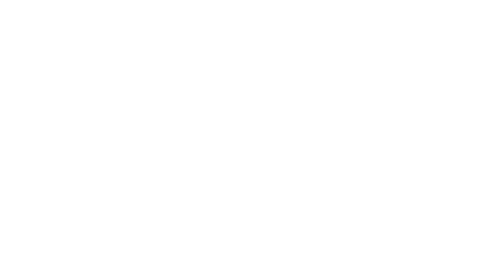
Рабочее место
– участок
производственной площади, закрепленный
за данным рабочим (или бригадой рабочих),
предназначенный для выполнения
определенной работы и оснащенный
оборудованием, приспособлениями,
инструментом и материалами в соответствии
с характером работы.
Рабочее место
слесаря
(рис. 1) состоит из слесарного верстака,
на котором установлены слесарные тиски
3, предохранительная проволочная сетка
4, электрическая лампа местного освещения
на шарнире 6, поверочная плита. Верстак
изготовляют металлическим, столешницу
(крышку верстака) 2 – из досок и сверху
покрывают кровельным железом или
фанерой. Со всех сторон столешницы
крепят деревянные планки-бортики,
препятствующие падению с верстака
мелких предметов. Под столешницей
верстака устанавливают выдвижные ящики
9 для хранения в определенном порядке
инструмента и вспомогательных материалов.
Необходимые инструменты, приспособления
и материалы разложены в ящике и на
верстаке. На верстаке должны находиться
только те предметы, которые необходимы
для выполнения данной операции, остальные
– в верстаке.
Хранить инструмент
следует в выдвижных ящиках верстака в
таком порядке, чтобы режущий и
измерительный инструмент не портились
от ударов, царапин, коррозии. Для этого
в ячейках делают поперечные полочки и
ячейки, предназначенные для одного
вида инструментов. Напильники раскладывают
по размерам, насечкам и формам поперечного
сечения. Сверла, метчики и плашки хранят
на плашках-планшетах со специальными
гнездами. На дне ящика хранят более
крупный и грубый инструмент: молотки,
зубила и т.д. Измерительный инструмент
должен находиться в футляре или на
куске ткани, постеленной на верстаке.
Рабочие инструменты
хранятся в подставках с гнездами,
документация (чертежи, технологические
карты) – на специальных планшетах,
измерительные инструменты – в деревянных
коробках или футлярах.
Рис. 1. Верстак
слесарный:
1 – каркас; 2 –
столешница; 3 – тиски;
4 – защитная сетка;
5 – планшет для
документации; 6 –
местное освещение;
7 – полочка для
измерительного инструмента;
8 – планшет для
рабочего инструмента;
9 – ящик для
хранения инструмента;
10 – полки; 11 –
сиденье
Габариты верстака:
длина – 1000-1200 мм
ширина
– 700-800 мм
высота
– 800-900 мм.
Тиски являются
основным оборудованием рабочего места
слесаря. Они служат приспособлением
для установки и закрепления заготовок
в удобном для обработки положении и
состоят из корпуса и двух зажимных
губок.
Тиски устанавливают
на верстаках и используют при различных
слесарных работах:
— стуловые – при
рубке, гибке, правке и других видах
обработки с ударными нагрузками;
— параллельные,
неповоротные и поворотные – при
выполнении более сложных и точных
работ, не связанных с сильными ударами
по заготовке;
— ручные – для
закрепления небольших заготовок, если
их неудобно или опасно держать руками.
Наиболее часто
применяются параллельные тиски (ГОСТ
4045-57) которые имеют следующие размеры:
— по ширине губок
– 60, 80, 100, 120, 140 мм;
— по разводу губок
– 45, 65, 100, 140, 180 мм.
Параллельные
тиски (рис. 2) состоят из основания 1,
которое с помощью болтов крепится к
верстаку. На основании закреплен корпус
9 неподвижной губки 7. В прямоугольном
вырезе, внутри неподвижной губки
располагается гайка, через которую
проходит зажимный винт 3. Одновременно
через прямоугольный вырез проходит
призматический выступ 8 подвижной губки
5. Винт 3 в подвижной губке закреплен
стопорной планкой 4. При вращении
зажимного винта рукояткой 2 он будет
ввинчиваться в гайку и перемещать
подвижную губку относительно неподвижной.
Рис. 2. Параллельные
тиски
Корпус тисков
изготовляют из чугуна. Для увеличения
срока службы к рабочим частям губок
крепят стальные планки 6. Поворот тисков
относительно вертикальной оси производят
вручную при отжатой рукоятке 10. У
неповоротных тисков корпус неподвижной
губки жёстко крепится к основанию без
возможности поворота вокруг вертикальной
оси.
Большое влияние
на производительность труда слесаря
оказывает правильная организация и
оснащенность рабочего места. Хорошая
организация рабочего места сводится
к следующим основным правилам:
-
Высота верстака
и тисков должна соответствовать росту
рабочего. При нормальном положении
локоть согнутой и прижатой к груди
правой руки должен находиться на уровне
губок тисков, а выпрямленные пальцы
этой руки должны касаться подбородка. -
Рабочее место
должно быть хорошо освещено дневным
или электрическим светом. Во время
работы свет не должен падать в глаза
работающему. -
На рабочем месте
необходимо располагать только
инструменты, необходимые для данной
работы. -
Инструменты,
которыми рабочий пользуется часто,
должны располагаться ближе к нему, а
используемые редко – дальше. Инструмент,
который держится правой рукой,
располагается справа от тисков, левой
– слева от тисков. -
Чертежи и
технологическая карта во время работы
должны находиться перед глазами
рабочего на специальной подставке. -
Рабочее место
должно содержаться в чистоте. После
окончания работы необходимо очистить
от стружки и вытереть насухо рабочие
инструменты и приспособления, убрать
стружку и сдать инструмент в кладовую.
Соседние файлы в предмете [НЕСОРТИРОВАННОЕ]
- #
- #
- #
Металлическая мебель нашего производства изготавливается под тремя зарегистрированными товарными знаками KRON®, Гефест® и KronVuz®. Все права на сайт принадлежат компании «KRONVUZ».
Использование наименований товаров и товарных знаков разрешено, только с письменного разрешения компании правообладательницы – «KRONVUZ».
При копировании любой информации с нашего сайта, вы обязательно должны сослаться на первоисточник – verstaki.com
Вся информация: описание, цены, характеристики, указанные на сайте, несут исключительно информационный характер и не при каких условиях не является публичной офертой. Внешний вид изделий и их характеристики могут быть изменены заводом производителем в любой момент ввиду модернизации или улучшения технических свойств.
Внимание! Все цены на сайте указаны без учета НДС.
Политика конфеденциальности
Мастер на все руки, Николай Михалыч даст вам массу полезных советов, которые помогут за короткое время справиться с маленькими техническими неполадками в вашем доме. Вы узнаете, как плавить металл с помощью пылесоса, как сверлить жесть и как извлечь мелкие детали из щели. Вы сможете правильно выбрать необходимые инструменты, сделать уютным свое рабочее место, а также намотаете на ус правила техники безопасности. Необходимо починить унитаз, ванну, водопроводный кран? С Михалычем это проще простого!
Оглавление
Оборудование и организация рабочего места слесаря
Общие требования
Рабочее место слесаря в домашних условиях может быть организовано по-разному. Однако для удобства и большей эффективности работы следует соблюдать некоторые основные правила.
В целях экономии движений и устранения ненужных поисков предметы на рабочем месте подразделяют на предметы постоянного и временного пользования; для тех и других отводят постоянные места хранения и расположения.
По возможности предметы на рабочем месте размещают так, чтобы избежать при выполнении работ поворотов и особенно нагибания корпуса, а также перекладывания предметов из одной руки в другую.
Инструменты и приспособления в процессе работы должны располагаться на верстаке в следующем порядке: все то, что берется левой рукой, нужно располагать в левой части верстака, то, что берется правой рукой, располагается в правой части верстака. Инструменты и приспособления, которыми слесарь пользуется чаще, нужно располагать ближе, и, наоборот, то, чем пользуются реже, располагать дальше. Такое расположение должно быть постоянным, чтобы слесарь во время работы мог брать нужный инструмент, приспособление или заготовку, не затрачивая излишнего времени на отыскание их.
Хранить инструмент следует в выдвижных ящиках верстака в таком порядке, чтобы режущий инструмент — напильники, метчики, сверла и т. п. — не портился, а измерительный инструмент — угольники, штангенциркули, микрометры и др. — не портился от забоин, царапин и ударов. Для этого в выдвижном инструментальном ящике слесарного верстака делают поперечные полочки шириной 100–150 мм. Каждая ячейка должна предназначаться для одного вида инструмента. В одном из инструментальных ящиков верстака, вдоль его боковых сторон, прибивают по 3–4 ступенчатых планки, на которые кладут напильники; при этом напильники больших размеров располагают на нижних ступеньках, а малых — на верхних.
Дно ящика делят на несколько клеток для хранения сверл, разверток, метчиков и плашек. На остальной площади ящика необходимо хранить более грубый инструмент, такой, как молотки, зубила, крейцмейсели и т. д.
Измерительные инструменты хранят в специальных футлярах или в деревянных коробках.
После окончания работы использованные инструменты и приспособления очищают от грязи и масла и протирают. Напильники необходимо очистить от металлических опилок и грязи проволочной щеткой, вытереть чистой тряпкой или салфеткой. Рабочие части режущего и мерительного инструмента следует смазывать тонким слоем вазелина. Поверхность верстака очищают щеткой от стружки и мусора.
Рабочее место должно иметь хорошее индивидуальное освещение. Свет должен падать на обрабатываемый предмет, а не на лицо работающего. Желательно, чтобы свет был рассеянным и не создавал бликов, мешающих работать.
Слесарный верстак
Для выполнения ручных работ большинство рабочих мест оборудуется слесарным верстаком, на котором устанавливают тиски и раскладывают необходимые для работы инструменты, приспособления, материалы.
Верстак (рис. 1) представляет собой специальный стол, на котором выполняют слесарные работы. Он должен быть прочным и устойчивым. Каркас верстака сварной конструкции из чугунных или стальных труб, стального профиля (уголка). Крышку (столешницу) верстаков изготовляют из досок толщиной 50–60 мм (из твердых пород дерева). Такая столешница не будет прогибаться и дрожать во время выполнения работ. Столешницу, в зависимости от характера выполняемых на верстаке работ, покрывают листовым железом толщиной 1–2 мм, линолеумом или фанерой. По периметру столешницу желательно окантовать бортиком, чтобы с нее не скатывались детали.
Под столешницей верстака желательно иметь два-три выдвижных ящика, разделенных на ряд ячеек для хранения в определенном порядке инструментов и мелких деталей.
Размеры слесарного верстака должны быть следующими: в длину 1000–1200 мм, в ширину 700–800 мм, в высоту 800–900 мм.
Особенно удобны верстаки с регулируемой высотой ножек, которые при необходимости разрешают устанавливать верстак по росту слесаря.
Для удобства работы к ножке верстака можно прикрепить откидное сиденье. Для предохранения от стружки, разлетающейся во время рубки металла, верстак желательно оградить проволочной сеткой, натянутой на рамку.
Слесарные тиски
Слесарные тиски представляют собой зажимные приспособления для удержания обрабатываемой детали в нужном положении. В зависимости от характера работы применяют стуловые, параллельные и ручные тиски.
Рис. 1. Слесарный верстак с регулируемыми по высоте тисками:
1 — винт подъема; 2 — каркас; 3 — труба;
4 — сетка; 5 — полочка; 6 — планшет;
7—рамка; 8 — маховичок
Стуловые тиски получили свое название от способа крепления их на деревянном основании в виде стула, но их можно закрепить и на верстаке. Применяются стуловые тиски в основном для выполнения грубых тяжелых работ, связанных с применением ударной нагрузки, — при рубке, клепке, гибке и пр.
Они состоят из неподвижной 3 и подвижной 4 губок (рис. 2, а). При вращении зажимного винта 5 подвижная губка 4 перемещается и зажимает деталь; при вывинчивании винта 5 под действием пружины 6 подвижная губка отходит и освобождает деталь. Крепление стуловых тисков к верстаку производят планкой (лапками) 2, а для большей их устойчивости неподвижная губка 3 имеет удлиненный стержень 7, который прикрепляется к ножке верстака.
Стуловые тиски отковывают из конструкционной углеродистой стали.
Ширина губок в зависимости от типа и размера стуловых тисков имеет размеры 100, 130, 150, 180 мм, наибольшее раскрытие губок — 90, 130, 150 и 180 мм.
На рабочие части губок наваривается накладка из инструментальной стали или укрепляются на винтах специальные пластины 8 (накладные губки, рис. 2, б). Рабочие поверхности этих пластин насекаются крестообразной насечкой и закаливаются.
Преимуществами стуловых тисков являются простота конструкции и высокая прочность. Недостатком стуловых тисков является то, что рабочие поверхности губок не во всех положениях параллельны друг другу, вследствие чего при зажиме узкие обрабатываемые предметы захватываются только верхними краями губок, а широкие — только нижними (рис. 2, б), что не обеспечивает прочности закрепления. Кроме того, губки тисков при зажиме врезаются в деталь, образуя на ее поверхности вмятины.
Рис. 2. Стуловые тиски: а — общий вид, б — схемы закрепления заготовок
Параллельные слесарные тиски разделяются на поворотные и неповоротные. В этих тисках подвижная губка при вращении винта перемещается, оставаясь параллельной неподвижной губке, отчего тиски и получили название параллельных.
Поворотные параллельные тиски (рис. 3) могут поворачиваться на произвольный угол. Эти тиски в корпусе неподвижной губки 9 имеют сквозной прямоугольный вырез, в который помещена гайка 10 зажимного винта. В вырез входит прямоугольный со сквозным отверстием призматический хвостовик подвижной губки 7. Зажимной винт 11, пропущенный через отверстие корпуса подвижной губки, закреплен стопорной планкой 6. При вращении зажимного винта в ту или другую сторону при помощи рычага 5 винт будет ввинчиваться в гайку 10 или вывинчиваться из нее и соответственно перемещать подвижную губку 7, которая, приближаясь к неподвижной губке 9, будет зажимать обрабатываемый предмет, а удаляясь, освобождать.
Неподвижная губка тисков соединена с основанием 3 центровым болтом, вокруг которого и осуществляется необходимый поворот тисков. Поворотную часть 4 тисков закрепляют в требуемом положении при помощи рукоятки 2 болтом 1.
Корпус параллельных слесарных тисков изготовляют из серого чугуна. Для увеличения срока службы тисков к рабочим частям губок прикрепляют винтами стальные (из инструментальной стали) призматические губки 8 с крестообразной насечкой. При зажиме в тисках на обрабатываемых предметах могут появляться вмятины от насечки закаленных пластин губок. Поэтому для зажима обработанной чистовой поверхности детали (изделия) рабочие части губок тисков закрывают накладными пластинками («нагубниками»), изготовленными из мягкой стали, латуни или алюминия.
Рис. 3. Поворотные параллельные тиски:
1 — болт; 2 — рукоятка; 3 — основание;
4 — поворотная часть; 5 — рычаг; 6 — стопорная планка;
7 — подвижная губка; 8 — пластинки;
9 — неподвижная губка; 10 — гайка; 11 — винт
Размеры слесарных тисков определяются шириной их губок, которая составляет для поворотных тисков 80, 100, 120 и 140 мм и раскрытием (разводом) их на 65, 100, 140 и 180 мм.
Неповоротные параллельные тиски (рис. 4) имеют основание 6, с помощью которого они крепятся болтами к крышке верстака, неподвижную 4 и подвижную 2. Для увеличения срока службы рабочие части губок 4 и 2 делают сменными в виде призматических пластинок 3 с крестообразной насечкой из инструментальной стали и прикрепляют к губкам винтами. Подвижная губка 2 перемещается своим хвостовиком в прямоугольном вырезе неподвижной губки 4 вращением винта 5 в гайке 7 при помощи рычага 1. От осевого перемещения в подвижной губке зажимный винт 5 удерживается стопорной планкой 8. Ширина губок неповоротных параллельных тисков составляет 60, 80, 100, 120 и 140 мм, наибольшее раскрытие губок — 45, 65, 100, 140 и 180 мм.
Рис. 4. Неповоротные параллельные тиски:
1 — рычаг; 2 — подвижная губка; 3 — пластинки;
4 — неподвижная губка;
5 — винт; 6 — основание;
7 — гайка; 8 — стопорная планка
Рис. 5. Закрепление деталей в ручных тисках и струбцинах:
а, б — ручные слесарные тиски, в — использование косогубых тисков, г — применение струбцины
Ручные тиски (рис. 5, а) изготавливаются с шириной губок: 36, 40, 50 и 56 мм и раскрытием губок 28, 30, 40, 50 и 55 мм; тип 2 для мелких работ (рис. 5, б) с шириной губок 6, 10 и 16 мм и раскрытием губок 5,5 и 6,5 мм. Иногда форма детали не дает возможности зажать ее в нужном положении, так например, в случае, когда требуется опилить фаску под некоторым углом. В таких случаях применяют косогубые тисочки (рис. 5, в), в которые захватывают деталь и зажимают в губки параллельных тисков. Для удобства одновременной обработки нескольких одинаковых деталей или тонких длинных заготовок применяют специальные струбцины (рис. 5, г).
Ручные тиски изготовляются из качественной конструкционной углеродистой стали марки 45–50; для пружин используют инструментальную углеродистую сталь марки У7 или сталь марки 65Г. Допускается изготовление пружин и из стали марки 60–70.
При работе на тисках следует соблюдать следующие правила:
— перед началом работы осматривать тиски, обращая особое внимание на прочность их крепления к верстаку;
— не выполнять на тисках грубых работ (рубки, правки или гибки) тяжелыми молотками, так как это приводит к быстрому разрушению тисков;
— при креплении деталей в тисках не допускать ударов по рычагу, что может привести к срыву резьбы ходового винта или гайки;
— по окончании работы очищать тиски волосяной щеткой от стружки, грязи и пыли, а направляющие и резьбовые соединения смазывать маслом;
— после окончания работ разводить губки тисков, так как в сжатом состоянии возникают излишние напряжения в соединении винта и гайки.
Рабочий инструмент
При выполнении слесарных работ пользуются разнообразными инструментами и приспособлениями. Рабочий инструмент слесаря подразделяется на ручной и механизированный.
Типовой набор ручного инструмента делится на:
а) режущие инструменты — зубила, крейцмейсель, набор напильников, ножовка, шаберы, спиральные сверла, цилиндрические и конические развертки, круглые плашки, метчики, абразивные инструменты (бруски и пасты) и др.;
б) вспомогательные инструменты — слесарный и рихтовальный молотки, керн, чертилка, разметочный циркуль, плашкодержатель, вороток и т. п.;
в) слесарно-сборочные инструменты — отвертки, гаечные ключи, бородок, плоскогубцы, ручные тиски и др.
Молотки слесарные являются наиболее распространенным ударным инструментом. Они служат для нанесения ударов при рубке, пробивании отверстий, клепке, правке и т. д. В слесарном деле применяются молотки двух типов — с круглыми и квадратными бойками (рис. 6, а). Молотки с круглым бойком применяют в тех случаях, когда требуется значительная сила или точность удара. Молотки с квадратным бойком выбирают для более простых работ. Молотки изготавливаются из сталей марок 50, 40Х или из стали У7; их рабочие части — боек и носок — подвергают закалке на длину не менее 15 мм с последующей зачисткой и полировкой.
Вес молотков в зависимости от назначения варьируется в следующих пределах: 50, 100, 200 и 300 г — для выполнения инструментальных работ, 400, 500 и 600 г — для слесарных работ, 800, 1000 г — для ремонтных работ.
Материалом для ручек молотков служат кизил, рябина, клен, граб, береза — породы деревьев, древесина которых отличается прочностью и упругостью. В сечении ручка должна быть овальной, а ее свободный конец делают в полтора раза толще, чем у отверстия молотка. Длина ручки зависит от веса молотка. В среднем она делается длиной 250–350 мм; для молотков весом 50—200 г длина ручек берется 200–270 мм, для тяжелых — 350–400 мм. Конец ручки, на который насаживается молоток, расклинивается деревянным клином, смазанным столярным клеем, или же металлическим клином с насечкой.
Зубило применяется для разрубания на части металла различного профиля, удаления припусков с поверхности заготовки, срубания приливов и литников на литых заготовках, головок заклепок при ремонте заклепочных соединений и т. п.
Зубило состоит из трех частей — рабочей, средней и ударной (рис. 6, б). Рабочая часть зубила имеет форму клина, углы заточки которого выбираются в зависимости от обрабатываемого материала. Средней части слесарного зубила придается овальное или многогранное сечение без острых ребер на боковых гранях, чтобы не поранить руки. Головке (ударной части) зубила придается форма усеченного конуса.
Конец ознакомительного фрагмента.
Содержание страницы
- 1. Рабочее место слесаря
- 1.1. Организация рабочего места
- 1.2. Правила содержания рабочего места
- 2. Слесарный инструмент
- 3. Измерительный и проверочный инструмент
- 3.1. Универсальные измерительные и контрольные инструменты
- 3.2. Специальные измерительные и контрольные инструменты
- 4. Слесарные работы
- 4.1. Разметка
- 4.2. Правка и гибка металлов
- 4.3. Рубка металлов
- 4.4. Резка металлов
- 4.5. Опиливание металлов
- 4.6. Сверление, зенкование, зенкерование и развертывание отверстий
- 4.7. Нарезание резьбы
- 4.8. Клепальные работы
- 4.9. Шабрение
- 4.10. Шлифование
- 4.11. Притирка, полирование и отделка поверхности.
- 4.12. Пайка, лужение, металлизация и склеивание
- 4.13. Сборка деталей
- 5. Требования безопасности труда при выполнении слесарных работ
- 5.1. Требования безопасности труда
- 5.2. Правила производственной санитарии
1. Рабочее место слесаря
Профессия «слесарь» на современном предприятии является довольно распространенной. Слесарные работы выполняются при монтаже производственного оборудования, установку которого осуществляют слесари-монтажники и слесари-сборщики. Наладка установленного на месте постоянной работы оборудования связана с работой слесарей-наладчиков. Эксплуатация оборудования, машин и механизмов не обходится без участия слесарей-ремонтников. Изготовление специального инструмента и специфических деталей осуществляют слесари-инструментальщики. Каждая из названных групп слесарей характеризуется особыми для их работы знаниями и профессиональными навыками.
Однако для каждого слесаря базовым является овладение общеслесарными операциями, представляющими собой основу слесарного мастерства. К этим операциям относятся разметка, рубка, правка, гибка, резка, опиливание, сверление, зенкерование и развертывание отверстий, нарезание резьбы, шабрение, притирка и доводка. Эти операции выполняются ручными и механизированными инструментами, которыми должен уметь пользоваться каждый слесарь.
Современный слесарь также должен владеть навыками выполнения несложных работ на металлорежущих станках (токарных, фрезерных, шлифовальных), что позволяет заменить утомительную ручную обработку заготовок механизированной, облегчить труд и повысить качество выполняемых работ.
Рабочее место слесаря – часть производственной площади цеха, участка или мастерской, которая закрепляется за определенным работником или работниками (в случае посменной работы) для выполнения определенного вида работ и должна быть оснащена оборудованием, приспособлениями, инструментами и материалами, необходимыми для их проведения.
Основным оборудованием рабочего места слесаря является, как правило, одноместный верстак. Конструкций верстаков множество. Общий вид некоторых из них показан на рисунке 1.
Рис. 1. Слесарные верстаки
Слесарный верстак должен быть прочным и устойчивым, а его высота соответствовать росту работающего.
Верстак состоит из стального каркаса, на котором установлена столешница, обычно изготовленная из дерева твердых пород и покрытая листовой сталью толщиной 1–2 мм. По периметру столешницу желательно окантовать бортиком, чтобы с нее не скатывались детали. Под столешницей расположены выдвижные ящики для хранения инструментов, мелких деталей и технической документации. Для обеспечения удобства работы на верстаке располагаются планшет для режущих инструментов (чертилки, кернеры, зубила, напильники и т. д.) и инструментальная полка для измерительных инструментов.
1.1. Организация рабочего места
При размещении инструментов на верстаке необходимо учитывать частоту их использования в процессе работы и располагать инструменты таким образом, чтобы обеспечить удобный доступ к ним (рис. 2).
Рис. 2. Размещение инструмента на верстаке
К размещению заготовок, инструментов и материалов на рабочем месте предъявляют определенные требования:
- на рабочем месте должны находиться только те инструменты, материалы и заготовки, которые необходимы для выполнения данной работы;
- расположение инструментов и материалов должно соответствовать частоте их использования в процессе работы: то, что используется чаще, должно располагаться ближе (рис. 3, а, б). Эти зоны находятся справа и слева от работающего и обозначены дугой 1 в горизонтальной плоскости и дугой А в вертикальной плоскости. Радиус этих дуг приблизительно 350 мм. То, что используется реже, должно располагаться в зонах, обозначенных дугой 2 в горизонтальной плоскости и дугой Б в вертикальной плоскости. Радиус этих дуг приблизительно 500 мм. То, что используется крайне редко, должно находиться в зонах, обозначенных дугой 3 в горизонтальной плоскости и дугой В в вертикальной плоскости. Их досягаемость обеспечивается только при наклонах корпуса работающего;
- для размещения инструментов и приспособлений на рабочем месте слесаря возможна установка стеллажей, удобные и неудобные зоны доступа которых показаны на рисунке 3, в.
Рис. 3. Расположение удобных и неудобных зон на рабочем месте (размеры даны в миллиметрах): а, б – на верстаке; в – по высоте
1.2. Правила содержания рабочего места
В связи с тем, что рациональная организация рабочего места и правильное размещение инструментов и материалов в процессе работы играют существенную роль в обеспечении ее качества, необходимо соблюдать следующие правила.
До начала работы:
- проверить исправность верстака, тисков, приспособлений, индивидуального освещения и механизмов, используемых в работе;
- ознакомиться с инструкцией или технологической картой, чертежом и техническими требованиями к предстоящей работе;
- отрегулировать высоту тисков по своему росту;
- проверить наличие и состояние инструментов, материалов и заготовок, используемых в работе;
- разместить на верстаке инструменты, заготовки, материалы и приспособления, необходимые для работы.
Во время работы:
- иметь на верстаке только те инструменты и приспособления, которые необходимы для выполнения заданной работы (все остальное должно находиться в ящиках верстака);
- возвращать использованный инструмент на исходное место;
- постоянно поддерживать чистоту и порядок на рабочем месте.
По окончании работы:
- очистить инструмент от стружки, протереть, уложить в футляры и убрать в ящики верстака;
- очистить от стружки и грязи столешницу верстака и тиски;
- убрать с верстака неиспользованные материалы и заготовки, а также обработанные детали;
- выключить индивидуальное освещение.
2. Слесарный инструмент
При выполнении слесарных работ пользуются разнообразными инструментами и приспособлениями.
На верстаке устанавливают тиски.
Слесарные тиски представляют собой зажимные приспособления для удержания обрабатываемой детали в нужном положении. В зависимости от характера работы применяют стуловые, параллельные и ручные тиски.
Стуловые тиски (рис. 4) предназначены для выполнения тяжелых работ, связанных с большими ударными нагрузками (например, рубка, клепка, гибка металла), и имеют весьма ограниченную область применения.
Стуловые тиски закрепляют на верстаке 1 планкой крепления 2, которая обеспечивает плотное прижатие к верстаку стержня 8, изготовленного как единое целое с неподвижной губкой 3 тисков. Закрепление заготовки осуществляется между неподвижной 3 и подвижной 4 губками. Подвижная губка совершает колебательное движение относительно оси, установленной в кронштейне, закрепленном на стержне 8. Сведение губок осуществляется зажимным винтом 5, приводимым в движение рукояткой 6. Разведение губок после окончания обработки и освобождение обработанной детали осуществляется за счет пружины 7 при отпущенном зажимном винте.
Рис. 4. Стуловые тиски: а – общий вид; б – схематическое изображение
Параллельные поворотные тиски (рис. 5) для слесарных работ применяют наиболее часто. Параллельными их называют потому, что при перемещении подвижная губка 4 во всех положениях остается параллельной неподвижной губке 3. Тиски состоят из плиты основания 1 и поворотной части 2. Перемещение подвижной губки 4 обеспечивается винтовой парой (ходовой винт 7 и гайка ходового винта 5), а параллельность этого перемещения – направляющей призмой 6.
Для поворота верхней части тисков относительно плиты основания 1 необходимо ослабить при помощи рукоятки 11 болты 10, тогда при повороте верхней части тисков вокруг оси 9 гайка 12 с болтом 10 будут свободно перемещаться в круговом T-образном пазу 8. Верхняя часть тисков после установки в нужном положении закрепляется рукояткой 11.
Рис. 5. Параллельные поворотные тиски: а – общий вид; б – схематическое изображение
При выполнении слесарных работ находят применение и неповоротные параллельные тиски (рис. 6). Их устройство аналогично поворотным тискам за исключением возможности поворота вокруг своей оси.
Для зажима мелких деталей используют ручные тиски. Они выпускаются различных размеров и конфигураций (рис. 7).
Иногда на верстаках устанавливают небольшие точильные (рис. и вертикально-сверлильные (рис. 9) станки различной конструкции.
Рис. 6. Общий вид неповоротных параллельных тисков
Рис. 7. Ручные тиски
Рис. 8. Общий вид точильного станка
Рис. 9. Общий вид вертикально-сверлильного станка
Рабочий инструмент слесаря подразделяется на ручной и механизированный.
Типовой набор ручного инструмента:
а) режущие инструменты – зубила, крейцмейсель, набор напильников, ножовка, ножницы по металлу, шаберы, спиральные сверла, зенкеры, цилиндрические и конические развертки, круглые плашки, метчики, абразивные бруски и др. (рис. 10);
Рис. 10. Режущие инструменты: а – зубило; б – крейцмейсель; в – напильники; г – ножовка; д – шабер; е – спиральные сверла; ж – развертка; з – плашка; и – метчик; к – абразивный брусок; л – ножницы по металлу; м – зенкер
б) вспомогательные инструменты – слесарный и рихтовальный молотки, кернер, чертилка, разметочный циркуль, плашкодержатель, вороток для метчиков и т. п. (рис. 11);
в) слесарно-сборочные инструменты – отвертки, гаечные ключи, бородок, плоскогубцы и др. (рис. 12).
Рис. 11. Вспомогательные инструменты: а – слесарный молоток; б – рихтовальный молоток; в – кернер; г – чертилка; д – разметочный циркуль; е – плашкодержатель; ж – вороток для метчиков
Рис. 12. Слесарно-сборочные инструменты: а – отвертки; б – гаечные ключи; в – плоскогубцы; г – бородок
Рассмотрим назначение наиболее широко применяемых ручных слесарных инструментов.
Молотки слесарные являются самым распространенным ударным инструментом (см. рис. 11, а). Они служат для нанесения ударов при рубке, пробивании отверстий, клепке, правке и т. д. В слесарном деле применяются молотки двух типов – с круглыми и квадратными бойками. Молотки с круглым бойком применяют в тех случаях, когда требуется значительная сила или точность удара. Молотки с квадратным бойком выбирают для более простых работ. Молотки изготовляются из сталей марок 40Х, У7, У8. Их рабочие части (боек и носок) подвергают закалке на длину не менее 15 мм с последующей зачисткой и полировкой.
Масса молотков в зависимости от назначения варьирует в пределах 50, 100, 200 и 300 г – для выполнения инструментальных работ; 400, 500 и 600 г – для слесарных работ; 800 г, 1000 г – для ремонтных работ.
Материалом для ручек молотков служат клен, граб, береза – породы деревьев, древесина которых отличается прочностью и упругостью. В сечении ручка должна быть овальной, а ее свободный конец делают в 1,5 раза толще, чем у отверстия молотка. Длина ручки зависит от массы молотка. Для молотков массой 50–200 г длина ручек берется 200–270 мм, для тяжелых – 350–400 мм. Конец ручки, на который насаживается молоток, расклинивается деревянным клином, смазанным столярным клеем, или же металлическим клином с насечкой.
Зубило (см. рис. 10, а) применяется для разрубания на части металла различного профиля, удаления припусков с поверхности заготовки, срубания приливов и литников на литых заготовках, головок заклепок при ремонте заклепочных соединений. Зубило служит также для рубки или снятия слоя металла, когда не требуется точность обработки. Им можно производить разрезание, обрезание и вырезание материала.
Зубило состоит из трех частей – рабочей, средней и ударной. Рабочая часть зубила имеет форму клина, углы заточки которого выбираются в зависимости от обрабатываемого материала. Средней части придается овальное или многогранное сечение без острых ребер на боковых гранях, чтобы не поранить руки. Головке (ударной части) зубила придается форма усеченного конуса.
Материалом для изготовления зубил служит углеродистая сталь марок У7А и У8А. Рабочая часть зубила закаливается на длине 15–30 мм, а ударная – на длине 10–20 мм.
Крейцмейсель – инструмент, однотипный с зубилом, но с более узкой режущей кромкой (см. рис. 10, б). Он применяется для вырубания узких канавок и пазов. Изготовляют крейцмейсели из углеродистой стали марок У7А, У8А и закаливают, как зубило.
Бородок, или пробойник (см. рис. 12, г), применяется для пробивания отверстий в листовых или полосовых металлических или неметаллических материалах толщиной не более 4 мм, установки просверленных под заклепки отверстий одного против другого, выбивания забракованных заклепок, штифтов и др. Слесарные бородки изготовляют из стали марки У7А или У8А. Рабочая часть бородка закаливается на всю длину конуса.
Рабочая часть пробойника может иметь круглую, прямоугольную, квадратную, овальную или другую форму. Пробойник для кожи и жести в рабочей части имеет слепое отверстие, которое соединяется с продольным боковым отверстием, проходящим через стенку нижней части пробойника. Через это отверстие удаляются отходы.
Напильники представляют собой режущий инструмент в виде стальных закаленных брусков различного профиля с насечкой на их поверхности параллельных зубьев под определенным углом к оси инструмента (см. рис. 10, в). Материалом для изготовления напильников служит углеродистая инструментальная сталь марок У13 и У13А, а также хромистая шарикоподшипниковая сталь ШХ15.
Напильники имеют различные формы поперечного сечения: плоскую, квадратную, трехгранную, круглую и пр. В зависимости от характера выполняемой работы применяют напильники разной длины, с различным числом насечек.
Существуют три типа ручных напильников: обыкновенные, надфили и рашпили.
Обыкновенные напильники изготовляют из углеродистой инструментальной стали марок У13 и У13А. По числу насечек на 1 см длины они подразделяются на шесть номеров. Напильники с насечкой № 0 и № 1 (драчевые) имеют наиболее крупные зубья и служат для грубого (чернового) опиливания с погрешностью 0,5–0,2 мм. Напильники с насечкой № 2 и
№ 3 (личные) служат для чистового опиливания деталей с погрешностью 0,15–0,02 мм. Напильники с насечкой № 4 и № 5 (бархатные) применяются для окончательной точной отделки изделий. Погрешность при обработке – 0,01–0,005 мм.
По длине напильники могут изготовляться от 100 до 400 мм.
Надфили – те же напильники, но меньших размеров и с насечкой только на половину или три четверти своей длины. Гладкая часть надфиля служит рукояткой. Для изготовления надфилей используют стали марок У12 и У12А. Они применяются для обработки малых поверхностей и доводки деталей небольших размеров. Надфили изготовляют пяти номеров. Каждому номеру соответствует определенное число насечек на 1 см длины – от 20 до 112.
Рашпили отличаются от напильников и надфилей конструкцией насечки. Они применяются для грубой обработки мягких металлов – цинка, свинца и других, а также для опиливания дерева, кости, рога.
Спиральные сверла (см. рис. 10, е) служат для формирования отверстий различного диаметра и состоят из рабочей части, хвостовика и шейки. Рабочая часть сверла в свою очередь состоит из цилиндрической (направляющей) и режущей частей.
На направляющей части расположены две винтовые канавки, по которым отводится стружка в процессе резания. Режущая часть сверла образуется двумя режущими кромками, расположенными под определенным углом друг к другу. Этот угол называют углом при вершине. Его величина зависит от свойств обрабатываемого материала. Для стали и чугуна средней твердости он составляет 116–118°.
Хвостовик предназначен для закрепления сверла в сверлильном патроне или шпинделе станка и может быть цилиндрической или конической формы. Конический хвостовик имеет на конце лапку, которая служит упором при выталкивании сверла из гнезда.
Шейка сверла, соединяющая рабочую часть с хвостовиком, служит для выхода абразивного круга в процессе шлифования сверла при его изготовлении. На шейке обычно обозначают марку сверла.
Изготовляются сверла преимущественно из быстрорежущей стали марок Р9, Р18, Р6М5 и др. Все шире применяются металлокерамические твердые сплавы марок ВК6, ВК8 и Т15К6. Пластинками из твердых сплавов обычно оснащают только рабочую (режущую) часть сверла.
В процессе работы режущая кромка сверла притупляется, поэтому сверла периодически затачивают.
Шаберы (см. рис. 10, д) представляют собой стальные полосы или стержни определенной длины с тщательно заточенными рабочими гранями (концами). Служат для точной обработки поверхностей металлических изделий, обработки кромок, нанесения рисунков и надписей в гравировальном и литографском деле.
По конструкции шаберы разделяются на цельные и составные; по форме рабочей части – на плоские, трехгранные и фасонные, а по числу режущих граней – на односторонние, имеющие обычно деревянные рукоятки, и двусторонние без рукояток. Кроме цельных шаберов, в последнее время применяют и сменные, состоящие из держалки и вставных пластин. Режущими лезвиями таких шаберов могут служить пластинки инструментальной стали, твердого сплава и отходы быстрорежущей стали. Они изготовляются из инструментальной углеродистой стали марок У10А и У12А с последующей закалкой.
Отвертки (см. рис. 12, а) применяются для завинчивания и отвинчивания винтов и шурупов, имеющих прорезь (шлиц) на головке. Отвертка состоит из трех частей: рабочей части, стержня и ручки. Выбирают отвертку по ширине рабочей части, которая зависит от размера шлица в головке шурупа или винта.
Ключи гаечные являются необходимым инструментом при сборке и разборке болтовых соединений (см. рис. 12, б). Головки ключей стандартизированы и имеют определенный размер, который указывается на рукоятке ключа. Размеры зева (захвата) делаются с таким расчетом, чтобы зазор между гранями гайки или головки болта и гранями зева был от 0,1 до 0,3 мм.
Ключи гаечные разделяют на простые одноразмерные, универсальные (разводные) и ключи специального назначения.
Простые одноразмерные ключи бывают плоские односторонние и плоские двусторонние; накладные глухие; для круглых гаек; торцовые изогнутые и прямые. Торцовые ключи прямые и изогнутые применяются в тех случаях, когда гайку невозможно завинтить обычным ключом.
Простыми одноразмерными ключами можно завинчивать гайки только одного размера и одной формы. Раздвижные (разводные) ключи могут применяться для отвинчивания или завинчивания гаек различных размеров. Они имеют размеры зева от 19 до 50 мм при различных длинах рукояток.
Специальные ключи носят название по роду применения (например, ключ под вентиль, ключ к гайке муфты и т. д.), а также для работы в труднодоступных местах.
Ножовка ручная (см. рис. 10, г) обычно применяется для разрезания металла, а также для прорезания пазов, шлицев в головках винтов, обрезки заготовок по контуру и т. п. Ножовочные станки бывают цельными и раздвижными. Последние имеют то преимущество, что в них можно крепить ножовочные полотна различной длины.
Назначение и устройство некоторых инструментов будет изложено при описании разнообразных слесарных работ.
Для различных специализаций слесарей выпускают комплекты инструментов (рис. 13), обеспечивающие удобство их использования, переноски и хранения.
Рис. 13. Наборы слесарных инструментов
Использование рассмотренного выше ручного инструмента связано с трудоемкой и малопроизводительной работой. Однако до настоящего времени еще многие слесари применяют только ручной инструмент. В то же время значительная доля слесарных работ может быть механизирована путем использования различных стационарных и переносных машин, а также электрических и пневматических инструментов.
Применение таких инструментов позволяет значительно повысить производительность труда. Так, завертывание болтов и гаек механизированным гайковертом производится в 4–10 раз быстрее, чем вручную обычным гаечным ключом; зачистка поверхностей с помощью переносных шлифовальных машинок осуществляется в 5–20 раз быстрее, а шабрение механизированным шабером в 2–3 раза быстрее, чем ручные операции шабрения.
Механизированные ручные инструменты можно разделить по видам операций, для выполнения которых они предназначены, на инструменты для рубки и разрезания металлов, опиливания, шлифования и зачистки деталей, обработки отверстий, нарезания резьбы, шабрения и притирки, для сборки резьбовых соединений и т. п.
В зависимости от типа двигателя различают инструменты электрифицированные, питаемые электрическим током, и пневматические, действующие от сжатого воздуха.
Механизированные ручные инструменты подразделяют также по характеру движения рабочего органа (шпинделя) на инструмент с вращательным и с возвратно-поступательным движением рабочего органа.
Среди механизированных инструментов электрического действия наибольшее применение находят электрогайковерты, электрошпильковерты, электродрели, шлифовальные и полировальные машины, электронапильники, резьбонарезатели.
К инструментам пневматического действия относятся гайковерты, механические отвертки, молотки, сверлильные машинки и др.
В зависимости от конструкции корпуса различают ручной механизированный инструмент с нагрудником, с рукояткой, пистолетного типа и угловой.
Устройство и действие различных видов механизированных инструментов рассматриваются в руководствах по эксплуатации и при описании слесарных операций, в которых они применяются.
3. Измерительный и проверочный инструмент
При обработке заготовок необходимо выдерживать определенные геометрические параметры поверхностей: размеры, форму и относительное расположение. Степень приближения истинного параметра к его теоретическому значению называют точностью.
Действительная поверхность детали после обработки может иметь различные отклонения от номинальной поверхности, определенной чертежом. К таким отклонениям относятся отклонения действительных (измеренных) размеров детали от номинальных, отклонения во взаимном расположении поверхностей обработанной детали (отклонения от параллельности, перпендикулярности, заданных углов наклона одной поверхности относительно другой), волнистость поверхности и ее шероховатость.
Отклонения могут иметь разные числовые значения. Мерой точности того или иного параметра является допускаемое отклонение числового параметра от его номинального значения.
Размер детали, определенный измерительным инструментом, называют действительным размером. Деталь считается годной, если ее размер находится в интервале между наибольшим и наименьшим предельными размерами. Разность между наибольшим и наименьшим предельными размерами принято называть допуском. Размер допуска определяет точность изготовления детали. В соответствии с Единой системой допусков и посадок различают 19 квалитетов (степеней точности) изготовления деталей. Номер квалитета возрастает с увеличением допуска на размер. Таким образом, чем выше номер квалитета, тем меньшая точность требуется при обработке заготовок.
Точность, которая требуется при слесарной обработке деталей и сборке большинства механических узлов, колеблется в пределах 0,1–0,005 мм.
Точность измерения – это та ошибка, которая неизбежна при использовании в качестве измерителя того или иного инструмента. Абсолютно точное измерение получить невозможно.
Погрешность при измерении существует всегда. Слесарь же должен стремиться свести ее к минимуму. Самый простой способ уменьшения погрешности – провести измерение не один раз, а несколько, затем вычислить среднее арифметическое из результатов каждого замера.
Увеличение погрешности чаще всего вызывается ошибками, которых можно избежать. Самые распространенные ошибки, снижающие точность измерений:
- использование поврежденного измерительного инструмента;
- загрязненность рабочих поверхностей измерительного инструмента;
- неправильное положение нулевой отметки на шкале;
- неправильная установка инструмента относительно детали;
- измерение нагретой или охлажденной детали;
- измерение нагретым или охлажденным инструментом;
- неумение пользоваться инструментом;
- неправильно выбранная база измерения.
Линейные размеры металлических деталей и самого инструмента очень ощутимо меняются при нагревании или охлаждении металла, поэтому для измерений выбран следующий температурный стандарт: производить измерения необходимо при температуре 20 °C.
Слесарных измерительных и контрольных инструментов большое количество. С целью повысить точность измерений их конструкция постоянно совершенствуется.
Контрольно-измерительные слесарные инструменты можно разделить на две большие группы: универсальные и специальные.
3.1. Универсальные измерительные и контрольные инструменты
К универсальным измерительным инструментам для контроля размеров, используемым в слесарном деле, относятся инструменты, представленные на рисунке 14.
Для линейных измерений не слишком высокой точности слесари применяют обычно металлическую измерительную линейку – стальную полированную полосу с нанесенными на нее отметками (см. рис. 14, а). Поскольку металлические детали чаще всего невелики, то и длина линейки не должна превышать 200–300 мм (в редких случаях можно использовать линейку длиной до 1000 мм).
Рис. 14. Универсальные измерительные и контрольные слесарные инструменты: а – измерительная линейка; б – универсальный штангенциркуль; в – универсальный штангенциркуль с электронным индикатором; г – микрометр; д – микрометр с электронным индикатором; е – измерительная рулетка; ж – угломер; з – угломер с электронным индикатором; и – кронциркуль; к – нутромер; л – нутромер с электронным индикатором; м – угольник слесарный; н – угольник слесарный поверочный
Цена деления на измерительной линейке равна 1 мм, соответственно и точность измерения также равна 1 мм. Через каждые 5 мм штрих на линейке имеет несколько больший размер. Через каждый 1 см еще более удлиненный штрих снабжен цифрой, показывающей на количество сантиметров до начала шкалы. Масштабные линейки изготовляют жесткими или упругими из углеродистой инструментальной стали марки У7 или У8.
По измерительной линейке отсчитывают показания измерительных инструментов, таких как кронциркули, нутромеры и т. п.
Если точности, полученной с применением измерительной линейки недостаточно, пользуются другими, более точными инструментами.
Штангенциркуль (см. рис. 14, б) является универсальным измерительным инструментом, позволяющим с высокой точностью (до 0,1 мм) определять линейные (внутренние и наружные) размеры деталей и глубины отверстий. Существуют приборы специальной конструкции, с помощью которых можно измерить малые диаметры, расстояния между осями отверстий, толщину стенки трубы и пр.
Существуют четыре основных типа штангенциркулей, отличающихся конструкцией (конфигурацией и взаиморасположением измерительных поверхностей):
- двусторонние штангенциркули типа I;
- односторонние штангенциркули, снабженные глубиномером, измерительная поверхность которых выполнена из твердых сплавов (тип Т-1);
- двусторонние штангенциркули типа II;
- односторонние штангенциркули типа III.
Устройство и работу штангенциркуля рассмотрим для типа I. Штанга 1 с миллиметровыми делениями 3 с одной стороны заканчивается глубиномером 6, а с другой – губками для внутренних 4 и наружных 5 измерений (рис. 15). К неподвижным губкам примыкают подвижные губки.
Рис. 15. Основные части штангенциркуля
Подвижные губки снабжены вспомогательной шкалой 7, называемой нониусом. С помощью нониуса возможно производить измерения с точностью 0,1 мм. Подвижные губки могут свободно перемещаться вдоль штанги с помощью рамки 2. В нужном положении они фиксируются стопорным винтом 8.
Производя измерения, отсчитывают целые миллиметры по основной шкале на штанге напротив нулевого деления нониуса. Отсчет десятых долей миллиметра производится по тому делению нониуса, которое совпадает с делением основной шкалы на штанге. На рисунке 16 приведен пример отсчета размеров 0,1, 0,6 и 25,6 мм.
Рис. 16. Пользование шкалами штангенциркуля
Штангенциркули могут быть изготовлены с отсчетами различного типа:
- а) отсчет по нониусу (такие штангенциркули маркируются буквенным сочетанием ШЦ);
- б) отсчет по круговой шкале (маркировка – ШИК), выполненной в форме поворотного устройства индикации;
- в) с цифровым отсчетным устройством (ШЦЦ), обеспечивающим высокую степень автоматизации измерений (см. рис. 12, в).
В перечень основных функций штангенциркулей ШЦЦ входит:
- отображение измерительной информации в цифровом коде с указанием знака;
- запоминание результатов последних измерений (имеется не во всех моделях);
- установка нуля;
- перевод результата в любую систему измерения;
- подключение к персональному компьютеру с помощью кабеля, последующая обработка, протоколирование и сохранение результатов.
Микрометр – инструмент, с помощью которого производят измерения с точностью до 0,01 мм (см. рис. 14, г).
В состав микрометра входят скоба 1 с пяткой 2, микрометрический винт 3 с шагом 0,5 мм и стопор 4 (рис. 17). Микрометрический винт состоит из стебля 5, барабана 6 и головки 7.
Рис. 17. Устройство микрометра
Продольная шкала, нанесенная на стебель, разделена риской на основную и вспомогательную так, что расстояние между рисками двух шкал составляет 0,5 мм. Окружность барабана разделена на 50 равных делений. Поворот барабана на одно деление дает перемещение микрометрического винта на 0,01 мм. Трещотка, которой снабжена головка, позволяет передавать на микрометрический винт постоянное усилие. В случае, когда микрометрический винт упирается в пятку, торец барабана должен совместиться с нулевым делением основной продольной шкалы (рис. 18, а). При этом нулевое деление круговой шкалы на барабане должно совпадать с продольной риской основной шкалы.
При выполнении измерений барабан отходит на определенное расстояние, указывающее размер измеряемой детали. В качестве примера на рисунке 18, б торец барабана отошел на 16 делений от нуля по основной шкале и еще на деление по вспомогательной шкале. С продольной риской основной шкалы совместилось 37-е деление круговой шкалы барабана. Таким образом, размер, отложенный на микрометре, составляет 16 + 0,5 + 0,37 = 16,87 мм.
Рис. 18. Положение шкал микрометра: а – исходное положение; б – отсчет измерения
Микрометры выпускают ручные и настольные, в том числе со стрелочным и цифровым отсчетным устройством. Для цифровых микрометров (рис. 14, д) характерен ряд преимуществ:
- выставление на нуль одним нажатием кнопки;
- доступны относительные измерения (установка нуля в любой точке измерительного диапазона);
- переключение между дюймовой и метрической системами исчисления;
- во многих моделях возможна передача результатов измерений на персональный компьютер по нажатию кнопки или через заданный интервал времени.
Кронциркуль – инструмент, которым определяют наружные размеры деталей (см. рис. 14, и). Отсчет показаний производят по измерительной линейке с точностью около 0,5 мм. Состоит кронциркуль из двух изогнутых по большому радиусу ножек длиной 150–200 мм, шарнирно соединенных между собой.
Нутромер – инструмент, которым определяют внутренние размеры деталей (см. рис. 14, к). Отсчет показаний производят по измерительной линейке с точностью около 0,5 мм. Нутромер состоит из двух ножек, соединенных шарниром. Нижние концы ножек выгнуты наружу. Более точные результаты измерений дает электронный нутромер (см. рис. 14, л). Часто приходится изготовлять детали, поверхности которых сопрягаются под различными углами. Для измерения этих углов пользуются угольниками, малками, угломерами и др.
Угольник слесарный – инструмент, которым проводят проверку и разметку прямых углов (см. рис. 14, м). Угольником также удобно наносить прямые параллельные линии. Им же проверяют перпендикулярность деталей в процессе сборки оборудования. Угольники изготовляют четырех классов точности: 0, 1, 2, 3. Наиболее точные угольники класса 0. Стальные угольники с углом 90° бывают различных размеров, цельные или составные.
Для проверки прямых углов угольник накладывают на проверяемую деталь и определяют правильность обработки проверяемого угла на просвет. При проверке наружного угла угольник накладывают на деталь его внутренней частью, а при проверке внутреннего угла – наружной частью. Наложив угольник одной стороной на обработанную сторону детали, слегка прижимая его, совмещают другую сторону угольника с обрабатываемой стороной детали и по образовавшемуся просвету судят о точности выполнения прямого угла. Иногда размер просвета определяют с помощью щупов (см. рис. 20, ж).
Угольник слесарный поверочный с широким основанием (см. рис. 14, н) используется в целях контроля взаимно перпендикулярного расположения деталей в процессе монтажа различного оборудования.
Угломер – прибор (инструмент), предназначенный для измерения геометрических углов в различных конструкциях, в деталях и между поверхностями (см. рис. 14, ж). Измерение производится в градусах, на основе линейчатой шкалы, линейчато-круговой шкалы (с механическим указателем или стрелкой), нониуса или в электронном виде, в зависимости от типа прибора.
Простой угломер состоит из линейки 1 и транспортира 2 (рис. 19). При измерениях угломер накладывают на деталь так, чтобы линейка и нижний обрез m полки транспортира совпадали со сторонами измеряемой детали 3. Величину угла определяют по указателю 4, перемещающемуся по шкале транспортира вместе с линейкой. Простым угломером можно измерять величину углов с точностью 0,5–1,0°.
Рис. 19. Конструкция простого угломера
Современные производители выпускают широкий спектр электронных угломеров (см. рис. 14, з), имеющих разную конструкцию и обладающих различными функциональными возможностями.
Цифровой угломер является незаменимым при выполнении разметки объектов, проектных, строительных и монтажных работ. В отличие от используемых ранее механических угломеров, электронные устройства обладают гораздо более высокой точностью, что не только повышает качество измерения, но и значительно упрощает его выполнение.
Электронный угломер способен обеспечивать измерение углов до 180°. Он также позволяет выполнять простые вычислительные операции, включая сложение и вычитание, что упрощает ведение работ. Важным преимуществом является то, что цифровой угломер может использоваться также для измерения уклонов. В результате значительно расширяется область применения этих устройств.
Если приходится измерять длинномерные детали, то измерительная рулетка – один из самых распространенных и необходимых инструментов. Она представляет собой стальную или пластмассовую ленту, на поверхности которой нанесена шкала с ценой деления 1 мм (см. рис. 14, е). Ширина ленты обычно не превышает 25 мм. Ленту помещают в металлический или пластиковый корпус. Сейчас выпускают ленту в прорезиненном корпусе, что значительно увеличивает ударопрочность инструмента. Лента втягивается в корпус пружиной (самосвертывающиеся рулетки) или вращением рукоятки (простые рулетки).
Рулетки можно условно разделить на короткие и длинные.
Короткие рулетки имеют длину от 2 до 10 м, как правило, оснащены сматывающим механизмом. Также у них есть кнопка «Стоп», которая позволяет на определенной длине зафиксировать ленту.
Длинные рулетки достигают длины от 10 до 50 м. Снабжены такие рулетки ручным скручивающим механизмом. Их еще часто называют измерительной лентой.
Рулетки применяются для измерения линейных размеров: длины, ширины, высоты деталей и расстояний между их отдельными частями, а также длин дуг, окружностей и кривых.
3.2. Специальные измерительные и контрольные инструменты
К специальным инструментам для измерения и контроля различных параметров деталей и конструкций относятся инструменты, представленные на рисунке 20.
Линейка проверочная – инструмент, которым проверяют прямолинейность поверхностей (рис. 20, а).
В процессе обработки плоскостей пользуются проверочными лекальными линейками (рис. 20, б). Они подразделяются на линейки лекальные с двусторонним скосом, трехгранные и четырехгранные.
Рис. 20. Специальные измерительные и контрольные слесарные инструменты: а – линейка проверочная; б – линейки проверочные лекальные; в – малка; г – курвиметр; д – уровень; е – резьбомер; ж – щуп; з – призма проверочная; и – штангенглубиномер
Лекальные линейки изготовляют с высокой точностью, они имеют тонкие ребра с радиусом закругления 0,1–0,2 мм, благодаря чему можно весьма точно определить отклонение от прямолинейности по способу световой щели (на просвет). Для этого линейку своим ребром устанавливают на проверяемую поверхность детали против света. При этом имеющиеся отклонения от прямолинейности будут заметны между линейкой и поверхностью детали. При хорошем освещении можно обнаружить отклонение от прямолинейности до 0,005–0,002 мм. Лекальные линейки изготовляют длиной от 25 до 500 мм из углеродистой инструментальной или легированной стали с последующей закалкой.
Малка – инструмент, с помощью которого переносят размеры углов с детали на угломерный инструмент или на заготовку (рис. 20, в). При производстве слесарных разметочных работ применяют металлическую малку.
Простая малка состоит из обоймы и линейки, закрепленной шарнирно между двумя планками обоймы. Шарнирное крепление обоймы позволяет линейке занимать по отношению к обойме положение под любым углом. Малку устанавливают на требуемый угол по образцу детали или по угловым плиткам (рис. 21). Требуемый угол фиксируется винтом с барашковой гайкой.
Рис. 21. Способы применения малки
Штангенглубиномеры предназначены для измерений глубины элементов деталей (см. рис. 20, и). Состоят из штанги, имеющей шкалу, и рамки с нониусом (ШГ) или круговой шкалой с отсчетным устройством (ШГК) или электронным цифровым отсчетным устройством (ШГЦ). Принцип работы аналогичен штангенциркулю.
Уровень (ватерпас) – прибор, которым определяют горизонтальность поверхности (см. рис. 20, д). Уровень представляет собой брусок, в котором закреплена стеклянная прозрачная трубка, заполненная жидкостью, обычно спиртом, с небольшим пузырьком газа. Трубка с жидкостью имеет дугообразное продольное сечение. Если трубка с жидкостью расположена горизонтально, пузырек газа находится строго посередине трубки. Обычно в уровне расположены две трубки с жидкостью для проверки горизонтальных и вертикальных поверхностей.
Курвиметр – прибор, которым измеряют извилистые криволинейные отрезки (см. рис. 20, г). Производя измерения, зубчатое колесико курвиметра прокатывают по извилистой линии на чертеже или карте. Пройденное расстояние отсчитывают по циферблату. Обычно механический курвиметр снабжен двумя циферблатами, один из которых проградуирован в сантиметрах, а другой – в дюймах. Погрешность в измерении у механического курвиметра составляет 0,5 %.
Резьбомер – измерительный инструмент, представляющий собой набор различных резьбовых шаблонов (см. рис. 20, е). Резьбомер служит для измерения шага метрической резьбы либо для дюймовой резьбы числа витков на 1 дюйм.
Резьбовой шаблон – это зубчатая пластина с определенным шагом зубьев. На каждом метрическом шаблоне указан шаг резьбы в миллиметрах, а на каждом дюймовом шаблоне – число витков на 1 дюйм резьбы.
Набор шаблонов помещен в оправу из двух накладок, скрепленных винтами. На метрическом резьбомере стоит клеймо: «М60°», а на дюймовом – «Д55°».
Призмы проверочные (см. рис. 20, з) и разметочные – приспособления, с помощью которых делают проверку и разметку валов и цилиндрических деталей. Призмы изготовляют в комплектах попарно, что позволяет применять их как опоры при контроле и разметке длинных цилиндрических деталей.
Все измерительные приборы отличаются высокой точностью исполнения и требуют тщательного ухода. Обеспечение соответствующих условий использования и хранения является гарантией долговечности их работы и точности. Неправильное обращение ведет к преждевременному износу и порче, невозможности эксплуатации и даже к повреждению измерительных приборов.
При эксплуатации измерительного инструмента и приборов недопустимы механические повреждения, резкие перепады температуры, намагничивание, коррозия.
Необходимые требования при эксплуатации измерительного инструмента и приборов – соблюдение чистоты, квалифицированное обслуживание и прежде всего хорошее знание конструкций и условий эксплуатации измерительных приборов.
4. Слесарные работы
Слесарные работы – это обработка металлов, обычно дополняющая станочную механическую обработку или завершающая изготовление изделий соединением деталей, сборкой машин и механизмов, а также их регулированием. Они выполняются ручным или механизированным слесарным инструментом либо на станках.
Слесарные работы являются неотъемлемой частью технологического процесса предприятия.
Технологический процесс – это способ или совокупность способов изменения формы, размеров, физических свойств материалов или полуфабрикатов для получения изделия требуемой конфигурации и качества.
Технологический процесс состоит из отдельных операций.
Операция – это часть технологического процесса, выполняемая слесарем на одном рабочем месте с использованием ручного или механизированного инструмента, механизмов, приспособлений при обработке одной детали.
Элементами технологической операции являются установ, технологический переход, вспомогательный переход, рабочий ход, вспомогательный ход, позиция.
Установ – часть технологической операции, выполняемая при неизменном закреплении обрабатываемой детали или собираемой сборочной единицы. Например, сверление в детали одного или нескольких отверстий разного диаметра при неизменном закреплении детали.
Технологический переход – законченная часть операции, характеризуемая постоянством применяемого инструмента и поверхностей, образуемых при обработке или соединяемых при сборке. Например, соединение втулки с валом.
Вспомогательный переход – часть операции без изменения геометрии обрабатываемой поверхности или положения собираемых деталей, необходимая для выполнения технологического перехода (установка заготовки, смена инструментов и т. д.).
Рабочий ход – законченная часть операции, связанная с однократным перемещением инструмента относительно обрабатываемой детали, необходимая для осуществления изменения геометрии детали.
Вспомогательный ход не связан с изменением геометрии детали, но необходим для осуществления рабочего хода.
Позиция – это фиксированное положение, занимаемое закрепленной обрабатываемой деталью или собираемой сборочной единицей совместно с приспособлением относительно инструмента или неподвижной части оборудования для выполнения определенной части операции.
Карта технологического процесса является документом, содержащим описание процесса изготовления, сборки или ремонта изделия (включая контроль и перемещения) по всем операциям одного вида работ, выполняемых в одном цехе, в технологической последовательности с указанием данных о средствах технологического оснащения, материальных и трудовых нормативах. В ней определяются также место работы, вид и размеры материала, основные поверхности обработки детали и ее установка, рабочий инструмент и приспособления, а также продолжительность каждой операции.
Технологический процесс разрабатывается на основе чертежа, который для массового и крупносерийного производства должен быть выполнен очень детально. При единичном производстве часто дается только маршрутный технологический процесс с перечислением операций, необходимых для обработки или сборки.
Слесарные работы различных видов объединяет единая технология выполнения операций, к которым относятся разметка, правка и гибка, рубка, резка, распиловка, опиливание, сверление, зенкование и зенкерование, развертывание отверстий, нарезание резьбы, клепка, шабрение, притирка и доводка, пайка, лужение, склеивание и др.
На предприятиях серийного производства, где изготовляют однородные детали большими партиями, повышается точность механической обработки и соответственно уменьшается объем слесарных работ, но слесарь выполняет ручные работы, которые не могут быть выполнены машиной.
На предприятиях или в мастерских, выпускающих разнородные изделия в небольших количествах (единичное производство), от слесарей требуется универсальность. При необходимости он должен уметь работать на разных станках и выполнять различные слесарные работы. Рассмотрим основные из них.
4.1. Разметка
Разметкой называется операция нанесения линий и точек на заготовку, предназначенную для обработки. Линии и точки обозначают границы обработки.
Существуют два вида разметки: плоская и пространственная. Разметка называется плоской, когда линии и точки наносятся на плоскость, пространственной – когда разметочные линии и точки наносятся на геометрическое тело любой конфигурации.
Простыми разметочными и измерительными инструментами, используемыми при слесарных работах, являются молоток, чертилка, маркер, кернер обыкновенный, угольник, циркуль, линейка с делениями, штангенциркуль и кронциркуль.
Плоскую или пространственную разметку детали проводят на основании чертежа.
До разметки заготовка должна пройти обязательную подготовку, которая включает в себя следующие операции: очистка детали от грязи и коррозии; обезжиривание детали; осмотр детали с целью обнаружить дефекты (трещины, раковины, искривления); проверка габаритных размеров, а также припусков на обработку; определение разметочной базы; покрытие при необходимости белой краской поверхностей, подлежащих разметке и нанесению на них линий и точек; определение оси симметрии.
Разметочная база – это конкретная точка, ось симметрии или плоскость, от которой отмеряются, как правило, все размеры на детали.
Работы по разметке лучше всего выполнять на разметочной плите. Плита представляет собой чугунную отливку, горизонтальная рабочая поверхность и боковые грани которой очень точно обработаны. На рабочей поверхности больших плит делают продольные и поперечные канавки глубиной 2–3 мм и шириной 1–2 мм, которые образуют квадраты со стороной 200 или 250 мм. Это облегчает установку на плите различных приспособлений.
Разметку обычно осуществляют накерниванием – нанесением мелких точек-углублений на поверхности детали. Они определяют осевые линии и центры отверстий, прямые или кривые линии на изделии, необходимые для обработки. Накернивание выполняют в целях обозначения на детали стойких и заметных знаков, определяющих базу, границы обработки или место сверления, с использованием чертилки, кернера и молотка.
Разметка с использованием шаблона применяется при изготовлении значительного количества одинаковых деталей. Шаблон, выполненный из жести толщиной 0,5–2,0 мм, накладывается на плоскую поверхность детали и обводится чертилкой по контуру.
Точность разметки зависит от степени точности разметочной плиты, вспомогательных приспособлений (угольников и разметочных ящиков), мерительных инструментов, инструмента, используемого для перенесения размеров, а также от квалификации разметчика. Точность разметки обычно составляет 0,5–0,08 мм; при использовании эталонных плиток 0,05–0,02 мм.
При разметке следует осторожно обращаться с заостренными инструментами.
Для установки на разметочную плиту тяжелых деталей необходимо пользоваться талями, тельферами или кранами.
4.2. Правка и гибка металлов
Правкой называется операция по устранению дефектов заготовок и деталей в виде вогнутости, выпуклости, волнистости, коробления, искривления и т. д. Ее сущность заключается в сжатии выпуклого слоя металла и расширении вогнутого.
Металл подвергается правке как в холодном, так и в нагретом состоянии. Выбор того или иного способа правки зависит от величины прогиба, размеров и материала заготовки (детали).
Правка может быть ручной (на стальной или чугунной правильной плите) или машинной (на правильных вальцах или прессах).
Правильная плита, так же как и разметочная, должна быть массивной. Ее размеры могут быть от 400×400 мм до 1500×3000 мм. Устанавливается плита на металлические или деревянные подставки, обеспечивающие ее устойчивость и горизонтальность положения.
Для правки закаленных деталей (рихтовки) используют рихтовальные бабки. Они изготовляются из стали и закаливаются. Рабочая поверхность бабки может быть цилиндрической или сферической радиусом 150–200 мм.
Ручную правку выполняют специальными молотками с круглым, радиусным или вставным из мягкого металла бойком. Тонкий листовой металл правят киянкой (деревянным молотком).
При правке металла очень важно правильно выбрать места, по которым следует наносить удары. Силу удара необходимо соизмерять с кривизной металла и уменьшать по мере перехода от наибольшего прогиба к наименьшему.
При большом изгибе полосы на ребро удары наносят носком молотка для односторонней вытяжки (удлинения) мест изгиба. Полосы со скрученным изгибом правят методом раскручивания. Проверяют правку на глаз, а при высоких требованиях к прямолинейности полосы – лекальной линейкой или на проверочной плите.
Металл круглого сечения можно править на плите или на наковальне. Если пруток имеет несколько изгибов, то правят сначала крайние изгибы, а затем расположенные в середине.
Наиболее сложной является правка листового металла. Лист кладут на плиту выпуклостью вверх. Удары наносят молотком от края листа по направлению к выпуклости. Под действием ударов ровная часть листа будет вытягиваться, а выпуклая выправляться.
При правке закаленного листового металла наносят несильные, но частые удары носком молотка по направлению от вогнутости к ее краям. Верхние слои металла растягиваются, и деталь выпрямляется.
Валы и круглые заготовки большого сечения правят с помощью ручного винтового или гидравлического пресса.
По приемам работы и характеру рабочего процесса к правке металлов очень близко стоит другая слесарная операция – гибка металлов.
Гибкой называют операцию придания металлу определенной конфигурации без изменения его сечения и обработки металла резанием.
Гибку производят холодным или горячим способом вручную либо с использованием приспособлений и машин. Сущность ее заключается в том, что одна часть заготовки перегибается по отношению к другой на какой-либо заданный угол. Напряжения изгиба должны превышать предел упругости, а деформация заготовки должна быть пластической. Только в этом случае заготовка сохранит приданную ей форму после снятия нагрузки.
Ручную гибку производят в тисках с помощью слесарного молотка и различных приспособлений. Последовательность выполнения гибки зависит от размеров контура и материала заготовки.
Гибку тонкого листового металла производят киянкой. При использовании для гибки металлов различных оправок их форма должна соответствовать форме профиля детали с учетом деформации металла.
Выполняя гибку заготовки, важно правильно определить ее размеры. Расчет длины заготовки выполняют по чертежу с учетом радиусов всех изгибов. Для деталей, изгибаемых под прямым углом без закруглений с внутренней стороны, припуск заготовки на изгиб должен составлять 0,6–0,8 толщины металла.
При пластической деформации металла в процессе гибки нужно учитывать упругость материала: после снятия нагрузки угол загиба несколько увеличивается.
Изготовление деталей с очень малыми радиусами изгиба связано с опасностью разрыва наружного слоя заготовки в месте изгиба. Поэтому детали с малыми радиусами закруглений необходимо изготовлять из пластичных материалов или предварительно подвергать отжигу.
При изготовлении изделий иногда возникает необходимость в получении криволинейных участков труб, изогнутых под различными углами. Гибке могут подвергаться цельнотянутые и сварные трубы, а также трубы из цветных металлов и сплавов. Гибку труб производят с наполнителем (обычно сухой речной песок) или без него. Это зависит от материала трубы, ее диаметра и радиуса изгиба. Наполнитель предохраняет стенки трубы от образования в местах изгиба складок и морщин (гофров).
4.3. Рубка металлов
Рубкой называется операция, при которой с помощью зубила и слесарного молотка с заготовки удаляют слои металла или разрубают заготовку.
Физической основой рубки является действие клина, форму которого имеет рабочая (режущая) часть зубила. Рубка применяется в тех случаях, когда станочная обработка заготовок трудновыполнима или нерациональна.
Основным рабочим (режущим) инструментом при рубке является зубило, а ударным – молоток. Для рубки металлов применяют молотки массой 400–600 г.
Угол заострения зубила выбирается в зависимости от твердости обрабатываемого материала. Для наиболее распространенных материалов рекомендуются следующие углы заострения: для твердых (твердая сталь, чугун) – 70°; для материалов средней твердости (сталь) – 60°; для мягких (медь, латунь) – 45°; для алюминиевых сплавов – 35°.
С помощью рубки удаляют (срубают) с заготовки неровности металла, снимают твердую корку, окалину, острые кромки детали, вырубают пазы и канавки, разрубают листовой металл на части.
Для вырубания узких пазов и канавок пользуются зубилом с узкой режущей кромкой – крейцмейселем (см. рис. 10, б). Такое зубило может применяться и для снятия широких слоев металла: сначала прорубают канавки узким зубилом, а оставшиеся выступы срубают широким зубилом. Для вырубания профильных канавок (полукруглых, двугранных и др.) применяются специальные крейцмейсели-канавочники, отличающиеся только формой режущей кромки.
Разрубаемый материал (жесть, полосовое железо, стальная лента, профиль, пруток) следует положить на стальную плиту или на наковальню так, чтоб он прилегал всей своей поверхностью к поверхности плиты или наковальни. Материал, от которого нужно отрубить заготовку, может быть закреплен в тисках. Если металл имеет длину больше плиты или наковальни, его свешивающийся конец должен опираться на соответствующие подпорки. Острие зубила ставят на расстояние 1–2 мм от размеченной линии. Ударяя молотком по зубилу, разрубают жесть. Передвигая зубило вдоль контура и одновременно ударяя по нему молотком, вырубают деталь по контуру и отделяют ее от листа жести.
Вырубку элемента из толстого листового материала выполняют сначала с одной стороны листа, затем его переворачивают на другую сторону и вырубают окончательно (продвигая зубило по полученному следу от острия зубила). В последующем деталь по контуру обрабатывают ручным напильником.
Рубка металлов – операция очень трудоемкая. Для облегчения труда и повышения его производительности используют механизированные инструменты. Среди них наибольшее распространение имеет пневматический рубильный молоток. Он приводится в действие сжатым воздухом, который подается по шлангу от постоянной пневмосети или передвижного компрессора.
4.4. Резка металлов
Резкой называется операция разделения материала (предмета) на две отдельные части с помощью острогубцев (кусачек), ручных ножниц, зубила или специальных механических ножниц.
Распиловка – операция разделения материала (предмета) ручной либо механической ножовкой или круглой пилой.
Сущность операции разрезания металла острогубцами (кусачками) и ножницами заключается в разделении проволоки, листового или полосового металла на части под давлением двух движущихся навстречу друг другу клиньев (режущих ножей).
Режущие кромки у острогубцев смыкаются одновременно по всей длине. У ножниц же сближение лезвий идет постепенно от одного края к другому. Их режущие кромки не смыкаются, а сдвигаются одна относительно другой. И острогубцы, и ножницы представляют собой шарнирное соединение двух рычагов, у которых длинные плечи выполняют роль рукояток, а короткие – режущих ножей.
Острогубцы (кусачки) используют главным образом для разрезания проволоки. Угол заострения режущих кромок острогубцев может быть различным в зависимости от твердости разрезаемого материала. У многих острогубцев он равен 55–60°.
Ручные ножницы применяют для разрезания стальных листов толщиной 0,5–1,0 мм и листов из цветных металлов толщиной до 1,5 мм.
В зависимости от устройства режущих ножей ручные ножницы делятся на прямые – с прямыми режущими ножами, предназначенные в основном для разрезания металла по прямой линии или по окружности большого радиуса; кривые – с криволинейными ножами; пальцевые – с узкими режущими ножами для вырезания в листовом металле отверстий и поверхностей с малыми радиусами.
По расположению режущих ножей ручные ножницы делятся на правые и левые. У правых ножниц скос режущей кромки нижнего ножа находится справа, у левых – слева.
Стуловые ножницы отличаются от обычных ручных большими размерами и применяются для разрезания листового металла толщиной до 2 мм.
Рычажные ножницы применяются для разрезания листовой стали толщиной до 4 мм (цветных металлов – до 6 мм). Верхний шарнирно закрепленный нож приводится в действие от рычага. Нижний нож закреплен неподвижно.
Для механизации тяжелого и трудоемкого процесса разрезания листового металла используют, как уже отмечалось, электрические ножницы.
Ручная ножовка применяется для разрезания сравнительно толстых листов металла и круглого или профильного проката. Ножовкой можно также прорезать шлицы, пазы, обрезать и вырезать заготовки по контуру и др.
Ножовочное полотно (режущая часть ножовки) представляет собой тонкую и узкую стальную пластину с зубьями на одном из ребер. Его изготовляют из инструментальной или быстрорежущей стали. Длина наиболее распространенных ножовочных полотен составляет 250–300 мм. Каждый зуб полотна имеет форму клина (резца).
Для разрезания более твердых материалов угол заострения делают больше, для мягких – меньше. Чтобы ширина разреза, сделанного ножовкой, была немного больше толщины полотна, выполняют разводку зубьев. Это предотвращает заклинивание полотна и облегчает работу.
Более высокая производительность труда достигается при использовании пневматической ножовки.
Разрезание стальных труб сравнительно больших диаметров – операция трудоемкая, поэтому ее выполняют специальными труборезами (рис. 22).
Рис. 22. Труборез
Труборез состоит из скобы, двух неподвижных роликов, подвижного ролика (резца) и рукоятки. Труборез надевают на трубу, закрепленную в тисках или специальном приспособлении, вращением рукоятки придвигают подвижный ролик до соприкосновения с поверхностью трубы. Затем, поворачивая за рукоятку весь труборез вокруг трубы и постепенно поджимая воротком подвижный ролик, разрезают трубу.
4.5. Опиливание металлов
Опиливание – это процесс снятия припуска обыкновенными напильниками, надфилями или рашпилями. Оно основано на ручном или механическом снятии с обрабатываемой поверхности тонкого слоя материала.
Опиливание относится к основным и наиболее распространенным операциям. Оно дает возможность получить окончательные размеры и необходимую шероховатость поверхности изделия.
Различают следующие виды опиливания поверхностей: плоских и криволинейных, угловых, параллельных, сложных и фасонных.
Выбор напильника зависит от вида материала и вида опиливания, величины снимаемого слоя и обрабатываемой детали.
Форму напильников выбирают в зависимости от конфигурации обрабатываемого места. Плоские напильники используют для опиливания плоских, криволинейных выпуклых и наружных сферических поверхностей; квадратные напильники – для опиливания квадратных и прямоугольных отверстий; трехгранные – для обработки трехгранных поверхностей, заточки пил, а также для опиливания плоских поверхностей, расположенных под острым углом; ножовочные – для опиливания кромок острых углов, а также для выполнения узких канавок; ромбические – для обработки очень сложных контуров изделий; круглые – для выполнения полукруглых и круглых отверстий; овальные – для опиливания овальных отверстий; полукруглые и линзовые – для обработки криволинейных и вогнутых поверхностей.
Улучшение условий и повышение производительности труда при опиливании металла достигается применением механизированных (электрических и пневматических) напильников.
4.6. Сверление, зенкование, зенкерование и развертывание отверстий
В работе слесаря по изготовлению, ремонту или сборке деталей механизмов и машин часто возникает необходимость получения в этих деталях самых различных отверстий. Для этого производят сверление, зенкование, зенкерование и развертывание отверстий.
Сущность данных операций заключается в том, что процесс резания (снятия слоя материала) осуществляется вращательным и поступательным движениями режущего инструмента (сверла, зенкера и т. д.) относительно своей оси. Эти движения создаются с помощью ручных (коловорот, дрель) или механизированных (электрическая дрель) приспособлений, а также станков (сверлильных, токарных и др.).
Сверление – один из видов получения и обработки отверстий резанием специальным инструментом – сверлом.
Как и любой другой режущий инструмент, сверло работает по принципу клина. По конструкции и назначению сверла делятся на перовые, спиральные, центровочные и др. В современном производстве применяются преимущественно спиральные сверла и реже специальные виды сверл.
Сверлами производят не только сверление глухих (засверливание) и сквозных отверстий, т. е. получение этих отверстий в сплошном материале, но и рассверливание – увеличение размера (диаметра) уже полученных отверстий.
Зенкованием называется обработка верхней части отверстий в целях получения фасок или цилиндрических углублений, например под потайную головку винта или заклепки. Выполняется зенкование зенковками или сверлом большего диаметра.
Зенкерование – это обработка отверстий, полученных литьем, штамповкой или сверлением, для придания им цилиндрической формы, повышения точности и качества поверхности. Зенкерование выполняется специальными инструментами – зенкерами (см. рис. 10, м). Зенкеры могут быть с режущими кромками на цилиндрической или конической поверхности (цилиндрические и конические зенкеры), а также с режущими кромками, расположенными на торце (торцовые зенкеры). Для обеспечения соосности обрабатываемого отверстия и зенкера на торце последнего иногда делают гладкую цилиндрическую направляющую часть.
Зенкерование может быть процессом окончательной обработки или подготовительным к развертыванию. В последнем случае при зенкеровании оставляют припуск на дальнейшую обработку.
Развертывание – это чистовая обработка отверстий. По своей сущности она подобна зенкерованию, но обеспечивает более высокую точность и малую шероховатость обработки поверхности отверстий. Выполняется эта операция слесарными (ручными) или станочными (машинными) развертками.
Рассмотренные операции обработки отверстий выполняются в основном на сверлильных или токарных станках. Однако, если деталь невозможно установить на станок или отверстия расположены в труднодоступных местах, обработка производится вручную с помощью воротков, ручных или механизированных (электрических и пневматических) дрелей.
Если допускается некоторое повреждение поверхности в зоне отверстия и не требуются чистота и точность выполнения отверстия, то для его образования может применяться пробойник.
4.7. Нарезание резьбы
Это образование винтовой поверхности на наружной либо внутренней цилиндрической или конической поверхностях детали.
Приемы нарезания резьбы, и особенно применяемый при этом режущий инструмент, во многом зависят от вида и профиля резьбы.
Резьбы бывают однозаходные, образованные одной винтовой линией (ниткой), или многозаходные, образованные двумя и более нитками. По направлению винтовой линии резьбы подразделяют на правые и левые.
Профилем резьбы называется сечение ее витка плоскостью, проходящей через ось цилиндра или конуса, на котором выполнена резьба.
Для нарезания резьбы важно знать основные ее элементы: шаг, наружный, средний и внутренний диаметры, форму профиля резьбы.
Шагом резьбы называют расстояние между двумя одноименными точками соседних профилей резьбы, измеренное параллельно оси резьбы. Резьба М4 имеет шаг 0,7 мм; М6 – 1 мм; М8 – 1,25 мм; М10 – 1,5 мм; М12 – 1,75 мм; М14 – 2 мм; М16 – 2 мм; М18 – 2,5 мм; М20 – 2,5 мм; М22 – 2,5 мм; М24 – 3 мм; М27 – 3 мм; М30 – 3,5 мм.
Наружный диаметр – наибольшее расстояние между крайними наружными точками, измеренное в направлении, перпендикулярном оси резьбы.
Внутренний диаметр – наименьшее расстояние между крайними внутренними точками резьбы, измеренное в направлении, перпендикулярном оси.
Средний диаметр – расстояние между двумя противоположными параллельными боковыми сторонами профиля резьбы, измеренное в направлении, перпендикулярном оси.
По форме профиля резьбы подразделяют на треугольные, прямоугольные, трапецеидальные, упорные (профиль в виде неравнобокой трапеции) и круглые.
В зависимости от системы размеров резьбы делятся на метрические, дюймовые, трубные и др.
В метрической резьбе угол треугольного профиля равен 60°, наружный, средний и внутренний диаметры и шаг резьбы выражаются в миллиметрах. Пример обозначения: М201,5 (первое число – наружный диаметр, второе – шаг). Параметры в дюймовой резьбе определяются в дюймах.
Трубная резьба отличается тем, что ее исходным размером является не наружный диаметр резьбы, а диаметр отверстия трубы, на наружной поверхности которой нарезана резьба.
Нарезание винтовой поверхности на болтах, валиках и других наружных поверхностях деталей можно выполнять вручную или машинным способом. К ручным инструментам относятся круглые разрезные и неразрезные плашки (см. рис. 10, з), а также четырех- и шестигранные пластинчатые плашки, клуппы для нарезания резьбы на трубах. Для крепления плашек используются плашкодержатели (см. рис. 11, е) и клуппы. Круглая плашка используется также для машинного нарезания резьбы.
Нарезание наружной резьбы машинным способом может производиться на токарных станках резьбовыми резцами, гребенками, резьбонарезными головками с радиальными, тангенциальными и круглыми гребенками, вихревыми головками, а также на сверлильных станках резьбонарезными головками, на фрезерных станках резьбонарезными фрезами и на резьбошлифовальных станках однониточными и многониточными кругами.
Нарезание резьбы в отверстиях выполняют метчиками (см. рис. 10, и) вручную и машинным способом. Различают цилиндрические и конические метчики. Ручные метчики бывают одинарные, двух- и трехкомплектные. Обычно используют комплект, состоящий из трех метчиков: чернового, обозначенного одной черточкой или цифрой 1; среднего, обозначенного двумя черточками или цифрой 2; и чистового, обозначенного тремя черточками или цифрой 3.
Имеются специальные метчики: для плашек (плашечные метчики с длинной режущей частью), для гаек, для труб, для легких сплавов, а также с конической рабочей частью. Метчиками можно нарезать резьбу в сквозных и глухих отверстиях или калибровать маточными метчиками ранее нарезанную резьбу.
На хвостовик ручного метчика, заканчивающийся квадратной головкой, надевается вороток с постоянным или регулируемым квадратным отверстием (см. рис. 11, ж).
В ряде случаев применяются комбинированные метчики, которыми можно сверлить и нарезать резьбу.
Машинные метчики применяются для нарезания внутренней резьбы на сверлильных и токарных станках всех типов. Ими можно нарезать резьбу за один или несколько проходов. За один проход нарезают резьбу с шагом до 3 мм, а за два-три прохода – резьбу с более крупным шагом, особо длинную резьбу, а также гладкую резьбу в труднообрабатываемых материалах независимо от шага.
Перед нарезанием резьбы пруток должен быть очищен от ржавчины, на его торцовой поверхности должна быть снята заходная фаска.
4.8. Клепальные работы
Клепка – это операция получения неразъемного соединения материалов с использованием стержней, называемых заклепками. Заклепка, заканчивающаяся головкой, устанавливается в отверстие соединяемых материалов. Выступающая из отверстия часть заклепки расклепывается в холодном или горячем состоянии, образуя вторую головку.
Заклепочные соединения применяются:
- в конструкциях, работающих под действием вибрационной и ударной нагрузки, при высоких требованиях к надежности соединения, если сварка этих соединений технологически затруднена или невозможна;
- если нагревание мест соединения при сварке недопустимо вследствие возможности коробления, термических изменений в металлах и появляющихся значительных внутренних напряжениях;
- в случаях соединения различных металлов и материалов, для которых сварка неприменима.
Заклепки изготовляют из углеродистой стали, меди, латуни или алюминия (рис. 23, а). При соединении металлов подбирают заклепку из того же материала, что и соединяемые элементы.
Рис. 23. Заклепки: а – общий вид заклепок; б – строение заклепки
Заклепка состоит из закладной головки и цилиндрического стержня, называемого телом заклепки (рис. 23, б). Часть заклепки, выступающая с другой стороны соединяемого материала и предназначенная для формирования замыкающей головки, называется ножкой.
Для выполнения заклепочных соединений применяются следующие основные виды заклепок: с полукруглой головкой, с потайной головкой, с полупотайной головкой, трубчатая, взрывная (рис. 24). Кроме того, могут применяться заклепки с плоскоконической, плоской, конической головкой, с конической головкой и подголовкой, с овальной головкой, разрезные и др.
Рис. 24. Виды заклепок: а, б – с полукруглой головкой; в – с цилиндрической головкой; г – с потайной головкой; д – с полупотайной головкой; е – взрывная; ж – трубчатая
Стальную заклепку диаметром до 14 мм можно расклепывать в холодном состоянии. Заклепки диаметром более 14 мм клепаются в горячем состоянии. Диаметры заклепок от 10 до 37 мм увеличиваются через 3 мм.
Заклепочные соединения бывают внахлестку, встык с одной накладкой, встык с двумя накладками симметрично или несимметрично (рис. 25).
Рис. 25. Виды заклепочных соединений: а – внахлестку; б – встык с одной накладкой; в – встык с двумя накладками
С точки зрения прочности и плотности используются следующие виды заклепочных соединений: прочные, от которых требуется только механическая прочность; плотные, к которым предъявляются только требования плотности и герметичности; прочноплотные, от которых помимо механической прочности требуется также герметичность соединения. Последнее достигается увеличением головки и наличием подголовки заклепки, достаточно частым размещением заклепок, подчеканкой обреза соединяемых листов и головок заклепок.
При клепке используются просверленные, проколотые или пробитые отверстия. При прочных, плотных и прочноплотных заклепочных соединениях используются исключительно просверленные отверстия.
Заклепочные швы делятся на продольные, поперечные и наклонные. Они могут быть однорядные, двухрядные и многорядные (параллельные и с шахматным расположением заклепок). Швы могут быть полные и неполные.
В зависимости от диаметра заклепки и вида клепки используется ручная и механическая клепка.
Замыкающую головку получают ударной клепкой и клепкой давлением. Ударная клепка универсальная, но шумная; клепка давлением более качественная и бесшумная.
Для ручной клепки используются молотки для формирования головки заклепки, обжимки, поддержки, прихваты и клещи.
Для механической клепки используются пневматические или электрические молотки, клепальные клещи, подпоры подголовки заклепок, консоли. На больших промышленных предприятиях используются клепальные машины – эксцентриковые и гидравлические.
4.9. Шабрение
Это процесс получения требуемой по условиям работы точности форм, размеров и относительного положения поверхностей для обеспечения их плотного прилегания или герметичности соединения.
При шабрении срезаются тонкие стружки с неровных поверхностей, предварительно уже обработанных напильником или другим режущим инструментом.
Инструменты для шабрения называются шаберами (см. рис. 10, д). Различают ручные и механические шаберы.
При шабрении используются чугунные плиты для проверки поверхностей плоских деталей, плоские и трехгранные линейки для проверки плоскостности поверхности, призмы, плиты в виде прямоугольного параллелепипеда, контрольные валики, щупы и другие инструменты для контроля качества шабрения и притирки. Кроме упомянутых инструментов применяют щетки и обтирочные материалы.
Шабрение применяется, если нужно удалить следы обработки напильником или другим инструментом, а также если требуется получить высокую степень точности и малую шероховатость поверхности деталей машин, соединяемых друг с другом. Шабрение особенно часто применяется при обработке деталей пар трения.
Для выявления неровностей на деталях используется краска – смесь машинного масла с парижской лазурью или ультрамарином, имеющая консистенцию легкой пасты, иногда – смесь машинного масла с сажей.
Краска наносится тонким слоем на плиту или линейку кисточкой либо чистой ветошью, после чего плита или линейка накладывается на предназначенную для шабрения поверхность детали. После нескольких кругообразных движений плиты или возвратно-поступательных движений линейки по детали либо детали на плите деталь осторожно снимают с плиты. Появившиеся окрашенные пятна на детали свидетельствуют о неровностях, выступающих на ее поверхности. Неровности удаляются шабрением.
Шабрение начинают с самых выступающих мест, обозначенных светлым цветом краски. Затем следуют пятна с густой окраской. Светлые пятна не шабрятся.
Степень точности и шероховатости поверхности определяется по числу пятен краски в квадрате со стороной 25 мм (около 16 – хорошее шабрение, 25 – очень точное шабрение). Преимуществом этого вида обработки является возможность получения простыми инструментами высокой точности (до 2 мкм). К преимуществам также следует отнести возможность получения точных и гладких фигурных поверхностей, обработки закрытых поверхностей. Хорошо шабрятся чугунные и стальные поверхности небольшой твердости.
Недостатками шабрения являются слишком медленный процесс обработки и значительная трудоемкость, что требует от слесаря большой точности, терпения и времени.
4.10. Шлифование
Шлифованием называется обработка деталей и инструментов с использованием вращающихся абразивных или алмазных шлифовальных кругов, основанная на срезании зернами круга с поверхности очень тонкого слоя материала в виде мельчайших стружек. Цель шлифования – получение поверхностей деталей с незначительной шероховатостью и очень точных размеров.
Наиболее простым и распространенным шлифовальным станком является точильный станок (см. рис. 8). Он широко применяется как в небольших мастерских, так и на крупных предприятиях. Точильные станки бывают разных конструкций и мощности: одинарные и двойные, стационарные и настольные.
Шлифовальные станки бывают круглошлифовальные, внутришлифовальные, плоскошлифовальные, бесцентровошлифовальные, заточные и специальные (резьбошлифовальные, зубошлифовальные, шлицешлифовальные и др.).
Для шлифования используют и ручные электрические шлифовальные машинки, реже – пневматические.
В результате неправильного выбора глубины и подачи, небрежности в подводе шлифовального круга к детали (или детали к кругу) может произойти повреждение и даже разрыв шлифовального круга или детали, а также могут появиться прижоги, свидетельствующие о структурных изменениях в поверхности материала. При шлифовании обязательно применение охлаждения.
4.11. Притирка, полирование и отделка поверхности.
Притирка – это снятие тончайших слоев металла посредством мелкозернистых абразивных порошков в среде смазки или алмазных паст, нанесенных на поверхность инструмента (притира). В качестве инструмента используются притиры, изготовленные из серого чугуна перлитной структуры или другого мягкого металла. Они делятся на ручные, машинно-ручные, машинные (механические) и монтажные.
Притиры имеют вид плиток, притирочных плит, валиков, конусов, кругов, а также могут иметь сложную конфигурацию в соответствии с видом поверхности обрабатываемой детали. Они могут быть монолитные и разжимные. Пример некоторых притиров показан на рисунке 26.
Рис. 26. Притиры
Притирка – один из самых точных способов обработки поверхности металлических деталей. В результате такой обработки с поверхности детали удаляются все неровности при одновременном достижении очень высокой степени точности плоскостей (1 мкм). Цель притирки – получение точных посадок соприкасающихся поверхностей деталей машин.
Материалы для притирки делятся на пасты, притирочные порошки и полотно.
Полирование применяется для придания поверхности детали блеска. В результате полирования снижается шероховатость поверхности и достигается зеркальный блеск. Основное назначение полирования – декоративная обработка поверхности, а также уменьшение коэффициента трения, повышение коррозионной стойкости и усталостной прочности.
Полирование производится мягкими кругами (войлочными, фетровыми, матерчатыми), на которые наносится смесь абразивного порошка и смазки или полировочная паста.
Операция полирования может выполняться вручную или машинным способом. Мелкие детали полируются во вращающемся барабане с использованием стальных закаленных шариков диаметром 3–8 мм.
Поверхность некоторых деталей или изделий подвергается отделке.
«Наведение мороза» на поверхность – это один из способов окончательной отделки металлической поверхности, придания ей хорошего внешнего вида путем нанесения на нее мелких рисок по определенному узору. Эти риски выполняются осторожно и аккуратно шабером вручную или механическим способом.
Матирование – придание металлической поверхности матового пепельно-серого цвета. Эта операция выполняется механически на мелких кованых, литых, опилованных или отлитых деталях с использованием стальных или медных проволочных щеток, совершающих вращательное движение. Перед матированием металлическую поверхность увлажняют мыльными растворами.
Оксидирование – получение на поверхности стальной детали или изделия тонкого слоя оксида голубого или темноголубого цвета. Самый распространенный способ оксидирования при слесарных работах основан на покрытии хорошо очищенного от ржавчины предмета тонким слоем льняного масла и нагревании его в горне на раскаленном коксе.
Чернение стальной детали производится в такой последовательности: полирование поверхности, обезжиривание венской известью, промывка, сушка, покрытие травящим раствором. После покрытия травящим раствором деталь сушат при температуре 100 °C в течение нескольких часов, после чего она подвергается действию пара и горячей воды. Затем деталь очищают в мокром виде проволочной щеткой.
Окраска – покрытие поверхности слоем краски или лака с целью предупредить коррозию и придать детали или изделию товарный вид. Окраска выполняется вручную кистью или механически (малярным пистолетом). Краски могут быть водяные, масляные, нитрокраски и синтетические эмали.
4.12. Пайка, лужение, металлизация и склеивание
Пайка – процесс создания неразъемного соединения металлов с помощью присадочного связующего материала, называемого припоем. Припой в процессе пайки доводится до жидкого состояния. Температура плавления припоя значительно ниже, чем соединяемых металлов.
Твердость припоя определяется маркой и химическим составом применяемых для припоя металлов. Температура плавления твердых припоев составляет 600–1450 °C. Они делаются на основе меди, латуни, серебра, никеля и алюминия. Кроме того, различают жаропрочные и нержавеющие припои на основе никеля, марганца, серебра, золота, палладия, кобальта и железа.
Мягкими припоями являются оловянно-свинцовые (с добавлением или без добавления сурьмы). Температура плавления этих припоев 183–305 °C.
Мягкие припои применяются для неразъемного соединения и уплотнения металлов при незначительных требованиях к прочности и выносливости соединения на растяжение и удары; твердые припои – для неразъемных и герметичных соединений большой прочности и выносливости на растяжение и удары.
Припои выпускают в виде листа, ленты, прутков, проволоки, сеток, блоков, фольги, зерен, порошков и паяльной пасты. К химическим очищающим и травящим средствам относятся соляная кислота, хлорид цинка, бура, борная кислота, нашатырь. Поверхность можно очистить механическими средствами, абразивным материалом или напильником либо металлическими щетками. Во время пайки поверхность предохраняется от окисления такими средствами, как стеарин, скипидар и канифоль.
Неразъемное соединение металлов пайкой может быть выполнено паяльником, в газовом пламени, пайкой в печах, в ванне, химическим способом, автогенной пайкой и др.
Для пайки припоем необходимы паяльники, припои, а также средства, очищающие, травящие и предупреждающие окисление поверхности во время пайки.
Паяльник – это ручной инструмент различной формы и массы. Часть паяльника, которой непосредственно паяют, выполняется из меди. Медную часть паяльника можно нагревать с помощью электричества (электрический паяльник), над газовым пламенем (газовый паяльник) или в горне.
Для нагрева паяльников и некоторого прогрева соединяемых металлов могут применяться паяльные бензиновые лампы.
Лужением называется покрытие поверхности металлических изделий тонким слоем олова или сплавом на основе олова.
Цинкование производится способом холодного электролитического или горячего покрытия металлических изделий тонким слоем цинка.
Лужение и цинкование применяются при производстве бытовых изделий, в пищевой промышленности, строительстве, как средство для защиты от коррозии, окисления и образования химических соединений, вредных для здоровья и разрушающих металл.
Для лужения и цинкования в зависимости от детали и ее назначения нужно иметь чистое олово, цинк или их сплавы, паяльную лампу либо газовую горелку, очищающие средства, необходимые для обезжиривания и очистки поверхностей, подвергающихся лужению или цинкованию, ванны для плавки олова или цинка, обтирочный материал и клещи.
Металлизация напылением – это нанесение металлического покрытия на поверхность изделия путем разбрызгивания
под давлением расплавленного металла. Эта операция выполняется специальными пистолетами. Металлизация применяется для предохранения изделий от коррозии, для ремонта изношенных деталей машин, исправления дефектных отливок, а также для исправления дефектов, возникающих в результате обработки резанием.
Склеивание – неразъемное соединение деталей изделий путем обмазки соединяемых поверхностей изделия веществом (или смесью веществ), называемым клеем, их соединения и выдерживания под некоторой нагрузкой до затвердения клея. В ряде случаев применяется подогрев склеенных деталей.
Склеиваемые поверхности следует тщательно очистить механическим способом, затем обезжирить бензолом или толуолом. После обезжиривания изделие высушивают, не касаясь пальцами поверхностей, предназначенных для склеивания.
4.13. Сборка деталей
Соединение деталей в сборочные единицы (механизмы, узлы, машины и т. д.) называется сборкой. Сборка предусматривает не только соединение деталей, но и подгонку их перед сборкой, регулировку всей сборочной единицы.
Технологический процесс сборки состоит из последовательно выполняемых операций. При этом деталь, с которой начинают сборку, присоединяя к ней последовательно остальные детали, называют базовой.
Слесарно-сборочные работы выполняются с помощью различных монтажных инструментов (гаечных ключей, отверток, молотков) и приспособлений.
Правильность сборки механизмов обычно проверяется взаимодействием их деталей. Для этого приводят в движение вручную ведущую деталь и следят за тем, как это движение воспринимается всеми ведомыми деталями.
5. Требования безопасности труда при выполнении слесарных работ
5.1. Требования безопасности труда
Задача техники безопасности – предупреждение несчастных случаев, создание таких условий, которые обеспечивали бы полную безопасность труда работающего и его производительность.
Несчастные случаи чаще всего происходят в результате невнимательного отношения к выполнению инструкций по технике безопасности и правил внутреннего распорядка, а также в результате недостаточного усвоения необходимых производственных навыков и отсутствия опыта в обращении с инструментами и оборудованием.
На каждом предприятии существуют отраслевые инструкции по охране труда при выполнении слесарных работ. В данном учебном пособии приводятся обобщенные требования техники безопасности для слесаря-ремонтника.
Слесарные работы выполняют главным образом на слесарных верстаках, которые должны отвечать следующим требованиям:
- верстак должен иметь жесткую, прочную конструкцию и быть устойчивым;
- рабочая поверхность должна быть строго горизонтальной и покрыта листовой сталью;
- верстак должен быть оснащен выдвижными ящиками, разделенными на ячейки и располагаемыми под рабочей поверхностью, и полками для хранения инструментов, заготовок, мелких деталей и технической документации;
- на верстаке должен быть установлен защитный экран из органического стекла или металлической сетки с размером ячеек не более 3 мм, обеспечивающий защиту работающего от отлетающих частиц металла при выполнении таких операций, как, например, рубка зубилом. При использовании двухместных верстаков такие экраны необходимо устанавливать и посередине верстака;
- верстаки должны быть оборудованы светильниками местного освещения напряжением не более 220 В, которые можно регулировать по высоте и изменять угол наклона относительно зоны обработки;
- светильники должны быть защищены сетчатым ограждением и отражателями, направляющими световой поток в зону обработки;
- слесарные тиски, устанавливаемые на верстаке, должны обеспечивать надежное закрепление обрабатываемой заготовки. Для этого они снабжаются стальными сменными губками, которые должны иметь несработанную перекрестную насечку на рабочей поверхности с шагом 2–3 мм и глубиной 0,5–1,0 мм. Зазор между сомкнутыми губками слесарных тисков не должен превышать 0,1 мм. Подвижные части тисков должны перемещаться без заедания, рывков и надежно фиксировать закрепляемую заготовку;
- тиски, установленные на слесарном верстаке, должны иметь устройство, предупреждающее полное вывинчивание ходового винта из гайки.
При выполнении слесарных, сборочных и ремонтных работ применяют ручной и ручной механизированный (электрический и пневматический) инструмент, а также стационарное технологическое оборудование.
Ручной слесарный инструмент повседневного применения (молотки, чертилки, кернеры, зубила, крейцмейсели, напильники, шаберы, ножовки, ножницы, гаечные ключи и т. д.) должен быть закреплен за рабочим, который несет персональную ответственность за его техническое состояние.
Ручной слесарный инструмент для обеспечения его безопасного применения при выполнении работ должен отвечать следующим требованиям:
- молотки и кувалды должны иметь гладкую поверхность бойков (на поверхности бойков не допускаются трещины, сколы, выбоины, заусенцы);
- рукоятки молотков и кувалд должны быть изготовлены из хорошо просушенной древесины твердых лиственных пород (березы, дуба, клена, ясеня, граба) и не иметь сучков;
- рукоятки должны иметь по всей длине овальную форму в поперечном сечении, быть гладкими, без трещин;
- рукоятка молотка для предупреждения выскальзывания из рук работающего в процессе нанесения удара должна иметь коническую форму с утолщением к свободному концу;
- рукоятка кувалды к свободному концу должна несколько сужаться, так как ее насадка производится без клиньев от свободного (узкого) конца к широкому;
- ось рукоятки должна быть строго перпендикулярна продольной оси инструмента;
- клинья для крепления бойка на рукоятке молотка должны быть изготовлены из мягких сталей и снабжены насечкой, обеспечивающей удержание клина в материале рукоятки;
- напильники, шаберы и отвертки должны иметь рукоятки, выполненные из дерева или полимерных материалов (использование этих инструментов без рукояток категорически запрещено);
- при установке рукояток на заостренные части инструмента (хвостовики) напильников или шаберов необходимо в обязательном порядке применять металлические бандажные кольца;
- зубила, крейцмейсели, канавочники, бородки не должны иметь трещин, сбитых и скошенных торцов, а их рабочая часть не должна иметь видимых повреждений. Длина этих инструментов должна быть не менее 150 мм. Работу зубилом, крейцмейселем и канавочником необходимо выполнять с использованием защитных очков;
- рукоятки ручных ножниц для разрезания металла должны быть гладкими, без вмятин, зазубрин и заусенцев, а с их внутренней стороны должен быть предусмотрен упор, предотвращающий сдавливание пальцев руки;
- ручные рычажные ножницы должны быть надежно закреплены на верстаке и снабжены прижимами на верхнем подвижном ноже для обеспечения прижатия разрезаемого листа к поверхности стола (нижнего неподвижного ножа) и противовесом, обеспечивающим удержание верхнего ножа в безопасном положении;
- губки гаечных ключей должны быть строго параллельны, а их размер должен соответствовать размерам гаек и головок винтов или болтов (допускается увеличение размера зева ключа относительно размера гаек или головок винтов и болтов не более чем на 5 %).
Электроинструмент, применяемый при выполнении слесарных, сборочных и ремонтных работ, должен отвечать следующим требованиям:
- ручной электроинструмент должен подключаться к сети напряжением не более 42 В (в тех случаях, когда подключение инструмента к сети невозможно, допускается его подключение к сети напряжением до 220 В. При этом необходимо предусмотреть защитное отключение или наружное заземление корпуса);
- при работе электроинструментом, подключенным к сети напряжением 220 В, обязательно использование средств электрозащиты: резиновые коврики, диэлектрические перчатки и т. п.);
- кабели и провода для обеспечения их целостности (защита от излома и истирания) должны подводиться к электроинструменту через эластичную трубку длиной не менее пяти диаметров кабеля, которая устанавливается в корпус электроинструмента;
- рабочие органы электроинструментов, за исключением электрических дрелей (сверлильных машин), должны иметь защитные кожухи;
- в случае обнаружения неисправностей электроинструмента работа с ним должна быть немедленно прекращена;
- разборка и ремонт электроинструмента, штепсельных разъемов и проводов разрешается только персоналу, осуществляющему обслуживание электроинструмента (самостоятельный ремонт категорически запрещен).
Ручной пневматический инструмент, применяемый при выполнении слесарных работ, должен отвечать следующим требованиям:
- рабочая часть инструмента не должна иметь повреждений (трещин, выбоин, заусенцев) и должна быть правильно заточена;
- боковые грани инструмента не должны иметь острых ребер;
- хвостовая часть инструмента, устанавливаемого в присоединительное устройство, должна плотно прилегать к стенкам устройства и обеспечивать надежное центрирование инструмента;
- на хвостовой части инструмента не должно быть повреждений;
- сверлильные машинки, виброзубила, гайковерты и другие пневматические инструменты должны быть снабжены виброгасящими устройствами;
- инструмент должен быть оборудован глушителями выхлопов воздуха и не должен допускать попадания отработанного сжатого воздуха на работника, загрязняя зону его дыхания;
- ударные инструменты должны быть оборудованы устройствами, не допускающими вылета рабочего инструмента.
При работе с пневматическим инструментом следует соблюдать следующие меры безопасности:
- перед присоединением воздушного шланга к инструменту его необходимо продуть, направляя струю воздуха в зону, в которой не наблюдается присутствие людей;
- шланг к инструменту следует присоединять при помощи штуцера, ниппеля или стяжных хомутов;
- крепление шланга к инструменту или к соединительной трубке проволокой категорически запрещено;
- шланг пневматического инструмента к централизованной сети разводки сжатого воздуха присоединяют, используя вентиль, обеспечивающий перекрытие подачи сжатого воздуха (подсоединение шланга непосредственно к магистрали централизованной подачи сжатого воздуха категорически запрещено);
- отсоединяя шланг от пневматического инструмента, необходимо сначала перекрыть вентиль, соединяющий шланг с централизованной магистралью подачи сжатого воздуха;
- следует проверить работу пневматического инструмента на холостом ходу до установки рабочего инструмента, включив его на непродолжительное время;
- начинать работу пневматическим инструментом можно только после того, как рабочий инструмент (сверло, зубило) плотно прижат к обрабатываемой поверхности;
- ремонт пневматического инструмента на рабочем месте не допускается;
- при выполнении работ с применением пневматического инструмента не допускается натягивание и перегибание воздухоподводящих шлангов.
При выполнении сборочных и ремонтных работ достаточно часто приходится производить пайку соединяемых деталей. В таких случаях используется низкотемпературная (мягкими припоями) и высокотемпературная (твердыми припоями) пайка.
Пайка твердыми припоями, при которой основным источником теплоты является паяльная лампа, требует выполнения определенных правил, обеспечивающих безопасность работ:
- работники, осуществляющие пайку твердыми припоями, должны пройти специальный курс обучения, сдать квалификационный экзамен и получить соответствующее удостоверение;
- паяльные лампы необходимо не реже 2 раз в год подвергать контрольным гидравлическим испытаниям при двойном рабочем давлении, которые оформляют специальным актом;
- при пайке твердыми припоями запрещается применять бензиновые паяльные лампы;
- при работе с керосиновыми паяльными лампами категорически запрещается:
- разжигать лампы подачей горючего через горелку;
- приближаться с горящей паяльной лампой к легковоспламеняющимся объектам;
- заправлять паяльную лампу горючим веществом в процессе ее работы;
- выполнять разборку паяльной лампы вблизи открытого огня;
- заправлять керосиновую паяльную лампу бензином;
- выпускать воздух из резервуара паяльной лампы допускается только после того, как лампа будет погашена, а горелка полностью остынет до температуры окружающей среды;
- паяльные лампы могут быть использованы в технологическом процессе только в том случае, если расстояние от образованного лампой пламени составляет не менее 1,5 м до токоведущих частей напряжением до 10 кВ, при напряжении токоведущих частей более 10 кВ это расстояние должно составлять не менее 3 м;
- категорически запрещается разжигать паяльные лампы непосредственно под оборудованием, проводами и кабелями или вблизи маслонаполненных аппаратов.
5.2. Правила производственной санитарии
Производственная санитария предусматривает создание условий, обеспечивающих необходимую температуру в производственных помещениях, хорошую вентиляцию, достаточную освещенность рабочих мест, отсутствие сквозняков, наличие вспомогательных и бытовых помещений.
Температура производственных помещений должна поддерживаться в пределах 16–20 °С.
Вентиляция производственных помещений должна обеспечивать создание комфортных условий труда за счет поддержания необходимого температурного режима, удаления вредных газов, паров и пыли. Вентиляция может быть приточной и вытяжной.
Одним из показателей требуемого санитарного состояния помещения является его освещенность. Оптимальная освещенность на рабочем месте должна обеспечивать снижение нагрузки на глаза, облегчая работу и уменьшая возможность травматизма. Освещение может быть как естественным (дневное освещение), так и искусственным (электрическое освещение). Предпочтительным является естественное освещение.
Во время работы необходимо соблюдать общие правила гигиены:
- работник, приступающий к работе, должен быть здоров, опрятно одет; волосы необходимо заправить под головной убор (берет, косынку);
- по окончании работы следует привести в порядок рабочее место, спецодежду убрать в специальный шкаф;
- каждый рабочий участок или мастерская должны быть оснащены аптечкой.
Помимо общих правил гигиены большое значение имеет личная гигиена работника. Под личной гигиеной понимаются меры, направленные на сохранение здоровья, предупреждение и устранение условий, которые могут привести к нарушению здоровья.
Для сохранения здоровья и предупреждения заболеваний необходимо:
- отводить на сон не менее 8 ч в сутки;
- в процессе работы время от времени менять рабочую позу;
- после окончания рабочего дня мыть в душе с мылом все тело.