрезеровании: как посчитать по таблице
20.03.2020
- Суть процесса
- Особенности выбора режима резания фрез при фрезеровании
- Выбор инструмента
- Как посчитать режимы и скорость резания по параметрам
- Рекомендации при выборе режима на практике
- Полезные советы
- Вывод
Фрезерный станок – универсальный аппарат для металлообработки, на нем можно сделать большинство операций в короткие сроки. Но для каждой отдельной процедуры, для каждого обрабатываемого материала необходимо подстраиваться. Мы расскажем, как произвести расчет режимов и скорости резания при фрезеровании по формулам и таблицам.
Суть процесса
Технологически это снятие верхнего слоя сырья с поверхности. В результате получается стружка, которая отводится в выбранном направлении. Смысл в том, что режущая кромка касается определенных точек – тех, где необходимо создать паз или другое отверстие.
Заготовка из металла, пластика или дерева, оргстекла помещается на прочную станину и надежно закрепляется несколькими зажимами. Далее выбирается подходящее оборудование. Он зажимается в станке на движущимся шпинделе.
Резец погружается в материал на определенную глубину. Когда включается электродвигатель, резак начинает движение – вокруг своей оси или вперед, как при дисковом инструменте. Одновременно с этим выбирается подача – это передвижение заготовки и/или режущей кромки.
Вместе с нажимом под воздействием механического давления происходит обработка – постепенно убирается верхний слой поверхности.
Цель фрезеровки – глубокая черновая или чистовая металлообработка, а также в зависимости от фрезы и задачи, это может быть:
- создание определенного профиля – вырезка канавок, пазов;
- нарезка зубцов на зубчатых колесах и прочих деталях;
- поддержание определенной формы элемента;
- сверление отверстий;
- нарезание внутренней и внешней резьбы;
- обрезка торцов;
- художественное вытачивание узоров и гравировка.
Весь процесс отличается прерывистым характером – фрезеровщик делает паузы, чтобы направить резец, задать скорость и направление движения. Основные подачи:
- вращательная;
- перемещение по горизонтали и вертикали.
Особенности выбора режима резания фрез при фрезеровании
Стоит отметить, что есть несколько этапов металлообработки:
- Обдирной – очень грубое снятие верхнего слоя, часто заключается в устранении явных дефектов, а также в том, что убирается ржавчина.
- Черновой – обработка первичного типа, когда нужно устранить поверхность и снять стружку. При этом класс точности и шероховатости довольно низкий. Припуск оставляется достаточно большой – до 7 мм.
- Получистовой. На этой стадии производится зачистка и подготовка к финальным этапам. Особенность в том, что выбирается более тонкий инструмент, стружка получается тоньше, а точность увеличивается до 4-6 класса.
- Чистовой – Часто это последний уровень обработки, достигается оптимальная шероховатость. Размеры подгоняются очень точно.
- Тонкий (финишный) – сверхточное фрезерование на высоких скоростях. Снимается минимальная металлическая пыль.
- Шлифование – применяются резцы с напылением из абразивных частиц.
В зависимости от этапа делается расчет режимов резания при фрезеровании – его можно произвести онлайн или воспользоваться формулами и таблицами. Соответственно, выбирается тип сверла.
Выбор инструмента
В качестве оснастки фрезерных станков используются различные фрезы. Это приспособления для резки, изготовленные из инструментальной стали высокой прочности. Есть множество признаков, согласно которым происходит классификация:
- по материалу их режущих элементов;
- по расположению режущих частей зубьев;
- по виду заточки зубьев;
- по направлению зубьев (винтовые, наклонные и т.д.);
- по конструкции изделия (составное, цельное, сборное);
- по виду крепления режущих элементов.
- по назначению – название резца созвучно с задачей фрезеровщика. Рассмотрим некоторые из разновидностей.
Для плоских поверхностей
В основном при обработке плоскостей применяются цилиндрические и торцевые фрезы, а также дисковые – для распиловки. Если инструмент в виде цилиндра, то он может быть нескольких типов – с цельными или сменными режущими краями. Крупные монолитные обычно применяются на первых стадиях металлообработки, при черновых работах, в то время как небольшие и разборные – для чистовой.
Торцевой резец больше подходит для протяженных заготовок. Тогда ее зубья могут быть по бокам – с торца. Если это большой складной инструмент, то его используют, соответственно, для широких поверхностей.
Использование твердосплавных резцов обязательно, если вы имеете удовольствие работать с плохо обрабатываемыми тугоплавкими материалами. Но стоит учесть, что понадобится защитная ширина и протяженность режущей кромки, тогда будет отходить хорошая стружка.
Для художественного фрезерования
Декоративные металлические вставки пользуются особенной популярностью в интерьере жилья или офисного помещения, но также такие элементы можно добавлять при проектировании автомобилей, при гравировке любых изделий, например, наручных часов, и в прочих случаях.
В основном для этих целей применяются концевые или дисковые насадки. Более современный, производительный и точный способ – использование лазерных станков с ЧПУ, они быстро и идеально верно повторяют заданные контуры, наносят углубления и узоры. Их можно приобрести в интернет-магазине https://stanokcnc.ru/.
Режимы резания при фрезеровании концевыми или пазовыми фрезами идеально подходят для создания паза, канавки. Они могут иметь от 1 до 4 и более заходов, различную ширину и длину зубцов, сменные насадки или монолитные. Изготавливаются они из любого пригодного материала. Большое многообразие позволяет выбрать инструмент в зависимости от назначения. К слову, они подходят как для ручного управления станком, так и для числового.
Дисковые прекрасно справляются со множеством задач – начиная от грубой и быстрой распиловки, заканчивая тонкой, практически ювелирной работой по декоративному металлическому элементу.
Для обработки кромок
К сожалению, не каждый срез обладает идеальными характеристиками: гладкий, без зацепок и заусенцев, с правильным классом шероховатости и точности. То же касается всех углов – к ним сложно подобраться, по крайней мере не так легко, как к прямой поверхности. Для этого используют следующие насадки:
- Отрезная и шлицевая могут быть применимы для отделения одной части материала от основного массива.
- С помощью угловой можно обрабатывать углы и край. При этом есть две разновидности данного инструмента – с одной и двумя режущими кромками.
- Фасонная применяется для деталей с нестандартным и сложным изгибом – для круглых, вогнутых поверхностей. Очень часто используется для нарезания некоторого крепежного инструментария.
Обычно все из представленных видов имеют варианты с монолитным изготовлением из твердоплавкого сырья, а также складные – со съемными насадками. Первый вариант больше подходит для черновой металлообработки, а второй – для чистовой и тонкой.
Как посчитать режимы и скорость резания по параметрам
При выборе количества оборотов необходимо смотреть на множество факторов, каждый из которых имеет значение. Есть специальные таблицы для расчета, их мы приведем ниже. А пока познакомимся с важными особенностями.
Ширина фрезерования
Это то, как много будет в единый момент времени сниматься стружки с заготовки. Конечно, чем больше, тем выше продуктивность. Но это может повлиять на качество, особенно если лезвие не одинаково заточено по всей длине режущей кромки, а также если в обрабатываемом материале есть прочные включения, которые могут повредить саму инструментальную сталь. Особенности:
- Ширина среза зависит напрямую от того, какой диаметр у инструмента. Таким образом, параметр не регулируется во время выбора режима резания на фрезерном станке, но имеется в виду фрезеровщиком, когда он устанавливает определенную оснастку.
- Использование таких резаков приводит к изменению других параметров, все они взаимосвязаны. В частности, снижается срок эксплуатации насадки, если есть неблагоприятные условия на 75%. Таким образом, мы рекомендуем увеличивать ширину среза только в случае, если вы точно уверены в высоком качестве стали, а также в остальных факторах.
Положительно сказываются фрезы большого диаметра на количество проходов. Обычно требуется много раз пройтись по одному месту, но, например, при создании неглубоких канавок можно ограничиться одним разом.
Глубина резания
Это расстояние, которое определяется от поверхности обрабатываемой детали до предполагаемой линии среза. То есть то, какой будет убран слой. Особенности:
- Зависимость от материала: не каждая сталь позволит делать глубокие канавки, хрупкие сплавы могут переломиться.
- Черновая обработка позволяет задавать большую глубину резки, даже припуска на нее определяются сразу до 8 мм, в то время как чистовая – нет. Чем выше предполагаемая точность, тем меньше глубина.
- Естественное ограничение – длина режущей кромки инструмента.
Параметр определяет производительность оборудования, потому что при небольшом расстоянии за один проход приходится тратить в два-три раза больше времени.
Скорость
Это период, за который материал проходит полное изменение на нужную глубину при заданных прочих параметрах. От него напрямую зависит производительность, а также аккуратность среза и длительность эксплуатации рабочего инструмента.
Дадим приблизительные рекомендации, которые ориентированы на сырье:
Сплав | Количество оборотов в минуту |
Нержавейка – обладает составом, сложным к обработке из-за включения определенных химических веществ. | 45 – 95 |
Бронза – очень мягкая, не имеет твердых включений, поэтому с ней можно работать на высоких скоростях. | 90 – 150 |
Латунь – можно работать очень быстро, но нужно учесть, что при повышении нагрева материал становится очень пластичным, может непроизвольно деформироваться, поэтому нужно использовать охлаждающие составы. | 130 – 320 |
Алюминий. Характерно уточнение, как и для латуни, насчет температурного режима. Вторая особенность – большое разнообразие алюминиевых сплавов, в которых нужно разбираться. | 200 – 420 |
Частота вращения
По сути, этим термином также называется скорость, поскольку именно от количества оборотом вращения шпинделя, который держит резец, зависит быстрота. Мы рекомендуем не доверять таблицам, а произвести расчет самостоятельно по формуле: n=1000 V/ π*D, где:
- n – частота вращения;
- π – число Пи;
- V – рекомендуемые обороты резания;
- D – диаметр.
Подача на зуб: формула
Этим термином определяется движение заготовки навстречу фрезе. От него многое зависит, в том числе:
- насколько много можно снять стали за один проход;
- общая производительность механизма;
- какую обработку можно произвести: черновую или чистовую.
Этот показатель относится уже именно к инструменту, он характеризует то, как перемещается стол станка относительно зубца за один период его вращения.
Формула: S=fz*z*n(мм/мин), где:
- fz – подача на зуб;
- z – количество зубьев;
- n – частота вращения шпинделя, как ее вычислять, написано ранее.
Результат записывается в мм/мин.
Так как все параметры взаимосвязаны, приведем такой пример.
Когда увеличивается темп всего аппарата, обороты снижаются, потому что становится больше осевая нагрузка.
Режимы и минутная подача на зуб при фрезеровании исходя из материала, в таблице
Сплав | Скорость в метрах в минуту | Мм |
Латунь, бронза, медь | 120 – 250 | 0,01 – 0,07 |
Алюминий | 120 – 500 | 0,01 – 0,08 |
Магний | 150 – 300 | 0,01 – 0,075 |
Сталь | 35 – 50 | 0,005 – 0,03 |
Чугун | 40 – 60 | 0,005 – 0,04 |
Титан | 20 – 30 | 0,005 – 0,04 |
Рекомендации при выборе режима на практике
При подборе учитывайте:
- диаметр, рабочую глубину, угол наклона, количество режущих кромок, основу и качество создания фрезы;
- количество заходов и размер;
- из чего сделана заготовка;
- собственное умение.
По словам фрезеровщиков с большим опытом, никакие таблицы и учебники не могут научить правильно выставлять последовательность действий. Это можно сделать только после проб и ошибок, а также по прошествии определенного времени, за которое ты подготовишься к постоянной работе с данным станком.
Таблица режимов по неметаллическим веществам
Вид работы | Материал | Частота вращения, об/мин | Подача, мм/мин |
Выборка | Акрил | 18000 | 900 |
3D обработка | Древесина | 18 – 24 тысячи | 1800-3000 |
Раскрой | Композит | 15000-18000 | 1500-2400 |
В зависимости от типа фрезы
Обращайте внимание на:
- вид оснастки;
- качество ее изготовления;
- размер;
- количество зубцов;
- глубину захода режущей кромки;
- основу;
- конструкцию – цельная или сборная.
В зависимости от материала
Смотрите на характеристики:
- плотность;
- прочность;
- хрупкость;
- плавкость при повышении температуры;
- наличие твердых вкраплений;
- добавление легирующих веществ;
- внешние загрязнения, в том числе ржавчину.
Рекомендуем определять режим, исходя из приведенных выше таблиц.
Полезные советы
- Всегда работайте в защитной одежде защищайте руки и ноги, тело и лицо, надевайте маску или специальные очки – горячая стружка, окалина может попасть на кожу или слизистые оболочки и оставить ожог.
- Если вы занимаетесь профессиональным производством, закупайте оборудование, оснащенное числовым пультом управления, поскольку это увеличивает быстроту обработки, то есть производительность и точность. Хорошие станки с ЧПУ можно заказать в https://stanokcnc.ru/.
- Всегда сначала приспособьтесь, привыкните к новому оборудованию, и только потом начинайте ответственную фрезеровку.
Вывод
Мы рассказали про скорость и режимы резания. Будьте внимательны и аккуратны при работе с металлом.
Правильный подбор режимов резания заготовок из того или иного материала на фрезерном станке – очень важный аспект успешной эксплуатации оборудования. И вопрос тут не только в должном качестве конечной продукции. От правильного подбора этих режимов, отраженных в технологической карте обработки заготовки, во многом зависит срок эксплуатации и целостность инструмента и оборудования в целом. Поломка или преждевременное затупление фрезы, звон или иные нехарактерные звуки при работе и другие нерасчетные проявления – все это результат ошибок, допущенных при подборе режимов резания детали.
Именно поэтому подбор и расчет режимов резания на каждом этапе обработки должен выполнять специалист, что прошел соответствующую подготовку. А они при фрезеровке деталей зависят от целого ряда показателей. В первую очередь, от используемого инструмента, типа материала и его физических характеристик.
Чтобы понимать смысл методики расчетов и задание параметров обработки, мы предлагаем Вашему вниманию серию материалов для изучения. В этой статье мы дадим базовые представления о процессе расчета и подбора оптимальных характеристик режимов фрезеровки для ЧПУ-станков. Прежде всего, потому, что на них в отличие от универсальных фрезеров необходимо сразу назначать близкие к оптимальному режимы резания материалов, а затем корректировать их в пределах ±20%.
Режимы резания из каталогов
Выбор режимов резания инструмента может быть подобран из каталога производителя оборудования. Но далеко не всегда это гарантирует, что параметры обработки будут оптимальными. И тому есть несколько причин:
- Недобросовестные производители оборудование завышают паспортные показатели работы своей техники на 20-40% относительно реальных. Таким образом они надеются получить дополнительные преимущества в глазах конечного покупателя ЧПУ-фрезеров;
- Практический опыт с режущим инструментом и обработкой всевозможных материалов у производителя оставляет желать лучшего;
- Каталога под рукой у оператора станка в нужный момент не окажется.
В таком случае стоит опираться на методику расчета режима резания при фрезеровании, что мы предлагаем Вашему вниманию. В ней воплощен внушительный опыт наших разработчиков, что постоянно сталкивались с непосредственным взаимодействием с различными материалами.
Параметры режима резания: смысл и детальный разбор
В режимы резания для фрезы входит 3 параметра:
- S – частота вращения шпинделя (обороты шпинделя);
- F – подача (скорость, с которой движется инструмент);
- P – величина съема (слой материала, срезаемый фрезой).
Скорость резания
Скорость резания можно назвать наиболее важным параметром при подборе режима обработки заготовки. От нее зависит, за какое время будет снят слой материала, необходимый для получения конечного изделия. При подборе подходящей величины этого показателя, которая в большинстве случаев является постоянной на каждом этапе обработки, учитывается в первую очередь твердость и плотность снимаемого материала.
Таким образом:
- При работе с нержавеющей сталью диапазон скоростей варьируется в пределах 45-95 м/мин. Она определяется в первую очередь наличием тех или иных химических элементов в сплаве;
- Бронза как сплав с невысокой твердостью позволяет увеличить диапазон скоростей резания. Значения для работы с этим медным сплавом варьируются в спектре значений от 90-150 м/мин. Работать с бронзой может довольно ограниченная группа фрезерного оборудования;
- Латунь имеет относительно низкую твердость даже в сравнении с бронзой. Целый ряд запорных элементов и клапанов выполняется на ЧПУ-станках из этого сплава. За счет низкой твердости с такими заготовками можно работать на относительно высоких скоростях резания – от 130 до 320 м/мин. Стоит также иметь ввиду, что при повышенном нагреве вследствие высоких скоростей латунные изделия склонны к короблению;
- Алюминиевые сплавы при фрезеровке допускают скорость резания в пределах от 200 до 420 м/мин. За счет высокой пластичности при нагреве такие металлические заготовки нужно обрабатывать очень аккуратно. В противном случае велик риск брака конечного изделия.
Частота вращения фрезы
Рекомендуемые режимы резания в более обширном виде представлены в следующей таблице:
Стоит отметить, что подобных таблиц существует довольно много. В их основе лежат одни и те же формулы. Так, определение режимов резания для различных видов обрабатываемых материалов рассчитывается по формуле:
n=1000 V/ D, где
V – рекомендуемая скорость резания,
D – диаметр применяемой фрезы.
Стоит понимать, что шпиндель не рекомендуется использовать на максимальных оборотах. Это ощутимо повышает износ инструмента и оборудования. Поэтому полученный по формуле результат стоит уменьшить на 10-15%, а затем подобрать инструмент под полученную скорость вращения фрезы.
Скорость вращения инструмента является определяющим фактором для многих показателей работы станка. В частности, в их число входят:
- Качество поверхности конечного изделия. Обороты шпинделя при финишной обработке выбираются максимальными. За счет этого образующаяся стружка является очень мелкой и отлетает далеко из зоны контакта. Низкая шероховатость поверхности детали (вплоть до поверхности зеркального типа, если речь о металлических заготовках) также достигается на высоких скоростях вращения фрезы. При черновой же обработке обороты шпинделя принимаются относительно невысокими, поэтому размер стружки выходит средний или крупный.
- Производительность работы. Очевидно, что чем выше обороты шпинделя, тем быстрее выполняется обработка. Но это не должно производиться в ущерб качеству. Поэтому владельцу предприятия приходится всегда искать компромиссное решение между противоречивыми факторами. И оптимальный режим резки подразумевает поиск именно таких показателей работы оборудования.
- Степень износа инструмента. При высоком трении режущей кромки фрезы о твердый материал она быстрее изнашивается ввиду сильного нагрева. Это сказывается на эффективности производства и показателях точности изготовления изделия. Поэтому станки с мощным шпинделем снабжаются эффективными системами охлаждения, подающими СОЖ в рабочую зону.
Глубина резания
Необходимо понимать, что ввиду связанности всех параметров обработки, оптимальный режим резания выбирается с учетом этой связи. И одним из наиболее важных параметров является глубина резания (она же — глубина фрезерования).
Физический смысл характеристики – толщина слоя материала, что снимается за один проход фрезы. Она напрямую зависит от материала заготовки и тому, черновая или чистовая обработка заготовки осуществляется. При черновой выбирается большая глубина фрезерования, но при этом скорость резания при обработке выбирается меньшей. При чистовой – наоборот, высокая скорость и малая толщина снимаемого материала.
Если необходимо снять значительные объемы материала или же форма конечного изделия сложна, выполняется два и более прохода фрезы.
Помимо вида обработки (черновая или чистовая) глубина резания при фрезеровке зависит от нескольких факторов:
- Обрабатываемый материал. Чем тверже и плотнее изделие, тем меньшая глубина врезания выбирается;
- Особенностей самого изделия и конфигурации заготовки;
- Производительность оборудования. В особенности важным показателем является мощность шпинделя ЧПУ-фрезера;
- Конструктивные особенности инструмента. Режущая часть фрезы может иметь различные размеры. Соответственно, специфика снятия материала у различных фрез также отличается.
Отдельно стоит упомянуть технологический процесс фрезерования пазов. Он выполняется при помощи специального инструмента исключительно после чистовой обработки поверхности детали. Глубина фрезерования пазов может быть довольно внушительной.
Подача на зуб
Этот показатель определяет движение заготовки навстречу обрабатывающей ее инструменту. Обозначаемая в миллиметрах величина определяет несколько факторов – объемы снятого за один проход материала, производительность, вид производимой обработки. Но в отличие от обычной подачи он относится непосредственно к инструменту. Исходя из этого становится понятно, как перемещается заготовка относительно зубца за один период вращения последнего.
Подача на зуб в мм/мин рассчитывается по формуле:
S=fz×z×n, где:
- fz – подача на зуб;
- z – количество зубьев у инструмента;
- n – частота вращения шпинделя.
Скорость резания при фрезеровании и подача на зуб, как очевидно, связаны определенными зависимостями. В частности, при росте подачи скорость снижается. Объясняется это тем, что при повышении снимаемого объема металла за один проход осевая нагрузка на инструмент растет. При выборе высоких показателей подачи и скорости резания велик риск скорого износа или поломки инструмента.
По причине снижения величины подачи повышается общая скорость обработки резанием детали. Значительные обороты шпинделя фрезеровального станка позволяют повысить качество итоговой поверхности. Как показывает практический опыт, оптимальное значение подачи на зуб при работе с твердыми материалами лежит в диапазоне 0,1-0,25 мм/мин.
Ширина фрезерования
Последний параметр, играющий особое значение при подборе оптимального режима фрезерования заготовки – ширина обработки. Она может варьироваться в весьма широком диапазоне.
Среди особенностей этого показателя можно отметить такие пункты:
- Зависимость ширины фрезерования заготовки от диаметра применяемого инструмента;
- При росте ширины увеличивается объем снимаемого за один проход материала. Таким образом, варьируя этот параметр, можно получить необходимую поверхность максимально оперативно. Например, как это имеет место при формировании неглубоких канавок.
Стоит понимать, что правильно и точно выставлять оптимальные режимы обработки заготовок при фрезеровании возможно только при определенном опыте. То есть, таблицы и расчеты – это хорошо, но только практика использования конкретной модели станка и работы с материалами позволит выполнять это сразу и правильно. Компания «Миртелс» предлагает для этих целей свое оборудование – например, универсальные фрезеры серии «Дедал» или специализированные ЧПУ-фрезеры серии «Архимед» для обработки камня различных пород.