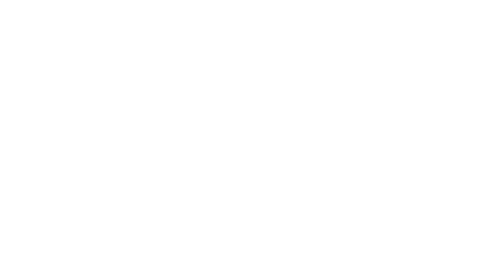
Классификация режимов работы турбин. Изменение энергетических характеристик ступеней и отсеков турбин и надежности их работы в нестационарных и переходных режимах.
Стационарный
режим отвечает
работе турбины при некоторой фиксированной
нагрузке. В этом режиме параметры пара
в проточной части и температурное
состояние ее деталей не изменяются во
времени. Под номинальной
мощностью турбин, не
имеющих регулируемых отборов понимают
мощность, которую должен длительное
время развивать турбоагрегат при
номинальных значениях всех основных
параметров: начальных Р0,
t0
, температуре
промперегрева, температуре питательной
воды.
Для теплофикационных
турбин с регулируемыми отборами пара
давление в отборах и т.д.
Под
частичной нагрузкой понимают режим
работы, при котором мощность или значение
регулируемых отборов пара меньше
номинальных. Работу при частичных
нагрузках называют переменным
режимом. К переменному
режиму относят работу турбины при
отношениях параметров свежего пара,
пара промперегрева или отработавшего
пара, отклонениях в тепловой схеме.
Под
максимальной мощностью
конденсационной турбины понимают
мощность которую может длительно
развивать турбина при номинальных
значениях всех основных показателей,
но при отсутствии отборов пара для
внешних потребителей теплоты.
Теплофикационные турбины развивают
максимальную мощность при уменьшении
регулируемых отборов.
Нестационарные
режимы, режимы при
которых изменяется тепловое состояние
турбоагрегата. Наиболее сложным является
пуск ПТУ- операции перед толчком ротора
паром, разворот ротора, включение
генератора в сеть и набор нагрузки. К
нестационарным относят также режим
остановки турбины (разгружение, отключение
от сети, выбег ротора, остывание).
К
аварийным режимам
относят режимы из-за неполадок дефектов
в различном оборудовании или самой
турбине. Наиболее напряженными деталями
турбины являются рабочие лопасти
регулирующей и последних ступеней, а
также упорный подшипник, надежность
которого определяется осевыми усилиями,
приложенными к ротору, диафрагмы,
валоповорот, паропроводы.
При переменном
пропуске пара через турбину изменение
давления и температуры перегретого
пара в ее проточной части подчиняется
формуле Флюгеля-Стодолы:
где
P00,
T00—
давление и температура перед любой
ступенью;
Рz0—
давление за турбиной
при номинальном пропуске пара Go;
P01,
Т01,
Рz1
–параметры для
нового расхода пара G,
т.к. в проточной части T00
= T01,для
конденсационной турбины Рz
<< Р0,
то
,
т.е. в проточной части конденсационной
турбины давление пара в ступенях
пропорциональны расходу пара. При
изменениях пропуска пара через турбину
изменяются параметры пара перед и за
ступенью, что приводит к изменению
теплоперепада ступени, это влечет за
собой изменение треугольников скоростей,
отклонение отношения скоростей Хф
от оптимального и
снижение КПД ступени. Увеличение степени
реакции при том же давлении за ступенью
приводит к увеличению осевого давления
на диск соответствующей ступени. При
изменении расхода пара через группу
ступеней изменяются их теплоперепады,
однако в основном это относится к
последней ступени. При изменении расхода
пара через группу ступеней осевое
усилие, действующее на рабочие диски и
рабочие лопатки этой группы меняется
пропорционально расходу пара. При
увеличении расхода пара через турбину
рабочие лопатки последней ступени
перегружаются и за счет увеличения
теплоперепада. Увеличение расхода пара
приводят к пропорциональному росту
осевого усилия и увеличению нагрузки
на колодки упорного подшипника. Поэтому
увеличение мощности сверх номинальной
может производиться эксплуатационным
персоналом строго в рамках допустимых
пределов.
№ 23
Соседние файлы в предмете [НЕСОРТИРОВАННОЕ]
- #
- #
- #
- #
- #
- #
- #
- #
- #
- #
- #
АЛМАТИНСКИЙ ИНСТИТУТ ЭНЕРГЕТИКИ И СВЯЗИ
Кафедра тепловых энергетических установок
ЭКСПЛУАТАЦИЯ ОСНОВНОГО ОБОРУДОВАНИЯ ТЭС
Конспект лекций
для студентов всех форм обучения
специальности 050717 – Теплоэнергетика
СОСТАВИТЕЛИ: А.А.Кибарин, Т.В.Ходанова. Эксплуатация
основного оборудования ТЭС. Конспект лекций для студентов всех форм обучения
специальности 050717 – Теплоэнергетика. – Алматы: АИЭС, 2008. -79 с.
В конспекте лекций представлены сведения об основах
эксплуатации энергетических котлов и паровых турбин, о режимах их работы,
приведены пусковые операции и пусковые схемы котельных и турбинных установок.
Представлены сведения о основных процессах происходящих на внешней стороне
поверхностей нагрева паровых котлов. Рассмотрены основные повреждения и аварии
паровых котлов. Представлены сведения по системам маслоснабжения, регулирования
современных паровых турбин. Вопросы эксплуатации и расчета конденсационных
установок. Конспект лекций предназначен для
студентов, обучающихся по специальности 050717
— Теплоэнергетика, всех форм обучения,
выбравших специализацию – Тепловые электрические станции.
Алматы 2008
Предисловие
Подготовка будущих бакалавров теплоэнергетиков невозможна
без изучения и понимания процессов, протекающих в основном оборудовании ТЭС в
период эксплуатации при различных режимах его работы. В этой связи в программу
подготовки студентов, обучающихся по специальности 050717 – Теплоэнергетика,
выбравших направление подготовки «Тепловые электрические станции» введен курс
«Эксплуатация основного оборудования ТЭС».
Возрастающая
неравномерность электропотребления значительно усложняет условия эксплуатации
котлов и турбинных установок. Котельные агрегаты и турбинные установки в
течение года подвергаются многократным плановым и аварийным пускам и остановам.
При этом в толстостенных элементах конструкций возникают значительные
термические напряжения. Если процесс пуска или останова проходит с отклонениями
от норм, то нарушаются допустимые условия эксплуатации, что, либо приводит к
аварии, либо уменьшает срок службы оборудования.
Эти процессы, а также
основы рационального ведения стационарных режимов работы основного оборудования
ТЭС, должны быть четко усвоены будущими специалистами — теплоэнергетиками.
Цель курса – приобретение студентами знаний и
навыков, необходимых для свободной ориентации в практике эксплуатации основного
оборудования ТЭС.
Задача курса
– знакомство студентов теплоэнергетиков с режимами работы котельных агрегатов,
теоретическими основами процессов, протекающих в паровых котлах при пусках и
остановах, основами их рациональной эксплуатации, знакомство с основами теории
эксплуатации паровых и газовых турбин и их вспомогательного оборудования.
В результате изучения дисциплины студенты должны:
иметь представление:
— об условиях работы
основных элементов паровых котлов, паровых и газовых турбин в процессе
эксплуатации;
— о структуре управления работой основного
оборудования ТЭС;
знать:
-режимы работы котельных агрегатов, паровых и газовых
турбин;
-порядок пуска и останова котельных установок и
процессы, влияющие на рациональное ведение пуско-остановочных режимов;
-основы организации и управления процессом
эксплуатации;
— основы теории теплообмена в турбомашинах при
переходных режимах их работы;
— пусковые схемы турбомашин;
— технологию пусков, остановов и обслуживания
турбомашин и их вспомогательного оборудования.
уметь:
-анализировать техническое состояние основного
оборудования ТЭС, оценивать экономичность и надежность работы основного
оборудования ТЭС.
1 Лекция 1. Введение.
Эксплуатационные режимы работы котлов
Содержание лекции: цель, объем и содержание дисциплины. Предмет дисциплины. Основные
задачи. Режимы работы котлов. Режимная карта. Эксплуатационные показатели
работы котлов. Стационарные режимы эксплуатации котлов. Нестационарные режимы работы
в диапазоне допустимых нагрузок. [1, 2, 7, 8].
Цель лекции: знакомство
с кругом изучаемых вопросов, литературой, рекомендуемой для изучения курса, эксплуатационными
режимами работы котлов.
1.1 Предмет и содержание курса
Для специализации «Тепловые электрические станции»
предметом курса является стационарная и станционная теплоэнергетика.
Содержание курса включает эксплуатационные показатели
работы котлов и турбин, основы эксплуатации паровых котлов и паротурбинных
установок, вопросы теплообмена при переходных режимах работы котлов и турбин,
вопросы безопасной эксплуатации и регулирования котлов и турбин.
1.2 Режимы работы котельных агрегатов
Работа на ТЭС связана
с выполнением графика электрической нагрузки, который изменяется крайне
неравномерно. Различают суточный, недельный и сезонный графики нагрузки.
Базовым считается режим в основном на нагрузке, близкой к номинальной, хотя
допускается изменение нагрузок и даже останов котельных агрегатов на нерабочие
дни. Полупиковым считается режим, при котором котел останавливается в резерв в
ночное время в будние дни и на все выходные дни. Пиковым считается режим, когда
котельный агрегат работает только для покрытия максимальных нагрузок.
Так как график
электрической нагрузки крайне неравномерен, котельный агрегат должен работать в
широком диапазоне нагрузок, иметь высокие маневренные свойства. В понятие маневренности
котельных агрегатов входят: показатели, определяющие диапазон рабочих
нагрузок котлов; пуско-остановочные характеристики оборудования; его
динамические свойства; характеристики внезапных сбросов (набросов) нагрузки.
Условия
эксплуатации оборудования при различных его нагрузках характеризуются
регулировочным диапазоном и диапазоном допустимых нагрузок.
Режим
работы на любой из нагрузок с незначительными отклонениями параметров пара
называют стационарным. Режимы, характеризующиеся изменениями нагрузки, а
также отклонениями параметров пара в результате внутренних или внешних
возмущений, называют нестационарными.
Внутренними
называют возмущения режима вследствие изменения одного или нескольких входных
параметров котла (расход или температура питательной воды, расход топлива или
воздуха и т. п.). Соответственно внешними называют возмущения, связанные с
изменением выходных условий (таких, как давление пара в общестанционном
коллекторе, нагрузка турбогенератора, степень открытия пускосбросных устройств
и т. п.). Важным показателем является способность котла к быстрому изменению
нагрузки, которую часто называют приемистостью. В основном она
определяется динамическими свойствами котла, т. е. его реакцией на возмущения
режима.
Задачей оперативного
персонала является поддержание наиболее благоприятного режима работы котла при
данных условиях, в соответствии с режимной картой, при составлении которой
используются рекомендации завода-изготовителя, данные наладки котла,
руководящие циркуляры вышестоящих организаций и накопленный опыт эксплуатации.
1.3 Режимные карты
Режимные карты представляют собой
документ, выполненный чаще всего в виде таблицы с указанием параметров, которые
должны выдерживаться для надежной и экономичной работы котла. Режимные карты
составляют по результатам испытаний при оптимальных, наиболее экономичных и
надежных режимах, определенных нагрузках, качестве топлива и сочетаниях
основного и вспомогательного оборудования.
В режимную карту входят:
—
давление и температура острого и
промежуточного пара, питательной воды;
—
температура уходящих газов;
—
количество и сочетание работающих мельниц, горелочных
устройств, дутьевых вентиляторов и дымососов;
—
состав продуктов сгорания (О2 или СО2);
—
показатели надежности и экономичности работы поверхностей
или элементов котла;
—
расход воздуха на мельницы и их загрузка;
—
температура среды и металла некоторых наиболее опасных
с точки зрения перегрева поверхностей нагрева;
—
другие показатели, например характеризующие
шлакование, загрязнение.
По параметрам, входящим в режимную карту,
настраивают защиты и системы автоматического регулирования. Паровые котлы,
вводимые после монтажа, подлежат первичной наладке, на основе которой составляются
временные режимные указания, действующие до завершения режимно-наладочных
испытаний и появления режимной карты.
1.4 Эксплуатационные показатели работы котлов
Основные показатели работы котельных установок могут
быть разделены на технологические, определяющие функциональные зависимости
рабочих процессов, экономические и режимные.
Основными показателями тепловой экономичности
котельных установок за данный период времени являются КПД, удельный расход
условного топлива на выработку пара, а также удельный расход электроэнергии и
теплоты на собственные нужды котла.
Основными показателями режима
работы котлов являются: годовой коэффициент рабочего времени и коэффициенты,
характеризующие нагрузку котлов. Годовой коэффициент рабочего времени,
краб=tраб/8760
где
tраб — число часов работы котла в году.
Полная продолжительность готовности
агрегата к несению нагрузки, характеризуется коэффициентом готовности
кгот= (tраб+tрез)/8760
где
tрез — продолжительность нахождения агрегата в резерве, ч.
Показателями, характеризующими режимы нагрузки котла,
являются:
а) коэффициент использования тепловой мощности котлов,
%,
ки=SD/(SDном×t)
где
SD — фактическая выработка пара котлами, т/год;
SDном — номинальная
производительность котлов, т/ч;
t — фактическое время работы котлов, ч;
б) число часов использования
установленной производительности котлов,
т. е. число непрерывной работы котлов при полной их производительности, при
которой могла бы быть получена годовая выработка пара, ч,
tном=SD/SDном.
Использование
установленной производительности котлов определяется графиком нагрузки,
резервной производительностью, надежностью установленного оборудования и т.д.
Снижение экономичности работы при увеличении числа часов использования
указывает на работу агрегатов с нагрузкой выше экономичной или ухудшение их
состояния.
1.5 Организация управления котлами
Организацией управления называют структуру связей между объектом управления,
обслуживающим персоналом и устройствами для контроля и управления объектом.
Система управления котла должна обеспечивать его работу с заданными
оптимальными технико-экономическими показателями.
Управление котельными установками применяется индивидуальное,
групповое и централизованное. При групповом и централизованном
управлении дежурный и его помощники обслуживают группу или все котельные
установки данного объекта.
В современных котельных установках система управления
включает следующие технические устройства — подсистемы: информационную; сигнализации;
дистанционного и автоматического управления; автоматического регулирования; технологической
защиты и блокировок.
1.6
Стационарные режимы эксплуатации котлов
При
постоянной нагрузке регулирование экономичности процесса горения заключается в
поддержании оптимального коэффициента избытка воздуха в топке (О2т)
и распределение воздуха по отдельным горелкам в соответствии с распределением
топлива.
В
эксплуатационных условиях важно обеспечить поддержание температур стенок труб в
зоне обогрева не выше допустимых величин, определяемых примененной маркой стали
и параметрами среды.
На
барабанном котле дополнительно должен поддерживаться в допустимых пределах
уровень воды в барабане.
Важным
направлением работы эксплуатационного персонала является организация режима с
минимальной интенсивностью протекания низкотемпературной коррозии хвостовых
поверхностей нагрева и газоходов.
Стационарные
режимы при работе котла на различных нагрузках неодинаковы. Зависимость
значения данного параметра среды или показателя режима работы от нагрузки
называют его статической характеристикой.
1.7 Нестационарные процессы в котлах
Изменение
тепловыделения в топке и нарушение энергетического баланса в переходный период
приводят к изменению тепловосприятия всех поверхностей нагрева котла. При
увеличении тепловыделения в топке повышается паропроизводительность котла.
Температура перегрева пара может увеличиваться или уменьшаться в зависимости от
соотношения конвективных и радиационных поверхностей нагрева пароперегревателя.
При конвективном пароперегревателе увеличение нагрузки на 10 % повышает
температуру пара на 5 – 10 °С.
При неизменной подаче питательной воды уровень воды в
барабане изменяется вследствие вытеснения ее паром
из труб испарительной поверхности нагрева. При повышении тепловосприятия
поверхностей нагрева в первый момент уровень воды в барабане повышается, а
затем начинает снижаться. Зависимость изменения параметров, характеризующих
работу барабанного котла в переходный период при увеличении тепловыделения в
топке, показана на рисунке 1.
В прямоточном котле нет фиксированных конструктивных
границ между экономайзерами, испарительными и пароперегревательными
поверхностями нагрева. При изменении количества подаваемой питательной воды или
тепловыделения в топке границы между отдельными элементами поверхности нагрева
перемещаются. Увеличение тепловой нагрузки на 10% повышает температуру пара на
100 °С. Уменьшение расхода воды на 10% увеличивает температуру пара на 110 °С.
Таким образом, в прямоточном котле небольшое отклонение в переходный период
тепловой нагрузки или расхода воды приводит к значительному изменению
температуры перегрева пара. Характер изменения расхода пара при возмущении по
каналу тепловой нагрузки показан на
рисунке 2.
В переходный период в барабанном и прямоточном котлах
изменяется теплота, аккумулированная в среде, заполняющей трубы, а также в
металле котла.
Количество теплоты и массы вещества котла называется аккумулирующей
емкостью. Аккумулированная емкость среды зависит от ее объема и давления в
котле. В барабанных котлах аккумулированная емкость среды в 3 — 4 раза больше,
чем в прямоточных.
2 Лекция 2. Рабочие диапазоны нагрузки котельных
агрегатов ТЭС
Содержание лекции: рабочие диапазоны нагрузки котельных агрегатов ТЭС. Устойчивость
гидравлического режима барабанных котлов. Гидравлический режим прямоточных
котлов. Влияние пароперегревателя на глубину разгрузки котлов. Устойчивость
топочного процесса. Шлакоудаление. Коррозия хвостовых поверхностей котельных
агрегатов. Максимальная нагрузка барабанных и прямоточных котлов [5, 9, 12, 14].
Цель лекции: знакомство
с факторами, влияющими на диапазон возможных нагрузок котельных агрегатов в
зависимости от конструкции котла и вида сжигаемого топлива.
2.1 Рабочие диапазоны нагрузки котельных агрегатов ТЭС
Возрастающая с каждым годом
неравномерность энергопотребления значительно усложняет условия эксплуатации
паровых котлов и требует
расширения пределов
изменения нагрузки. Пределы изменения длительно допустимой максимальной и
минимальной нагрузки котельного агрегата являются важнейшей маневренной
характеристикой ТЭС и обычно оцениваются по коэффициенту регулирования, который
для парового котла равен
Крег=(Dmax-Dmin)/Dmax=1-(Dmin/Dmax)
или по коэффициенту глубины (уровня) разгрузки
Ку=(Dmin/Dmax)×100,
где
D —
паропроизводительность
котла, т/ч.
Чем ближе Крег к единице, тем больше
возможности котла для покрытия неравномерностей графика нагрузки, и, наоборот,
чем меньше этот коэффициент, тем меньшее участие могут принимать агрегаты
станции в регулировании графика нагрузки.
Факторов, ограничивающих минимальную нагрузку парового
котла, достаточно много, основными являются надежность гидравлического режима,
устойчивость топочного процесса, поддержание нормальных параметров пара,
надежность шлакоудаления.
Максимальная нагрузка парового котла, как правило, не
должна превышать его номинальной производительности.
2.2 Устойчивость гидравлического режима барабанных
котлов
Нарушения гидродинамики в барабанных и прямоточных
котлах носят различный характер и, поэтому должны быть рассмотрены раздельно.
Барабанные котлы для блочных установок и для
электростанций с поперечными паровыми связями выполняются для номинальных
давлений
10 и 14 МПа с производительностью от 160 до 640 т/ч с топками для всех
видов энергетического топлива — бурых и каменных углей, мазута, газа, торфа и
сланцев.
Нарушения естественной циркуляции в циркуляционном
контуре барабанного котла (рисунок 3) проявляются в виде замедления, полного
прекращения (застоя) или даже изменения направления (опрокидывания) движения
рабочей среды в трубах контура. Во всех этих случаях ухудшается охлаждение
металла труб, что вызывает опасное повышение его температуры.
Особенно опасен застой циркуляции, при котором в
парогенерирующих подъемных трубах происходит расслоение воды и пара, образуются
паровые пробки и резко ухудшается теплоотдача металла, что приводит к
аварийному повышению температуры труб и часто завершается их пережогом.
Основной причиной таких нарушений гидравлического
режима в контуре циркуляции барабанных котлов является понижение их нагрузки до
некоторого критического значения. Всякое понижение производительности
барабанного котла связано с уменьшением форсировки топочного режима, при этом
снижается обогрев подъемных труб циркуляционного контура и повышается точка
закипания, что приводит к падению полезного напора циркуляции и ее ослаблению.
При достижении критической минимальной нагрузки
перемещение рабочей среды по контуру прекращается, кратность циркуляции
становится равной нулю и возникает застой циркуляции. Как показывает практика
эксплуатации, уже опасными являются режимы, при которых паросодержание в
подъемных трубах превышает 30-50 %, что соответствует кратностям циркуляции 3 —
2 при нормальной кратности 5 — 8 для котлов 14 МПа. Рекомендуется не уменьшать
кратность циркуляции ниже 4. Как показали опыты для большинства барабанных
котлов минимальная нагрузка по условию надежности циркуляции составляет
D
= 0,3-0,45 Dном.
2.3 Гидравлический режим прямоточных котлов
Основными элементами прямоточного котла являются
трубные панели, состоящие из многочисленных труб, присоединенных параллельно
друг другу к входному и выходному коллекторам. Одним из главных условий
надежности работы прямоточного котла является равномерность распределения
рабочей среды между отдельными трубами панелей. Гидравлика системы панелей
надежна тогда, когда расход воды (рабочей среды)
Di
в каждой параллельно включенной трубе равен среднему
расходу Dcp.
Однако при понижении нагрузки котла и уменьшении
расхода рабочей среды в трубах усиливается влияние неодинаковости
гидравлических сопротивлений и, кроме того, возникает так называемый
коллекторный эффект (изменение статического напора вдоль коллектора), поэтому
гидравлическая неравномерность усиливается.
Вследствие неодинакового обогрева отдельных труб из-за
тепловой разверки плотность рабочей среды в них становится также неодинаковой,
и это сказывается на значении так называемого нивелирного напора (составляющей
напора, определяемой массой столба воды в трубе), который уменьшается там, где
обогрев больше среднего, и увеличивается там, где обогрев меньше. В результате
разность статических напоров на концах труб, определяющая расход рабочей среды
в них, становится еще больше, вследствие чего гидравлическая неравномерность в
панели усиливается. При некоторых критических значениях нагрузки котла
неравномерность обогрева различных труб панели может оказаться настолько значительной,
что в наименее обогреваемых трубах нивелирный напор окажется больше разности
давлений в коллекторе. В этом случае рабочая среда в наименее обогреваемых
трубах начнет двигаться в обратную сторону, т. е. сверху вниз, и произойдет
опрокидывание циркуляции рабочей среды. С некоторым запасом минимальная
нагрузка прямоточных котлов по условиям гидравлики принимается равной 0,40 — 0,5
Dном в
зависимости от конструкции котла и вида сжигаемого топлива.
2.4 Влияние пароперегревателя на глубину разгрузки
котлов
Пароперегреватель является наиболее теплонапряженным
элементом парового котла. Общее тепловосприятие пароперегревательных
поверхностей возрастает с повышением номинальных параметров пара с 30 % у
котлов
14 МПа до 70 % у прямоточных котлов сверхкритического давления. В котлах с
рабочим давлением 10 МПа все пароперегревательные поверхности являются
конвективными, и он установлен в поворотной камере топки, в то время как у
котлов 14 МПа значительная часть пароперегревателя выполнена в виде
радиационных поверхностей, расположенных в верхней части топочной камеры. Еще
больше развиты радиационные поверхности в пароперегревателях котлов
сверхкритического давления.
При снижении нагрузки котлов уменьшается расход пара через
пароперегреватель, а следовательно, массовая и линейная скорость пара. В
результате этого температура перегрева пара на выходе из радиационного
пароперегревателя повышается, так как лучистая энергия факела поглощается здесь
меньшим количеством пара. В ширмовых пароперегревателях, включенных между
радиационными и конвективными поверхностями, продолжается интенсивный
теплообмен, лучистый, и конвективный, так что суммарное тепловосприятие ширм
мало зависит от нагрузки. Поэтому дополнительный перегрев пара, возникший в
радиационных панелях, сохранится и на выходе из ширм, причем температура его
может значительно превышать расчетную температуру пара. Одновременно из-за
снижения линейной скорости парового потока резко ухудшается теплоотдача
металла. Совокупное действие обеих этих причин приводит при пониженной нагрузке
котла к значительному возрастанию температуры металла труб пароперегревателя.
При тепловых нагрузках 300 кВт/м2, обычных
в зоне радиационных панелей, и при условии применения для труб
пароперегревателя стали 12Х1МФ с предельной допустимой рабочей температурой 575
°С, скорость пара должна быть не меньше 5 м/с. Эта скорость соответствует
расходу пара примерно 0,5 Dном (рисунок
4) и, таким образом, минимальная нагрузка барабанного котла 14 МПа с
комбинированным пароперегревателем по условиям надежности металла труб пароперегревателя составляет около 50 %
паропроизводительности.
2.5 Устойчивость топочного процесса
Уменьшение нагрузки котла ведет к снижению
устойчивости горения топлива в топочной камере, и при некотором критическом
значении Dmin возникает пульсация факела, завершающаяся его срывом и погасанием. Это
критическое значение и определяет минимальную нагрузку котла по условиям
устойчивости факела.
Существуют две причины неустойчивости факела:
неустойчивость подачи топлива при малых нагрузках и общее понижение температуры
в топке.
При уменьшении нагрузки котла сначала уменьшают подачу
топлива и воздуха через все включенные горелки (качественное регулирование).
Это снижает турбулентность потока топливовоздушной смеси, замедляет распространение
пламени и ослабляет интенсивность горения, что и приводит к общему понижению
температуры в топке. Все это ведет к снижению стабильности факела, к
возникновению пульсации и погасанию его при дальнейшем понижении нагрузки.
Этот процесс при малых расходах топлива ускоряется
возникновением пульсаций подачи топлива через горелки. В топках с жидким
шлакоудалением режим понижения расхода топлива приводит к понижению
температуры ядра факела и в нижней части топки, что приводит к прекращению
выхода жидкого шлака. Поэтому разгружение котла начиная с уровня (0,80 — 0,75)
Dном производится
количественным регулированием, т. е. отключением части горелок, что дает
возможность повысить тепловую мощность оставшихся в работе горелок и поддержать
необходимую для жидкого шлакоудаления температуру в нижней части топки. Все же
и при этом способе регулирования удается снизить нагрузку лишь до (0,60 — 0,65)
Dном.
Технические минимумы нагрузки котлов по условиям
устойчивости процесса горения неодинаковы для различных типов котлов и
составляют от 0,5 до 0,75 Dном, так
как температура и длительность воспламенения, зависящие от влажности топлива и
выхода летучих и характеризующие реакционную способность топлива, различны для
разных топлив.
У мазутных котлов устойчивость факела практически не
лимитирует минимальной нагрузки ввиду высокой реакционной способности мазута,
однако необходимо следить за распыливанием мазута при низких нагрузках, так как
понижение его расхода сопровождается понижением давления и ухудшением распыливания.
При сжигании газа устойчивость факела также не лимитирует минимальной нагрузки.
Расширение диапазона регулирования котлов, работающих
на АШ и тощих углях с малым выходом летучих, достигается с помощью утепления
топки в зоне расположения горелок.
2.6 Коррозия хвостовых поверхностей котельных
агрегатов
При наличии в органическом составе топлива серы
неизбежно присутствие в уходящих газах паров серной кислоты, которые образуется
при взаимодействии паров чистой воды, свободного кислорода и оксидов серы -сернистого
(SO2) и
серного (SO3)
ангидрида по схеме
S + O2
® SO2 2SO2 + O2
® SO3 SO3 + H2O
® H2SO4
Температура конденсации паров серной кислоты (точка
росы) зависит от их парциального давления в смеси сухих топочных газов и
водяных паров. Это давление возрастает при уменьшении нагрузки котла, и с ним
возрастает температура конденсации. Такой же, но более пологий характер имеет
зависимость температуры уходящих газов от нагрузки котла. Конденсация паров
серной кислоты происходит при соприкосновении их с металлом
воздухоподогревателей в тех случаях, когда температура его оказывается ниже
точки росы, а это имеет место при нагрузках котла, меньших (0,4 — 0,5)
Dном.
Существуют также экономические границы нижнего предела
нагрузки паровых котлов, определяемые резким возрастанием потерь и падением КПД
при работе на пониженных нагрузках. Эти ограничения у большинства типов паровых
котлов соответствуют приблизительно половинной нагрузке.
Например, при изменении нагрузки прямоточного котла
ПК-39-2 (25 МПа, 950 т/ч), работающего на экибастузском угле, от номинальной до
0,5 Dном -температура
уходящих газов повышается с 130 до 250°С, механические потери увеличиваются с
0,8 до 4-5 %, потери от химической неполноты горения — от 0,5 также до 4 — 5%,
а КПД котла падает с 92 до 70-72%.
2.7 Максимальная нагрузка барабанных и прямоточных
котлов
Повышение нагрузки барабанных и прямоточных котлов
сверх номинальной потребует форсировки тяги и дутья, т. е. увеличения расхода
воздуха и топочных газов, что приведет к перегрузке дутьевых вентиляторов и
дымососов. При этом растут присосы и увеличивается гидравлическое сопротивление
тракта котла, падает напор и производительность тягодутьевых установок, что, в
конечном счете, ограничивает повышение нагрузки и даже приводит к необходимости
ее понижения. Таким образом, режим тягодутьевых установок является одним из
серьезных факторов, лимитирующих повышение нагрузки котельных агрегатов сверх
номинальной.
Другим немаловажным фактором, ограничивающим
возможности повышения нагрузки котлов, является абразивный золовой износ
поверхностей нагрева, приводящий, как правило, к необходимости аварийного
ремонта. Этот износ в котлах, сжигающих высокозольное твердое топливо,
пропорционален кубу скорости топочных газов.
Эксплуатационная статистика показывает, что наибольшее
число внеплановых аварийных остановок котлов приходится на период зимнего
максимума, когда они работают в наиболее напряженных условиях с максимальной
нагрузкой.
В котлах с твердым шлакоудалением доля золы в уносе
составляет
85 — 90 %, при жидком шлакоудалении — 70 – 80 %, в циклонных топках –
30 – 50 %. При твердом шлакоудалении частицы золы обладают очень большой
абразивностью, так как они не оплавлены и имеют острые края.
Экибастузский уголь является наиболее износоопасным
из-за своей высокой зольности, превосходящей 40 % и из-за высокого коэффициента
абразивности золы. Предельные допустимые скорости топочных газов в котлах,
сжигающих такие угли, подсчитанные с учетом приемлемого срока службы металла
труб поверхностей нагрева, находятся на низком уровне (6—7 м/с) и сильно
ограничивают максимальную производительность котельного агрегата.
В котлах с жидким шлакоудалением и в котлах с
циклонными топками абразивный износ хотя и существует, но его интенсивность
намного меньше и этот фактор там почти не ограничивает предельной мощности.
Еще одним фактором, ограничивающим возможности
повышения нагрузки котлов сверх расчетной, является шлакование поверхностей
нагрева.
Существует понятие «бесшлаковочной» мощности
котельного агрегата, т.е. такой производительности, при которой температурный
режим в топке не вызывает шлакования поверхностей нагрева. Номинальная нагрузка
котла должна быть, как правило, несколько ниже «бесшлаковочной» мощности и не
превышать ее ни при каких условиях.
Серьезное ограничение максимальной производительности
барабанных котлов обусловлено ухудшением сепарации влаги в барабане котла при
повышенных нагрузках. При работе современных турбин предъявляются очень жесткие
требования к влажности пара, которая не должна превышать 0,1 %. Объясняются эти
требования недопустимостью твердых отложений в проточной части турбины, а также
во всем пароводяном тракте энергоблока. Занос солями проточной части турбины
снижает ее мощность и КПД.
3 Лекция 3. Подготовка
котла к пуску
Содержание лекции: этапы подготовительных работ перед пуском, последовательность операций.
Сборка растопочных схем. Заполнение котла водой [1, 9, 10, 12].
Цель лекции: знакомство
с подготовительными операциями при пуске котла.
3.1 Общие положения
Пуск котла — наиболее
сложный режим его работы с большим числом операций по управлению, которые
должны проводиться в определенной последовательности и часто за минимальное
время. В этих условиях требуются четкое распределение обязанностей между
персоналом оперативной вахты, координация ее действий, высокая дисциплина.
Поэтому после монтажа,
выхода из капитального или среднего ремонта пуск котла должен производится под
руководством начальника цеха или его заместителя. Во всех остальных случаях
котел пускается под руководством начальника смены или старшего машиниста.
Перед пуском
котлоагрегата из ремонта или длительного резерва (более 3 суток) необходимо
проверить исправность и готовность к работе вспомогательного оборудования,
контрольно-измерительных приборов (КИП), средств дистанционного управления
арматурой и механизмами, авторегуляторов, защит, блокировок и средств
оперативной связи. Выявленные неисправности должны быть устранены.
При неисправности защит,
действующих на останов котла, пуск его запрещается.
Пуск оборудования в
эксплуатацию после монтажа или ремонта производится только после составления
заключения лабораторией металлов электростанции (или договорной организации) о
выполнении установленного объема работ по входному контролю металла.
3.2 Подготовительные
работы и осмотр котлоагрегата
Растопку котла производят после очередного
останова или ремонта. Предварительно проверяют качество выполнения ремонтных
работ, а также устранены ли дефекты и учтены ли замечания, записанные в журнал
дефектов перед остановом котла. Для этого осматривают котел и его
вспомогательное оборудование, проверяя состояние горелок, обмуровки, обшивки,
коллекторов, паро- и водопроводов, их арматуры и подвесок (опор).
Кроме того, осматривают: вспомогательные
механизмы и их приводы, тягодутьевые машины (вентиляторы, дымососы,
воздуходувки, электро- и турбоприводы, системы охлаждения и смазки); мельницы,
питатели сырого топлива и пыли, бункера; элементы системы пылеприготовления,
обдувки; системы шлакозолоулавливания и удаления. Обязательным условием
является проверка связи, освещения, противопожарной готовности блока. Затем
проверяют запасы топлива в бункерах и воды в баках конденсата, положение
арматуры и гарнитуры на пароводяном и газовоздушном трактах, подготовку
мазутного и газового хозяйства, работу защитно-запальных устройств,
бесперебойность подачи пара от постороннего источника, правильность установки
грузов предохранительных клапанов.
После осмотра основного и вспомогательного
оборудования, проверки выполнения работ и закрытия нарядов начальник смены цеха
делает соответствующую запись в оперативном журнале с указанием времени начала
пусковых операций, о чем оповещаются связанные с пуском начальники
электрического, химического, топливного и транспортного цехов, а также цеха
контрольно-измерительных приборов и автоматики.
После сборки электрических схем
дистанционного управления, сигнализации, блокировок, защит и автоматики, их
проверки в соответствии с местными условиями и включения
контрольно-измерительных приборов собирают электрические схемы электропривода
собственных нужд блока и начинают собирать и готовить к включению
технологические схемы котла (газовоздушного тракта, растопочного, паромазутного
хозяйства, пылеприготовления, шлакозолоулавливания и удаления, обдувки и
очистки).
Тщательно вентилируют
топку и газоходы котла в течении 10 минут при открытых шиберах газовоздушного
тракта с расходом воздуха не менее 25% номинального. Перед растопкой котла из
неостывшего состояния при сохранившемся избыточном давлении в пароводяном
тракте вентиляция должна начинаться не ранее, чем за 15 минут до розжига
форсунок, для предотвращения опасных термических напряжений и переохлаждения.
До вентиляции котла
запрещается вносить в топку и газоходы котла любой открытый огонь, а также
переносную электролампу из-за опасности хлопков или взрыва скопившихся газов.
После вентиляции котла необходимо взять пробу из верхней части топки для
определения отсутствия газа.
Не допускается растопка
котлоагрегата при неисправном состоянии КИП, автоматики, защит, блокировок и
сигнализации.
Кроме того, в период
подготовки к пуску, необходимо проверить запально-защитные устройства, а при их
отсутствии подготовить достаточное количество ручных запальников. Подготовить
схему дренажей главных паропроводов. Опробовать в работе шлаковые транспортеры
шлакоудаления.
Подать воду в шлаковые
ванны, на систему золоочистки и на побудительные сопла по каналам ГЗУ.
3.3
Заполнение котла водой
Для заполнения
котельного агрегата должна использоваться деаэрированная вода. Заполнение не
деаэрированной водой, содержащей растворенный кислород и свободную углекислоту,
способствует интенсификации коррозии внутренней поверхности трубной системы и
поэтому недопустимо.
В
котельном агрегате элементы водного и парового тракта имеют разную толщину
стенок и прогреваются с различной скоростью. Экономайзерные и парообразующие
трубы, имеющие относительно небольшую толщину, прогреваются быстро, а толстые
стенки барабанов и коллекторов -значительно медленнее.
Внутренние слои металла барабана быстрее нагреваются,
чем наружные. Опыты показали, что температурная разность в стенке
Dtст (рисунок 5) может быть определена по следующей
формуле
.
Здесь
w — скорость подъема температуры
греющей среды;
а —
коэффициент температуропроводности.
Следовательно, изменение температуры по толщине стенки
происходит по квадратичной параболе. Разность температур внутренней и наружной
поверхностей стенки барабана пропорциональна скорости подъема температуры
греющей среды, которую определить достаточно трудно
.
При
быстром заполнении горячей водой неравномерный прогрев барабана может вызвать
опасные температурные напряжения внутри стенок барабана, в особенности при
низкой начальной температуре стенок. Нагретые слои металла стремятся расшириться,
в то время как холодные слои препятствуют расширению. В результате этого, во
внутренних слоях стенок барабана возникают напряжения сжатия, а в наружных —
напряжения растяжения. Теоретические расчеты показали, что эти напряжения могут
достигать достаточно больших значений и при многократном повторении пусков
могут вызвать малоцикловую усталость металла и трещины в нем.
В приближенных расчетах, принимая стенку барабана
плоской, температурные напряжения можно рассчитать по упрощенной формуле
.
Технические
обследования, проводимые на электростанциях, выявили повреждения барабанов
котлов высокого давления в виде трещин на поверхности трубных отверстий, на
поверхности обечаек, днищ, в швах приварки штуцеров, в зонах приварки
внутрибарабанных устройств. Указанные повреждения связаны с комплексом
различных факторов, в том числе и эксплуатационных, связанных с заполнением
котла водой с температурой, значительно отличающейся от температуры металла
барабана.
Поэтому при заполнении
котла водой во избежание недопустимых термических напряжений в теле барабана,
следует руководствоваться следующими положениями:
1. Запрещается
заполнение водой горячего барабана (tст
=
200 – 300 °С) при давлении в котле близком к атмосферному. Заполнение неостывшего
котла для проведения растопки разрешается при температуре металла верха
опорожненного барабана не выше 160 °С. Если температура в какой-либо точке
барабана превышает 140 °С заполнение его водой для гидроопрессовки запрещается.
2. При пуске котла из
холодного состояния и заполнении его питательной водой с температурой выше
температуры стенки барабана котел должен вначале питаться небольшим количеством
воды, чтобы при охлаждении ее в экономайзере разность температуры между водой,
поступающей в барабан и телом барабана не превышала 40 °С.
3. При заполнении
барабана котла питательной водой с температурой ниже температуры стенки
барабана допускается разность температур стенки низа барабана и питательной
воды не более 40 °С.
Во избежание повышенных
напряжений, которые могут вызвать расстройство соединений, для заполнения котла
при пусках из холодного состояния желательно использовать воду с температурой
не выше 100 °С.
В начальный период рекомендуется вести заполнение котла с небольшим расходом,
чтобы температура воды на входе в барабан не превышала
60 — 70 °С. По мере прогрева тракта и повышения расхода температуру перед
барабаном доводят до 80 -90 °С. Учитывая, что величина перепада температур определяется
скоростью прогрева, заполнение котла водой рекомендуется вести в течение 1 — 2
часов, в зависимости от состояния металла барабана.
Котел следует заполнить
водой до растопочного уровня (низший уровень в водоуказательном приборе). Во
время заполнения котла следует проверить плотность дренажей экранов котла и экономайзера
(по температуре труб после запорных вентилей на ощупь).
После заполнения котла
следует убедиться, что уровень воды в барабане не снижается, в противном случае,
нужно найти неплотности и устранить их, после чего подпитать котел до прежнего
уровня.
4 Лекция 4. Пуск котельной установки (барабанный
котел)
Содержание лекции: требования к пусковым операциям. Последовательность розжига, скорость
подъема давления. Действия персонала во время операций по подъему давления.
Основные ограничения скорости пуска котла [1, 8, 9, 10, 11, 12].
Цель лекции: знакомство
с пусковыми операциями.
4.1 Общие положения
Целью пуска котельной
установки является достижение номинальных параметров пара и такой паропроизводительности,
при которых котел мог бы работать без использования растопочных горелок.
Продолжительность пуска котла (период времени от розжига первой растопочной
горелки до достижения требуемой нагрузки и параметров пара) зависит главным
образом:
—
от начального теплового
состояния котла, определяемого длительностью его простоя и способом останова;
—
рабочих параметров,
схемы и мощности котла;
—
приспособленности котла
к пуску (в том числе от степени автоматизации пусковых процессов);
—
применяемой технологии
пуска.
Режим пуска котла должен
удовлетворять следующим требованиям: должно обеспечиваться надежное протекание
внутрикотловых процессов, необходимых для охлаждения или равномерного прогрева
всех элементов котла; скорость прогрева элементов котла не должна превышать
величину, определяемую допустимыми термическими напряжениями в металле;
пусковые потери топлива и энергии должны быть по возможности минимальными;
должна обеспечиваться безопасность работы обслуживающего персонала и
оборудования. Пусковая схема барабанного котла представлена на рисунке 6.
Рисунок 6 — Пусковая схема барабанного котла:
РКНП –
регулировочный клапан непрерывной продувки. В – воздушник. рец. – линия
рециркуляции. –
дренажи. ПП – продувка пароперегревателя. ГПЗ – главная паровая задвижка. СП –
соединительный паропровод. РР – растопочный расширитель. РРОУ – растопочная
редукционно-охладительная установка. К.С.Н. – коллектор собственных нужд. К.О.П.
– коллектор острого пара. РПК – регулировочный питательный клапан. РУ –
растопочный узел. ПМ – питательная магистраль.
4.2 Розжиг и подъем
давления
Перед розжигом
необходимо включить все контрольно-измерительные приборы, дистанционное
управление и все технологические защиты и блокировки, не препятствующие пуску
котла, а также регулятор разрежения в топке и регулятор растопочного впрыска
(если он имеется). Развернуть дутьевые вентиляторы и дымососы и отрегулировать
разрежение в верхней части топки (2 — 3 кгс/м2).
Приступить к розжигу. При
отсутствии на котле ЗЗУ допускается применение ручного запальника.
Если при розжиге первой
мазутной форсунки мазут сразу не загорится или погаснет в процессе
регулирования горения, то следует немедленно прекратить подачу мазута и пара к
форсунке, установить причину погасания и устранить ее. После этого, вновь
приступить к розжигу в вышеуказанном порядке, предварительно провентилировав в
течении 10 — 15 минут топку и газоходы котла.
При погасании мазутного
факела нескольких форсунок следует немедленно прекратить подачу мазута и пара
ко всем форсункам. Только после устранения причин погасания и тщательной
вентиляции топки и газоходов котла пятидесятипроцентным расходом воздуха в
течении 15 минут приступить к растопке в вышеуказанном порядке.
Отсутствие достаточного
количества воздуха у устья горелки или плохое перемешивание его с мазутом может
привести к забросу мазута на экранные поверхности и под топки, выносу его из
топочной камеры, осаждением в газоходах котла и возможным загоранием на
поверхностях нагрева.
Многочисленные
исследования условий пуска котла свидетельствуют о том, что узлами, лимитирующими
эти процессы, являются толстостенные элементы котла, змеевики
пароперегревателя, пускосбросные устройства, система розжига, устройства
контроля, автоматики и управления.
Контроль за скоростью
растопки удобней всего производить по температуре насыщения. В современных
котельных агрегатах в начальный период растопки наблюдается существенная
неравномерность прогрева стенок барабана. Стенки его верхней части, находящиеся
в паровом пространстве, прогреваются более интенсивно, чем нижней, так как коэффициент
теплоотдачи при конденсации пара в 3 — 4 раза превышает коэффициент теплоотдачи
от воды к стенке. В результате неравномерность может достигать 60 — 80 °С в
разные периоды растопки. При значительной разности температур барабан может
подвергаться деформации в форме изгиба. Исследования показывают, что уже при
разности температур 20 — 30 °С напряжения в металле возрастают примерно в 2
раза.
Исходя из вышесказанного
в период растопки котла скорость роста температуры насыщения, по условию
допустимых термических напряжений стенок барабана котла и допустимых температур
стенок пароперегревателя не должна превышать 2 °С в минуту при давлении в
барабане меньше 20 кгс/см2 и 2,5 °С в минуту при давлении более 20
кгс/см2, что обеспечивается подъемом давления в котле в соответствии
с графиком растопки.
Отсюда следует, что
продолжительность растопки из холодного состояния барабанного котла составляет,
в зависимости от параметров пара, примерно
3 — 5 часов.
Основным условием
нормального пуска котла является соблюдение критериев пуска, т.е. работа в
пределах допустимых температур, перепадов температур и скоростей их изменения
для всех элементов котла. По условиям экономичности каждый из этапов пуска
котла должен проводиться с предельно допустимой скоростью, что позволяет
сократить продолжительность пуска и уменьшить пусковые потери.
Во время растопки
необходимо тщательно следить за температурами дымовых газов в конвективной
части котла и температурой воздуха за воздухоподогревателем. При признаках
возникновения пожара (практически признаком загорания следует считать резкое
повышение температуры газов в газоходе на 20 — 30 °С выше обычной) немедленно
произвести осмотр газоходов. Если в результате осмотра подтвердится
возникновение пожара, необходимо немедленно прекратить растопку, остановить
дутьевые вентиляторы, вентиляторы горячего дутья, дымососы, закрыть направляющие
аппараты дымососов и вентиляторов, закрыть клапаны на подводах вторичного
воздуха к горелкам, проверить плотность закрытия всех гляделок и лазов и
включить установку пожаротушения.
Обязательно проверить
включение и исправность работы сниженных указателей уровня. Переход на контроль
за уровнем воды в барабане по сниженным указателям уровня производится лишь
после того, как их показания будут совпадать с показаниями водоуказательных
приборов.
При растопке котла
необходимо поддерживать уровень воды в барабане между нижним и верхним
допускаемым значениями, сбрасывая при необходимости избыток воды через линию
аварийного слива. Подпитка котла в начале растопки производится вручную. Перед
включением автоматики регулятора питания котла следует включить защиты по
уровню воды в барабане.
При подпитках
температура воды, поступающей в барабан, не должна отличаться от температуры
тела барабана более, чем на 40 °С.
4.3 Повышение надежности
работы экономайзера и пароперегревателя при пуске
Большое значение при
пусках котла уделяется повышению надежности охлаждения экономайзера. В
нормальных условиях работы скорость воды в водяных экономайзерах (ВЭ)
достаточна и тепловая неравномерность мала. Однако в процессе пуска режим
работы ВЭ резко отличается от нормального. При отсутствии надежного охлаждения
в его выходных участках может образоваться перегретый пар и чрезмерный перегрев
труб. В период растопки питание обычно осуществляется периодически. Поэтому
возникают пульсации температуры воды и температурные напряжения в стенках.
Для защиты водяных
экономайзеров от перегрева в период растопки широко используют две схемы: схема
рециркуляции, в которой барабан котла соединяется с нижним коллектором
экономайзера (при многоступенчатой компоновке — к входному коллектору выходной
ступени); схема со сгонной линией, в которой вода после экономайзера
возвращается в деаэратор или питательный бак станции.
При растопке котла необходимо
следить за температурами металла змеевиков пароперегревателя. Режим растопки
организовать таким образом, чтобы эти температуры не превышали допустимых.
Хотя количество теплоты,
отдаваемое газами в области пароперегревателя при пуске значительно меньше, чем
при номинальной нагрузке, расход пара через них невелик и поэтому возможен
существенный перегрев змеевиков ПП во время растопки. В обычных условиях
температура стенки выше температуры пара на 12 — 30
°С. Иная картина при пуске котла. В
начальный период растопки эта разница может достигать 150 — 250
°С, поэтому во избежание пережога труб в
период растопки через пароперегреватель необходимо пропускать 10 — 15 % пара
(продувка пароперегревателя). В зависимости от параметров пара продувка может
полезно использоваться. Для горизонтальных пароперегревателей можно
использовать заливку его водой.
В случае недостаточности
охлаждения труб протекающим паром, следует изменить режим растопки, чтобы не
допускать чрезмерного повышения температуры газов в районе пароперегревателя.
Кроме того, для защиты
металла змеевиков топочных ширм во время растопки на котлах устанавливаются растопочные
пароохладители с впрыском питательной воды.
5 Лекция 5. Включение
котла в магистраль и переход на основной вид топлива
Содержание лекции: прогрев паропровода, скорость прогрева паропровода, подключение котла к
магистрали. Условия перевода котла на твердое топливо, последовательность
операций при переводе [1, 7, 8, 9, 10].
Цель лекции: знакомство
с операциями и условиями подключения котла к магистрали и перевода котла на
твердое топливо.
5.1 Прогрев паропровода до магистрали
До включения котла в магистраль
необходимо прогреть соединительный паропровод от котла до паровой магистрали.
Подъем давления и температуры в паропроводе необходимо вести равномерно для
предотвращения чрезмерных внутренних напряжений.
При прогреве убедиться,
что подключены все приборы по давлению пара и его температуры, металла на
прогреваемом участке, что открыты все вентили ревизии на прогреваемом участке.
Прогрев паропровода осуществлять
через байпасы паровой задвижки. Медленно дать пар в паропровод и установить
давление 1-2 кгс/см2. Затем параллельно с подъемом давления на котле
осуществлять подъем давления в паропроводе.
В процессе подъема
давления убедиться, что конденсат с ревизий сошел и идет пар. Открыть вентиль
продувки главного паропровода на расширитель продувок высокого давления,
закрыть ревизии.
Следить чтобы скорость
прогрева паропровода не превышала 3 — 4
°С/мин.
Общая продолжительность
прогрева паропровода составляет обычно
2,5 — 3 часа.
При подъеме давления в
паропроводе скорость повышения температуры металла главного паропровода
регулировать вентилем продувки на расширитель продувок высокого давления.
После подъема давления
до полного, открыть ГПЗ и закрыть ее байпасы.
При прогреве паропровода
не допускать гидроударов, вибрации, следить за состоянием опор, подвесок,
арматуры, за тепловыми расширениями паропровода по реперам.
5.2 Включение котла в магистраль
Включение котла в магистраль
производить только после тщательного дренирования и прогрева паропровода от
ГПЗ-1 до ГПЗ-2.
Давление пара за котлом
при включении должно быть несколько ниже (не более 1 — 2 кгс/см2)
или равно давлению в общем паропроводе. Это условие необходимо выполнять для
того, чтобы поток пара, возникающий из-за разницы давлений при открытии байпаса,
двинулся не в магистраль, а в котел, где в паровом объеме барабана он затормозится,
при этом давление станет ровным без возникновения скачков давления. Большие перепады
давления, как в большую, так и в меньшую сторону приведут к возникновению
гидравлических ударов и изменению температуры в паропроводе.
При включении необходимо
следить за температурой острого пара и не допускать резких снижений или
набросов температуры перед турбинами. Включение котла следует производить осторожно,
медленным открытием байпаса магистральной паровой задвижки. После выравнивания давления
по сторонам задвижки открывается задвижка, а байпас после полного ее открытия
закрывается. Если при этом в паропроводе возникают гидравлические удары и толчки,
следует немедленно приостановить операции по включению котла, понизить давление
в котле, тщательно прогреть паропровод, после чего вновь приступить к включению
котла.
Дренажи на паропроводе перед
магистральными задвижками закрыть после полного открытия задвижек.
Во время включения котла
запрещается изменять режим горения.
После включения котла в магистраль
следует приступить к отключению РРОУ (или продувки пароперегревателя) и подъему
нагрузки, тщательно следя при этом за показаниями манометров, расходомеров воды
и пара, уровнем воды в барабане, а также за температурами пара по тракту
пароперегревателя и за температурами металла змеевиков пароперегревателя.
Включение регуляторов
температуры перегретого пара производится при достижении номинальной температуры
пара. Остальные автоматические регуляторы включаются после достижения
устойчивого режима работы и нагрузки котла около 70 % от номинальной.
Если котел растапливается
впервые или после капитального ремонта, то при достижении полного давления, до
включения котла в магистраль производится регулировка предохранительных
клапанов.
5.3 Перевод котла на сжигание твердого топлива
Для надежного воспламенения
угольной пыли при растопке котла необходимо предварительно прогреть топочную
камеру растопочным топливом. Степень прогрева зависит от вида топлива, его
реакционной способности, влажности и т.д.
При переводе котла на
сжигание твердого топлива все мазутные форсунки должны находиться в работе. Перевод
котла на сжигание твердого топлива должен производиться только при достижении
устойчивого горения факела мазутных форсунок и при температуре горячего воздуха
за воздухоподогревателем более 250
°С,
что соответствует устойчивому воспламенению угольной пыли. На котлах,
работающих на топливах с выходом летучих менее 15%, переход на сжигание
твердого топлива разрешается при тепловой нагрузке топки не ниже 30 %
номинальной. При работе на топливах с выходом летучих более 15 % разрешается
подача пыли при меньшей нагрузке, которая устанавливается инструкцией по
эксплуатации.
При переходе на сжигание
пыли и настройке режима работы системы пылеприготовления необходимо следить за
факелом в топке. В случае полного обрыва факела необходимо прекратить подачу
пыли в топку, отключить подачу мазута к форсункам. После тщательной вентиляции топки
и газоходов вновь зажечь мазутные форсунки и при достижении устойчивого горения
возобновить подачу пыли к горелкам.
В процессе перевода котла
на сжигание пыли, внимательно следить за уровнем воды в барабане, за температурами
металла, змеевиков пароперегревателя, за температурами газов по тракту, за
отсутствием сепарации пыли из факела.
6 Лекция 6. Пусковая
схема прямоточного котла. Особенности пуска
Содержание лекции: требования к пусковым схемам. Типовая схема, основные элементы,
требования к пусковым операциям. Одно байпасные и двух байпасные пусковые
схемы. Пуски из различных тепловых состояний [2, 3, 4, 8, 9, 10, 12].
Цель лекции: знакомство
с пусковыми операциями и особенностями пусков прямоточных котлов.
6.1 Пусковые схемы прямоточных котлов
Прямоточные котельные установки
применяются в основном для мощных энергетических блоков. Необходимость обеспечения
маневренности и мобильности блоков, сохранение их высокой надежности и
экономичности при различных режимах работы требуют большого внимания к
разработке тепловых и пусковых схем.
Разнообразие пусковых схем блоков
объясняется применением различных типов котлов, турбин, растопочных и
пускосбросных устройств, методов регулирования температуры основного и промежуточного
пара, а также конструкций и способов охлаждения промежуточного
пароперегревателя. Основное внимание, уделим блокам с прямоточными паровыми
котлами сверхкритического давления как наиболее распространенным и
перспективным.
Наиболее полно условия надежного пуска
блока удовлетворяются при режиме скользящего изменения параметров свежего и
промежуточного пара. В тракте котла имеются встроенные задвижки. Тогда перед
задвижкой давление поддерживается близким к рабочему, а за ней снижается до
требуемого уровня (в зависимости от условий прогрева последующих поверхностей и
турбины).
Чтобы обеспечить режим работы на
скользящих параметрах, наряду с встроенными задвижками предусматривают
растопочные сепараторы, которые могут располагаться за паровым котлом или у задвижки.
В соответствии с этим схемы получили названия: с выносными и встроенными сепараторами.
Наиболее часто используют схему с
встроенными сепараторами 4 (рисунок 7), которые через трубопроводы с
дроссельными клапанами 5 присоединяют к тракту 2 котла перед встроенной
задвижкой 6. Сепараторы устанавливают на каждый поток рабочего тела.
Отсепарированная влага через систему трубопроводов и
дроссельный клапан 3 сбрасывается в конденсатор 14 турбины, а пар поступает в
перегревательный тракт 8 за встроенной задвижкой. Расход пара регулируется
открытием редукционно-охладительной установки 9 (РОУ) или пускосбросного устройства
10 (ПСБУ).
По условиям охлаждения топочных экранов
при пуске целесообразно поддерживать расход рабочего тела около 30%
номинального. Максимальный расход топлива при пуске определяется температурными
условиями работы первого пакета пароперегревателя за встроенной задвижкой. По
результатам исследований температуры стенки этого пакета на обеспаренном режиме
стартовый расход топлива при пуске из холодного состояния должен быть не более
10 — 12% (иногда до 20 %) номинального. Контрольным параметром является
температура газов перед этой поверхностью, которая не должна превышать 550
°С.
В зависимости от схемы сброса пара и
охлаждения промежуточного пароперегревателя различают одно- и двухбайпасные пусковые
схемы блоков.
При однобайпасной схеме избыток свежего
пара из паропровода через пускосбросное устройство сбрасывается в конденсатор.
Промежуточный пароперегреватель либо не охлаждается, либо охлаждается паром из
коллектора собственных нужд или растопочного узла котла.
В двухбайпасной схеме предусмотрен сброс
пара из паропровода свежего пара в «холодный» паропровод промперегрева, а затем
после прохождения промежуточного пароперегревателя из «горячего» паропровода
промперегрева в конденсатор. Для этой цели устанавливают два пускосбросных
устройства, которые должны работать синхронно. Двухбайпасную схему применяют,
когда промежуточный пароперегреватель располагается в зоне высоких температур
газа (более 850 °С) и его необходимо обязательно охлаждать.
6.2 Пусковые операции
При сепараторном режиме перед ВЗ рабочая
среда направляется в сепаратор 4, после которого требуемое количество пара поступает
в перегревательные поверхности, а остальная часть – в растопочный расширитель.
Применение встроенной задвижки позволяет поддерживать номинальное давление
среды до нее и переменные, постепенно повышающиеся давление и температуру в
перегревательных поверхностях, паропроводах и перед турбиной. Это обеспечивает
надежную работу напряженных поверхностей до ВЗ при постепенном прогреве их и
паропроводов за ней. Повышение параметров за ВЗ определяется начальным
состоянием котла перед пуском и требуемой скоростью прогрева наиболее
толстостенных деталей – коллекторов, арматуры, корпусов устройств парораспределения
и турбин.
Пуск из холодного состояния. После
длительного останова пуск блока начинается при низком уровне температуры и
давления рабочей среды и обычно сопровождается горячей промывкой поверхностей
нагрева до ВЗ, проводимой при включенных растопочных горелках. Тракты
промперегрева начинают прогреваться после толчка турбины и поступления в них
пара. При этом постоянно контролируют температуру пара, стенок элементов котла
и паропроводов и регулируют ее, включая впрыски и охлаждение. После прогрева
паропроводов подают пар в ЦСД и начинают постепенно повышать нагрузку.
Завершив подготовительные операции,
включают форсунки, после чего сразу открывается клапан 7 (Др-3) во избежание
последующих тепловых ударов при внезапном вводе в перегреватели разогретого
пара и его конденсации на еще холодных поверхностях. При проведении горячей
промывки до ее окончания устанавливают расход топлива В= (0,06 — 0,07) Вном.
Окончив горячую промывку, переводят воду из расширителя Р-20 в конденсатор 14 и
настраивают регулятор уровня Р-20. Затем начинают повышать параметры и расход
пара, увеличивая расход топлива до растопочного Вр= (0,10 — 0,12)
Вном. При этом контролируют температуру среды перед ВЗ (tвоз=300 — 310
°С) и газов в
поворотной камере (JПК=500 — 550
°C).
После достижения перед ВЗ температуры
t’B3=410°C,
превышающей температуру насыщения, переходят на прямоточный режим, полностью
закрывая клапан Др-2 и задвижки на сбросе воды и пара из сепаратора 4. Дальнейшее
нагружение турбины проводят на прямоточном режиме, увеличивая тепловыделение в
котле (расход топлива) и переходя в это время на основное топливо.
При нагрузке N=0,6 Nnom, прикрывая
регулирующие клапаны, переводят свежий пар на номинальное давление 24 МПа,
включают регулятор давления блока, полностью открывают ВЗ и переводят систему
впрысков на полное давление. С переходом на номинальное давление нагружают блок
на 100%-ную нагрузку, постепенно повышая температуру пара. До достижения
номинальной температуры свежего пара и пара промперегрева регулирование ведут
пусковыми впрысками, а затем переходят на штатные впрыски, отключая пусковые.
Пуски блока из холодного состояния и их
графики-задания являются базовыми для проведения пусков из других состояний.
Пуски из неостывшего и горячего
состояния, из горячего резерва. При неполном охлаждении котла (температура коллектора
превышает 80°С) пуск производят как из неостывшего состояния. Различают
несколько разновидностей пусков блоков из неостывшего состояния в зависимости
от продолжительности предыдущего останова и степени охлаждения коллекторов,
паропроводов и толстостенных деталей турбин. Условно выделяют пуски из
неостывшего состояния после длительных остановов (до 90 ч), когда требуется
прогрев паропроводов промперегрева, и после остановов меньшей продолжительности
( до 45 ч), когда предварительный прогрев не требуется.
Пуск из горячего состояния производится после останова блока на 2-8 ч и
характеризуется более быстрым его включением, исключением сброса воды из
расширителя в циркуляционный водовод, уменьшением или отсутствием пропуска пара
на предварительный прогрев паропроводов, повышением частоты вращения после
толчка турбины сразу до n=50 1/с без выдержек на промежуточной частоте. Время
пуска из горячего состояния до полной нагрузки составляет до 2,5 ч, что в 1,8-2,5
раза меньше времени пуска из неостывшего и холодного состояния.
Пуск из горячего резерва (после простоя менее 30 мин) непродолжителен и может
выполняться по прямоточному режиму.
Существующая тенденция развития энергетики
и энергопотребления предполагает частый вывод блоков в горячий резерв или на
останов, поэтому пуски их из неостывшего и горячего состояния становятся
наиболее распространенными.
7 Лекция 7. Останов
и расхолаживание котельной установки
Содержание лекции: основные виды остановов котельных агрегатов. Нормальный останов
парового котла. Основные операции при останове котла. Расхолаживание котла. Консервация котла. Аварийный останов
[1, 8, 9, 10, 11, 12].
Цель лекции: знакомство
с остановочными операциями, случаями аварийного останова котла.
Следует различать четыре
вида остановок котельного агрегата, характеризующих условия расхолаживания котла
и действия оперативного персонала: останов в «горячий» резерв; останов
в «холодный» резерв; останов в ремонт; аварийный останов.
7.1 Нормальный останов
парового котла
При останове котла постепенно снижают
нагрузку, уменьшая расход топлива, питательной воды, воздуха и загрузку
дымососов. В схемах с прямым вдуванием пыли расход топлива уменьшают разгрузкой
питателей сырого топлива и последующим постепенным остановом их и
соответствующих мельниц. В схемах с промежуточными бункерами первоначально
отключают питатели сырого топлива и мельницы, а затем уменьшают загрузку
питателей пыли и постепенно выводят их из работы. Скорость снижения нагрузки
определяется допустимой скоростью изменения температуры металла наиболее
толстостенных элементов оборудования. Чтобы не появились значительные
температурные напряжения в начальный период останова (иногда до минимально
устойчивой нагрузки), поддерживают номинальную температуру пара. Номинальное давление
пара за котлом разрешается поддерживать до нагрузки не ниже 50 % от
номинальной.
Если котел или система
пылеприготовления останавливаются на длительное время, следует срабатывать все топливо
из бункеров и питателей сырого угля.
После отключения системы
пылеприготовления погасить все мазутные форсунки, провентилировать топку и
газоходы в течение 10 — 15 минут, при условии, что расход воздуха через топку,
определяемый по загрузке электродвигателей дутьевых вентиляторов, составляет не
менее 50 % от номинального. Остановить дутьевые вентиляторы и дымососы, закрыть
их направляющие аппараты.
По мере снижения
нагрузки питания котла перевести с основной на байпасную линию узла питания. При
переходе на питание котла через байпас перейти с основного регулятора питания на
растопочный регулятор питания.
При прекращении
постоянной подпитки котла открыть задвижки на линии рециркуляции из барабана к
экономайзеру. При снижении уровня воды в барабане на 100 мм от среднего
произвести подпитку котла с возможно меньшим расходом для предотвращения недопустимых
термических напряжений в теле барабана. Подпитать котел до +100 мм от среднего
уровня после чего питание прекратить. Перед подпиткой проверить закрытие задвижек
на линии рециркуляции из барабана в трубопровод перед экономайзером. Наблюдение
за уровнем продолжать до сохранения в котле давления.
Запрещается производить подпитку
остановленного котла с дренированием воды в целях ускоренного охлаждения барабана.
Во время останова котла также,
как при пуске необходим тщательный контроль за разностью температур верха и
низа барабана, которая не должна превышать 60
°С, для чего необходимо охлаждение проводить со скоростью
1,5 °С/мин при давлении в
барабане меньше 100 кгс/см2.
В процессе снижения нагрузки
следить за температурой пара и при ее снижении уменьшить подачу конденсата в
пароохладители. При снижении температуры пара до минимально возможной по
условиям работы станции включить РРОУ и закрыть магистральную задвижку перед
главным паропроводом. После снижения параметров пара до минимально возможных,
по условиям работы РРОУ, (давление 16-20 кгс/см2 и температура 300
°С) отключить РРОУ, включить продувку
пароперегревателя в атмосферу или на барбатер, закрыть ГПЗ-1 и открыть дренаж
паропровода.
При прекращении подачи
пара из котла продувку пароперегревателя закрыть.
В случае необходимости
ускоренного расхолаживания котла для ремонта включить паровое расхолаживание барабана
согласно инструкции по эксплуатации УПРО.
После останова котла
следует внимательно следить за температурой газов и воздуха по конвективной
шахте по приборам и производить обходы с целью выявления загораний через 5-6
часов.
При признаках загорания
немедленно произвести осмотр газохода, проверить температуру газов и воздуха по
всем установленным термопарам, поставить в известность пожарную команду и в
дальнейшем вести наблюдение за участком вероятного возгорания.
При останове котла без применения
устройства парового охлаждения барабана пуск дымососа для расхолаживания
разрешается не ранее, чем через 10 часов после останова котла — для котлов с
давлением пара до 140 кгс/см2, через 18 часов — для котлов давлением
140 кгс/см2 и выше, при условии, если
разность между
температурой стенки верха и низа барабана не превышает 60
°С.
Через шесть часов после
останова котла необходимо произвести продувку нижних точек для удаления шлама,
после чего медленно подпитать котел до высшего уровня.
Через восемь-десять часов
продувку через нижние точки и подпитку повторить.
В случае необходимости
спуска воды при останове котла спуск следует производить немедленно после
снижения давления до атмосферного, используя для осушки внутренних поверхностей
тепло, аккумулированное обмуровкой.
При необходимости
ревизии внутрибарабанных устройств после слива воды отключить котел от всех трубопроводов,
находящихся под давлением. Люк барабана открывать осторожно: вначале слегка
ослабить болты и лишь убедившись, что воды и пара нет, открыть люк.
Для обеспечения безопасности
во время расхолаживания дежурный персонал должен осуществлять контроль за остановленным
котлом до полного снижения давления в котле и снятия напряжения с
электродвигателей.
Это требование
обусловлено также тем, что на остановленном оборудовании не исключены случаи загорания
отложений в пылесистемах и газоходах котла.
7.2 Консервация котла
Для предотвращения стояночной
коррозии пароводяной тракт котла должен подвергаться консервации при выводе
котла в резерв, останове его на текущий и капитальный ремонт и других кратковременных
аварийных и плановых остановах.
Стояночная коррозия протекает
под воздействием кислорода воздуха, попадающего в пароводяной тракт при останове
котла и снижении давления в нем до атмосферного.
Характерные особенности стояночной
коррозии — образование на поверхности металла язвин и накопление большого
количества продуктов коррозии металла, что приводит к развитию коррозионных
процессов при последующей эксплуатации оборудования.
Остановы котла по длительности
можно условно разделить на две группы:
— кратковременные остановы
в резерв на срок не более трех суток;
— длительные остановы на
срок более трех суток (резерв или ремонт).
Для защиты от коррозии применяют
сухой, мокрый и газовый способ консервации, в ряде случаев применяют консервацию
избыточным давлением.
7.3 Аварийный останов
котла
Котельный агрегат должен
быть немедленно остановлен действием защит или персоналом, без согласования
действий с руководством цеха и станции, в случаях:
а) недопустимого повышения
или понижения уровня воды в барабане или выходе из строя всех водоуказательных
приборов;
б) быстрого снижения
уровня воды в барабане несмотря на усиленное питание котла;
в) прекращения действия всех
питательных устройств (насосов);
г) недопустимого повышения
давления в пароводяном тракте котла;
д) прекращения действия
более 50% предохранительных клапанов или других заменяющих предохранительных
устройств;
е) разрыва труб
пароводяного тракта или обнаружения трещин, выпучин, пропусков в сварных швах в
основных элементах котла (барабане, коллекторах, паропроводах), питательных
трубопроводах и пароводяной арматуре);
ж) погасания факела в
топке;
з) недопустимого понижения
давления газа или мазута за регулирующим клапаном(при работе котла на одном из
этих видов топлива);
и) отключения всех
дымососов или дутьевых вентиляторов;
к) взрыва в топке, взрыва
или загорания горючих отложений в газоходах и золоуловителе, разогрева докрасна
несущих балок каркаса, при обвале обмуровки, а также других повреждениях,
угрожающих персоналу или оборудованию;
л) пожара, угрожающего
персоналу или оборудованию, а также цепям дистанционного управления отключающей
арматуры, входящей в систему защиты котла;
м) исчезновения напряжения
на устройствах дистанционного и автоматического управления и на всех контрольно-измерительных
приборах.
Допустимые повышения и
понижения параметров оговариваются в инструкциях по эксплуатации. Отключение
котла, в большинстве случаев, должно осуществляться действием защит, однако, если
не сработает защита, все операции по останову котла должен производить
оперативный персонал.
Кроме перечисленных выше
аварийных случаев, могут возникнуть такие повреждения, с которыми котел может
проработать некоторое время. В этих случаях решение об останове котла принимает
главный инженер станции по согласованию с диспетчером энергосистемы. Приведем некоторые
примеры. Котел должен быть остановлен в случаях:
а) обнаружения свищей в трубах
поверхностей нагрева, паропроводах, коллекторах, в питательных трубопроводах, а
также течей и парений в арматуре, фланцевых соединениях;
б) недопустимого повышения
температуры металла поверхностей нагрева, если снизить температуру изменением режима
работы не удается;
в) выхода из строя всех
дистанционных указателей уровня воды в барабане котла;
г)
резкого ухудшения качества питательной воды против установленных норм;
д) прекращении работы
золоуловителей;
е) неисправности отдельных
защит или устройств дистанционного и автоматического управления, а также контрольно-измерительных
приборов.
Следует сказать, что
длительная работа с указанными повреждениями недопустима, так как может
привести к серьезным авариям.
8 Лекция 8. Загрязнения, эрозия и коррозия
конвективных поверхностей нагрева
Содержание лекции: загрязнение поверхностей нагрева, виды отложений, влияние отложений на
эффективность работы котла. Абразивный износ. Способы защиты от абразивного
износа. Высокотемпературная коррозия, причины, борьба с ней. Низкотемпературная
коррозия [2, 4, 6, 8, 12, 13, 14].
Цель лекции: знакомство
с физико-химическими процессами проходящими на внешней стороне конвективных
поверхностей нагрева.
8.1 Загрязнения и абразивный износ конвективных
поверхностей нагрева
Поступающие вместе с топливом в зону горения
минеральные примеси подвергаются высокотемпературным физическим
преобразованиям: часть из них плавится и даже испаряется, другие в этих
условиях образуют новые эвтектические сплавы и соединяются в более крупные
расплавленные частицы, которые выпадают в нижнюю часть топки (холодную воронку)
в виде . Основная масса мелких золовых частиц
уносится из топки с продуктами сгорания в виде летучей золы.
В составе летучей золы имеются три группы частиц,
отличающиеся по химическому составу и физическим свойствам в зоне высоких
температур.
Легкоплавкие компоненты имеют температуру плавления
700-850°С (NaCI, CaCl2, Na2SO4, MgCl2,
Al2(SO4)3).
Среднеплавкие компоненты золы с температурой плавления
900-1100°С (FeS, Na2SiO3, K2SO4 и
др.).
Тугоплавкими компонентами являются, как правило,
оксиды металлов типа МеО (CaO, MgO, FeO), а также SiO2, Fe2O3,
Al2O3 и др. Температура их плавления (1600-2800°С)
превышает температуру газов в ядре факела.
Особенно неблагоприятными характеристиками обладает
оксид кальция. При содержании в золе СаО = 25 — 40% и наличии оксидов серы в
потоке газов, в отложениях активно происходит сульфатизация. В результате
развивается цементация (спекание) слоя отложений и его постепенное нарастание.
Это явление называют шлакованием конвективной поверхности нагрева.
При увеличении в золе оксидов Al2O3
+ SiO2 (особенно более 60% массы летучей золы) температура плавления
золы заметно увеличивается и шлакование поверхностей исключается.
Особый вид связанных липких и цементирующихся
отложений образуется на поверхности воздухоподогревателя при температуре стенки
ниже 200°С, где начинается конденсация на поверхности нагрева паров серной
кислоты совместно с влагой.
В зоне относительно низких температур газового потока
— менее 700°С — наиболее распространены при сжигании твердых топлив сыпучие
отложения, которые имеют слабую механическую связь с поверхностью и между собой
и легко удаляются при встряхивании или прямом ударе по участку отложений.
Интенсивность образования сыпучих отложений сильно зависит от фракционного
состава золы. Крупные фракции золы размером свыше 30 мкм обладают достаточно
большой кинетической энергией при движении около трубы и разрушают нарастающие
отложения за счет более мелких частиц. В таких случаях отложения оказываются
незначительными.
Большое влияние на степень загрязнения поверхности
оказывают тип пучка труб (шахматный или коридорный) и продольный шаг труб s2
в шахматном пучке. При равных прочих условиях (скорость газов, диаметр труб)
коэффициент загрязнения коридорного пучка в 1,7-3,5 раза больше, чем
шахматного.
Загрязнение труб существенно возрастает при низких
скоростях газового потока, поэтому скорости газов в поверхностях менее 3-4 м/с
не допускаются, а с учетом рабочего диапазона нагрузок котла скорости газов при
номинальной нагрузке принимаются не ниже 6 м/с для поперечно омываемых пучков
труб и не менее 8 м/с — для продольного тока газов в поверхностях
воздухоподогревателей.
определяется тем, что крупные частицы , обладающие достаточной твердостью и остротой граней,
при ударах о стенку трубы непрерывно срезают с поверхности микроскопически
малые слои оксида металла, постепенно уменьшая в этом месте толщину стенки
трубы. Частицы несгоревшего топлива (чаще у антрацитов и полуантрацитов) также
вызывают истирание поверхности.
Таким образом, золовой износ прежде всего определяется
частиц золы.
зависит от содержания SiO2 в золе и заметно увеличивается, когда SiO2
> 60%. Так, например, сильно абразивными свойствами обладают зола
экибастузского каменного угля, так как в ее составе содержание SiO2
> 80%. Интенсивность износа также зависит от общего количества золы в
топливе.
Интенсивность износа неравномерна как по сечению
газохода, так и по периметру труб. При входе в конвективную шахту из
горизонтального газохода газы имеют разворот на 90°, в результате чего наиболее
грубые фракции золы отбрасываются к задней стене шахты и имеют там повышенную
концентрацию.
При поперечном обтекании трубы наибольшему износу
подвергаются боковые ее стенки под углом 30-50°, где обтекающий трубу поток
проходит по касательной к поверхности. Коридорные пучки подвергаются
существенно меньшему износу, так как по ходу газов трубы находятся в
аэродинамической тени первой (лобовой) трубы, на которую к тому же поток газов
набегает с более низкой скоростью (из свободного газохода), чем скорость газов
в межтрубном пространстве пучка.
Интенсивность износа определяется:
— кинетической энергией отдельных частиц золы, которая
зависит от квадрата скорости газов w2г;
— количеством частиц, проходящих у поверхности в
единицу времени, которое зависит от концентрации частиц в потоке газов mЗЛ
и является возрастающей функцией от скорости wг;
— неравномерностью концентраций золы в потоке km
и скоростей газов в сечении kW;
— плотностью расположения труб в поперечно омываемом
пучке, что определяет торможение частиц при контакте с поверхностью и
уменьшение их скорости по сравнению со скоростью газов.
В итоге интенсивность износа, мм/год, зависит в
третьей степени от скорости газов:
где
а — коэффициент абразивности золы, мм·с3/(г·ч);
m — относительный показатель износоустойчивости труб,
зависящий от химического состава стали;
tР — время эксплуатации поверхности, ч/год;
km = 1,2 — 1,25, kW = 1,25 —
1,3.
Допустимым считается износ стенки трубы Iиз
= 0,2 мм/год из расчета нормальной работы трубы не менее 10 лет (tР
= 60 — 70 тыс. ч).
Методами пассивной локальной защиты являются накладки
сверху на всю длину трубы полуцилиндрических сменных манжет, наплавка прутков с
двух сторон трубы в зоне наибольшего износа,
установка на входе в трубы воздухоподогревателя внутренних цилиндрических
вставок длиной не более 10dвн.
8.2
Высокотемпературная коррозия
Под термином высокотемпературная коррозия понимается
коррозионное разрушение металла труб поверхностей нагрева, соприкасающихся с
продуктами сгорания высокой температуры (υ
> 700 °С). К высокотемпературной коррозии относятся два вида коррозии
металла, происходящие в разных зонах котла и имеющие различный химический
характер. Одним из видов является наружная коррозия
топочной камеры в зоне расположения ядра, определяемая контактом сернистых
газов с металлом труб. Другой вид характеризуется коррозией труб
пароперегревателей, разрушением элементов их креплений за счет присутствия в
газовом потоке оксидов ванадия.
Наружная коррозия труб экранов возникает при сжигании
топлив с малым выходом летучих веществ и сернистого мазута и связана с
образованием вблизи поверхности труб экранов заметной концентрации сероводорода
H2S.
Коррозия экранов развивается интенсивно на уровне
расположения горелок, когда экраны непосредственно омываются расширяющейся
струей аэросмеси на выходе из .
Скорость коррозии металла лобовой части труб может
составить 3-4 мм/год, т.е. трубы экранов выходят из строя менее чем через год
(при толщине стенки 5-6 мм допустимое локальное уменьшение толщины составляет 2 мм).
Даже при незначительных объемных концентрациях H2S
у поверхности экранов (0,04 — 0,07 %) скорость коррозии металла возрастает в
5-10 раз по сравнению с допустимой при содержании H2S = 0,01%.
Для исключения коррозионного разрушения экранов
необходимо обеспечить равномерную раздачу топлива и воздуха по горелкам так,
чтобы в каждой из них постоянно имел место избыток воздуха больше единицы.
Кроме того, следует исключить прямой удар пылевоздушной струи из горелки в
боковой экран на близком расстоянии от амбразуры.
Второй вид коррозии связан с окислением труб и
крепежных деталей пароперегревателей, когда температура металла превышает 610 —
620°С. Этот тип коррозии определяется участием оксидов ванадия и называется
ванадиевой коррозией и проявляется при сжигании мазутов,
которых содержит оксид V2O4.
В процессе горения углеводородов V2O4
окисляется до V2O5 и образуются ванадаты 5V2О5·Na2O·V2O4
и пиросульфаты натрия Na2S2O7, имеющие
температуру плавления около 600°С. На поверхности труб или крепежных деталей
при tст > 610°С возникает жидкая пленка, обладающая высокой
окислительной способностью по отношению к сталям разного типа (углеродистой,
легированной, аустенитной).
Радикальным средством предупреждения коррозии могла бы
быть очистка сжигаемого мазута от примесей ванадия и натрия, но это довольно
дорого и требует строительства специальных заводов. Поэтому кардинальным
решением этой проблемы для паровых котлов, сжигающих мазут, явилось снижение
температуры перегретого пара (основного и промежуточного перегревателей) до
545°С, хотя при этом снижается термодинамический КПД цикла перегретого пара.
При сжигании других видов топлив этот тип коррозии не имеет места.
8.3 Низкотемпературная коррозия
Коррозия возникает в нижней части поверхности
воздухоподогревателя, находящейся в области наиболее низких температур как
газов, так и рабочей среды (воздуха). По своему характеру — это сернокислотная
коррозия. Определяющим фактором интенсивной низкотемпературной коррозии
является наличие в потоке дымовых газов паров серной кислоты H2SO4.
Содержание SO3 в газах составляет 1-5%
количества SO2 или 0,002-0,10% полного объема газов.
В зоне температур газов ниже 500° С начинается
образование паров серной кислоты за счет реакции SO3 с водяными
парами, находящимися в газовом потоке. Этот процесс завершается при температуре
около 250°С.
Коррозия поверхности нагрева может начаться при
условии, если температура стенки и пристенного пограничного слоя окажется ниже
температуры конденсации паров влаги или паров серной кислоты, соответствующей
их парциальному давлению в газах.
Температура, при которой начинается конденсация влаги
на поверхности, называется термодинамической температурой росы tР.
Температура росы (точка росы) чистых водяных паров при
их парциальном давлении в продуктах сгорания pH2O = 0,01 — 0,015 МПа
составляет tтр = 45 — 54°С. При наличии в потоке газов паров серной
кислоты температура конденсации (сернокислотная точка росы tSР)
значительно увеличивается и может достигать 140-160 °С.
Коррозия металла происходит при наличии на его
поверхности пленки сконденсировавшейся влаги, содержащей H2SO4.
Скорость коррозии пропорциональна скорости конденсации паров серной кислоты. В
то же время интенсивность коррозии зависит от процентного содержания H2SO4
в конденсирующейся пленке на поверхности металла. При более низкой температуре
(ниже 110°С) в пленке растет масса влаги и снижается доля серной кислоты.
Для исключения низкотемпературной коррозии необходимо
иметь tст < tSР + (10 — 15)°С, однако, это
экономически оправдано лишь при сжигании малосернистых мазутов и сернистых
твердых топлив, у которых tSР не превышает 110 °С. В
других случаях при высоком значении tСТ температура уходящих газов
будет чрезмерно велика, заметно возрастут потери с уходящими газами.
При значении tSР > 130 °С
допускается в поверхности воздухоподогревателя невысокая скорость коррозии (не
более 0,2 мм/год), что обеспечивается за счет предварительного подогрева
воздуха на входе в воздухоподогреватель.
9 Лекция 9. Аварии и повреждения паровых котлов
Содержание лекции: понятие аварии и отказа, причины аварий и отказов. Обнаружение и
устранение повреждений паровых котлов. Основные аварии и повреждения котлов [1,
8, 9, 10, 11, 12].
Цель лекции: знакомство
с видами повреждений их причинами и возможными путями их устранения.
9.1 Аварии и неполадки паровых котлов
При эксплуатации паровых котлов возможны
нарушения – устранимые и неустранимые, для ликвидации которых соответственно
требуется или не требуется останавливать оборудование. В зависимости от характера
неполадок, их последствий и степени повреждения оборудования различают отказы,
аварии и внезапные (незапланированные) отключения потребителя.
Нарушение работоспособности оборудования
электростанции называют отказом. Внезапное возникновение режима работы,
создающего условия, опасные для обслуживающего персонала, либо приводящего к
полному или частичному разрушению оборудования, называют аварией.
При возникновении аварийных ситуаций
необходимы быстрые, решительные действия, порядок выполнения которых строго
регламентирован. Большое значение имеют противоаварийные тренировки, во время которых
отрабатываются практические навыки работы с оборудованием в аварийных
ситуациях.
Аварии и отказы в работе происходят в
результате поломок оборудования, вызванных физическими и химическими
процессами, а также неправильных действий обслуживающего персонала
электростанции, низкого качества изготовления оборудования, его монтажа или
ремонта.
Воздействие физико-химических процессов на
оборудование может быть своевременно зарегистрировано персоналом с помощью
средств контроля.
В котельных цехах аварийные остановы
вызываются разрывами труб поверхностей нагрева, а также трубопроводов пара и
воды; пожарами, хлопками взрывами в топке, газоходах, системах топливоподачи и
пылеприготовления; повреждениями арматуры; разрушением обмуровки и элементов
каркаса; шлакованием топочных экранов и поверхностей нагрева; выходом из строя
отдельных видов оборудования, вызывающим останов котла. Кроме того, причиной
останова может быть повреждение или неисправность контрольно-измерительных
приборов, системы управления, автоматики и защиты.
9.2 Обнаружение и
устранение аварий и неполадок в паровых котлах
Разрывы труб поверхностей нагрева являются основной причиной аварийных
остановов и отказов котлов. Наиболее серьезные последствия с обязательным
остановом котла наблюдаются при разрывах экранных труб. При появлении свищей и
трещин в экономайзерах и пароперегревателях иногда допускается работа котла в
течение некоторого времени, однако при этом усиливают контроль, особенно
дефектных участков, и, как только предоставляется возможность, котел
останавливают, чтобы избежать более серьезных повреждений. Разрывы экранных
труб в барабанных котлах сопровождаются сильным шумом в топочной камере и
газоходах, понижением уровня воды в барабане (несмотря на усиленное питание),
ростом давления в топке и выбиванием из нее газов, снижением давления в
барабане и др. При разрывах в других поверхностях нагрева вследствие меньших
диаметров труб эти же признаки проявляются в меньшей степени: разрыв труб
пароперегревателей не сказывается на изменении уровня воды.
Основными причинами разрывов труб
поверхностей нагрева являются:
превышение давления; нарушение температурных условий работы;
коррозионно-эрозионные процессы, происходящие на наружной и внутренней
поверхностях труб; неудовлетворительный водный режим котла; усталостные
разрушения и повышенные напряжения (например, при защемлениях труб); низкое
качество изготовления труб и применение несоответствующего материала;
некачественные монтаж и ремонт (особенно плохая сварка); недостаточный
технический надзор за состоянием труб.
Во избежание чрезмерного повышения давления
на паропроводах свежего и вторично перегретого пара устанавливают
предохранительные клапаны, исправность которых регулярно контролируют. Пуск
котла при неисправных предохранительных клапанах запрещается. Нарушения
температурных условий работы труб наблюдаются при повышении температуры сверх
допустимых пределов или резких ее колебаниях, вызывающих появление усталостных
трещин. Сопротивление металла действующим нагрузкам уменьшается при повышении
температуры, которое может быть вызвано недостаточным расходом пара или воды
через трубу, ростом температуры газа и тепловых потоков образованием
значительных внутренних отложений из-за неустойчивой циркуляции среды по
трубам.
Недостаточный расход охлаждающей среды может возникнуть из-за
невнимательности машиниста, упуска воды из барабана, появления разрывов в
трубах, неустойчивости или нарушения циркуляции, неисправности
контрольно-измерительных приборов, связанных с питанием котла. Причиной
повышения температуры газов может быть чрезмерный расход топлива, неудовлетворительный
топочный режим, вызывающий общее затягивание горения, или неравномерность
(«перекосы» температур) газов по сечению топки и газоходов (неправильная
загрузка горелок).
Внутренние отложения появляются при неудовлетворительных водном режиме и
химподготовке воды, интенсивном протекании коррозионных процессов,
недостаточной очистке пара. Увеличение содержания солей в котлах вызывается
забросом влаги из барабана при повышении уровня воды сверх допустимого. Кроме
точного соблюдения режима эксплуатации и топочного процесса, а также
постоянного контроля показаний приборов для сокращения аварий из-за разрыва
труб персоналу станции следует регулярно проводить водяные и кислотные промывки
внутренних поверхностей труб.
Коррозионные процессы протекают как с внутренней стороны труб, так и со
стороны движения газа. Внутренняя коррозия определяется наличием в воде или
паре коррозионно-активных соединений (кислорода, водорода, углекислого газа,
нитратов, нитритов и др.). Коррозия может протекать как при работающем, так и
остановленном котле (стояночная коррозия). При работе оборудования в
большинстве случаев внутренняя коррозия происходит из-за неудовлетворительной
деаэрации питательной воды и низкого качества внутрикотловой обработки воды.
Стояночную коррозию, вызванную
проникновением атмосферного воздуха в трубы при остановах оборудования,
устраняют при консервации котлов, которую выполняют в соответствии с
«Руководящими указаниями по консервации теплоэнергетического оборудования».
Наружная коррозия труб в высокотемпературных котлах наиболее сильно проявляется
при сжигании мазута и твердых топлив с повышенным содержанием серы (ванадиевая,
сульфидная коррозия) и в поверхностях нагрева в зоне низких температур газов
(низкотемпературная сернистая коррозия).
Водный режим котла в значительной степени определяет коррозионные
процессы и образование внутренних отложений. Для снижения аварийности в
соответствии с требованиями «Правил технической эксплуатации» следует:
поддерживать общее солесодержание питательной воды и содержание соединений
железа, меди, кремния, кислорода не выше допустимых пределов; правильно
дозировать обрабатывающие материалы (гидразин, аммиак, фосфат и др.);
выдерживать требуемый расход воды непрерывной продувки и своевременно выполнять
периодическую продувку; проводить предпусковые промывки котлов. Повышенные
напряжения и усталостные разрушения могут быть вызваны неправильным
проектированием оборудования, а также заклиниванием (защемлением) труб, резкими
сменами температур. При пусках, остановах и эксплуатации оборудования
контролируют удлинение трубопроводов и состояние поверхности труб, выявляют
поврежденные участки и своевременно заменяют их.
Аварии и отказы из-за низкого качества
изготовления, монтажа и ремонта
вызываются: браком металла; отсутствием входного контроля; браком заводских,
монтажных или ремонтных сварных стыков; применением несоответствующих
материалов; нарушениями технологии и объема работ.
При разрыве труб пароводяного тракта, появлении трещин, выпучин, пропусков в сварных
стыках и соединениях основных элементов (барабане, коллекторе, перепускных
трубах и др.) котел следует немедленно остановить. В прямоточных котлах при
резком снижении давления в тракте до встроенной задвижки может произойти
вскипание воды, что приводит к неравномерной раздаче пароводяной смеси по
отдельным трубам, вызывает пульсацию давлений и расхода в них, увеличение
температуры. Поэтому при недопустимом превышении или понижении давления до
встроенной задвижки котел должен быть остановлен.
Хлопки и взрывы в топках и газоходах происходят из-за скопления значительных
количеств непрореагировавшего топлива при не налаженном топочном режиме, обрыве
факела и повторном зажигании его без вентиляции, и особенно при подаче угольной
пыли в ненагретую топку. Хлопки и взрывы могут происходить также при обрушении
значительных глыб шлака в водяную ванну шлакового комода. При сжигании
газообразного топлива взрывы (часто с тяжелыми последствиями) наблюдаются во
время растопки котла с не провентилированной топкой при утечке в нее газа, а также
зажигании факела (после обрыва) без предварительной вентиляции топки и
газоходов. Пожары и взрывы при сжигании жидкого топлива происходят вследствие
плохого его распыла и неналаженного топочного процесса. При взрыве в топке или
газоходах, особенно, в случае разрушения обмуровки, каркаса или других
элементов, котел следует немедленно остановить. Котел должен быть также
остановлен в ситуациях, которые могут вызвать взрыв с серьезными последствиями.
Такими аварийными ситуациями являются погасание факела и недопустимое понижение
давления за регулирующими клапанами газа или мазута. Аварии с хлопками и взрывами
большей частью происходят по вине обслуживающего персонала, нарушающего
пусковые и эксплуатационные инструкции, в частности указания о вентиляции котла
перед пуском.
Пожары в газоходах возникают вследствие неудовлетворительного ведения
топочного процесса, когда продукты неполного сгорания (несгоревшее топливо,
сажа, смолистые вещества) оседают и скапливаются на поверхностях нагрева
экономайзеров и воздухоподогревателей. Возгорание этих отложений вызывает
серьезные повреждения поверхностей нагрева и газоходов. Признаками загораний
являются несвойственное для данной зоны повышение температуры газов, ухудшение
тяги, выбивание пламени, разогрев обшивки. Обнаружив пожар, немедленно
прекращают подачу топлива, локализуют горение (отключением дутьевых
вентиляторов и дымососов и плотным закрытием газовых и воздушных шиберов) и
включают местное пожаротушение.
Шлакование топок и поверхностей нагрева также снижает надежность
работы и создает аварийные ситуации. Кроме неравномерности обогрева труб и
нарушения циркуляции шлакование вызывает деформацию и повреждение отдельных
экранных труб и их подвесной системы, разрушение холодной воронки, шлаковых
шахт, устройств шлакоудаления и обмуровки (при падении глыб шлака), повышает
температуру в топке и увеличивает тепловые потоки на незашлакованные участки
труб. Шлакование экранов и поверхностей нагрева значительно ограничивает мощность
котла и увеличивает затраты на тягу. При сильном шлаковании топки, когда
наблюдаются перекрытие шлаком ее нижней части и прекращение его выхода с
накоплением в топке, производят аварийный останов котла.
10 Лекция 10.
Основы эксплуатации паротурбинных установок
Содержание лекции: основные принципы эксплуатации паровых турбин. Безотказность и
ремонтопригодность. Классификация режимов работы турбоустановок. Стационарные и
переходные режимы. Режимы работы теплофикационных установок [1, 14, 15, 16].
Цель лекции: знакомство
с основными принципами эксплуатации паровых турбин и режимами работы турбин.
10.1 Обеспечение
надежности и экономичности — основные
принципы эксплуатации
К паровым турбинам в
процессе эксплуатации
предъявляются два основных связанных между собой требования:
надежность и экономичность. Под надежностью ПТУ понимают ее способность к выработке
предусмотренных мощности и тепла при заданных условиях и режимах эксплуатации.
Надежность ПТУ как сложной системы определяется прежде всего надежностью ее
оборудования: турбины, теплофикационной и конденсационной установок,
питательных и
конденсационных насосов, деаэраторов, подогревателей и т.д. Чем выше
надежность элементов ПТУ, тем выше ее надежность в целом.
Событие,
заключающееся в нарушении работоспособности ПТУ, называется отказом. Отказ,
после возникновения которого ПТУ становится полностью неработоспособной,
называется полным. Если же отказ приводит только к частичной потере
работоспособности, то такой отказ называется частичным.
Свойство ПТУ или
турбины непрерывно сохранять работоспособность называется безотказностью. Безотказность
не может быть абсолютной.
Количественной мерой безотказности в работе является наработка на
отказ — средняя суммарная (без учета перерывов) продолжительность работы между отказами.
Мощные
турбины при соблюдении правил технической эксплуатации должны иметь наработку
на отказ не менее
6250 ч.
Свойство ПТУ или
турбины, заключающееся в приспособленности к предупреждению и обнаружению
причин возникновения их отказов, предупреждений и устранению их последствий
путем
проведения
ремонтов и технического обслуживания, называется ремонтопригодностью.
Чем проще вскрытие
турбины, совершеннее диагностика повреждений и их ликвидация, тем выше ее
ремонтопригодность.
Процесс обнаружения
и устранения отказа (повреждения) ПТУ или турбины с целью восстановления работоспособности
(исправности) называется
восстановлением, а время этого процесса —
временем
восстановления.
Для поддержания
высокой надежности оборудование проходит техническое обслуживание, текущий, средний или
капитальный ремонты. При текущем или среднем ремонтах заменяются или
восстанавливаются поврежденные детали и узлы, контролируются исправность
и техническое состояние других узлов, предусмотренные нормативно-технической документацией.
При капитальном ремонте проводится почти полное восстановление работоспособности и ресурса
оборудования с заменой, если требуется, любых его частей. Время между
капитальными ремонтами называется межремонтным периодом. Межремонтный период составляет
не менее 5 лет.
Для комплексной
оценки надежности используют коэффициент готовности — отношение наработки на
отказ к сумме времен наработки на отказ и восстановление. У освоенных турбин
коэффициент
готовности равен 98-99 %, а у осваиваемых может составить 60-65 %. Коэффициент готовности современных
турбин должен быть не ниже 98 %.
В число показателей
надежности входят также
безопасность и долговечность. Под безопасностью понимают
свойство не допускать ситуаций, опасных для обслуживающего персонала и окружающей среды. Под долговечностью
оборудования
понимают его свойство сохранять работоспособность в течение определенной
предельной наработки (ресурс) или календарного времени (срок службы). Срок
службы турбины 40 лет.
Следует подчеркнуть,
что требования надежности и экономичности тесно связаны. Ненадежная установка
не может быть экономичной.
Задача эксплуатации как раз и
состоит в том, чтобы обеспечить
наивысшую экономичность при высокой надежности. Грамотная
эксплуатация оборудования, основанная на четком понимании тепловых и механических процессов,
протекающих в турбине, на понимании связи турбоагрегата с другим оборудованием, играет
исключительно важную роль в обеспечении надежности и экономичности.
10.2 Классификация
режимов работы паровых турбин
Прежде всего, по
тепловому состоянию турбины режимы
работы можно разделить на стационарные и переходные.
Для теплофикационных
турбин, обеспечивающих выработку электрической и тепловой энергии,
характерно очень
большое число возможных режимов работы. Оно настолько велико, что их классификация весьма
затруднительна и потому условна.
10.2.1 Классификация
по тепловому состоянию турбины
Стационарный режим
— это режим, при котором параметры пара
внутри турбины (температура,
давление, влажность, скорости пара) и состояние ее
деталей (температура,
деформация) не изменяются
во времени. Строго говоря, стационарных режимов
не существует,
поскольку всегда имеются некоторые пульсации параметров. Однако, при стационарных режимах их
уровень мал на фоне средних значений, а сами средние значения остаются неизменными во времени.
Переходный,
или нестационарный
режим работы — это процесс перехода от одного стационарного режима к
другому. Поскольку параметры пара
и температурное состояние деталей на
различных стационарных режимах разные, то в процессе переходного периода
параметры пара и температурное
состояние деталей изменяются, что приводит к ряду
новых явлений, в том
числе к появлению температурных напряжений и расширений, которые могут привести
к аварийной ситуации.
Стационарные режимы паровых турбин
можно разделить на две большие группы: ординарные и специфические.
Ординарные
стационарные режимы — это режимы нормальной эксплуатации турбины.
Ординарные режимы в
свою очередь можно разделить на три вида:
а) режим номинальной
нагрузки;
б) режим частичной
нагрузки;
в) режим максимальной
нагрузки.
Специфические
стационарные режимы — это режимы, при которых условия работы турбины таковы,
что необходимы ограничения их длительности, изменения состава работающего
оборудования и т.д. Условно к ним можно отнести:
режимы с отклонениями частоты вращения,
начальных, конечных и промежуточных
параметров пара; режимы холостого хода; режимы с отключенными регенеративными подогревателями; беспаровые и малорасходные режимы; моторный режим.
Малорасходные режимы
— это
режимы с малым
расходом пара через турбину, ее отдельные цилиндры или отсеки. К ним
относятся беспаровой режим,
холостой ход, режим нагрузки собственных нужд, моторный
режим.
Беспаровым режимом
называется режим
работы при отсутствии расхода пара через цилиндр. Он возникает,
например, в ЦНД при полном закрытии регулирующей диафрагмы.
Холостым ходом
называется работа турбины при номинальной частоте вращения с мощностью на зажимах
генератора, равной нулю.
Режим нагрузки
собственных нужд реализуется при расходе пара, обеспечивающем мощность,
достаточную для электроснабжения всего оборудования энергоблока и
общестанционного оборудования, необходимого для работы энергоблока; электрическая
энергия в сеть при этом режиме не отпускается.
Моторный режим — это режим,
при котором
вращение ротора турбины осуществляется генератором при номинальной частоте вращения.
В моторном
режиме пар в переднюю часть турбины не подается, в конденсаторе турбины
поддерживается давление, близкое к номинальному, а охлаждение проточной части,
нагревающейся за счет трения, осуществляется паром сниженной температуры от
постороннего
источника, подаваемым в ресивер
ЦНД или в один из отборов ЦСД.
Переходные, или нестационарные
режимы можно
условно разделить на три вида: изменения нагрузки, пуски и остановки.
В свою очередь, изменения
нагрузки можно разделить на две категории: автоматические и плановые.
Пуском турбоагрегата
называется
процесс его
подготовки к развороту, толчка ротора и разворота
до синхронной частоты
вращения, синхронизации и
нагружения до требуемой мощности.
Пуски турбин
различаются либо по времени простоя, либо по температуре металла перед пуском. Чаще всего пуск
после нескольких часов простоя называют пуском из горячего резерва, после
ночного простоя —
пуском из горячего состояния,
после простоя в воскресенье или в субботу и воскресенье
— пуском из неостывшего состояния, при
большей длительности простоя — пуском из
холодного
состояния.
Остановкой
турбоагрегата называется процесс его разгружения с прекращением подачи пара
в турбину,
отключения генератора от сети и выбега вплоть до момента включения
валоповоротного устройства.
Различают три вида остановок: в резерв, с
расхолаживанием и аварийные.
Остановку в резерв
ведут с учетом последующего пуска через относительно короткое время (после
ночного простоя или
после простоя в субботу и воскресенье). Поэтому ее ведут так, чтобы по возможности сохранить
температуру оборудования, что облегчает последующий пуск.
Наоборот, остановку с
расхолаживанием используют при последующем выводе оборудования в ремонт, для
начала которого необходимо ее охлаждение до достаточно низкой температуры.
Аварийная остановка
осуществляется при возникновении аварийных ситуаций, угрожающих аварией в настоящее
время или в будущем, или при
авариях.
При остановках турбины возникают такие же явления, как и при
пуске, однако проявляются они более
специфично и часто более опасно, чем при
пусках.
10.2.2 Классификация
по составу работающего оборудования
Режимы работы теплофикационной турбоустановки можно разделить на две большие группы: конденсационные и теплофикационные.
Конденсационные
режимы —
это режимы, при которых нет тепловой нагрузки (промышленные и теплофикационные
отборы отключены). Пар, поступающий на турбину, проходит всю ее проточную
часть (часть пара,
естественно, уходит в систему регенерации) и поступает в конденсатор. Иными словами, эти режимы
работы ничем не отличаются от режимов работы конденсационной турбины. В таких
режимах
теплофикационная турбина работает летом, когда небольшая тепловая нагрузка (чаще
всего,
горячее
водоснабжение) обеспечивается одним или
несколькими турбоагрегатами ТЭЦ, а остальные
работают в конденсационном режиме.
Теплофикационные режимы — это режимы, при которых через отборы турбины осуществляется отпуск тепла для целей промышленного потребления или нагрева сетевой воды. В свою очередь, теплофикационные режимы можно разделить на две подгруппы: режимы работы по тепловому графику
и режимы работы по электрическому графику.
При работе по
тепловому графику теплофикационная турбина работает как турбина с противодавлением:
она обеспечивает выработку тепла в заданном количестве и с заданными
параметрами теплоносителя, попутно вырабатывая количество электроэнергии,
определяемое расходом и параметрами
свежего и отработавшего пара.
Режим работы по
тепловому графику
часто называют просто «теплофикационным режимом», «режимом работы с
противодавлением» или «режимом работы с закрытой диафрагмой» (имеется в виду
регулирующая диафрагма ЧНД).
При режимах работы
по теплофикационному
графику в работе находится и конденсатор турбины, в
трубную систему которого (в основной и встроенные пучки) поступает охлаждающая
вода (циркуляционная,
сетевая, подпиточная и т.д.). Работа конденсатора
обеспечивает конденсацию небольшого количества
пара, поступившего в ЧНД через неплотности
регулирующих органов (диафрагмы).
Теплофикационный
режим, особенно при нагреве сетевой или подпиточной воды во встроенном
пучке конденсатора,
является самым экономичным режимом главным образом из-за малых потерь тепла
конденсации в конденсаторе (или их отсутствия вообще).
Режимы работы по
электрическому графику —
это режимы, при которых тепловая и электрическая
нагрузки регулируются
независимо (правильнее поэтому сказать, что это режимы работы по двум графикам —
электрическому и тепловому). При этом
режиме в конденсатор поступает охлаждающая
вода и через турбину протекает два потока пара: теплофикационный и
конденсационный. Экономичность работы по электрическому графику зависит от
соотношения расходов этих потоков: чем
больше доля теплофикационного потока, тем
более
экономичной
будет работа турбоустановки.
11 Лекция 11. Система регулирования и защиты паровой
турбины (часть 1)
Содержание лекции: регулирование частоты вращения ротора турбоагрегата. Принципиальная
схема регулирования частоты вращения. Статическая характеристика системы
регулирования. Степень неравномерности и степень нечувствительности.
Статическое и астатическое регулирование
[14, 17, 18].
Цель лекции:
знакомство с основными принципами работы САР паровых турбин.
11.1 Регулирование частоты вращения валопровода
турбоагрегата
Качество электроэнергии определяется частотой и
напряжением переменного тока. Номинальное значение частоты сети энергосистем в
Казахстане равно 50 Гц, поддержание которой при любых нагрузках составляет
основную задачу регулирования турбоустановок ТЭС. Для этого, все турбоагрегаты
снабжены системами автоматического регулирования (САР).
На рисунке 8 представлены кривые изменения
крутящего момента Мт (турбины), и момента сопротивления Мг
на валу электрогенератора. При изменении нагрузки электрической сети
характеристика электрогенератора сместится (например, в положение, определяемое
линией 3 на рисунке 8).
Если положение регулирующих клапанов не изменится, то
установится новый режим работы в точке b
с другой частотой вращения nb. Таким образом, турбина и генератор
могут переходить из одного устойчивого режима работы в другой без какого-либо
воздействия на них. Этот процесс называют саморегулированием и он определяется
тем, что в точке пересечения моментных характеристик
DМТ/Dn < 0, а
DМГ/Dn > 0. Для того, чтобы частота вращения оставалась в
допустимом диапазоне ее изменения (например, со значением nс),
следует сместить характеристику турбины в положение 4 изменением расхода пара.
Все установившиеся режимы
работы турбоагрегата при совместном изменении характеристик турбины и
генератора в итоге определяются линией 5, которую называют статической характеристикой турбоагрегата.
Допуская некоторое малое
отклонение частоты вращения от номинального значения, это отклонение можно
использовать в качестве командного импульса для системы автоматического
управления турбиной. При этом речь в итоге идет о воздействии на крутящий
момент, формируемом водяным паром в рабочих решетках турбинных ступеней. Это
воздействие определяется изменением расхода пара в турбину посредством его
дросселирования в регулирующих клапанах системы парораспределения.
11.2 Принципиальная
схема регулирования частоты вращения
Схема регулирования
частоты вращения ротора турбины показана на рисунке 9, в которой основными
элементами являются: регулятор скорости, отсечной золотник, сервомотор,
регулирующий клапан турбины.
С ростом частоты
вращения ротора турбины под действием центробежных сил грузы регулятора
скорости перемещают его муфту (сжимая пружину в ней), в результате чего рычаг АВ поворачивается вокруг точки В.
Тогда поршни золотника 2 смещаются вверх, в результате чего верхняя полость
сервомотора 3 соединяется с линией 4 (в этом случае напорной), а нижняя — с
линией 5 (сливной).
Поршень сервомотора перемещается вниз
и через передаточные механизмы формируется усилие на закрытие регулирующего
клапана 6. В итоге
расход пара в турбину сокращается и уменьшается крутящий момент на валу
турбины, что приводит к смещению моментной характеристики MТ в
положение, обеспечивающее исходное значение частоты вращения ротора.
Одновременно с помощью
обратной связи (правый конец рычага АВ связан со штоком сервомотора) отсечной золотник
возвращается в исходное среднее положение, что стабилизирует переходный процесс
и обеспечивает устойчивость регулирования.
11.3 Характеристики
системы регулирования
Совокупность
установившихся режимов работы турбины и положений органов ее САР представляется
развернутой статической характеристикой (рисунок 10, а). Здесь зависимость
перемещения муфты регулятора скорости от частоты вращения x = f(n) в квадранте II
представленной диаграммы является статической характеристикой регулятора
частоты, характер которой определяется его конструкцией. Зависимость хода
поршня сервомотора от перемещения муфты регулятора является прямолинейной (z = f(x)
в III квадранте). В IV квадранте дана зависимость электрической мощности от
хода сервомотора NЭ = f(z). В итоге простых построений в I
квадранте получается собственно статическая характеристика регулирования n = f(NЭ),
связывающая частоту вращения с мощностью турбоагрегата. Из нее следует, что при
изменении мощности турбины частота вращения не остается постоянной, например,
несколько снижается с ростом мощности. Наклон статической характеристики
определяется степенью неравномерности регулирования частоты
где nxx — частота вращения при
холостом ходе, nнн — то же при номинальной мощности, n0 –
то же номинальная.
| | |
а) | б) |
Рисунок 10 — Развернутая (а) и
реальная (б) статические характеристики САР турбоагрегата
При номинальных значениях
параметров водяного пара в турбине степень неравномерности не должна превышать
δ = 4…5%.
Наличие сил трения в
механических элементах системы автоматического регулирования, люфтов в ее
передаточных механизмах и других приводит к нечувствительности регулирования
(рисунок 10, б), которая характеризуется степенью нечувствительности по
частоте вращения: εn = Dn/n0. Этой величиной определяется
совершенство САР. Для паровых турбин мощностью свыше 150 МВт с гидравлическими
системами регулирования степень нечувствительности не должна превышать 0,1 %, а
в электрогидравлической системе с регулятором мощности – εn < 0,06%.
Частота электрического
тока в энергосистеме в соответствии с ПТЭ (правилами технической эксплуатации
энергетического оборудования) должна поддерживаться на уровне
50 ± 0,1 Гц. Временно допускается отклонение частоты не более
± 0,2 Гц. В то же время степень неравномерности
δ = 4 — 5% соответствует изменение частоты
2 — 2,5 Гц, т.е. на порядок больше допустимого уровня. Поэтому в
САР должен быть механизм управления частотой вращения при работе турбины в
энергосистеме, когда частота в ней поддерживается всеми параллельно работающими
турбоагрегатами. Этот механизм называют МУТ — механизмом управления турбиной
(ранее МУТ называли синхронизатором). С его помощью изменяется положение
какого-либо звена системы передачи импульса на перемещение от регулятора
скорости к регулирующим клапанам (буксы золотника регулятора частоты вращения).
11.3. Статическое и
астатическое регулирование
Представленная на
рисунке 9 схема позволяет осуществлять статическое регулирование, при котором в
изолированной сети любое изменение нагрузки потребителей электроэнергии
приводит к отклонению частоты вращения ротора турбины в пределах, определяемых
степенью неравномерности δ. Но изменение частоты можно свести к нулю при
смещении статической характеристики n = f(NЭ), воздействуя на МУТ (рисунок 11).
Механизм, который осуществляет эту
операцию автоматически, называют изодромным устройством (изодромом). В схемах
изодромного (астатического) регулирования после завершения переходного процесса
при изменении нагрузки частота вращения восстанавливается к исходному значению.
Схема изодромного регулирования показана на рисунке 12, в которой правый конец
рычага АВ связан со штоком сервомотора не непосредственно, а через катаракт 4. Катаракт представляет собой
цилиндр с поршнем, полости которого соединяются через дроссельное устройство.
Допустим, что при работе
турбины в изолированной сети сократилась нагрузка потребителей электроэнергии.
Это приведет к росту частоты вращения ее ротора с n1 до n2
(рисунок 12).
На начальном этапе переходного процесса система
регулирования с изодромом (при большом сопротивлении его дроссельного
устройства) действует как обычная САР с жесткой обратной связью и со степенью
неравномерности δд, которую называют временной или
динамической. На втором этапе переходного процесса изодром дополнительным
прикрытием главного сервомотора постепенно снижает частоту вращения от n2 до n1 при постепенном
смещении статической характеристики вниз (рисунок 12). В точке 3 статическая
характеристика пересекает линию n1 = const при NЭ2.
12 Лекция 12. Система
регулирования и защиты паровой
турбины (часть 2)
Содержание лекции: электрическая часть САР (ЭЧСР) и гидравлическая часть (ГЧСР). ГЧСР конденсационной турбины. Регулирование турбин с
противодавлением и отбором пара. Защита турбины от разгона. Виды защит паровой
турбины [14, 17, 18].
Цель лекции:
знакомство с основными схемами САР паровых турбин и основными защитами.
Системы автоматического
регулирования современных паровых турбин в большинстве своем являются
электрогидравлическими, а для турбоагрегатов на сверхкритические параметры
водяного пара унифицированными по датчикам регулируемых величин, усилителям и
маслонапорным станциям. Электрическая и гидравлическая части системы
взаимодействуют друг с другом. Так регулирующие воздействия из электрической
части САР (ЭЧСР) передаются в ее гидравлическую часть (ГЧСР) через два входа: быстродействующий
(электрогидравлический преобразователь — ЭГДП) и медленнодействующий (механизм
управления турбиной — МУТ). Использование ЭЧСР позволило улучшить статические и
динамические характеристики турбоагрегата, повысить его приемистость и надежность
противоразгонной защиты. Быстрота передачи импульса в электрической части
системы, простота реализация любого закона регулирования, компактность и
экономичность — основные преимущества ЭЧСР. Именно в ней формируются основные
управляющие сигналы по регулированию частоты вращения валопровода турбоагрегата
и его мощности, которые в итоге приводят к воздействию на регулирующие клапаны
паровой турбины. Вместе с тем, в гидравлической части системы сохранены
механические датчики частоты вращения, обеспечивающие работу турбоагрегата в
условиях временного отключения ЭСЧР.
В качестве примера,
представлена схема ГЧСР (рисунок 13) конденсационной турбины.
Быстродействующий ввод
воздействий от ЭЧСР в ГЧСР осуществляется через ЭГП 4, состоящего из электромеханического
преобразователя (ЭМП) магнитоэлектрического типа и гидроусилителя.
Соответствующий сигнал из ЭЧСР через ЭМП вызывает соответствующее смещение
промежуточного золотника. В нормальных эксплуатационных режимах сигнал на
выходе ЭГП близок к нулю. В ЭЧСР имеется и регулятор мощности турбины (РМТ),
воздействующий на ГЧСР через двигатель МУТ таким образом, чтобы обеспечивать
регулирование мощности с коррекцией по частоте сети и давлению свежего пара
(рисунок 13).
Рисунок 13 -Гидравлическая часть системы автоматического
регулирования конденсационной турбины: 1 — регулятор частоты вращения; 2 — блок золотников
регулятора частоты вращения; 3 — механизм управления турбиной; 4 —
электрогидравлический преобразователь; 5 — сервомотор регулирующего клапана
ЦВД; 6 — электромагнитный выключатель; 7 — золотник электромагнитного
выключателя; 8 — сервомотор регулирующих клапанов ЦСД; 9 — сервомотор сбросного
клапана; 10 — промежуточный золотник; 11 — медленнодействующий ограничитель
мощности
12.1 Системы регулирования теплофикационных турбин
Системы регулирования теплофикационных турбин поддерживают в заданных пределах два регулируемых
параметра: частоту вращения валопровода ТА и давление водяного пара в одном из
двух отопительных отборов. Поэтому в составе САР находятся два регулятора —
частоты вращения и давления, управляющих двумя главными сервомоторами систем
парораспределения ЧВД и ЧНД.
В теплофикационных турбинах применяются как
гидравлические, так и электрогидравлические несвязанные (статически) системы
регулирования (рисунок 14). В такой САР нет необходимости в использовании
сложного гидравлического блока регуляторов, в котором в связанной системе осуществляется
суммирование импульсов от регуляторов и формирование воздействий на
сервомоторы. В представленной схеме указаны следующие импульсы: n — по частоте вращения; f — по частоте сети; Nэ
— по электрической мощности; tпр — по температуре сетевой воды на
выходе из верхнего сетевого подогревателя; tн — по температуре
сетевой воды на выходе из нижнего сетевого подогревателя; tоб — по
температуре обратной сетевой воды; рот — по давлению водяного пара в
отборе турбины; рвс — по давлению воды за сетевыми насосами; tвп
— по температуре воды на выходе из встроенного пучка конденсатора; tк
— по температуре пара в конденсаторе; Зд — от задатчика.
Главные сервомоторы и весь контур регулирования
частоты вращения здесь выполнены гидравлическими, что обеспечивает выполнение
высоких требований по быстродействию и надежности. Процессы регулирования
мощности, тепловой нагрузки отборов пара и температуры подпиточной воды на
выходе из встроенного пучка конденсатора протекают сравнительно медленно, что
дает возможность применения электронных регуляторов. Соединение регуляторов с
их исполнительными механиз-мами, например МЭО (механизм электрический
однооборотный), и тем самым формирование контуров регулирования осуществляется
переключателем режимов 5.
Система регулирования паровой
турбины с противодавлением (рисунок 15) поддерживает в
заданных пределах один из двух регулируемых параметров — частоту вращения или
противодавление. Оба регулятора управляют одним главным сервомотором ЧВД. При
работе по тепловому графику (с противодавлением) турбоагрегатом управляет
регулятор давления, который формирует команды на поддержание расхода водяного пара в турбину,
определяемого тепловым потребителем. Например, при росте тепловой нагрузки
давление пара на выходе из турбины снижается, и регулятор давления дает команду
на открытие регулирующих клапанов. Регулятор частоты вращения обеспечивает
некоторое участие турбоагрегатов в
первичном регулировании частоты сети. Так, при
увеличении частоты сети регулятор формирует команду на прикрытие клапанов. При
этом уменьшается расход пара на выходе из нее и, соответственно его давление,
что приводит в действие регулятор давления, который дает команду на возврат
клапанов в прежнее положение. Таким образом, при работе по тепловому графику
функции регулятора давления являются ведущими. Регулятор частоты вращения
управляет САР при пуске турбоагрегата и осуществляет защитные функции при
сбросе нагрузки с отключением его от сети. В этом случае регулятор частоты дает
команду на закрытие клапанов, несмотря на противодействие регулятора давления.
12.2 Системы защиты турбоагрегатов
Наряду с режимами
нормальной эксплуатации энергоблоков могут возникать и аварийные режимы, в том
числе, связанные со сбросом нагрузки и отключением турбоагрегата от сети (из-за
коротких замыканий, отключений линий электропередачи, сильного отклонения
напряжения и частоты). На ТЭС при сбросе полной нагрузки с отключением
электрогенератора от сети основным требованием является условие, чтобы
максимальное повышение частоты вращения оставалось ниже уровня настройки
автоматов безопасности турбины. При этом необходимо очень большое
быстродействие системы регулирования, чтобы предотвратить увеличение частоты
вращения на 10…11% от номинального значения (nсз = (1,11 — 1,12)·n0).
Это обеспечивается быстрым закрытием автоматических стопорных клапанов (АСК) и
регулирующих клапанов, а также поворотных диафрагм и обратных клапанов на
линиях регулируемых и регенеративных отборов водяного пара из турбины. Сброс
водяного пара из котла в таких ситуациях осуществляется через БРОУ и
предохранительные клапаны. Система защиты является заключительной ступенью
управления турбоустановкой и срабатывает при недопустимом:
—
повышении частоты вращения
валопровода;
—
увеличении осевого сдвига ротора;
—
снижении давления масла в системе
маслоснабжения подшипников турбоагрегата;
—
повышении давления в конденсаторе;
—
росте уровня вибрации валопровода
турбоагрегата;
—
повышении температуры свежего пара
или при ее резком снижении;
—
повышении уровня конденсата в ПВД
регенеративной системы.
Все турбины оснащаются
двумя обязательными и независимыми линиями защиты, первой из которых является
сама система автоматического регулирования, а второй — собственно система
защиты турбоагрегата. Кроме представленных ранее, применяются и многие другие
виды защит, например:
—
от недопустимого относительного
удлинения ротора;
—
от недопустимой разности температур
по верху и низу корпуса цилиндра турбины;
—
при резком сбросе нагрузки до 30% и
до 50%;
—
при повышении давления свежего пара
до 1-го предела (включение БРОУ) и 2-го предела (открытие импульсных
предохранительных клапанов);
—
при повышении температуры вторичного
перегретого пара;
—
при понижении давления среды в
системе автоматического регулирования турбины.
13 Лекция 13. Масляная система турбины и эксплуатация
маслохозяйства
Содержание лекции: схемы маслоснабжения. Масло, его характеристики. Схемы маслоснабжения с
насосами объемного типа и центробежного. Схема маслоснабжения мощных паровых
турбин. Конструкции основных элементов системы маслоснабжения. Обслуживание
системы маслоснабжения [1, 16, 18].
Цель лекции: знакомство
со схемами и составом системы маслоснабжения турбин, а также принципами
обслуживания маслохозяйства.
13.1 Схемы маслоснабжения
Масло в турбоустановках применяется в качестве рабочей
среды в гидравлических системах регулирования, в подшипниках валопровода
турбоагрегата, в уплотнениях генератора и в гидромуфтах питательных
электронасосов. До 1980 года основным маслом для турбин ТЭС являлось турбинное
масло Тп-22. В настоящее время на ТЭС и АЭС поставляется в основном
дистиллятное масло Тп-22С селективной очистки (с уменьшенным содержанием
сернистых соединений). Такие масла легко воспламеняются при соприкосновении с
поверхностями, температура которых около 370 — 380°C. Поэтому нашли
широкое применение огнестойкие масла Иввиоль-3 и ОМТИ (нетоксичное). Их
температура самовоспламенения около 720°C. Плотность огнестойкого масла на 30% выше плотности нефтяного масла марки 22 и на 14% выше плотности воды. При этом
кинематическая вязкость данных масел приблизительно одинакова.
По уровню давления масляные системы делят на две
группы: низкого давления (для смазки и уплотнения генератора) и высокого
давления (для САР). В ряде турбин в их системах регулирования рабочей средой
является вода. При использовании ОМТИ система регулирования полностью
отделяется от системы смазки. Если в САР применяется масло, то в системе ее
маслоснабжения и смазки подшипников масляный бак, насосы и трубопроводы едины.
На рисунке 16, а представлена такая система с главным масляным
насосом объемного типа.
| | |
а) | б) |
Рисунок 16 — Схемы маслоснабжения турбины с насосом
объемного типа (а) и центробежным насосом (б): 1 – главный масляный насос (в схеме а –
зубчатый или винтовой с приводом через редуктор 2 от вала турбины, в схеме б –
насос центробежного типа с непосредственным приводом от вала турбины); 3 –
масляный бак; 4 – система регулирования турбоагрегатом; 5 – в схеме а –
редуктор, в схеме б – инжекторы 1-й и 2-й ступеней; 6, 7 – в схеме а –
предохранительные клапаны в напорной линии и линии смазки, в схеме б – 6, 7 –
обратные затворы главного насоса и на линии подачи масла к подшипникам; 8 –
маслоохладитель; 9 – вспомогательный масляный насос с турбоприводом; 10 –
обратный затвор; 11 – аварийный масляный насос с электроприводом; 12 –
электродвигатель постоянного тока; 13 – масло к подшипникам турбоагрегата
Зубчатый или винтовой насос 1 через редуктор 2 соединен с валом турбины и
подсасывает масло из бака 3. В установившемся режиме работы турбины расход
масла в САР 4 мал и редуктор 5 перепускает масло в систему обеспечения
подшипников 13. Во время переходных режимов редукционный клапан 5
прикрывается, и больший расход масла направляется для перемещения
поршней сервомоторов. Масло на подшипники в основном поступает из сливной линии
системы регулирования. Клапаны 6 и 7 являются предохранительными и
устанавливают необходимый уровень давления в напорной линии и в линии смазки.
Маслоохладители 8 поверхностного типа снижают температуру масла перед
подшипниками до 45 — 50°C. Для предотвращения обводнения масла его
давление в охладителях выше, чем давление охлаждающей воды. К подшипникам 13
масло подается через шайбы, дозирующие расход. При пусках и остановах турбины
масло к подшипникам подает турбонасос 9 через обратный затвор 10.
Вспомогательный насос 11 низкого давления с приводом от двигателя постоянного
тока 12 подает масло только в систему смазки в случаях отказа насосов 1 и 9.
Поскольку слабым элементом такой схемы является
редукторная передача 2 (нередко выходит
из строя), то в современных турбоагрегатах мощностью до 200 МВт
применяется схема маслоснабжения с главным насосом центробежного типа (рисунок
16, б), который соединяется непосредственно с валом турбины. Но при этом
требуется его полное заполнение маслом, для чего в маслобаке устанавливают
маслоструйный инжектор 2, который поддерживает перед главным насосом небольшое
избыточное давление.
Представленные схемы маслоснабжения установлены на
турбинах мощностью до 200 МВт включительно. Для турбин большой мощности в
целях повышения надежности устанавливают несколько насосов: главные с
двигателями переменного тока (два или три) и аварийные с двигателями
постоянного тока (два или три). Работают только часть главных насосов, а
остальные находятся в резерве. Кроме того, устанавливают вспомогательные насосы
с большим напором 9,8 — 11,8 МПа, обеспечивающим в режиме работы
валоповоротного устройства всплытие ротора в подшипниках. Для водяных систем
регулирования рабочей средой является вода (конденсат особо высокой очистки). В
этих системах трубопроводы и узлы регулирования выполняют из нержавеющей стали.
13.2 Конструкции основных элементов системы
маслоснабжения
Конструкция винтового масляного насоса ЛМЗ
представлена на рисунке 17, а пример насосной группы центробежного типа
ТМЗ показан на рисунке 18.
На рисунке 19 показана инжекторная группа для
системы маслоснабжения с главным масляным насосом центробежного типа. Инжектор
первой ступени служит для создания избыточного давления на всасе насоса, а
инжектор второй ступени — для подачи масла через маслоохладитель к подшипникам
турбины и генератора.
Для централизованной системы смазки предусмотрено
тройное резервирование, где первой ступенью являются резервные насосы с
приводом переменного тока, второй ступенью – насосы с приводом постоянного
тока, а третьей – аварийные емкости, из которых масло самотеком подается в
подшипники при выходе из строя предыдущих насосов. Обычно аварийные бачки
встраиваются в крышки подшипников.
Масляный бак (рисунок 20) предназначен не только для
хранения масла, но и для выделения из него воздуха, шлама, воды. Степень
очистки зависит от времени пребывания масла в баке. Кроме отстоя очистка масла
от примесей осуществляется с помощью сеток фильтра 4. В итоге формируются чистый 1 и грязный 2 отсеки.
На крышке маслобака располагают вспомогательные
насосы, указатели уровня и эксгаустеры (вытяжные вентиляторы), удаляющие
масляные пары. Такая вентиляция необходима, так как масло из системы уплотнения
электрического генератора с водородным охлаждением, несмотря на предшествующую
вакуумную обработку с целью удаления водорода, содержит некоторую его дозу.
Поэтому возможно образование взрывоопасной смеси
воздуха и водорода (гремучего газа). Масло из подшипников сливают в бак по
трубке на поверхность масла, а из узлов САР, где аэрация масла мала, сливают
под уровень.
Рисунок 20
— Конструкция масляного бака: 1 –
чистый отсек; 2 – грязный отсек; 3 – указатель уровня масла; 4 –
фильтрующие сетки
13.3 Обслуживание системы маслоснабжения
Масло подвергается тщательному и систематическому
контролю качества (цеховой – 1 раз в сутки и лабораторный 1 раз в 2 месяца).
Проверяются внешний вид масла, содержание шлама, определяется кислотное число,
реакция водной вытяжки, вязкость, температура вспышки, наличие воды. В
результате эксплуатации масло подвергается старению с потерей первоначальных
свойств. Поэтому периодически масло подвергается регенерации с использованием
физических и химических методов. Используются специальные адсорбенты для
удаления органических и низкомолекулярных кислот, смол и других примесей.
Для уверенной работы системы маслоснабжения должны
подвергаться регулярной проверке резервные и аварийные масляные насосы и
устройства их автоматического включения с частотой 2 раза в месяц. Кроме того,
их проверяют перед каждым пуском и остановкой турбины.
Качество работы маслоохладителей проверяется по
разности давлений на входе и выходе по маслу и охлаждающей воде и по нагреву
охлаждающей воды и охлаждению масла. Если при неизменном расходе охлаждающей
воды перепад давлений по маслу и температура масла на выходе из маслоохладителя
растут, то это говорит о засорении маслоохладителя и необходимости его чистки.
В этом случае обычно подключают резервный маслоохладитель, а загрязненный
направляют в чистку.
В каждой инструкции оговариваются минимальные
допустимые значения уровня масла в баке, максимально допустимые температуры на
выходе из маслоохладителя (обычно 40-45 °С) и из подшипников (обычно 60-65 °С).
При выходе значений одного из этих параметров за предельные, а тем более при
одновременном нарушении нескольких предельных значений положение на турбине
рассматривается как аварийное, и машинист турбины должен действовать в
соответствии с противоаварийной инструкцией.
14
Лекция 14. Эксплуатация конденсационной установки (часть 1)
Содержание лекции: назначение, принцип действия, схема и состав конденсационной установки.
Тепловой баланс конденсатора и переохлаждение конденсата. Нагрев
охлаждающей воды и кратность охлаждения. Компоновка трубной системы
конденсатора. Компоновки и конструкции конденсаторов паровых турбин. Тепловой
расчет конденсатора. Определение числа и длины конденсаторных трубок [1, 14,
16, 17, 18].
Цель лекции: знакомство
с принципом действия, схемами и составом конденсационной установки, а также
принципами теплового расчета конденсатора.
14.1 Назначение, принцип действия, схема и состав
конденсационной установки
Конденсатор – это теплообменник, предназначенный для
превращения отработавшего в проточной части паровой турбины водяного пара в
жидкое состояние – конденсат. Для обеспечения высокой экономичности цикла
необходимо выполнять конденсацию пара при низком давлении (pк << pа), что
дает рост термодинамического КПД турбоустановки. В конденсационных установках
холодному источнику (охлаждающей воде) отдается до 50% количества теплоты в
цикле, что в итоге определяет абсолютный КПД ПТУ на уровне 40–45 %. При
изменении давления в конденсаторе на 1 кПа экономичность паротурбинной
установки ТЭС изменяется примерно на 1%.
Под конденсационной установкой
(рисунок 21) понимают совокупность конденсатора 1 и следующих основных устройств:
2 – циркуляционных насосов; 3 – конденсатных насосов; 4 – эжекторной установки.
В зависимости от вида охлаждающей среды конденсаторы бывают водяные
(охлаждающая среда – вода) и воздушные (охлаждающая среда – воздух).
Современные паротурбинные установки большой мощности снабжены преимущественно
водяными конденсаторами.
Поскольку водяной пар, поступающий из выходного
патрубка ЦНД турбины, всегда содержит воздух, попадающий через неплотности
различных фланцевых соединений, концевые уплотнения ЦНД, арматуру, находящуюся
под разрежением, то необходимы специальные насосы 4 (эжекторы), постоянно отсасывающие
неконденсирующиеся газы. Сегодня используются пароструйные и водоструйные
эжекторы, в которых рабочей средой является, соответственно, водяной пар и
вода. Кроме того, существуют водокольцевые насосы для отсоса паровоздушной
среды из объема конденсатора. Подача охлаждающей воды в конденсатор
осуществляется циркуляционным насосом 2. Конденсатные насосы 3 служат для
подачи конденсата в систему регенеративного подогрева питательной воды.
Схема поверхностного конденсатора водяного типа
приведена на рисунке 22. Он состоит из корпуса 1, торцевые стенки которого закрыты трубными досками 4.
В досках завальцованы конденсаторные трубки 5, открытые своими концами в
водяных камерах. В зависимости от числа ходов охлаждающей воды (два, четыре)
водяные камеры разделяются перегородками, которые делят все конденсаторные
трубки на соответствующее число секций.
Рисунок 22 — Устройство двухходового конденсатора ПТУ
Для двухходового конденсатора охлаждающая вода через
входной патрубок 15 направляется к нижней
секции трубок, разворачивается в поворотной водяной камере 16 и далее
движется по трубкам верхней секции. Пар, поступающий из турбины через горловину
конденсатора 6 в паровое пространство, конденсируется на поверхности
конденсаторных трубок, внутри которых течет охлаждающая вода. За счет резкого
уменьшения удельного объема пара в конденсаторе создается низкое давление. Чем
ниже температура охлаждающей воды и больше ее расход, тем больше разрежение в
конденсаторе. Образующийся конденсат поступает в конденсатосборник 7. Удаление
воздуха (паровоздушной смеси) из конденсатора осуществляется через патрубок
отсоса в специально выделенном отсеке – воздухоохладителе 9.
14.2. Тепловой баланс конденсатора и переохлаждение
конденсата
Тепловой баланс поверхностного конденсатора
представлен следующим выражением:
Gк·(hк — h‘к) = Wm·(t2в — t1в)·cв,
где
hк — энтальпия пара, поступающего в конденсатор, кДж/кг;
h‘к = cв·tк — энтальпия конденсата;
cв = 4,19 кДж/(кг×К) – теплоемкость
воды;
Wm – массовый расход охлаждающей
воды, кг/с;
t1в,
t2в —
температура охлаждающей воды на входе в конденсатор и выходе из него.
Расход конденсируемого пара
Gк, кг/с и энтальпия
hк известны из расчета паровой турбины. Температура
конденсата на выходе из конденсатора принимается равной температуре насыщения
пара tп, соответствующей его
давлению pк с учетом переохлаждения конденсата
Dtк:
tк = tп — Dtк.
Переохлаждение конденсата
(разность между температурой насыщения пара при давлении в горловине
конденсатора и температурой конденсата во всасывающем патрубке конденсатного
насоса) является следствием понижения парциального давления и температуры
насыщенного пара из-за наличия воздуха и
парового сопротивления конденсатора. Переохлаждение может достигать
2-3 °С. В современных ПТУ переохлаждение допускается не более 1 °С.
Современные конденсаторы, обладающие минимальным паровым сопротивлением и
рациональной компоновкой трубного пучка, в номинальном режиме эксплуатации
турбоустановки практически не имеют переохлаждения. Но оно появляется при
изменении паровой нагрузки конденсатора, росте присосов воздуха, снижении
температуры охлаждающей воды (в зимнее время) и изменении ее расхода. Поэтому
для уменьшения переохлаждения конденсата в зимнее время следует сокращать
расход охлаждающей воды.
14.3. Нагрев охлаждающей воды и кратность охлаждения
Разность
Dtв = t2в — t1в
называют нагревом охлаждающей воды в конденсаторе. Для одноходовых
конденсаторов Dtв = 6-7°С, двухходовых –
Dtв = 7-9°С, четырехходовых –
Dtв = 10-12°С. Температура воды на входе
зависит от географического местонахождения ТЭС, системы водоснабжения (прямоточное,
оборотное), а также от времени года и климатических условий.
Одним из важнейших параметров конденсатора является
кратность охлаждения
Разность энтальпий для разных типов турбин
hк — h‘к ³ 2200 кДж/кг
и представляет в основном теплоту парообразования. Видно, что нагрев
Dtв обратно пропорционален кратности охлаждения. Чем
больше m, тем меньше
Dtв и тем
ниже может быть давление в конденсаторе. Однако при увеличении
m возрастает
расход охлаждающей воды и растут затраты электроэнергии на привод
циркуляционных насосов. Оптимальная кратность охлаждения принимается для
одноходовых конденсаторов m = 80…100, для двухходовых
m = 60…70,
трех – и четырехходовых m = 40…50.
14.4 Компоновка трубной системы конденсатора
При компоновке трубный пучок разбивают на две части:
основной пучок, в котором происходит массовая конденсация пара при практически
отсутствующем относительном содержании воздуха, и пучок воздухоохладителя, где
конденсация происходит с меньшей скоростью, а образующийся конденсат
переохлажден. В современных турбоустановках используется компоновка в виде
ленты, расположенный симметрично вертикальной оси, с глубокими проходами для
пара. К пучку воздухоохладителя смесь поступает только после прохождения
основного пучка. Кроме того, в трубки воздухоохладителя подается охлаждающая
вода из первого хода (с более низкой температурой). Ленточная компоновка
обеспечивает свободный доступ пара к зеркалу конденсата, что обеспечивает его
подогрев и снижение переохлаждения.
Для обеспечения глубокой деаэрации конденсата в ряде
конструкций конденсаторов используются конденсатосборники деаэрационного типа
(со струйной или с барботажной деаэрацией конденсата).
14.5 Компоновки и конструкции конденсаторов паровых
турбин
По отношению к оси паровой турбины конденсаторы могут
располагаться в продольном или поперечном направлениях. При поперечной
компоновке конденсаторные трубки направлены поперек продольной оси турбины.
Продольно расположенные конденсаторы могут выполняться одно, двух и трехсекционными.
Из-за различной начальной температуры охлаждающей воды, поступающей в отдельные
секции, давление в них будет различным. Такие конденсаторы называются
секционированными. В зависимости от числа потоков охлаждающей воды конденсаторы
выполняют однопоточными и двухпоточными. Различают также подвальное (нижнее)
расположение конденсаторов, боковое и осевое. В основном применяется подвальное
расположение.
14.6 Тепловой расчет конденсатора
Задачей теплового расчета конденсатора является
определение площади поверхности конденсаторных трубок, обеспечивающей
достижение заданного давления на выходе из паровой турбины. Площадь поверхности
охлаждения конденсатора Fк
определяется из формулы:
где
k – средний коэффициент теплопередачи поверхности
охлаждения, Вт/(м2·К);
Dtср —
средняя разность между температурами пара и охлаждающей воды, которая
вычисляется по формуле
где
Dtв = t2в — t1в –
нагрев охлаждающей воды в конденсаторе (Dtв = 6 — 7°С
– для одноходовых; Dtв = 7 — 9°С – для двухходовых и
Dtв = 10 — 12°С – для трех– и
четырехходовых конденсаторов);
δt = tп — t2в – недогрев (температурный напор) охлаждающей воды в
конденсаторе.
Недогрев зависит от паровой нагрузки конденсатора
dк = Gк/Fк, чистоты внутренней поверхности конденсаторных
трубок, воздушной плотности конденсатора, температуры и скорости движения
охлаждающей воды. Обычно значение температурного напора находится в диапазоне
δt = 5 — 10°С.
Среднее значение коэффициента теплопередачи для
конденсаторных трубок можно оценить по формуле Л.Д. Бермана
где а –
коэффициент, учитывающий влияние загрязнения поверхности охлаждения;
wв – скорость воды в конденсаторных
трубках;
d2 – внутренний диаметр трубок, мм;
х = 0,12·а·(1 + 0,15·t1в);
Фz – множитель, учитывающий влияние числа
ходов z воды в конденсаторе и определяемый по формуле
Фd – множитель, учитывающий изменение
паровой нагрузки dк конденсатора.
В итоге, вычислив значение
Qк = Gк·(hк — h‘к), находится площадь
Fк поверхности охлаждения конденсатора.
Гидравлическое сопротивление конденсатора (разность
давлений охлаждающей воды на входе и выходе из конденсатора) для турбин с
высоким начальным давлением пара оценивается в диапазоне
Dp0в = 25 — 40 кПа.
Паровое сопротивление в конденсаторах современных
турбин составляет диапазон значений
Dpп = 270 — 410 Па.
Это сопротивление зависит от конструкции трубного пучка. В конденсаторах
используют шахматную, треугольную, коридорную и лучевые разбивки трубного
пучка. Минимальное значение шага между трубками принимают в диапазоне
t = (1,25 — 1,3)·d1.
При этом к компоновке трубного пучка предъявляют
следующие требования: максимально возможное увеличение площади
«живого» сечения для прохода пара; создание постоянной скорости
протекания пара; организация наиболее короткого пути для паровоздушной смеси к
месту ее отсоса эжекторной установкой.
14.7 Определение числа и длины конденсаторных трубок
Объемный расход охлаждающей воды через конденсатор
Wv = 0,25·p·d22·nz·wв, м3/с,
где
nz –
среднее число трубок в одном ходе конденсатора, которое можно оценить по объемному
или массовому расходам охлаждающей воды.
Полное количество трубок при числе
z ходов
конденсатора n = nz·z. Массовый
расход охлаждающей воды Wm = Wv · rв,
кг/с вычисляется по расходу водяного пара Gк, кг/с в
конденсатор и значению кратности охлаждения
Длина конденсаторных трубок определяется по площади
поверхности охлаждения
Условный диаметр трубной доски
где
uтр = 0,22 — 0,32
– коэффициент использования трубной доски (отношение L/Dу должно находиться в пределах
1,5 — 2,5).
15
Лекция 15. Эксплуатация конденсационной установки (часть 2)
Содержание лекции: основы эксплуатации конденсационных установок. Характеристика конденсатора. Основные источники и признаки
ухудшения в работе конденсационной установки Воздухоудаляющие устройства.
Причины ухудшения работы пароструйных эжекторов [1, 14, 17, 18].
Цель лекции: знакомство
с основами эксплуатации конденсационных установок
15.1 Основы эксплуатации конденсационных установок
Основными показателями, определяющими качество работы
конденсационной установки являются: давление пара в конденсаторе
рк; температурный напор δt; нагрев
охлаждающей воды Dtв; паровая нагрузка конденсатора
dк; температура конденсата на выходе; давление пара
перед соплами эжектора; солесодержание конденсата.
Зависимость давления
pк от температуры воды на входе
t1в, паровой нагрузки
dк и расхода охлаждающей воды Wm называется характеристикой конденсатора.
Точная характеристика строится на основе результатов специальных испытаний
конденсатора. Для построения расчетной характеристики конденсатора используется
выражение
tп = t1в + Dtв + δt.
Температурный напор оценивается по формуле
δt = n·(31,5 + t1в)-1·(dк + 7,5)
где
n = 5 — 7 – коэффициент,
учитывающий чистоту поверхности охлаждения и воздушную плотность конденсатора.
На рисунке 23 представлена характеристика
конденсатора 300 КЦС-1 для турбины К-300-23,5 ЛМЗ.
Увеличение
Dtв
указывает на недостаток расхода охлажда-ющей воды и уменьшение из-за этого
кратности охлаждения. Увеличение δt свидетельствует об ухудшении условий теплообмена в
конденсаторе, что вызывается ростом присосов воздуха, изменением работы
эжекторов, загрязнением поверхностей.
15.2 Основные источники и признаки ухудшения в работе
конденсационной установки.
1.
Загрязнение трубок и трубных досок
конденсатора проверяется по разнице температуры насыщения пара при данном
давлении в конденсаторе и температуры циркуляционной воды на входе
(температурный напор). Например, при чистых трубках для температуры воды
25 — 30°С и расходе пара 150 — 160 т/ч недогрев должен
быть равен 6 — 7,5°С. Повышенный температурный напор свидетельствует
о загрязнении трубок. Признаками загрязнения являются повышенное давление в
конденсаторе и охлаждающей воды перед конденсатором.
2.
Высокий уровень конденсата в
конденсатосборнике (требуется проверка работы автомата уровня рециркуляции).
3.
Недостаточное давление пара,
направляемого на концевые уплотнения ЦНД турбины (требуется проверка работы
регулятора уплотнений).
4.
Плохая работа эжекторной группы.
5.
Срыв работы или уменьшение
производительности циркуляционных насосов (в том числе из-за попадания во
всасывающий участок насоса посторонних предметов).
6.
Плохая плотность вакуумной
системы, которая должна периодически проверяться и при необходимости
опрессовываться посредством заливки воды до уровня концевых уплотнений.
При эксплуатации конденсатора осуществляется
постоянный контроль за чистотой его теплообменных поверхностей и их
периодические очистки, которые выполняются, если давление в конденсаторе
увеличивается на 0,5% по сравнению с нормативным значением. Различают три
группы загрязнений: механические, биологические и солевые.
К механическим относят загрязнения трубок и трубных
досок травой, землей, водорослями и т.п. Для их предотвращения на водозаборных
и водоочистительных сооружениях устанавливаются разного рода сетки (крупно- и
мелкоячеистые), включая и подвижные. Кроме того, осуществляется очистка трубок
мягкими ершами и их промывка. Наиболее эффективным является использование
непрерывной очистки внутренних поверхностей конденсаторных трубок посредством
резиновых шариков.
Для борьбы с биологическими отложениями используется
метод термической сушки конденсаторов (при температурах 40 — 60°С
большинство микроорганизмов и водорослей погибает и в воздушной среде
высыхает).
Солевые отложения в форме накипей, образующихся при
выпадении из воды растворенных в ней солей, удаляются при обработке охлаждающей
воды фосфатами или кислотами (при оборотной схеме водоснабжения).
Одна из важнейших задач при эксплуатации
турбоагрегата — определение мест присосов воздуха в его вакуумной системе.
Современный способ отыскания неплотностей — использование галоидных
течеискателей, принцип действия которых основан на свойстве разогретого
платинового элемента испускать ионы. В области неплотности газ вместе с
воздухом попадает в вакуумную систему и далее отсасывается эжектором, в котором
устанавливается датчик, фиксирующий наличие галоидов. Обычно для обдувки
подозрительных мест используется газ фреон-12, который не является токсичным.
Высокие требования, предъявляемые к качеству
питательной воды, формируются уже на линии конденсата. Прежде всего, речь идет
о допустимом уровне присосов охлаждающей воды в конденсаторе:
0,001 — 0,005% для пресной воды; 0,0001% для сильно минерализованной
прудовой или морской воды. При этом в условиях непрерывной очистки к конденсату
предъявляются высокие требования по его жесткости. Нарушения водного режима
связаны с механическими повреждениями различных элементов конденсатора. Кроме
того, имеют место эрозионные и коррозионные процессы во влажно-паровой среде.
Обеспечение гидравлической плотности конденсатора зависит от качества
вальцовочных соединений трубок в трубных досках конденсатора. Для повышения их
герметичности используются уплотняющие покрытия на трубных досках (например,
битумное или покрытие на основе эпоксидных смол) со стороны водяных камер,
применяются конструкции с двойными трубными досками, а также организуются
солевые отсеки в паровом пространстве конденсатора.
15.3 Воздухоудаляющие устройства
Для поддержания номинального значения давления pк в конденсаторе паротурбинной установки
посредством отсоса воздуха из его объема используются пароструйные,
водоструйные и центробежные типы эжекторов. Подавляющее распространение
получили пароструйные эжекторы, простые по конструкции и компактные, не
требующие механического привода и позволяющие создать начальный уровень
разрежения в конденсаторе за короткое время (5 — 6 мин). Вместе
с тем, водоструйные эжекторы сегодня конкурируют с пароструйными в
турбоустановках с высоким начальным давлением водяного пара. В ряде
турбоустановок применяются центробежные типы эжекторов.
Одноступенчатый эжектор может создать разрежение до
600 мм рт. ст. Для получения большего разрежения при
удовлетворительной экономичности используют двух– и трехступенчатые эжекторы,
каждая ступень которых производит не полное, а частичное сжатие паровоздушной
смеси. Между ступенями устанавливают промежуточные охладители поверхностного
типа. В них большая часть пара конденсируется и теплота конденсации
используется для подогрева основного конденсата.
15.4 Причины неполадок в работе пароструйных эжекторов
При работе пароструйных эжекторов возможны следующие
неполадки:
—
повышенное давление всаса из-за
недостаточного расхода рабочего пара при снижении его давления, засорении сопел
или срыве режима работы сопел;
—
рециркуляция части воздуха через
одну из ступеней эжектора из-за опорожнения гидрозатвора на дренажной линии
промежуточного холодильника (часть воздуха возвращается в конденсатор);
—
колебания давления всасывания и
прерывистый выхлоп паровоздушной смеси из-за недостаточного расхода основного
пара при понижении его давления;
—
рост давления на стороне
всасывания в результате уменьшения сечения на линии отсоса паровоздушной смеси
из-за скопления в ней конденсата;
—
гидравлические удары внутри
корпуса эжектора из-за затопления одного из холодильников при засорении
перепускной трубки или разрыва трубки холодильника эжектора;
—
запаривание эжектора (большой
выброс влаги) при затоплении холодильника последней ступени или недостаточного
расхода конденсата при низких его расходах (высоких температурах).
16 Лекция 16. Явления, возникающие в турбине при
нестационарных режимах
Содержание лекции: явления, возникающие при относительно быстром изменении параметров в
проточной части турбины. Возникновение в деталях турбин и других элементах
турбоустановки нестационарного распределения температур. Взаимные деформации
деталей и их последствия. [18, 19, 20, 21].
Цель лекции: знакомство
с явлениями, возникающими в турбине при нестационарных режимах.
Любые нестационарные режимы всегда связаны со
снижением надежности и экономичности энергетического оборудования. Задача
эксплуатационного персонала состоит в том, чтобы вести эти режимы в строгом
соответствии с инструкцией, составленной на основе расчетов и опыта
эксплуатации аналогичного оборудования, допуская лишь минимальное снижение
надежности и небольшой перерасход топлива.
При изменении режима работы турбоустановки давления и
температуры в проточной части турбины изменяются. Ниже рассматриваются явления,
возникающие при относительно быстром изменении параметров в проточной части
турбины.
Быстрое изменение расхода пара и, следовательно,
давления в проточной части опасно для турбоустановок, имеющих большие
аккумулирующие емкости пара (например, промежуточный пароперегреватель). В этом
случае осевые усилия, приложенные к различным роторам (например, ЦВД и ЦСД),
изменяются во времени по-разному, и это приводит к появлению значительной
неуравновешенной осевой силы.
К еще большим последствиям приводит изменение
температуры в проточной части. Основным следствием изменения температуры
является возникновение в деталях турбин и других элементах турбоустановки
нестационарного распределения температур — нестационарных температурных полей.
В свою очередь, это приводит к двум явлениям.
Во-первых, детали турбины «в среднем» прогреваются
по-разному. Это приводит к тому, что их тепловое расширение оказывается различным
в различные моменты времени и, поэтому возникает опасность задеваний
вращающихся деталей о неподвижные, освобождения отдельных деталей на валу,
затруднения свободного теплового расширения одних деталей относительно других.
Во-вторых, в деталях вследствие неравномерного
прогрева возникают температурные напряжения, приводящие при их циклическом
повторении к трещинам малоцикловой усталости.
При нестационарных режимах наиболее важными являются
следующие взаимные деформации деталей:
а) продольное расширение или сокращение ротора
относительно статора;
б) тепловой изгиб ротора;
в) деформация корпуса вследствие несимметричного
прогрева.
При быстром повышении температуры пара ротор турбины
нагревается быстрее, чем корпус, поскольку его масса меньше, а поверхность и
интенсивность теплообмена с паром значительно больше. Поэтому ротор расширяется
быстрее статора, и это вызывает опасность осевых задеваний в проточной части.
При подаче в турбину пара с температурой более низкой, чем температура ее
деталей, происходит сокращение ротора относительно статора. Это явление еще
более опасно, чем относительное расширение ротора, поскольку осевые зазоры
между рабочим диском и предшествующей по ходу пара диафрагмой всегда меньше,
чем между диском и стоящей за ним диафрагмой.
Тепловой изгиб ротора возникает при его не осесимметричном
прогреве. Перед пуском конденсационной турбины в ней создается вакуум с помощью
эжектора. Для этого на уплотнения турбины подается пар, а из внутренней полости
турбины отсасывается паровоздушная смесь. Подвод уплотняющего пара к ротору
осуществляется не по всей окружности в месте подвода, а по его части и, если
подать пар на неподвижный ротор, он будет нагреваться по окружности
неравномерно. Возникнет тепловой изгиб ротора. Поэтому в процессе всего пуска,
пока в турбину не поступает пар от регулирующих клапанов, ротор турбины
вращается валоповоротным устройством.
При частичной нагрузке турбины в камере регулирующей
ступени температура пара, прошедшего через полностью и частично открытые клапаны,
будет различной, температура за дугой подвода пара, питаемой от частично
открытого клапана, будет большей из-за дросселирования пара в клапане.
Неравномерный нагрев корпуса турбины по окружности приводит к его изгибу
вследствие того, что более нагретые образующие корпуса расширяются сильнее, чем
менее нагретые.
Первые испытания турбины Т-100-130 TМЗ показали, что
при нагрузке примерно 30-45 МВт разность температур между верхом и низом
корпуса ЦВД составляла 70-80 °С. При этом корпус изгибался осью вверх со
стрелой прогиба 0,7-0,8 мм. Одной из причин такого прогиба оказалось сильное
дросселирование пара в частично открытом клапане (с 3,3 до 0,3 МПа), вследствие
чего разность температур составила 88 °С. Другой причиной были
неудовлетворительные условия для окружной циркуляции пара в камере регулирующей
ступени. В результате принятых мер удалось уменьшить разность температур верха
и низа корпуса до 10 °С.
Ориентировочные оценки показывают, что каждые 10 °С
разности температур верха и низа создают прогиб корпуса вверх примерно на 0,13-0,15
мм. Поэтому каждый турбинный завод оговаривает ту предельную разность
температур верха и низа корпуса, при которой разрешаются пуск и эксплуатация
турбины. При больших разностях возникает опасность задеваний между ротором и
гребешками уплотнений, расположенными в нижних частях диафрагм. Обычно
допускаемая разность температур составляет 25-35 °С. Такой же выгиб корпуса
турбины может произойти из-за неодинакового нагрева фланцев: при более нагретых
верхних фланцах корпус изгибается стрелой вверх. Если левый фланец корпуса
турбины нагрет сильнее, чем правый, то он прогнется стрелой наружу, а правый —
внутрь по отношению к оси турбины. На одной из турбин ПТ-60-130 ЛМЗ вследствие
несимметричного обогрева нижний фланец нагревался сильнее верхнего на 30 °С, в
результате чего радиальные зазоры в проточной части уменьшались на 0,6 мм. При
неравномерном прогреве отдельной детали и отсутствии свободы тепловых
расширений в ней возникают температурные напряжения.
Следует запомнить, что температурные напряжения в
любой точке детали пропорциональны разности температуры в этой точке и средней
температуры детали. Поэтому, если поверхность детали нагревается быстро, а сама
деталь не успевает прогреваться (т.е. ее средняя температура остается низкой),
возникают высокие температурные напряжения. Наоборот, если температура
поверхности детали изменяется медленно и мало отличается от средней
температуры, возникающие температурные напряжения будут небольшими.
Многократное повторение высоких
температурных напряжений при каждом пуске, остановке или резком изменении
нагрузки приводит к появлению в деталях трещин малоцикловой усталости. В
некоторых случаях высокие температурные напряжения могут вызвать хрупкое
разрушение детали.
Турбоустановка, кроме турбины, включает в себя и
другие элементы, температура которых при нестационарных режимах быстро
изменяется, и в которых возникают высокие температурные напряжения.
К ним относятся: корпуса регулирующих и стопорных
клапанов, установленных вне турбины; корпуса задвижек на паропроводах;
тройники; сами паропроводы. Если теплофикационная турбина входит в состав
энергетического блока, то существенным температурным напряжениям подвергается
барабан, если котел барабанный, или сепаратор, если котел прямоточный. В результате
довольно сложных расчетов и анализа температурных напряжений, проводимых
научно-исследовательскими институтами, натурных экспериментов, экспериментов на
моделях, а также с учетом опыта эксплуатации устанавливаются критерии
безопасного пуска. В большинстве случаев, это разности температур ΔT в
характерных точках детали: по толщине стенки корпуса, по ширине фланца, между
фланцем и шпилькой, между крышкой и корпусом стопорного клапана и т.д. В тех
случаях, когда измерить и вывести на прибор такие разности затруднительно
(например, между поверхностью ротора и его расточкой), задают предельно
допустимые скорости изменения параметров пара, омывающего рассматриваемую
деталь.
Общее правило, обеспечивающее безопасные температурные
напряжения, состоит в том, что температура среды, омывающей деталь, не должна
существенно отличаться от температуры поверхности детали. При этом
предпочтительнее иметь температуру пара большей, чем температуру детали.
Вызвано это тем, что при охлаждении детали в ней возникают температурные
напряжения растяжения, которые более опасны, чем напряжения сжатия.
При нестационарных режимах затраты топлива на
производство электроэнергии всегда оказываются повышенными. Особенно велики
потери теплоты при пусках энергоблоков. При подготовительных операциях к пуску
производятся деаэрация питательной воды, набор вакуума в конденсаторе, промывка
трубной системы котла, его растопка и доведение параметров за ним до
необходимых, приведение ротора турбины во вращение, разгон турбины до
номинальной частоты и включение турбогенератора в сеть.
На всех этих этапах, суммарная длительность которых
может достигать несколько часов, затрачивается большое количество топлива и
электроэнергии для привода вспомогательных механизмов, а выработки полезной
электроэнергии не происходит. При нагружении турбины (этот период также может
длиться несколько часов) турбина работает в нерасчетном режиме по пропуску
пара, начальным параметрам и конечному давлению, и потому имеет сниженную
экономичность.
17
Лекция 17. Пуск паротурбинной установки
Содержание лекции: виды пусков. Подготовка к пуску. Основные пусковые операции. Набор
оборотов и подъем нагрузки. Особенности пуска блочной ПТУ [14, 16, 18].
Цель лекции: знакомство
с основными пусковыми операциями и технологией пуска.
17.1
Подготовка к пуску
Нормальная работа турбинной установки
складывается из нескольких характерных режимов: пуска, длительной работы на
номинальной мощности или частичных нагрузках, переходных режимов, останова.
Пуск турбины – одну из ответственных операций – выполняют, точно соблюдая
Правила технической эксплуатации электрических станций и сетей, а также
действующие инструкции. Особенностью пуска является необходимость прогрева
металлоемкого оборудования: паропроводов, стопорных клапанов и арматуры,
корпуса и ротора турбины. При слишком быстром прогреве в металле оборудования
возникают большие разности температур, которые вызывают появление опасных температурных
напряжений, тем больших, чем выше температура пара, его расход и разница температур
между металлом и паром в начале пуска. Температура металла оборудования перед
пуском зависит от того, сколько времени прошло с момента останова турбинной
установки.
Паропроводы свежего пара и
стопорные клапаны остывают двое-трое суток, а цилиндры турбины – только через
пять-шесть суток. Температура оборудования зависит от времени простоя перед
пуском.
Различают пуски из
холодного, горячего и неостывшего состояний. Холодным называют такое состояние
оборудования, когда котел и паропроводы блока остыли полностью, а температура
металла турбины составляют не более 150°С. Мощные энергоблоки остывают до
такого состояния за 90…100 ч. Горячим называют такое состояние, при котором
металл турбины имеет температуру не ниже 420—450°С (обычно через 6…10 ч после
останова). Состояния, соответствующие промежуточным температурам металла
турбины, называют неостывшими.
Принципиально схема пуска
при всех тепловых состояниях примерно одинакова. Начальное тепловое состояние
оборудования в основном влияет на длительность отдельных операций, которые
должны выполняться в строгом соответствии с указаниями станционной инструкции
по пуску турбины.
Любой пуск включает в себя
такие этапы, как подготовка к нему, прогрев паропроводов и арматуры, пуск
конденсационной установки и турбины, синхронизация генератора, нагружение
турбины. Проверка оборудования – важный элемент подготовки к пуску.
Перед пуском турбины
обязательно проверяют исправность и положение всех ее запорных и управляющих
органов и состояние средств технологической защиты (плотность задвижек,
стопорных и регулирующих клапанов и т. д.). При полностью закрытых регулирующих
и стопорных клапанах и электрогенераторе, отключенном от сети, ротор турбины не
должен вращаться. Если закрыт только стопорный или регулирующий клапан, ротор
разгоняется паром, проходящим через неплотности между седлами и головками
клапанов. Эти неплотности появляются в процессе работы, например из-за тепловых
расширений. Нельзя пускать турбину, если неисправны элементы автоматической
защиты (реле осевого сдвига, вакуум-реле, реле падения давления масла в системе
смазки и др.). При срабатывании любой из защит турбины появляются световой и
звуковой сигналы. До пуска должна быть проверена и опробована система регулирования
и защиты турбины от разгона. Это особенно важно, так как разгон турбины при
внезапном сбросе нагрузки может вызвать серьезную аварию, если неисправна
система регулирования или защиты.
Особое внимание уделяют
системе маслоснабжения турбины. Масло должно быть прозрачным, без влаги и
механических примесей и иметь температуру не менее 40-45°С. При более низкой
температуре масло становится слишком вязким, и ротор после пуска может начать
вибрировать на масляной пленке. Для подогрева масла его до пуска некоторое
время (особенно зимой) прокачивают масляным насосом через систему смазки.
Нельзя пускать турбину, если неисправны один из вспомогательных масляных
насосов или система автоматического включения резерва.
Перед пуском необходимо
убедиться также, что все контрольно-измерительные приборы, позволяющие следить
за режимом работы турбины и вспомогательного оборудования, исправны и включены,
а дистанционное управление готово к работе.
17.2 Пуск турбины
Одной из первых пусковых
операций является прогрев паропроводов свежего пара и промперегрева, а также
стопорных клапанов турбины. В это время из паропроводов и органов паровпуска через дренажные линии отводится
конденсат, образующийся при прогреве холодных стенок паром. Скорость прогрева
паропроводов и стопорных клапанов обязательно контролируют. Контроль
температуры позволяет следить за тепловым состоянием элементов и вести прогрев
в точном соответствии с требованиями инструкции. Нельзя превышать предписанную
инструкцией скорость прогрева, так как при слишком быстром прогреве из-за
температурных напряжений в стенках паропроводов и стопорных клапанов могут
появиться трещины. Во время прогрева необходимо следить по указателям в контрольных
сечениях за перемещением паропроводов в результате расширения.
После прогрева паропроводов
и стопорных клапанов включают систему маслоснабжения турбины, проверив уровень масла в масляном
баке, а затем вспомогательный масляный турбонасос, после чего масло начинает
поступать в систему смазки и регулирования. Давление, которое должен создать
вспомогательный масляный насос, указано в инструкции по пуску. При давлении
ниже необходимого ротор турбины задевает поверхности вкладышей подшипников. При
малом давлении масла система регулирования турбины не работоспособна, так как
развиваемые им усилия недостаточны для перемещения отдельных элементов системы
регулирования (золотников, поршней и др.). Поэтому, если давление масла меньше
указанного в инструкции, пуск турбины запрещается. При проверке системы следует
убедиться, что масло поступает ко всем подшипникам и его температура после
подшипников, а также давление в контрольных точках соответствует инструкции.
Затем проводят пробный пуск валоповоротного устройства.
Следующей операцией
является пуск конденсационной установки. До подачи пара на концевые уплотнения турбина и
конденсационная установка заполнены воздухом атмосферного давления. Для
эффективного конденсирования пара после турбины необходимо откачать этот воздух
из конденсатора. Предварительно конденсатор заполняют конденсатом или химически
очищенной водой, так чтобы уровень по водоуказательному стеклу находился на 3/4
его высоты, запускают циркуляционные насосы с закрытыми задвижками на напорной
линии и подают в трубки конденсатора циркуляционную воду, для чего сначала
открывают задвижки на выходе ее из конденсатора, а потом – на впуске. Затем
включают конденсатные насосы, работающие в это время в режиме рециркуляции, и
запускают основной и пусковой эжекторы, которые начинают откачивать воздух из
конденсатора и корпуса турбины. После включения валоповоротного устройства,
когда начинает вращаться ротор, пар подается на концевые уплотнения турбины.
Если ротор неподвижен, подавать пар на концевые уплотнения нельзя. Количество
пара, которое подается на уплотнения, зависит от давления в корпусе турбины и
конденсаторе. По мере того, как это давление уменьшается («углубляется
вакуум»), расход пара на уплотнения увеличивают.
При вакууме в конденсаторе
40 кПа (300 мм рт. ст.) начинают сбрасывать пар и горячий конденсат из
пускосбросных устройств и дренажей паропроводов, что уменьшает потери воды при
пусках. Так как поступающий в конденсатор конденсат может быть загрязнен, его
возвращают в цикл тепловой электростанции после очистки в блочной
обессоливающей установке. После прогрева паропроводов и стопорного клапана,
проверки нормальной работы маслосистемы и конденсационной установки пар
подается в проточную часть турбины. В конденсаторе, в это время вакуум должен
быть равен 53-77 кПа (400-500 мм.рт.ст.).
Когда под действием пара
ротор начинает вращаться, валоповоротное устройство автоматически отключается.
Момент начала ускорения вращения ротора под действием пара называют толчком
ротора.
Вначале подают такое
количество пара, которое обеспечивает частоту вращения ротора 400-500 об/мин, убеждаются прослушиванием, в нормальной
работе подшипников турбины и проверяют температуру масла после них. При вакууме
в конденсаторе примерно 80 кПа (600 мм.рт.ст.) отключают пусковой эжектор и
оставляют работать только основной. К моменту выхода ротора турбины на
номинальную частоту вращения вакуум должен быть не менее
86 кПа (650 мм рт. ст.).
Чтобы снизить температуру в
выхлопной части низкого давления и не допустить ее перегрев, а также перегрев
рабочих лопаток последней ступени, необходимо при работе на холостом ходу
поддерживать вакуум на уровне 86 кПа. Особенно опасен перегрев турбин, у
которых лопатки последней ступени выполнены из титановых сплавов, так как
прочность этих сплавов значительно снижается с увеличением температуры.
Для каждой турбины
существуют такие частоты вращения, при которых резко увеличивается вибрация
турбоагрегата, т. е. роторы турбины и электрогенератора попадают в резонанс.
Эти частоты, называемые критическими, необходимо «проходить» быстро и не
допускать работу турбины при них. Когда частота вращения ротора увеличивается
до 1500-2000 об/мин, убедившись, что главный масляный насос вступил в работу, отключают
вспомогательный масляный турбонасос. Для проверки начала работы главного насоса
уменьшают частоту вращения ротора вспомогательного масляного турбонасоса и
следят за давлением масла. Если оно не падает, значит, главный масляный насос
работает нормально. После этого, частоту вращения ротора турбины доводят до
номинальной, увеличивая пропуск пара через проточную часть, проверяют
регулирование турбины, автомат безопасности и, если турбина устойчиво работает
на холостом ходу, синхронизируют работу электрогенератора с сетью и подключают
его к сети.
В мощных турбинах скорость
прогрева металла корпуса и ротора существенно зависит от расхода пара и,
следовательно, от нагрузки. Нагружать турбину нужно быстро, но с такой
скоростью, при которой не возникает опасных температурных напряжений и
деформаций. Именно такой график нагружения предписан инструкцией по пуску.
Увеличение нагрузки быстрее, чем это допускается инструкцией, может привести к
аварии. При нагружении турбины необходимо обращать внимание на работу системы
обогрева фланцев и смещение ротора относительно корпуса. При нагрузке, равной
25-30 % номинальной, расход пара, поступающего в конденсатор, достаточен,
чтобы, отключив рециркуляцию конденсата, довести нагрузку турбины с заданной
скоростью до номинальной.
17.3 Особенности пусковых режимов блочных установок
Особенностью пусковых режимов блочных установок
является то, что одновременно пускают котел и турбину. График и режим их пуска должны быть хорошо
согласованы друг с другом. Пуск блоков из холодного состояния производят на
скользящих параметрах. Это позволяет экономить топливо, так как котел при пуске
вырабатывает практически столько пара, сколько потребляется турбиной. В начальный
момент пара требуется немного: для прогрева паропроводов и «разворота» ротора
турбины. При пуске из холодного состояния прогревать паровпускные устройства и
цилиндр высокого давления нужно паром возможно меньшей температуры, которая
определяется пусковой схемой блока. Однако давление должно быть таким, чтобы
температура была выше температуры насыщения не менее чем на 50°С.
Наилучшие условия пуска создаются при температуре
свежего пара 250-300°С. Пар такой температуры должен поступать в турбину при
толчке ротора и увеличении частоты вращения до номинальной.
Особенности пуска
блока с неостывшей турбиной связаны с тем, что металл турбины нагрет, а
паропроводы успевают остыть и их необходимо прогреть. Кроме того, нельзя
подавать в горячую турбину пар, температура которого ниже температуры металла.
Так, для блоков 300 МВт температура свежего пара должна быть больше температуры
металла наружного корпуса ЦВД на 80°С.
Правила технической эксплуатации предписывают во время
пуска блока из любого состояния контролировать скорость прогрева паропроводов,
стопорных клапанов, пароперепускных труб, относительное удлинение и осевое
положение роторов, вибрацию подшипников турбины, генератора и возбудителя,
прогиб ротора части высокого давления турбины, разность температур в верхней и
нижней частях ее цилиндров, фланцев и шпилек, температуру масла на сливе из
подшипников.
При пуске турбины, действующие на ротор и
воспринимаемые упорным подшипником осевые усилия могут достигать предельных
значений. При этом поверхности колодок подшипника могут подплавиться, в результате
чего ротор будет задевать корпус. Поэтому во время пуска важно постоянно
следить за осевым положением ротора. Об увеличении осевого усилия можно судить
по температуре масла на сливе из упорного подшипника или упорных колодок.
Особо ответственным является пуск турбины после
капитального ремонта. Операции, которые необходимо дополнительно провести в
этом случае, оговариваются специальной инструкцией.
18
Лекция 18. Останов паротурбинной установки
Содержание лекции: способы останова турбины. Снижение нагрузки. Выбег ротора. Операции при
останове. Аварийный останов турбоустановки
[14, 16, 18,].
Цель лекции — знакомство
с основными операциями при останове турбины и аварийными остановами турбин.
18.1
Плановый останов турбины
При плановом останове турбины известны время и цель.
Время и причины аварийного останова турбины, заранее неизвестны. Останов
турбины производят в основном двумя способами: без расхолаживания и с расхолаживанием.
«Правила технической эксплуатации» не предписывают единых жестких требований к
режимам останова, так как каждая установка, имеет свои особенности. Общими
требованиями являются проверка исправности и опробование резервных и аварийных
масляных насосов, а также стопорного клапана.
При останове турбины без расхолаживания важно так
подобрать режим, чтобы возможно дольше сохранить ее в горячем состоянии.
Например, при останове блока мощностью 300 МВт сначала производят плавную
разгрузку до 150 МВт. На этом режиме блок еще работает устойчиво (по условиям
работы питательного турбонасоса). Затем котел гасят, в течение 1-2 мин турбину
разгружают до 90-100 МВт и отключают. При этом давление в котле сохраняется
близким к номинальному и блок находится в состоянии «горячего резерва».
При нулевом расходе пара цилиндры среднего и низкого
давления быстро разогреваются до недопустимых температур, если электрогенератор
не отключен от сети и ротор вращается на холостом ходу. Потери на вентиляцию
преобразуются в теплоту, которая разогревает турбину. Поэтому работа на беспаровом
режиме не должна превышать 10-20 мин. Из этого состояния можно наиболее быстро
выйти на исходную нагрузку.
При останове турбины с расхолаживанием следует
поддерживать температуру пара не менее чем на 50 °С больше, чем температура
насыщения при данном давлении. Это условие необходимо, чтобы в турбину не попал
влажный пар. Начиная с определенного давления, система автоматики перестает
работать и далее температуру свежего пара снижают с помощью ручного управления.
Из-за трудности ручного управления на этом этапе допускается поочередное
изменение паропроизводительности, температуры и давления свежего пара.
Одновременное снижение паропроизводительности, давления и температуры свежего
пара возможно в конце расхолаживания при сепараторном режиме. Расхолаживание
можно вести без перевода котла на сепараторный режим, т. е. на прямоточном
режиме, как это делается на блоках 300 МВт. При постоянных параметрах свежего
пара блок разгружают примерно наполовину. Затем закрывают встроенные задвижки
котла и полностью открывают регулирующие клапаны турбины при необходимом
снижении температуры и давления пара. Далее при постоянных температуре и
давлении паропроизводительность котла уменьшают до растопочной. На последнем
этапе часть пара через БРОУ сбрасывают в конденсатор турбины, и расход пара
через турбину уменьшается. Для прекращения подачи пара в турбину закрывают
стопорный кран и отключают электрогенератор. При этом остается подача пара на уплотнения
и запускается резервный масляный насос.
При выбеге ротора турбины ее необходимо
«прослушивать». В это время ротор вращается по инерции, пар не шумит внутри
турбины, поэтому и хорошо прослушиваются посторонние звуки. С момента
прекращения подачи пара в проточную часть до полной остановки ротора проходит
определенное для каждой турбины время. Согласно «Правилам технической
эксплуатации» время выбега ротора определяют при всех остановах турбины. Через
200-300 ч эксплуатации на исправной турбине проводят специальные испытания, во
время которых снимают график выбега ротора при ее останове с нормальным
вакуумом в конденсаторе. Этот график показывает зависимость частоты вращения
ротора от времени с момента закрытия стопорного клапана до момента полной
остановки ротора. Такой график имеется у машиниста турбины. При изменении
состояния турбины (увеличении трения в подшипниках или редукторах, задеваниях)
время выбега заметно, уменьшается. Задевания легко определяют на слух во время
выбега ротора. Появление неплотностей в стопорном или регулирующих клапанах и
запорной арматуре отборов также увеличивает время выбега ротора. Об отклонении
времени выбега более чем на 2-3 мин от контрольного ставят в известность
дежурного инженера станции и руководство цеха. Для разных турбин время выбега
колеблется от 20 до 30 мин.
После снижения частоты вращения ротора до 400-500
об/мин, уменьшая подачу пара в конденсатор, чтобы к моменту остановки ротора в
нем установилось атмосферное давление, одновременно уменьшают подачу пара на
эжекторы: Сразу после остановки ротора включают валоповоротное устройство,
время работы которого для каждой турбины оговорено инструкцией и обычно
составляет несколько часов. В это время масло на смазывание подшипников
подается от резервного масляного насоса.
Конденсатные насосы останавливают после прекращения
подачи пара в турбину. Через 1 ч после полного останова турбины можно
остановить циркуляционные насосы. Заключительной операцией является закрытие
всех запорных органов паропровода. Паропровод, подводящий пар к турбине,
отключают от паровой магистрали и соединяют с атмосферой. При останове турбины
необходимо следить за разницей температур между верхом и низом ее корпуса,
фланцами и шпильками, наружными и внутренними стенками стопорных клапанов и
паропроводов.
18.2 Аварийный останов турбины
При возникновении аварийных ситуаций, если не
сработала одна из защит, персонал обязан прекратить доступ пара в турбину
командой с дистанционного щита управления или нажатием кнопки автомата безопасности
на корпусе переднего подшипника. При этом необходимо убедиться, что стопорный и
регулирующий клапаны закрылись. «Правилами технической эксплуатации»
предусмотрены следующие основные причины останова:
—
частота вращения ротора выше уровня, при котором
срабатывает автомат безопасности;
—
недопустимо большие осевой сдвиг или относительное
перемещение ротора турбины;
—
резкие отклонения температуры свежего пара и пара
промежуточного перегрева от установленных верхних и нижних предельных значений;
—
слышимые металлические звуки и необычные шумы внутри
турбины;
—
появление искр или дыма из подшипников и концевых
уплотнений турбины или генератора;
—
внезапная сильная вибрация турбоагрегата;
—
появление признаков гидравлических ударов в
паропроводахсвежего пара или турбине;
—
разрыв или трещины в паропроводах свежего пара, пара
промежуточного перегрева или отбора, трубопроводах основного конденсата и питательной
воды, маслопроводах, коллекторах, тройниках, сварных и фланцевых соединениях, а
также в корпусах клапанов и распределительных коробках;
—
воспламенение масла на турбине и невозможность
немедленной ликвидации пожара имеющимися средствами;
—
уменьшение разности давлений между маслом и водородом
ниже предельного значения;
—
недопустимое снижение давления масла в системе смазки
турбины или его уровня в масляном баке, а также недопустимое повышение
температуры масла на сливе из любого подшипника или на любой из колодок
упорного подшипника;
—
снижение вакуума в конденсаторе до аварийного.
Разгон турбины до частоты вращения, превышающий
значение, указанное заводом-изготовителем, при несрабатывании автомата
безопасности и дополнительной защиты приводит к разрушению лопаточного
аппарата, поломке валопровода.
Разрушение валопровода приводит к повреждению
подшипников турбины и генератора, загоранию масла и водорода, выводу из строя
турбоагрегата на длительное время.
Наиболее опасными режимами с точки зрения возможности
разгона роторов являются:
— испытание автомата безопасности повышением частоты
вращения, сопровождающееся неправильными действиями персонала;
— неконтролируемый пуск турбины с самопроизвольным
набором частоты вращения из-за неисправности систем парораспределения,
регулирования и ошибок персонала;
— внезапный сброс нагрузки с отключением генератора и
динамическим забросом частоты вращения ротора, неудержанием холостого хода и
несрабатыванием автомата безопасности.
После закрытия стопорного клапана отключают от сети
генератор и перекрывают доступ пара к стопорному клапану и отборам турбины.
Для этого закрывают главные паровые задвижки на
паропроводах регулируемых отборов. Время работы на беспаровом режиме
ограничено.
В ряде случаев немедленный останов турбины не
требуется. Решение о времени останова принимает главный инженер электростанции.
Список литературы
1.
РД 34 РК.20.501-02 Правила
технической эксплуатации электрических станций и сетей РК., 2002 г.
2.
Резников М.И., Липов Ю.М. «Паровые
котлы тепловых электростанций: Учебник для ВУЗов». — М.: Энергоиздат,
1981.
3.
«Парогенераторы: Учебник
для ВУЗов» / Ковалев А.П., Лелеев Н.С., Виленский Т.В. — М.:
Энергоиздат, 1985.
4.
Стырикович М.А., Катковская К.Я.,
Серов Е.П. «Парогенераторы электростанций». — М.: Энергия, 1966.
5.
Сидельковский Л.Н., Юренев В.Н.
«Парогенераторы промышленных предприятий». — М.: Энергия, 1978.
6.
Мейкляр М.В. «Современные
котельные агрегаты ТКЗ». — М.: Энергия, 1978.
7.
Елизаров П. П. Эксплуатация
котельных установок высокого давления на электростанциях. — М.-Л.:
Госэнергоиздат, 1961.
8.
Качан А. Д. Режимы работы и
эксплуатации тепловых электрических станций. – Минск: Высшая школа, 1978.
9.
Гиршфельд В. Я., Князев А. М.,
Куликов В. Е. Режимы работы и эксплуатация ТЭС. — М.: Энергия, 1980.
10.
Цвинар Л. Пуск паровых котлов. —
М.: Энергоиздат, 1981.
11.
Прокопенко А. Д., Мысак И. С.
Стационарные, переменные и пусковые режимы энергоблоков ТЭС. — М.:
Энергоатомиздат, 1990.
12.
Липов Ю.М., Третьяков Ю.М.
Котельные установки и парогенераторы. – Москва-Ижевск: НИЦ «Регулярная и
хаотичная динамика», 2003. — 592 с.
13.
Росляков П.В. Методы защиты
окружающей среды: Учебник для вузов. – М.: Изд. МЭИ, 2006. – 330 с.
14.
Электронная энциклопедия
энергетики. М.: Изд. МЭИ, 2007.
15.
Паровые и газовые турбины/ Под
ред. Костюка А.Г. и Фролова В.В. – М.: Энергоатомиздат, 2001. – 350 с.
16.
Капелович Б.Э. Эксплуатация
паротурбинных установок. – М.: Энергоатомиздат, 1985.-304 с.
17.
Трухний А.Д. Стационарные паровые
турбины. – М.: Энергоатомиздат, 1990.-640 с.
18.
Трухний А. Д., Ломакин Б. В.
Теплофикационные паровые турбины и турбоустановки. – М.: МЭИ, 2002. – 540 с.
19.
Генбач А.А. Нагнетатели и тепловые
двигатели. Переходные режимы работы турбомашин ТЭС (нестационарный теплообмен в
турбомашинах): Конспект лекций. – Алматы: АИЭС, 1999.- 83 с.
20.
Плоткин Е.Р., Лейзерович А.Ш.
Пусковые режимы турбин энергоблоков. – М.: Энергия, 1980. – 120 с.
21.
Зысина-Моложен Л.М., Моложен Л.М.,
Поляк М.П. Теплообмен в турбомашинах. — Л.: Машиностроение, 1974.-336 с.
Содержание
Предисловие.………………………………………………………………………….3
1 Лекция
1. Введение. Эксплуатационные режимы работы котлов ……….…….4
2 Лекция
2. Рабочие диапазоны нагрузки котельных
агрегатов ТЭС ……………..8
3 Лекция
3. Подготовка котла к пуску …………………………………..……….14
4 Лекция
4. Пуск котельной установки (барабанный
котел)……………….……18
5 Лекция
5. Включение котла в магистраль и переход на основной вид
топлива ……………………………………………………………………………..22
6 Лекция
6. Пусковая схема прямоточного котла. Особенности пуска ………..24
7 Лекция
7. Останов
и расхолаживание котельной установки
…………..……..28
8 Лекция
8. Загрязнения, эрозия и коррозия
конвективных поверхностей нагрева …………………………………………………………………………..….32
9 Лекция
9. Аварии и повреждения паровых котлов ………………..…………..36
10
Лекция 10. Основы эксплуатации паротурбинных установок……………….40
11 Лекция 11. Система регулирования и защиты паровой
турбины (часть 1)……..45
12 Лекция 12. Система регулирования и защиты паровой
турбины (часть 2)…….49
13
Лекция 13. Масляная система турбины и эксплуатация маслохозяйства……53
14
Лекция 14. Эксплуатация конденсационной установки (часть 1)……………58
15 Лекция 15. Эксплуатация
конденсационной установки (часть 2)……………63
16 Лекция 16.
Явления, возникающие в турбине при нестационарных режимах…….66
17
Лекция 17. Пуск паротурбинной установки…………………………………..70
18
Лекция 18. Останов паротурбинной установки……………………….………74
Список
литературы…………………………………………………………………78
С позиций соблюдения режимных характеристик ПСУ при их эксплуатации основное внимание уделяется постоянным и переменным режимам работы паровой турбины.
Постоянный режим работы паровой турбины. Для современных мощных турбоустановок на тепловых и атомных электростанциях единичной мощностью от нескольких сотен МВт до 1000–1500 МВт, которые, как правило, эксплуатируются в постоянном режиме максимальной нагрузки, на первое место выходят такие показатели, как экономичность, надежность, долговечность и ремонтопригодность.
Экономичность ПТУ характеризуется как коэффициентом полезного действия (к.п.д.) турбоустановки (ТУ), так и удельным расходом теплоты брутто (т.е. без учета затрат энергии на собственные нужды ТУ). Показателями экономичности для теплофикационных турбоустановок с регулируемыми отборами на отопление и горячее водоснабжение являются удельный расход пара на теплофикационном режиме, удельный расход теплоты на конденсационном режиме, удельный расход теплоты на выработку электроэнергии и др. Удельный расход теплоты брутто для конденсационных турбин большой мощности находится на уровне 7640– 7725 кДж/(кВт·ч); для ТЭС – 10200 кДж/(кВт·ч) и 11500 кДж/(кВт·ч) для АЭС. Удельный расход теплоты брутто для теплофикационных турбоустановок при температуре охлаждающей воды 20°С на конденсационном режиме составляет порядка 8145–9080 кДж/(кВт·ч), а удельный расход пара на теплофикационном режиме – не более 3,6–4,3 кг/(кВт·ч).
Надежность и долговечность характеризуются рядом количественных показателей, таких как средняя наработка на отказ, полный назначенный срок службы, полный назначенный ресурс элементов, средний срок службы между капитальными ремонтами, коэффициент технического использования, коэффициент готовности и другими. Полный назначенный срок службы энергоблока выпуска до 1991 года составляет не менее 30 лет, оборудования выпуска после 1991 года – не менее 40 лет. Полный назначенный ресурс (парковый ресурс) основных элементов, работающих при температурах выше 450°С, составляет 220 тыс. часов эксплуатации. Для турбин большой мощности установлена наработка на отказ не менее 5500 ч и коэффициент готовности не менее 97%.
Переменный режим работы паровой турбины предполагает прежде всего изменение расхода пара через проточную часть – в сторону уменьшения от номинального. При этом минимальные потери при переменном, т.е. «частичном», расходе пара достигаются при сопловом регулировании, когда полностью открыты клапаны (клапан), обслуживающие одну определенную группу сопел. Теплоперепады существенно изменяются только на регулирующей и последней ступени проточной части. Теплоперепады промежуточных ступеней остаются почти постоянными при уменьшении расхода пара через турбину. Условия работы промежуточных ступеней и, следовательно, к.п.д. всех ступеней высокого давления (кроме первой ступени), среднего давления и низкого давления (кроме последней ступени) практически не изменяются.
Чем больше подъем клапана, обслуживающего какую-либо одну группу сопел, тем меньшее приращение расхода приходится на «единицу» его подъема. При достижении h/d ≈ 0,28 (где h – линейное смещение клапана при его открытии, а d – диаметр клапана) приращение расхода пара через клапан практически прекращается. Поэтому для обеспечения плавности процесса нагружения предусматривается открытие клапана, обслуживающего следующую группу сопел, с некоторой «перекрышей», т.е. несколько раньше, чем полностью откроется предыдущий клапан.
Для последней ступени цилиндра низкого давления уменьшение относительного объемного расхода пара до величины ниже 0,4 GV 2 приводит к образованию вихрей в основном потоке как у корня рабочих лопаток последней ступени, так и у их периферии, что опасно с точки зрения динамических нерасчетных напряжений в этих лопатках, которые и без того нагружены до предела.
Основы эксплуатации паровых турбин. Требования к маневренности и надежности современных паровых турбин в процессе их эксплуатации связаны с общими условиями работы энергосистем, суточными, годовыми графиками энергопотребления, структурой генерирующих мощностей в энергосистемах, их состоянием и техническими возможностями. В настоящее время графики электрических нагрузок энергосистем характеризуются большой неравномерностью: резкие пики нагрузок в утренние и вечерние часы, провалы в ночные часы и выходные дни, при необходимости обеспечения быстрого повышения и снижения нагрузок. Под маневренностью понимают способность энергоблока изменять мощность в течение суток для покрытия графика нагрузки энергосистемы. Важными в этой связи являются периоды нагружения и разгружения турбоагрегата, а также пуска из различных тепловых состояний (горячего – после предварительного простоя менее 6–10 ч, неостывшего – после предварительного простоя от 10 ч до 70–90 ч, холодного – после предварительного простоя более 70–90 ч). Также учитывают количество остановов-пусков за весь срок службы, нижний предел регулировочного диапазона, т.е. нижний предел интервала нагрузки, когда мощность изменяется автоматически без изменения состава вспомогательного оборудования, и возможность работы на нагрузке собственных нужд после сброса нагрузки.
Надежность работы энергоблока в значительной мере зависит от того, насколько собственно турбина и ее вспомогательное оборудование защищены от опасного воздействия нестационарных процессов. Статистика повреждаемости оборудования показывает, что подавляющее большинство отказов происходит именно в момент осуществления переходных режимов эксплуатации, когда меняется та или иная совокупность параметров. Для того, чтобы избежать развития аварийной ситуации, применяют аварийную остановку турбины: со срывом вакуума или без срыва вакуума.
Со срывом вакуума турбину (для турбин с частотой вращения ротора 3000 об/мин) следует немедленно остановить в следующих случаях: при увеличении числа оборотов сверх 3360 об/мин; при внезапном повышении вибрации на величину 20 мкм (виброскорость 1 мм/с) и более на любом из подшипников; при внезапном повышении температуры масла на сливе любого подшипника выше 70°C; при падении давления масла на подшипниках ниже 0,15 МПа; при повышении температуры баббита любого из подшипников выше 100°C.
Внезапный принудительный останов необходим также при любых ударах в проточной части турбины, при разрыве паропроводов, любом воспламенении на турбине или генераторе.
Остановка без срыва вакуума предусмотрена при следующих отклонениях от нормального режима эксплуатации: при отклонении параметров свежего пара или пара промперегрева на величину: до ±20°C – по температуре и до +0,5 МПа – по давлению свежего пара; при резком, со скоростью более 2°C за минуту изменении температуры свежего пара или пара промперегрева; после 2 минут работы генератора в моторном режиме; при повреждении атмосферных мембран в выхлопном патрубке цилиндра низкого давления; при обнаружении протечек масла.
Системы защиты турбины для мощных паровых турбин предусматривают остановку при достижении следующих величин : при достижении осевого сдвига ротора на –1,5 мм в сторону регулятора или +1,0 мм в сторону генератора (защита срабатывает со срывом вакуума в конденсаторах); при достижении относительного расширения РНД-2 (ротора низкого давления) –3,0 мм (ротор короче корпуса) или +13,0 мм (ротор длиннее корпуса); при повышении температур выхлопных патрубков ЦНД до 90°C и выше; при падении уровня масла в маслобаке на величину 50 мм (необходим немедленный останов турбины).
Работа турбин при полной или частичной постоянной нагрузке предусмотрена в соответствии с заводской инструкцией по эксплуатации. Пуск турбины также регламентируется подробной заводской инструкцией и не допускает отклонений от заданных графиков пуска.
Общие представления об устройстве паровых турбин
Основные технические требования к паровым турбинам и их характеристики
Паровая турбина представляет собою роторный лопаточный двигатель, в котором энергия давления поступающего из котла пара сначала преобразуется в кинетическую энергию пара, вытекающего с большой скоростью из сопел, а затем, на лопатках ротора,- в механическую энергию вращения вала. Сопла это направляющие аппараты, предназначенные для преобразования внутренней энергии пара в кинетическую энергию упорядоченного движения молекул.
Схема простейшей паровой турбины представлена на рис. 1.
Основной частью турбины является ротор, состоящий из вала 1 с насаженным на нем рабочим колесом 2, на котором укреплены рабочие лопатки 3 изогнутой формы. Перед диском с рабочими лопатками имеется сопло 4, из которого пар поступает на рабочие лопатки турбины.
1 – вал; 2 – рабочее колесо; 3 – рабочая лопатка; 4 – сопло
Рисунок 3.1– Принцип действия турбины
Сопло и рабочее колесо составляют одну ступень. На рисунке 1.1, таким образом, представлена принципиальная схема одноступенчатой турбины.
Полученный в парогенераторе перегретый пар при температуре 600 С и давлении 30 МПа по паропроводам передаётся в сопла.
Если перед входом в сопло пар имел некоторую начальную скорость и начальное давление (см. рис. 2), то после выхода из сопла в результате расширения пара происходит увеличение его скорости до значения и уменьшение давления до значения. Скорость входа пара на рабочую лопатку называют абсолютной скоростью. Температура пара также при этом значительно понижается.
После выхода из сопла пар подается на рабочие лопатки турбины. Если турбина активная, то между ее рабочими лопатками расширения пара не происходит, следовательно, давление пара не меняется. Абсолютная скорость движения пара уменьшается с до вследствие вращения турбины со скоростью V. V – это окружная или переносная скорость.
Рис.2 – Схема активной турбины
Конструктивно турбина выполняется в виде нескольких ступеней, каждая из которых состоит из одного венца сопловых лопаток и одного венца рабочих лопаток.
Реактивными турбинами называют такие турбины, у которых расширение пара происходит не только в соплах перед поступлением пара на рабочие лопатки, но и на лопатках самого рабочего колеса. Это достигается тем, что канал, образованный рабочими лопатками выполняется суживающимся.
Изменение параметров пара в реактивной ступени турбины показано на рис. 3. В соплах турбины происходит частичное расширение пара до промежуточного давления.
Дальнейшее расширение пара до давления происходит в каналах между лопатками. Абсолютная скорость пара в сопле увеличивается до значения, а в началах между лопатками уменьшается из-за вращения лопаток до значения.
Рис.3 – Схема работы реактивной турбины
В настоящее время турбины выполняют многоступенчатыми, причем водной и той же турбине могут быть как активные, так и реактивные ступени.
Устройство паровой турбины
Турбина состоит из трех цилиндров (ЦВД, ЦСД и ЦНД), нижние половины корпусов которых обозначены соответственно 39, 24 и18. Каждый из цилиндров состоит из статора, главным элементом которого являются неподвижный корпус, и вращающегося ротора. К полумуфте 12 присоединяется полумуфта ротора электрогенератора (не показан), а к нему — ротор возбудителя. Цепочка из собранных отдельных роторов цилиндров, генератора и возбудителя называется валопроводом. Его длина при большом числе цилиндров (а самое большое их число в современных турбинах — 5) может достигать 80 м.
Рис.4 Устройство паровой турбины
Валопровод вращается во вкладышах 42, 29, 23, 20 и т.д. опорных подшипников скольжения на тонкой масляной пленке Как правило, каждый из роторов размещают на двух опорных подшипниках. Расширяющийся в турбине пар заставляет вращаться каждый из роторов, возникающие на них мощности складываются и достигают на полумуфте 12 максимального значения.
Каждый из роторов помещают в корпус цилиндра (см., например, поз. 24). При больших давлениях (а в современных турбинах оно может достигать 30 МПа » 300 ат) корпус цилиндра (обычно ЦВД) выполняют двухстенным (из внутреннего 35 и внешнего 46 корпусов). Это уменьшает разность давлений на каждый из корпусов, позволяет сделать его стенки более тонкими, облегчает затяжку фланцевых соединений и позволяет турбине при необходимости быстро изменять свою мощность.
Все корпуса в обязательном порядке имеют горизонтальные разъемы 13, необходимые для установки роторов внутри цилиндров при монтаже, а также для легкого доступа внутрь цилиндров при ревизиях и ремонтах. Пар внутри турбины имеет высокую температуру, а ротор вращается во вкладышах на масляной пленке, температура масла которой как по соображениям пожаробезопасности, так и необходимости иметь определенные смазочные свойства, не должна превышать 100 °С (а температура подаваемого и отводимого масла должна быть еще ниже). Поэтому вкладыши подшипников выносят из корпусов цилиндров и размещают их в специальных строениях — опорах Таким образом, вращающиеся концы каждого из роторов соответствующего цилиндра необходимо вывести из невращающегося статора, причем так, чтобы с одной стороны исключить какие-либо (даже малейшие) задевания ротора о статор, а с другой — не допустить значительную утечку пара из цилиндра в зазор между ротором и статором, так как это снижает мощность и экономичность турбины. Поэтому каждый из цилиндров снабжают концевыми уплотнениями (см. поз. 40, 32, 19) специальной конструкции.
Турбина устанавливается в главном корпусе ТЭС на верхней фундаментной плите. В плите выполняются прямоугольные окна по числу цилиндров, в которых размещаются нижние части корпусов цилиндров, а также осуществляется вывод трубопроводов, питающих регенеративные подогреватели, паропроводы свежего и вторично перегретого пара, переходный патрубок к конденсатору.
После изготовления турбина проходит контрольную сборку и опробование на заводе-изготовителе. После этого ее разбирают на более-менее крупные блоки, доводят до хорошего товарного вида, консервируют, упаковывают в деревянные ящики и отправляют для монтажа на ТЭС.
При работе турбины пар из котла по одному или нескольким паропроводам (это зависит от мощности турбины) поступает сначала к главной паровой задвижке, затем к стопорному (одному или нескольким) и, наконец, к регулирующим клапанам (чаще всего — 4). От регулирующих клапанов (на рис. 4 не показаны) пар по перепускным трубам 1 (на рис. 4 их четыре: две из них присоединены к крышке 46 внешнего корпуса ЦВД, а две других подводят пар в нижние половины корпуса) подается в паровпускную камеру 33 внутреннего корпуса ЦВД. Из этой полости пар попадает в проточную часть турбины и, расширяясь, движется к выходной камере ЦВД 38. В этой камере в нижней половине корпуса ЦВД имеются два выходных патрубка 37. К ним приварены паропроводы, направляющие пар в котел для промежуточного перегрева.
Вторично перегретый пар по трубопроводам поступает через стопорный клапан (не показан на рис. 4) к регулирующим клапанам 4, а из них — в паровпускную полость ЦСД 26. Далее пар расширяется в проточной части ЦСД и поступает в его выходной патрубок 22, а из него — в две перепускные трубы 6 (иногда их называют ресиверными), которые подают пар в паровпускную камеру ЦНД 9. ЦВД и ЦСД, ЦНД почти всегда выполняют двухпоточными: попав в камеру 9, пар расходится на два одинаковых потока и, пройдя их, поступает в выходные патрубки ЦНД 14. Из них пар направляется вниз в конденсатор. Перед передней опорой 41 располагается блок регулирования и управления турбиной 44. Его механизм управления 43 позволяет пускать, нагружать, разгружать и останавливать турбину.
Уплотнение представлено на рис. 5.
Рис.5. Лабиринтное уплотнение для валов турбин
В обойме 7, имеющей такую же конструкцию, как и обойма диафрагм выполнена кольцевая расточка 1, в которую вставляются сегменты уплотнений 3 (по три сегмента в каждую половину обоймы). Сегменты имеют тонкие (до 0,3 мм) кольцевые гребни, устанавливаемые по отношению к валу с очень малым зазором (0,5—0,6 мм). Совокупность кольцевых щелей между гребнями 4 и кольцевыми выступами 6 и кольцевых камер между ними называется лабиринтовым уплотнением. Высокое гидравлическое сопротивление, которым оно обладает, обеспечивает малую утечку пара помимо проточной части турбины.
Типичная рабочая лопатка (рис. 6) состоит из трех основных элементов: профильной части 1; хвостовика 2, служащего для крепления лопатки на диске; шипа 6 прямоугольной, круглой или овальной формы, выполняемого на торце профильной части лопатки за одно целое.
Рис.6.Рабочая лопатка ЦВД и ЦСД
Лопатки изготавливаются из нержавеющей стали, содержащей 13 % хрома, методом штамповки и последующего фрезерования и набираются на диске через два специальных колодца, в которые затем устанавливаются замковые лопатки с хвостовиками специальной формы.
Отдельно прокатывают бандажную ленту 7, в которой пробивают отверстия, соответствующие форме шипов и расстоянию между ними. Лента нарезается на куски со строго рассчитанным числом объединяемых лопаток. Бандажная лента надевается на шипы, которые затем расклепываются. Ряд соседних лопаток (обычно от 5 до 14), объединенных бандажной лентой (бандажом), называется пакетом рабочих лопаток. Главная цель пакетирования — обеспечить вибрационную надежность рабочих лопаток (не допустить их поломки от усталости вследствие колебаний). После расклепки шипов на бандажах рабочих лопаток ротор устанавливают на токарный станок и окончательно протачивают гребни уплотнений.
На рис. 6 показана лишь одна из типичных конструкций, которые отличаются большим разнообразием как типов хвостовиков, так и бандажей. В современных конструкциях бандажи фрезеруют заодно с профильной частью (с шириной бандажа, равной шагу лопаток), иногда соединяют рабочие лопатки в пакете сваркой.
Рис.7 Ротор двухпоточного ЦНД мощной турбины
На рис. 7 показан двухпоточный ротор ЦНД в процессе обработки на токарном станке. Первые две ступени имеют ленточные бандажи, а последние ступени — две проволочные связи.
Главным элементом проточной части турбины, определяющим весь ее облик, является рабочая лопатка последней ступени. Чем большую длину она имеет и чем на большем диаметре она установлена (иными словами, чем больше площадь для прохода пара последней ступени), тем более экономичнее турбина. Поэтому история совершенствования турбин — это история создания последних ступеней. В начале 50-х годов ЛМЗ была разработана рабочая лопатка длиной 960 мм для последней ступени со средним диаметром 2,4 м, и на ее базе созданы турбины мощностью 300, 500 и 800 МВт. В конце 70-х была создана новая рабочая лопатка длиной 1200 мм для ступени со средним диаметром 3 м. Это позволило создать новую паровую турбину для ТЭС мощностью 1200 МВт и для АЭС мощностью 1000 МВт.
Рис.8 Опора валопровода
На рис. 8 показана одна из опор валопровода. Основанием 12 нижняя половина корпуса 2 устанавливается на фундаментную раму (на рисунке не показана). В расточку корпуса на колодках 1, 4 и 10 помещается нижняя половина вкладыша 3. Внутренняя поверхность 8 обеих половин вкладыша выполнена цилиндрической или овальной и залита баббитом, — легкоплавким антифрикционным сплавом на основе олова, допускающего вращение ротора на очень низкой частоте вращения даже при отсутствии смазки. Прямо на поверхность вкладыша 8 и на аналогичную поверхность соседнего вкладыша при монтаже турбины укладывается ротор. Сверху его накрывают верхней половиной вкладыша и притягивают к нижней половине шпильками, ввинчиваемыми в отверстия 9. Затем устанавливается крышка корпуса подшипника.
Масло для смазки шеек валов подается насосами из масляного бака, установленного на нижней отметке конденсационного помещения. Размер масляного бака зависит от мощности турбины: чем больше мощность, тем больше цилиндров и, следовательно, роторов и их опор, требующих смазки. Кроме того, с ростом мощности растет диаметр шеек, и эти два обстоятельства требуют большого расхода масла и соответственно масляного бака большой емкости, достигающей 50—60 м3. Для смазки подшипников используется либо специальное (турбинное) минеральное масло, либо синтетические негорючие масла. Последние намного дороже, но зато пожаробезопаснее.
От насосов по трубопроводам масло, пройдя через маслоохладители, поступает к емкостям, располагаемым в крышках подшипника, а из них — к отверстиям 6 и к выборке 7, раздающей масло на всю ширину шейки вала. Масло за счет гидродинамических сил «загоняется» под шейку вала, и таким образом вал «плавает» на масляной пленке, не касаясь баббитовой заливки. Масло, пройдя под шейкой вала, выходит через торцевые зазоры вкладыша и стекает на дно корпуса подшипника, откуда самотеком направляется обратно в масляный бак. Вкладыш опоры показан на рис. 9.
Рис.9 Опорный вкладыш опоры валопровода
Типы паровых турбин и области их использования
Для понимания места и роли паровых турбин рассмотрим их общую классификацию. Из большого разнообразия используемых паровых турбин, прежде всего можно выделить турбины транспортные и стационарные.
Транспортные паровые турбины чаще всего используются для привода гребных винтов крупных судов.
Стационарные паровые турбины — это турбины, сохраняющие при эксплуатации неизменным свое местоположение. В настоящей книге рассматриваются только стационарные паровые турбины.
В свою очередь стационарные паровые турбины можно классифицировать по ряду признаков.
- По назначению различают турбины энергетические, промышленные и вспомогательные.
Энергетические турбины служат для привода электрического генератора, включенного в энергосистему, и отпуска тепла крупным потребителям, например жилым районам, городам и т.д. Их устанавливают на крупных ГРЭС, АЭС и ТЭЦ. Энергетические турбины характеризуются, прежде всего, большой мощностью, а их режим работы — постоянной частотой вращения, определяемой постоянством частоты сети.
Основным производителем энергетических паровых турбин в России является Ленинградский металлический завод (Санкт-Петербург). Он выпускает мощные паровые турбины для ТЭС (мощностью 1200, 800, 500, 300 и 200 МВт), ТЭЦ (мощностью 180, 80 и 50 МВт и менее), АЭС (мощностью 1000 МВт).
Другим крупным производителем энергетических паровых турбин является Турбомоторный завод (ТМЗ, г. Екатеринбург). Он выпускает только теплофикационные турбины (мощностью 250, 185, 140, 100 и 50 МВт и менее).
На ТЭС России установлено достаточно много мощных паровых турбин Харьковского турбинного завода (ХТЗ, Украина) (мощностью 150, 300 и 500 МВт). Им же произведены все паровые турбины, установленные на АЭС России мощностью 220, 500 и 1000 МВт.
Таким образом, в настоящее время в России функционирует всего два производителя мощных паровых турбин. Если говорить о зарубежных производителях турбин, то их число также является небольшим. Большинство из них являются транснациональными объединениями. В Европе главными производителями паровых турбин являются компании Siemens (Германия), Acea Brown Bovery (ABB, германско-швейцарское объединение), GEC-Alsthom (англо-французское объединение), Scoda (Чехия). В США производителями мощных энергетических турбин являются компании General Electric и Westinghouse, в Японии — Hitachi, Toshiba, Mitsubisi. Все перечисленные производители выпускают паровые турбины вплоть до мощности 1000 МВт и выше. Технический уровень некоторых из них не только не уступает нашим производителям, но и превосходит их.
Промышленные турбины также служат для производства тепловой и электрической энергии, однако их главной целью является обслуживание промышленного предприятия, например, металлургического, текстильного, химического, сахароваренного и др. Часто генераторы таких турбин работают на маломощную индивидуальную электрическую сеть, а иногда используются для привода агрегатов с переменной частотой вращения, например воздуходувок доменных печей. Мощность промышленных турбин существенно меньше, чем энергетических. Основным производителем промышленных турбин в России является Калужский турбинный завод (КТЗ).
Вспомогательные турбины используются для обеспечения технологического процесса производства электроэнергии — обычно для привода питательных насосов и воздуходувок котлов.
Питательные насосы энергоблоков мощностью вплоть до 200 МВт приводятся электродвигателями, а мощностью выше — с помощью паровых турбин, питаемых паром из отбора главной турбины. Например, на энергоблоках мощностью 800 и 1200 МВт установлено соответственно по два и три питательных турбонасоса мощностью 17 МВт каждый, на энергоблоках мощностью 250 (для ТЭЦ) и 300 МВт — один питательный турбонасос мощностью 12 МВт; на энергоблоках мощностью 1000 МВт для АЭС используется два питательных насоса мощностью 12 МВт.
Котлы энергоблоков мощностью 800 и 1200 МВт оборудованы соответственно двумя и тремя воздуходувками, привод которых осуществляется также паровыми турбинами мощностью по 6 МВт каждая. Основным производителем вспомогательных паровых турбин в России является КТЗ.
- По виду энергии, получаемой от паровой турбины, их делят на конденсационные и теплофикационные.
В конденсационных турбинах (типа К) пар из последней ступени отводится в конденсатор, они не имеют регулируемых отборов пара, хотя, как правило, имеют много нерегулируемых отборов пара для регенеративного подогрева питательной воды, а иногда и для внешних тепловых потребителей. Главное назначение конденсационных турбин — обеспечивать производство электроэнергии, поэтому они являются основными агрегатами мощных ТЭС и АЭС. Мощность самых крупных конденсационных турбоагрегатов достигает 1000—1500 МВт.
Теплофикационные турбины имеют один или несколько регулируемых отборов пара, в которых поддерживается заданное давление. Они предназначены для выработки тепловой и электрической энергии, и мощность самой крупной из них составляет 250 МВт. Теплофикационная турбина может выполняться с конденсацией пара и без нее. В первом случае она может иметь отопительные отборы пара (турбины типа Т) для нагрева сетевой воды для обогрева зданий, предприятий и т.д., или производственный отбор пара (турбины типа П) для технологических нужд промышленных предприятий, или тот и другой отборы (турбины типа ПТ и ПР). Во втором случае турбина носит название турбины с противодавлением (турбины типа Р). В ней пар из последней ступени направляется не в конденсатор, а обычно производственному потребителю. Таким образом, главным назначением турбины с противодавлением является производство пара заданного давления (в пределах 0,3—3 МПа). Турбина с противодавлением может также иметь и регулируемый теплофикационный или промышленный отбор пара, и тогда она относится к типу ТР или ПР.
Теплофикационные турбины с отопительным отбором пара (типа Т) спроектированы так, чтобы при максимальной теплофикационной нагрузке ступени, расположенные за зоной отбора, мощности не вырабатывали. В последние годы ряд турбин проектируются так, что даже при максимальной нагрузке последние ступени вырабатывают мощность. Такие турбины относятся к типу ТК.
- По используемым начальным параметрам пара паровые турбины можно разделить на турбины докритического и сверхкритического начального давления, перегретого и насыщенного пара, без промежуточного перегрева и с промежуточным перегревом пара.
Как уже известно критическое давление для пара составляет примерно 22 МПа, поэтому все турбины, начальное давление пара перед которыми меньше этого значения, относятся к паровым турбинам докритического начального давления. В России стандартное докритическое давление для паровых турбин выбрано равным 130 ат (12,8 МПа), кроме того, имеется определенный процент турбин на начальное давление 90 ат (8,8 МПа). На докритические параметры выполняются все паровые турбины для АЭС и ТЭЦ (кроме теплофикационной турбины мощностью 250 МВт), а также турбины мощностью менее 300 МВт для ТЭС. Докритическое начальное давление зарубежных паровых турбин обычно составляет 16—17 МПа, а максимальная единичная мощность достигает 600—700 МВт.
Все мощные конденсационные энергоблоки (300, 500, 800, 1200 МВт), а также теплофикационный энергоблок мощностью 250 МВт выполняют на сверхкритические параметры пара (СКД) — 240 ат (23,5 МПа) и 540 °С. Переход от докритических параметров пара к СКД позволяет экономить 3—4 % топлива.
Все турбины ТЭС и ТЭЦ работают перегретым паром, а АЭС — насыщенным (с небольшой степенью влажности).
Все мощные конденсационные турбины на докритические и сверхкритические параметры пара выполняют с промежуточным перегревом. Из теплофикационных турбин только турбина ЛМЗ на докритические параметры мощностью 180 МВт и турбина ТМЗ на СКД мощностью 250 МВт имеют промежуточный перегрев. Устаревшие конденсационные турбины мощностью 100 МВт и менее и многочисленные теплофикационные паровые турбины вплоть до мощности 185 МВт строятся без промперегрева.
- По зоне использования турбин в графике электрической нагрузки паровые турбины можно разделить на базовые и полупиковые. Базовые турбины работают постоянно при номинальной нагрузке или близкой к ней. Они проектируются так, чтобы и турбина, и турбоустановка имели максимально возможную экономичность. К этому типу турбин следует, безусловно, отнести атомные и теплофикационные турбины. Полупиковыетурбины создаются для работы с периодическими остановками на конец недели (с ночи пятницы до утра в понедельник) и ежесуточно (на ночь). Полупиковые турбины (и турбоустановки) с учетом их малого числа часов работы в году выполняют более простыми и соответственно более дешевыми (на сниженные параметры пара, с меньшим числом цилиндров). Электроэнергетика России в силу ряда причин всегда страдала от недостатка в энергосистеме полупиковых мощностей. Примерно 25 лет назад ЛМЗ спроектировал полупиковую конденсационную турбину мощностью 500 МВт на параметры 12,8 МПа, 510 °С/510 °С. Головной образец этой турбины предполагалось установить на Лукомльской ГРЭС (б. Белоруссия). Однако до сих пор ни одной специальной полупиковой турбины в России не работает. Вместе с тем в Японии и США работают десятки полупиковых турбин упрощенной конструкции.
- По конструктивным особенностям паровые турбины можно классифицировать по числу цилиндров, частоте вращения и числу валопроводов.
По числу цилиндров различают турбины одно- и многоцилиндровые. Количество цилиндров определяется объемным пропуском пара в конце процесса расширения. Чем меньше плотность пара, т.е. меньше его конечное давление, и чем больше мощность турбины, т.е. больше массовый расход, тем больше объемный пропуск и соответственно требуемая площадь для прохода пара через рабочие лопатки последней ступени. Однако если рабочие лопатки делать длиннее, а радиус их вращения больше, то центробежные силы, отрывающие профильную часть лопатки, могут возрасти настолько, что лопатка оторвется. Поэтому с увеличением мощности сначала переходят на двухпоточный ЦНД, а затем увеличивают их число. Конденсационные турбины можно выполнить одноцилиндровыми вплоть до мощности 50—60 МВт, двухцилиндровыми — до 100—150 МВт, трехцилиндровыми — до 300 МВт, четырехцилиндровыми — до 500 МВт, пятицилиндровыми — вплоть до 1300 МВт.
По частоте вращения турбины делятся на быстроходные и тихоходные. Быстроходные турбины имеют частоту вращения 3000 об/мин = 50 об/с. Они приводят электрогенератор, ротор которого имеет два магнитных полюса, и поэтому частота вырабатываемого им тока равна 50 Гц. На эту частоту строят большинство паровых турбин для ТЭС, ТЭЦ и частично для АЭС в нашей стране и почти во всем мире. В Северной Америке и на части территории Японии быстроходные турбины строят на частоту вращения 3600 об/мин = 60 об/с, так как там принятая частота сети равна 60 Гц.
Ранее в говорилось о том, что поскольку из-за низких начальных параметров работоспособность пара в турбинах АЭС мала, а снижение капитальных затрат требует увеличения мощности, т.е. массы пропускаемого пара, то объемный расход на выходе из турбины оказывается столь значительным, что оказывается целесообразным переход на меньшую частоту вращения. Так как число магнитных полюсов в электрогенераторе должно быть целым и четным, то переход на использование четырехполюсного электрогенератора и получения той же частоты сети, что и при двухполюсном электрогенераторе, требует снижения частоты вдвое. Таким образом, тихоходные турбины в нашей стране имеют частоту вращения 1500 об/мин = 25 об/с.
Рис.10 Тихоходная турбина насыщенного пара мощностью 1160 МВт для американской АЭС
На рис. 10 показана тихоходная атомная турбина фирмы ABB мощностью 1160 МВт на частоту вращения 30 об/с. Гигантские размеры турбины хорошо видны в сравнении с фигурой человека, стоящего у средней опоры ее валопровода. Турбина не имеет ЦСД, и пар из ЦВД направляется в два горизонтальных сепаратора-пароперегревателя (СПП), а из них — раздается на три двухпоточных ЦНД. По такой же схеме на частоту вращения 25 об/с построены энергоблоки мощностью 1000 МВт на Балаковской и Ростовской АЭС.
Для АЭС, построенных для теплых климатических условий, т.е. для высокой температуры охлаждающей воды и соответственно высокого давления в конденсаторе), можно строить и быстроходные атомные турбины (рис. 11). Пар к ЦВД турбины поступает из реакторного отделения по четырем паропроводам 11. Пройдя ЦВД, пар поступает к СПП 10 вертикального типа, а после них с помощью ресивера 3 раздается на три одинаковых двухпоточных ЦНД 4. Под каждым ЦНД установлен свой конденсатор, также хорошо видный на макете.
По числу валопроводов различают турбины одновальные (имеющие один валопровод — соединенные муфтами роторы отдельных цилиндров и генератора) и двухвальные(имеющие два валопровода каждый со своим генератором и связанные только потоком пара). На российских тепловых электростанциях используют только одновальные турбины.В начале 70-х годов на Славянской ГРЭС на Украине построена единственная двухвальная турбина мощностью 800 МВт, да и то потому, что в то время не было электрогенератора мощностью 800 МВт.
Рис.11 Быстроходная атомная турбина мощностью 1093 МВт для испанской АЭС (“ Трилло”), построенная фирмой Siemens
Для обозначения типов турбин ГОСТ предусматривает специальную маркировку, состоящую из буквенной и числовой частей. Буквенная часть указывает тип турбины, следующее за ней число — номинальную мощность турбины в мегаваттах. Если необходимо указать и максимальную мощность турбины, то ее значение приводят через косую черту. Следующее число указывает номинальное давление пара перед турбиной в МПа: для теплофикационных турбин далее через косую черту указывают давление в отборах или противодавление в МПа. Наконец, последняя цифра, если она имеется, указывает номер модификации турбины, принятый на заводе-изготовителе.
Приведем несколько примеров обозначений турбин.
Турбина К-210-12,8-3 — типа К, номинальной мощностью 210 МВт с начальным абсолютным давлением пара 12,8 МПа (130 кгс/см2), третьей модификации.
Трубина П-6-3,4/0,5 — типа П, номинальной мощностью 6 МВт, с начальным абсолютным давлением пара 3,4 МПа и абсолютным давлением отбираемого пара 0,5 МПа.
Турбина Т-110/120-12,8 — типа Т, номинальной мощностью 110 МВт и максимальной мощностью 120 МВт, с начальным абсолютным давлением пара 12,8 МПа.
Турбина ПТ-25/30-8,8/1 — типа ПТ, номинальной мощностью 25 МВт и максимальной мощностью 30 МВт, с начальным абсолютным давлением пара 8,8 МПа (90 ат) и абсолютным давлением отбираемого пара 1 МПа.
Турбина Р-100/105-12,8/1,45 — типа Р, номинальной мощностью 100 МВт максимальной мощностью 105 МВт, с начальным абсолютным давлением пара 12,8 МПа и абсолютным противодавлением 1,45 МПа.
Турбина ПР-12/15-8,8/1,45/0,7 — типа ПР, номинальной мощностью 12 МВт и максимальной мощностью 15 МВт, с начальным абсолютным давлением 8,8 МПа, давлением в отборе 1,45 МПа и противодавлением 0,7 МПа.
Основные технические требования к паровым турбинам и их характеристики
Для того чтобы увидеть, насколько совершенной машиной является паровая турбина, достаточно рассмотреть технические требования, предъявляемые к ней. Они сформулированы в государственных стандартах (ГОСТ). Здесь мы остановимся только на наиболее важных из них.
Прежде всего, к турбине предъявляется ряд требований, которые можно охватить одним термином — надежность. Надежность технического объекта — это его свойство выполнять заданные функции в заданном объеме при определенных условиях функционирования. Применительно к паровой турбине надежность — это бесперебойная выработка мощности при предусмотренных затратах топлива и установленной системе эксплуатации, технического обслуживания и ремонтов, а также недопущения ситуаций, опасных для людей и окружающей среды.
Важно подчеркнуть, что понятие надежности включает в себя и понятие экономичности. Бесперебойно работающая турбина, работающая с низкой экономичностью из-за износа или с ограничением мощности из-за внутренних неполадок, не может считаться надежной. Надежность — это комплексное свойство, характеризуемое такими подсвойствами, как безотказность, долговечность, ремонтопригодность, сохраняемость, управляемость, живучесть, безопасность. Не вдаваясь в строгие определения этих подсвойств, отметим главные из них.
Безотказность — это свойство турбины непрерывно сохранять работоспособное состояние в течение некоторой наработки. Средняя наработка на отказ для турбин ТЭС мощностью 500 МВт и более должна быть не менее 6250 ч, а меньшей мощности — не менее 7000 ч, а для турбин АЭС — не менее 6000 ч. Если учесть, что в календарном году 8760 ч и что какое-то время турбина не работает (например, по указанию диспетчера энергосистемы), то это означает, что отказы по вине турбины в среднем должны происходить не чаще 1 раза в год.
Полный установленный срок службы турбины ТЭС должен быть не менее 40 лет, а турбин АЭС — не менее 30 лет. При этом оговаривается два важных обстоятельства. Первое: этот срок службы не относится к быстроизнашивающимся деталям, например, рабочим лопаткам, уплотнениям, крепежным деталям. Для таких деталей важен средний срок службы до капитального ремонта (межремонтный период). В соответствии с ГОСТ он должен быть не менее 6 лет (кроме того, на ТЭС и АЭС реализуется плановая система текущих и планово-предупредительных ремонтов).
Для турбин ТЭС, а точнее для их деталей, работающих при температуре свыше 450 °С, кроме такого показателя долговечности, как срок службы, вводится другой показатель — ресурс — суммарная наработка турбины от начала эксплуатации до достижения предельного состояния. На этапе проектирования предельное состояние определяется как назначенный ресурс. По определению — это ресурс, при достижении которого эксплуатация турбины должна быть прекращена независимо от ее технического состояния. На самом деле при достижении назначенного ресурса турбина может сохранить значительную дополнительную работоспособность (остаточный ресурс) и, учитывая ее высокую стоимость, срок работы турбины продляют. Учитывая нелогичность применительно к турбине термина «назначенный ресурс», стали употреблять термин «расчетный ресурс». Таким образом, расчетный (назначенный) ресурс — это наработка турбины, которая гарантируется заводом-изготовителем; при ее достижении должен быть рассмотрен вопрос о ее дальнейшей эксплуатации.
ГОСТ не регламентирует расчетного ресурса (он должен быть установлен в технических условиях или техническом задании на ее проектирование в каждом конкретном случае). Долгие годы расчетный ресурс составлял 100 тыс. ч, сейчас — как правило, 200 тыс. ч. Важнейшим требованием к турбине является высокая экономичность. Коэффициент полезного действия турбины оценивается по КПД ее цилиндров.
Коэффициент полезного действия цилиндра характеризуется той долей работоспособности пара, которую удалось преобразовать в механическую энергию. Наивысшую экономичность имеет ЦСД: в хороших турбинах он составляет 90—94 %. Коэффициент полезного действия ЦВД и ЦНД существенно меньше и в среднем составляет 84—86 %. Это уменьшение обусловлено существенно более сложным характером течения пара в решетках очень малой (несколько десятков миллиметров в первых ступенях ЦВД) и очень большой (1 м и более) в последних ступенях ЦНД высотой решеток. Рассчитать это течение и подобрать под него профили лопаток затруднительно даже при современных вычислительных средствах. Кроме того, значительная часть проточной части ЦНД работает влажным паром, капли влаги имеют скорость существенно меньшую, чем пар, и оказывают на вращающиеся рабочие лопатки тормозящее действие.
Кроме приведенных технических требований ГОСТ содержит многочисленные другие требования, в частности, к системе защиты турбины при возникновении аварийных ситуаций, к маневренности (диапазон длительной работы — обычно 30—100 % номинальной мощности; продолжительности пуска и остановки, число возможных пусков и т.д.), к системе регулирования и управления турбиной, к ремонтопригодности и безопасности (пожаробезопасности, уровня вибрации, шума и т.д.), методов контроля параметров рабочих сред (пара, масла, конденсата), транспортирования и хранения.
Источник: Языки программирования — Life-prog
1 – вал; 2 – рабочее колесо; 3 – рабочая лопатка; 4 – сопло
Рисунок 3.1– Принцип действия турбины
Сопло и рабочее колесо составляют одну ступень. На рисунке 1.1, таким образом, представлена принципиальная схема одноступенчатой турбины.
Полученный в парогенераторе перегретый пар при температуре 600 С и давлении 30 МПа по паропроводам передаётся в сопла.
Если перед входом в сопло пар имел некоторую начальную скорость и начальное давление (см. рис. 2), то после выхода из сопла в результате расширения пара происходит увеличение его скорости до значения и уменьшение давления до значения. Скорость входа пара на рабочую лопатку называют абсолютной скоростью. Температура пара также при этом значительно понижается.
После выхода из сопла пар подается на рабочие лопатки турбины. Если турбина активная, то между ее рабочими лопатками расширения пара не происходит, следовательно, давление пара не меняется. Абсолютная скорость движения пара уменьшается с до вследствие вращения турбины со скоростью V. V – это окружная или переносная скорость.
Рис.2 – Схема активной турбины
Конструктивно турбина выполняется в виде нескольких ступеней, каждая из которых состоит из одного венца сопловых лопаток и одного венца рабочих лопаток.
Реактивными турбинами называют такие турбины, у которых расширение пара происходит не только в соплах перед поступлением пара на рабочие лопатки, но и на лопатках самого рабочего колеса. Это достигается тем, что канал, образованный рабочими лопатками выполняется суживающимся.
Изменение параметров пара в реактивной ступени турбины показано на рис. 3. В соплах турбины происходит частичное расширение пара до промежуточного давления.
Дальнейшее расширение пара до давления происходит в каналах между лопатками. Абсолютная скорость пара в сопле увеличивается до значения, а в началах между лопатками уменьшается из-за вращения лопаток до значения.
Рис.3 – Схема работы реактивной турбины
В настоящее время турбины выполняют многоступенчатыми, причем водной и той же турбине могут быть как активные, так и реактивные ступени.
Устройство паровой турбины
Турбина состоит из трех цилиндров (ЦВД, ЦСД и ЦНД), нижние половины корпусов которых обозначены соответственно 39, 24 и18. Каждый из цилиндров состоит из статора, главным элементом которого являются неподвижный корпус, и вращающегося ротора. К полумуфте 12 присоединяется полумуфта ротора электрогенератора (не показан), а к нему — ротор возбудителя. Цепочка из собранных отдельных роторов цилиндров, генератора и возбудителя называется валопроводом. Его длина при большом числе цилиндров (а самое большое их число в современных турбинах — 5) может достигать 80 м.
Рис.4 Устройство паровой турбины
Валопровод вращается во вкладышах 42, 29, 23, 20 и т.д. опорных подшипников скольжения на тонкой масляной пленке Как правило, каждый из роторов размещают на двух опорных подшипниках. Расширяющийся в турбине пар заставляет вращаться каждый из роторов, возникающие на них мощности складываются и достигают на полумуфте 12 максимального значения.
Каждый из роторов помещают в корпус цилиндра (см., например, поз. 24). При больших давлениях (а в современных турбинах оно может достигать 30 МПа » 300 ат) корпус цилиндра (обычно ЦВД) выполняют двухстенным (из внутреннего 35 и внешнего 46 корпусов). Это уменьшает разность давлений на каждый из корпусов, позволяет сделать его стенки более тонкими, облегчает затяжку фланцевых соединений и позволяет турбине при необходимости быстро изменять свою мощность.
Все корпуса в обязательном порядке имеют горизонтальные разъемы 13, необходимые для установки роторов внутри цилиндров при монтаже, а также для легкого доступа внутрь цилиндров при ревизиях и ремонтах. Пар внутри турбины имеет высокую температуру, а ротор вращается во вкладышах на масляной пленке, температура масла которой как по соображениям пожаробезопасности, так и необходимости иметь определенные смазочные свойства, не должна превышать 100 °С (а температура подаваемого и отводимого масла должна быть еще ниже). Поэтому вкладыши подшипников выносят из корпусов цилиндров и размещают их в специальных строениях — опорах Таким образом, вращающиеся концы каждого из роторов соответствующего цилиндра необходимо вывести из невращающегося статора, причем так, чтобы с одной стороны исключить какие-либо (даже малейшие) задевания ротора о статор, а с другой — не допустить значительную утечку пара из цилиндра в зазор между ротором и статором, так как это снижает мощность и экономичность турбины. Поэтому каждый из цилиндров снабжают концевыми уплотнениями (см. поз. 40, 32, 19) специальной конструкции.
Турбина устанавливается в главном корпусе ТЭС на верхней фундаментной плите. В плите выполняются прямоугольные окна по числу цилиндров, в которых размещаются нижние части корпусов цилиндров, а также осуществляется вывод трубопроводов, питающих регенеративные подогреватели, паропроводы свежего и вторично перегретого пара, переходный патрубок к конденсатору.
После изготовления турбина проходит контрольную сборку и опробование на заводе-изготовителе. После этого ее разбирают на более-менее крупные блоки, доводят до хорошего товарного вида, консервируют, упаковывают в деревянные ящики и отправляют для монтажа на ТЭС.
При работе турбины пар из котла по одному или нескольким паропроводам (это зависит от мощности турбины) поступает сначала к главной паровой задвижке, затем к стопорному (одному или нескольким) и, наконец, к регулирующим клапанам (чаще всего — 4). От регулирующих клапанов (на рис. 4 не показаны) пар по перепускным трубам 1 (на рис. 4 их четыре: две из них присоединены к крышке 46 внешнего корпуса ЦВД, а две других подводят пар в нижние половины корпуса) подается в паровпускную камеру 33 внутреннего корпуса ЦВД. Из этой полости пар попадает в проточную часть турбины и, расширяясь, движется к выходной камере ЦВД 38. В этой камере в нижней половине корпуса ЦВД имеются два выходных патрубка 37. К ним приварены паропроводы, направляющие пар в котел для промежуточного перегрева.
Вторично перегретый пар по трубопроводам поступает через стопорный клапан (не показан на рис. 4) к регулирующим клапанам 4, а из них — в паровпускную полость ЦСД 26. Далее пар расширяется в проточной части ЦСД и поступает в его выходной патрубок 22, а из него — в две перепускные трубы 6 (иногда их называют ресиверными), которые подают пар в паровпускную камеру ЦНД 9. ЦВД и ЦСД, ЦНД почти всегда выполняют двухпоточными: попав в камеру 9, пар расходится на два одинаковых потока и, пройдя их, поступает в выходные патрубки ЦНД 14. Из них пар направляется вниз в конденсатор. Перед передней опорой 41 располагается блок регулирования и управления турбиной 44. Его механизм управления 43 позволяет пускать, нагружать, разгружать и останавливать турбину.
Уплотнение представлено на рис. 5.
Рис.5. Лабиринтное уплотнение для валов турбин
В обойме 7, имеющей такую же конструкцию, как и обойма диафрагм выполнена кольцевая расточка 1, в которую вставляются сегменты уплотнений 3 (по три сегмента в каждую половину обоймы). Сегменты имеют тонкие (до 0,3 мм) кольцевые гребни, устанавливаемые по отношению к валу с очень малым зазором (0,5—0,6 мм). Совокупность кольцевых щелей между гребнями 4 и кольцевыми выступами 6 и кольцевых камер между ними называется лабиринтовым уплотнением. Высокое гидравлическое сопротивление, которым оно обладает, обеспечивает малую утечку пара помимо проточной части турбины.
Типичная рабочая лопатка (рис. 6) состоит из трех основных элементов: профильной части 1; хвостовика 2, служащего для крепления лопатки на диске; шипа 6 прямоугольной, круглой или овальной формы, выполняемого на торце профильной части лопатки за одно целое.
Рис.6.Рабочая лопатка ЦВД и ЦСД
Лопатки изготавливаются из нержавеющей стали, содержащей 13 % хрома, методом штамповки и последующего фрезерования и набираются на диске через два специальных колодца, в которые затем устанавливаются замковые лопатки с хвостовиками специальной формы.
Отдельно прокатывают бандажную ленту 7, в которой пробивают отверстия, соответствующие форме шипов и расстоянию между ними. Лента нарезается на куски со строго рассчитанным числом объединяемых лопаток. Бандажная лента надевается на шипы, которые затем расклепываются. Ряд соседних лопаток (обычно от 5 до 14), объединенных бандажной лентой (бандажом), называется пакетом рабочих лопаток. Главная цель пакетирования — обеспечить вибрационную надежность рабочих лопаток (не допустить их поломки от усталости вследствие колебаний). После расклепки шипов на бандажах рабочих лопаток ротор устанавливают на токарный станок и окончательно протачивают гребни уплотнений.
На рис. 6 показана лишь одна из типичных конструкций, которые отличаются большим разнообразием как типов хвостовиков, так и бандажей. В современных конструкциях бандажи фрезеруют заодно с профильной частью (с шириной бандажа, равной шагу лопаток), иногда соединяют рабочие лопатки в пакете сваркой.
Рис.7 Ротор двухпоточного ЦНД мощной турбины
На рис. 7 показан двухпоточный ротор ЦНД в процессе обработки на токарном станке. Первые две ступени имеют ленточные бандажи, а последние ступени — две проволочные связи.
Главным элементом проточной части турбины, определяющим весь ее облик, является рабочая лопатка последней ступени. Чем большую длину она имеет и чем на большем диаметре она установлена (иными словами, чем больше площадь для прохода пара последней ступени), тем более экономичнее турбина. Поэтому история совершенствования турбин — это история создания последних ступеней. В начале 50-х годов ЛМЗ была разработана рабочая лопатка длиной 960 мм для последней ступени со средним диаметром 2,4 м, и на ее базе созданы турбины мощностью 300, 500 и 800 МВт. В конце 70-х была создана новая рабочая лопатка длиной 1200 мм для ступени со средним диаметром 3 м. Это позволило создать новую паровую турбину для ТЭС мощностью 1200 МВт и для АЭС мощностью 1000 МВт.
Рис.8 Опора валопровода
На рис. 8 показана одна из опор валопровода. Основанием 12 нижняя половина корпуса 2 устанавливается на фундаментную раму (на рисунке не показана). В расточку корпуса на колодках 1, 4 и 10 помещается нижняя половина вкладыша 3. Внутренняя поверхность 8 обеих половин вкладыша выполнена цилиндрической или овальной и залита баббитом, — легкоплавким антифрикционным сплавом на основе олова, допускающего вращение ротора на очень низкой частоте вращения даже при отсутствии смазки. Прямо на поверхность вкладыша 8 и на аналогичную поверхность соседнего вкладыша при монтаже турбины укладывается ротор. Сверху его накрывают верхней половиной вкладыша и притягивают к нижней половине шпильками, ввинчиваемыми в отверстия 9. Затем устанавливается крышка корпуса подшипника.
Масло для смазки шеек валов подается насосами из масляного бака, установленного на нижней отметке конденсационного помещения. Размер масляного бака зависит от мощности турбины: чем больше мощность, тем больше цилиндров и, следовательно, роторов и их опор, требующих смазки. Кроме того, с ростом мощности растет диаметр шеек, и эти два обстоятельства требуют большого расхода масла и соответственно масляного бака большой емкости, достигающей 50—60 м3. Для смазки подшипников используется либо специальное (турбинное) минеральное масло, либо синтетические негорючие масла. Последние намного дороже, но зато пожаробезопаснее.
От насосов по трубопроводам масло, пройдя через маслоохладители, поступает к емкостям, располагаемым в крышках подшипника, а из них — к отверстиям 6 и к выборке 7, раздающей масло на всю ширину шейки вала. Масло за счет гидродинамических сил «загоняется» под шейку вала, и таким образом вал «плавает» на масляной пленке, не касаясь баббитовой заливки. Масло, пройдя под шейкой вала, выходит через торцевые зазоры вкладыша и стекает на дно корпуса подшипника, откуда самотеком направляется обратно в масляный бак. Вкладыш опоры показан на рис. 9.
Рис.9 Опорный вкладыш опоры валопровода
Типы паровых турбин и области их использования
Для понимания места и роли паровых турбин рассмотрим их общую классификацию. Из большого разнообразия используемых паровых турбин, прежде всего можно выделить турбины транспортные и стационарные.
Транспортные паровые турбины чаще всего используются для привода гребных винтов крупных судов.
Стационарные паровые турбины — это турбины, сохраняющие при эксплуатации неизменным свое местоположение. В настоящей книге рассматриваются только стационарные паровые турбины.
В свою очередь стационарные паровые турбины можно классифицировать по ряду признаков.
- По назначению различают турбины энергетические, промышленные и вспомогательные.
Энергетические турбины служат для привода электрического генератора, включенного в энергосистему, и отпуска тепла крупным потребителям, например жилым районам, городам и т.д. Их устанавливают на крупных ГРЭС, АЭС и ТЭЦ. Энергетические турбины характеризуются, прежде всего, большой мощностью, а их режим работы — постоянной частотой вращения, определяемой постоянством частоты сети.
Основным производителем энергетических паровых турбин в России является Ленинградский металлический завод (Санкт-Петербург). Он выпускает мощные паровые турбины для ТЭС (мощностью 1200, 800, 500, 300 и 200 МВт), ТЭЦ (мощностью 180, 80 и 50 МВт и менее), АЭС (мощностью 1000 МВт).
Другим крупным производителем энергетических паровых турбин является Турбомоторный завод (ТМЗ, г. Екатеринбург). Он выпускает только теплофикационные турбины (мощностью 250, 185, 140, 100 и 50 МВт и менее).
На ТЭС России установлено достаточно много мощных паровых турбин Харьковского турбинного завода (ХТЗ, Украина) (мощностью 150, 300 и 500 МВт). Им же произведены все паровые турбины, установленные на АЭС России мощностью 220, 500 и 1000 МВт.
Таким образом, в настоящее время в России функционирует всего два производителя мощных паровых турбин. Если говорить о зарубежных производителях турбин, то их число также является небольшим. Большинство из них являются транснациональными объединениями. В Европе главными производителями паровых турбин являются компании Siemens (Германия), Acea Brown Bovery (ABB, германско-швейцарское объединение), GEC-Alsthom (англо-французское объединение), Scoda (Чехия). В США производителями мощных энергетических турбин являются компании General Electric и Westinghouse, в Японии — Hitachi, Toshiba, Mitsubisi. Все перечисленные производители выпускают паровые турбины вплоть до мощности 1000 МВт и выше. Технический уровень некоторых из них не только не уступает нашим производителям, но и превосходит их.
Промышленные турбины также служат для производства тепловой и электрической энергии, однако их главной целью является обслуживание промышленного предприятия, например, металлургического, текстильного, химического, сахароваренного и др. Часто генераторы таких турбин работают на маломощную индивидуальную электрическую сеть, а иногда используются для привода агрегатов с переменной частотой вращения, например воздуходувок доменных печей. Мощность промышленных турбин существенно меньше, чем энергетических. Основным производителем промышленных турбин в России является Калужский турбинный завод (КТЗ).
Вспомогательные турбины используются для обеспечения технологического процесса производства электроэнергии — обычно для привода питательных насосов и воздуходувок котлов.
Питательные насосы энергоблоков мощностью вплоть до 200 МВт приводятся электродвигателями, а мощностью выше — с помощью паровых турбин, питаемых паром из отбора главной турбины. Например, на энергоблоках мощностью 800 и 1200 МВт установлено соответственно по два и три питательных турбонасоса мощностью 17 МВт каждый, на энергоблоках мощностью 250 (для ТЭЦ) и 300 МВт — один питательный турбонасос мощностью 12 МВт; на энергоблоках мощностью 1000 МВт для АЭС используется два питательных насоса мощностью 12 МВт.
Котлы энергоблоков мощностью 800 и 1200 МВт оборудованы соответственно двумя и тремя воздуходувками, привод которых осуществляется также паровыми турбинами мощностью по 6 МВт каждая. Основным производителем вспомогательных паровых турбин в России является КТЗ.
- По виду энергии, получаемой от паровой турбины, их делят на конденсационные и теплофикационные.
В конденсационных турбинах (типа К) пар из последней ступени отводится в конденсатор, они не имеют регулируемых отборов пара, хотя, как правило, имеют много нерегулируемых отборов пара для регенеративного подогрева питательной воды, а иногда и для внешних тепловых потребителей. Главное назначение конденсационных турбин — обеспечивать производство электроэнергии, поэтому они являются основными агрегатами мощных ТЭС и АЭС. Мощность самых крупных конденсационных турбоагрегатов достигает 1000—1500 МВт.
Теплофикационные турбины имеют один или несколько регулируемых отборов пара, в которых поддерживается заданное давление. Они предназначены для выработки тепловой и электрической энергии, и мощность самой крупной из них составляет 250 МВт. Теплофикационная турбина может выполняться с конденсацией пара и без нее. В первом случае она может иметь отопительные отборы пара (турбины типа Т) для нагрева сетевой воды для обогрева зданий, предприятий и т.д., или производственный отбор пара (турбины типа П) для технологических нужд промышленных предприятий, или тот и другой отборы (турбины типа ПТ и ПР). Во втором случае турбина носит название турбины с противодавлением (турбины типа Р). В ней пар из последней ступени направляется не в конденсатор, а обычно производственному потребителю. Таким образом, главным назначением турбины с противодавлением является производство пара заданного давления (в пределах 0,3—3 МПа). Турбина с противодавлением может также иметь и регулируемый теплофикационный или промышленный отбор пара, и тогда она относится к типу ТР или ПР.
Теплофикационные турбины с отопительным отбором пара (типа Т) спроектированы так, чтобы при максимальной теплофикационной нагрузке ступени, расположенные за зоной отбора, мощности не вырабатывали. В последние годы ряд турбин проектируются так, что даже при максимальной нагрузке последние ступени вырабатывают мощность. Такие турбины относятся к типу ТК.
- По используемым начальным параметрам пара паровые турбины можно разделить на турбины докритического и сверхкритического начального давления, перегретого и насыщенного пара, без промежуточного перегрева и с промежуточным перегревом пара.
Как уже известно критическое давление для пара составляет примерно 22 МПа, поэтому все турбины, начальное давление пара перед которыми меньше этого значения, относятся к паровым турбинам докритического начального давления. В России стандартное докритическое давление для паровых турбин выбрано равным 130 ат (12,8 МПа), кроме того, имеется определенный процент турбин на начальное давление 90 ат (8,8 МПа). На докритические параметры выполняются все паровые турбины для АЭС и ТЭЦ (кроме теплофикационной турбины мощностью 250 МВт), а также турбины мощностью менее 300 МВт для ТЭС. Докритическое начальное давление зарубежных паровых турбин обычно составляет 16—17 МПа, а максимальная единичная мощность достигает 600—700 МВт.
Все мощные конденсационные энергоблоки (300, 500, 800, 1200 МВт), а также теплофикационный энергоблок мощностью 250 МВт выполняют на сверхкритические параметры пара (СКД) — 240 ат (23,5 МПа) и 540 °С. Переход от докритических параметров пара к СКД позволяет экономить 3—4 % топлива.
Все турбины ТЭС и ТЭЦ работают перегретым паром, а АЭС — насыщенным (с небольшой степенью влажности).
Все мощные конденсационные турбины на докритические и сверхкритические параметры пара выполняют с промежуточным перегревом. Из теплофикационных турбин только турбина ЛМЗ на докритические параметры мощностью 180 МВт и турбина ТМЗ на СКД мощностью 250 МВт имеют промежуточный перегрев. Устаревшие конденсационные турбины мощностью 100 МВт и менее и многочисленные теплофикационные паровые турбины вплоть до мощности 185 МВт строятся без промперегрева.
- По зоне использования турбин в графике электрической нагрузки паровые турбины можно разделить на базовые и полупиковые. Базовые турбины работают постоянно при номинальной нагрузке или близкой к ней. Они проектируются так, чтобы и турбина, и турбоустановка имели максимально возможную экономичность. К этому типу турбин следует, безусловно, отнести атомные и теплофикационные турбины. Полупиковыетурбины создаются для работы с периодическими остановками на конец недели (с ночи пятницы до утра в понедельник) и ежесуточно (на ночь). Полупиковые турбины (и турбоустановки) с учетом их малого числа часов работы в году выполняют более простыми и соответственно более дешевыми (на сниженные параметры пара, с меньшим числом цилиндров). Электроэнергетика России в силу ряда причин всегда страдала от недостатка в энергосистеме полупиковых мощностей. Примерно 25 лет назад ЛМЗ спроектировал полупиковую конденсационную турбину мощностью 500 МВт на параметры 12,8 МПа, 510 °С/510 °С. Головной образец этой турбины предполагалось установить на Лукомльской ГРЭС (б. Белоруссия). Однако до сих пор ни одной специальной полупиковой турбины в России не работает. Вместе с тем в Японии и США работают десятки полупиковых турбин упрощенной конструкции.
- По конструктивным особенностям паровые турбины можно классифицировать по числу цилиндров, частоте вращения и числу валопроводов.
По числу цилиндров различают турбины одно- и многоцилиндровые. Количество цилиндров определяется объемным пропуском пара в конце процесса расширения. Чем меньше плотность пара, т.е. меньше его конечное давление, и чем больше мощность турбины, т.е. больше массовый расход, тем больше объемный пропуск и соответственно требуемая площадь для прохода пара через рабочие лопатки последней ступени. Однако если рабочие лопатки делать длиннее, а радиус их вращения больше, то центробежные силы, отрывающие профильную часть лопатки, могут возрасти настолько, что лопатка оторвется. Поэтому с увеличением мощности сначала переходят на двухпоточный ЦНД, а затем увеличивают их число. Конденсационные турбины можно выполнить одноцилиндровыми вплоть до мощности 50—60 МВт, двухцилиндровыми — до 100—150 МВт, трехцилиндровыми — до 300 МВт, четырехцилиндровыми — до 500 МВт, пятицилиндровыми — вплоть до 1300 МВт.
По частоте вращения турбины делятся на быстроходные и тихоходные. Быстроходные турбины имеют частоту вращения 3000 об/мин = 50 об/с. Они приводят электрогенератор, ротор которого имеет два магнитных полюса, и поэтому частота вырабатываемого им тока равна 50 Гц. На эту частоту строят большинство паровых турбин для ТЭС, ТЭЦ и частично для АЭС в нашей стране и почти во всем мире. В Северной Америке и на части территории Японии быстроходные турбины строят на частоту вращения 3600 об/мин = 60 об/с, так как там принятая частота сети равна 60 Гц.
Ранее в говорилось о том, что поскольку из-за низких начальных параметров работоспособность пара в турбинах АЭС мала, а снижение капитальных затрат требует увеличения мощности, т.е. массы пропускаемого пара, то объемный расход на выходе из турбины оказывается столь значительным, что оказывается целесообразным переход на меньшую частоту вращения. Так как число магнитных полюсов в электрогенераторе должно быть целым и четным, то переход на использование четырехполюсного электрогенератора и получения той же частоты сети, что и при двухполюсном электрогенераторе, требует снижения частоты вдвое. Таким образом, тихоходные турбины в нашей стране имеют частоту вращения 1500 об/мин = 25 об/с.
Рис.10 Тихоходная турбина насыщенного пара мощностью 1160 МВт для американской АЭС
На рис. 10 показана тихоходная атомная турбина фирмы ABB мощностью 1160 МВт на частоту вращения 30 об/с. Гигантские размеры турбины хорошо видны в сравнении с фигурой человека, стоящего у средней опоры ее валопровода. Турбина не имеет ЦСД, и пар из ЦВД направляется в два горизонтальных сепаратора-пароперегревателя (СПП), а из них — раздается на три двухпоточных ЦНД. По такой же схеме на частоту вращения 25 об/с построены энергоблоки мощностью 1000 МВт на Балаковской и Ростовской АЭС.
Для АЭС, построенных для теплых климатических условий, т.е. для высокой температуры охлаждающей воды и соответственно высокого давления в конденсаторе), можно строить и быстроходные атомные турбины (рис. 11). Пар к ЦВД турбины поступает из реакторного отделения по четырем паропроводам 11. Пройдя ЦВД, пар поступает к СПП 10 вертикального типа, а после них с помощью ресивера 3 раздается на три одинаковых двухпоточных ЦНД 4. Под каждым ЦНД установлен свой конденсатор, также хорошо видный на макете.
По числу валопроводов различают турбины одновальные (имеющие один валопровод — соединенные муфтами роторы отдельных цилиндров и генератора) и двухвальные(имеющие два валопровода каждый со своим генератором и связанные только потоком пара). На российских тепловых электростанциях используют только одновальные турбины.В начале 70-х годов на Славянской ГРЭС на Украине построена единственная двухвальная турбина мощностью 800 МВт, да и то потому, что в то время не было электрогенератора мощностью 800 МВт.
Рис.11 Быстроходная атомная турбина мощностью 1093 МВт для испанской АЭС (“ Трилло”), построенная фирмой Siemens
Для обозначения типов турбин ГОСТ предусматривает специальную маркировку, состоящую из буквенной и числовой частей. Буквенная часть указывает тип турбины, следующее за ней число — номинальную мощность турбины в мегаваттах. Если необходимо указать и максимальную мощность турбины, то ее значение приводят через косую черту. Следующее число указывает номинальное давление пара перед турбиной в МПа: для теплофикационных турбин далее через косую черту указывают давление в отборах или противодавление в МПа. Наконец, последняя цифра, если она имеется, указывает номер модификации турбины, принятый на заводе-изготовителе.
Приведем несколько примеров обозначений турбин.
Турбина К-210-12,8-3 — типа К, номинальной мощностью 210 МВт с начальным абсолютным давлением пара 12,8 МПа (130 кгс/см2), третьей модификации.
Трубина П-6-3,4/0,5 — типа П, номинальной мощностью 6 МВт, с начальным абсолютным давлением пара 3,4 МПа и абсолютным давлением отбираемого пара 0,5 МПа.
Турбина Т-110/120-12,8 — типа Т, номинальной мощностью 110 МВт и максимальной мощностью 120 МВт, с начальным абсолютным давлением пара 12,8 МПа.
Турбина ПТ-25/30-8,8/1 — типа ПТ, номинальной мощностью 25 МВт и максимальной мощностью 30 МВт, с начальным абсолютным давлением пара 8,8 МПа (90 ат) и абсолютным давлением отбираемого пара 1 МПа.
Турбина Р-100/105-12,8/1,45 — типа Р, номинальной мощностью 100 МВт максимальной мощностью 105 МВт, с начальным абсолютным давлением пара 12,8 МПа и абсолютным противодавлением 1,45 МПа.
Турбина ПР-12/15-8,8/1,45/0,7 — типа ПР, номинальной мощностью 12 МВт и максимальной мощностью 15 МВт, с начальным абсолютным давлением 8,8 МПа, давлением в отборе 1,45 МПа и противодавлением 0,7 МПа.
Основные технические требования к паровым турбинам и их характеристики
Для того чтобы увидеть, насколько совершенной машиной является паровая турбина, достаточно рассмотреть технические требования, предъявляемые к ней. Они сформулированы в государственных стандартах (ГОСТ). Здесь мы остановимся только на наиболее важных из них.
Прежде всего, к турбине предъявляется ряд требований, которые можно охватить одним термином — надежность. Надежность технического объекта — это его свойство выполнять заданные функции в заданном объеме при определенных условиях функционирования. Применительно к паровой турбине надежность — это бесперебойная выработка мощности при предусмотренных затратах топлива и установленной системе эксплуатации, технического обслуживания и ремонтов, а также недопущения ситуаций, опасных для людей и окружающей среды.
Важно подчеркнуть, что понятие надежности включает в себя и понятие экономичности. Бесперебойно работающая турбина, работающая с низкой экономичностью из-за износа или с ограничением мощности из-за внутренних неполадок, не может считаться надежной. Надежность — это комплексное свойство, характеризуемое такими подсвойствами, как безотказность, долговечность, ремонтопригодность, сохраняемость, управляемость, живучесть, безопасность. Не вдаваясь в строгие определения этих подсвойств, отметим главные из них.
Безотказность — это свойство турбины непрерывно сохранять работоспособное состояние в течение некоторой наработки. Средняя наработка на отказ для турбин ТЭС мощностью 500 МВт и более должна быть не менее 6250 ч, а меньшей мощности — не менее 7000 ч, а для турбин АЭС — не менее 6000 ч. Если учесть, что в календарном году 8760 ч и что какое-то время турбина не работает (например, по указанию диспетчера энергосистемы), то это означает, что отказы по вине турбины в среднем должны происходить не чаще 1 раза в год.
Полный установленный срок службы турбины ТЭС должен быть не менее 40 лет, а турбин АЭС — не менее 30 лет. При этом оговаривается два важных обстоятельства. Первое: этот срок службы не относится к быстроизнашивающимся деталям, например, рабочим лопаткам, уплотнениям, крепежным деталям. Для таких деталей важен средний срок службы до капитального ремонта (межремонтный период). В соответствии с ГОСТ он должен быть не менее 6 лет (кроме того, на ТЭС и АЭС реализуется плановая система текущих и планово-предупредительных ремонтов).
Для турбин ТЭС, а точнее для их деталей, работающих при температуре свыше 450 °С, кроме такого показателя долговечности, как срок службы, вводится другой показатель — ресурс — суммарная наработка турбины от начала эксплуатации до достижения предельного состояния. На этапе проектирования предельное состояние определяется как назначенный ресурс. По определению — это ресурс, при достижении которого эксплуатация турбины должна быть прекращена независимо от ее технического состояния. На самом деле при достижении назначенного ресурса турбина может сохранить значительную дополнительную работоспособность (остаточный ресурс) и, учитывая ее высокую стоимость, срок работы турбины продляют. Учитывая нелогичность применительно к турбине термина «назначенный ресурс», стали употреблять термин «расчетный ресурс». Таким образом, расчетный (назначенный) ресурс — это наработка турбины, которая гарантируется заводом-изготовителем; при ее достижении должен быть рассмотрен вопрос о ее дальнейшей эксплуатации.
ГОСТ не регламентирует расчетного ресурса (он должен быть установлен в технических условиях или техническом задании на ее проектирование в каждом конкретном случае). Долгие годы расчетный ресурс составлял 100 тыс. ч, сейчас — как правило, 200 тыс. ч. Важнейшим требованием к турбине является высокая экономичность. Коэффициент полезного действия турбины оценивается по КПД ее цилиндров.
Коэффициент полезного действия цилиндра характеризуется той долей работоспособности пара, которую удалось преобразовать в механическую энергию. Наивысшую экономичность имеет ЦСД: в хороших турбинах он составляет 90—94 %. Коэффициент полезного действия ЦВД и ЦНД существенно меньше и в среднем составляет 84—86 %. Это уменьшение обусловлено существенно более сложным характером течения пара в решетках очень малой (несколько десятков миллиметров в первых ступенях ЦВД) и очень большой (1 м и более) в последних ступенях ЦНД высотой решеток. Рассчитать это течение и подобрать под него профили лопаток затруднительно даже при современных вычислительных средствах. Кроме того, значительная часть проточной части ЦНД работает влажным паром, капли влаги имеют скорость существенно меньшую, чем пар, и оказывают на вращающиеся рабочие лопатки тормозящее действие.
Кроме приведенных технических требований ГОСТ содержит многочисленные другие требования, в частности, к системе защиты турбины при возникновении аварийных ситуаций, к маневренности (диапазон длительной работы — обычно 30—100 % номинальной мощности; продолжительности пуска и остановки, число возможных пусков и т.д.), к системе регулирования и управления турбиной, к ремонтопригодности и безопасности (пожаробезопасности, уровня вибрации, шума и т.д.), методов контроля параметров рабочих сред (пара, масла, конденсата), транспортирования и хранения.
Источник: Языки программирования — Life-prog
режимы работы паровой турбины
Режимы работы паротурбинной установки на примере машины Т-100-130 Уральского турбомоторного завода
Пуск турбины и холостой ход
После создания в системе регулирования ПМН давления масла 12-14 атм. золотники автомата безопасности перемещаются на верхний упор. Вращением маховика синхронизатора в сторону «Повышение» опускается букса синхронизатора. При этом напорное масло через окно в неподвижной буксе и маслопровод поступает в верхнюю камеру ЗАБ и подготовит их к возможности срабатывания в случаи воздействия на них через кнопку от руки, электромагнитом или АБ.
Одновременно с взведением ЗАБ напорное масло поступает в:
- напорный этаж блока регулирования;
- камеры дросселей настройки системы отсечных золотников сервомоторов ЧВД и ЧНД.
Из напорного этажа блока регуляторов масло через тангенциальные окна поршня золотника № 1 РС и поршня золотника РД поступает в их надпоршневые камеры и далее от надпоршневой камеры золотника № 1 РС в камеру под подвижную буксу синхронизатора (в камеру над золотником Æ 65 РС) и от надпоршневой камеры золотника РД к соплу мембранно-ленточной системы РД.
В отсечных золотниках напорное масло из камеры дросселя настройки через внутреннее сверление в золотниках поступает под поршень отсечного золотника сервомотора ЧВД и ЧНД и через его тангенциальные щели в этажи ЧВД и ЧНД блока регулирования.
При дальнейшем опускании подвижной буксы синхронизатора масло через второе окно в неподвижной буксе и маслопровод будет поступать в верхнюю камеру над отсечным золотником автозатвора, давление в камере поднимется, отсечной золотник пойдёт вниз и подаст напорное масло в камеру под поршень автозатвора, последний пойдёт вверх и откроет связанный с ним стопорный клапан.
После открытия стопорного клапана подвижная букса синхронизатора при дальнейшем опускании своей кромкой начнёт прикрывать слив из камеры над поршнем золотника № 1 РС, что приведёт к его опусканию.
Опускаясь вниз, золотник № 1 РС уменьшит слив из этажа ЧВД блока регуляторов, связанного с камерой под поршнем отсечного золотника сервомотора ЧВД. Золотник сервомотора ЧВД пойдёт вверх и подаст напорное масло под поршень сервомотора ЧВД. Подъём поршня сервомотора ЧВД вызовет открытие регулирующих клапанов ЦВД турбины. Вместе с поршнем сервомотора ЧВД поднимется вверх конус обратной связи, при этом он уменьшит подвод масла под золотник сервомотора, последний займёт отсечное положение и сервомотор остановиться.
Если пуск турбины осуществляется на «скользящих» параметрах пара или байпасом ГПЗ, при высокой температуре масла ЦВД, ТО пред пуском регулирующие клапана ЦВД воздействием на синхронизатор в сторону «Повышение» открываются полностью.
После толчка ротора турбины и достижения им 2700 об/мин в работу вступает импеллер и регулятор скорости.
По мере подъёма оборотов, давление масла на мембрану регулятора скорости увеличивается, мембрана прогибается, а связанная с ней лента отходит от сопла, при этом увеличивается слив масла через него. Увеличение слива ведёт к нарушению равновесного состояния поршня золотника Æ 65 РС. Поршень идёт вниз и увеличением подвода масла через тангенциальные щели компенсирует изменение слива в сопле, восстанавливая первоначальное давление в камере под поршнем. Одновременно золотник Æ 65, опускаясь вниз увеличивает слив из камеры под поршнем № 1 РС. это вызывает подъём золотника № 1 РС, увеличение слива из этажа ЦВД блока регуляторов, опускание сервомотора ЧВД, прикрытие регулирующих клапанов до установления пропуска пара на турбину, соответствующего холостому ходу (сервомотор ЧВД отключен от регуляторов, регулирующие диафрагмы открыты).
Дальнейший подъём оборотов (от 2700 до 3000) производится вращением маховичка синхронизатора в сторону «Повышение». При этом опускаясь вниз, букса синхронизатора уменьшит слив из камеры над поршнем золотника № 1 РС. Золотник пойдёт вниз и прикроет слив масла из этажа ЧВД, что вызовет подъём сервомотора ЧВД и увеличение пропуска пара в турбину.
Появляется избыточная мощность, число оборотов турбины возрастает, слив масла через сопло мембранно-ленточной системы увеличивается. Золотник Æ 65 РС при этом пойдёт вниз и скомпенсирует уменьшение слива буксой синхронизатора из камеры под поршнем золотника № 1 РС. Золотник № 1 РС поднимаясь, займёт своё первоначальное положение относительно окон в этажах блока регуляторов.
Работа на конденсационном режиме без отборов пара
При этом режиме работы турбины РД отопительных отборов включён (синхронизатор РД установлен в нулевое положение по шкале). Управляемый синхронизатором РД, конус в этом случае открывает максимальный слив из камеры под поршнем золотника РД, а переключатель отсекает сервомотор ЧНД от этажа блока регуляторов. Золотник РД и сервомотор ЧНД находится на верхних упорах.
Изменение электрической нагрузки при работе ТГ в сеть производится воздействием на синхронизатор РС.
При одиночной работе ТГ изменение эл. нагрузки производится отключением или подключением потребителей.
Число оборотов турбины при этом автоматически поддерживается почти постоянным, некоторая корректировка числа оборотов при изменении нагрузки производится синхронизатором РС.
Воздействием на синхронизатор РС, подвижная букса в зависимости от направления вращения маховичка изменяет своё положение, что влечёт за собой соответствующее перемещение золотника РС, а следовательно и золотника № 1 РС, вследствии чего уменьшается или увеличивается слив из этажа ЧВД блока регулятора.
Изменение давления в этаже ЧВД нарушает равновесное состояние отсечного золотника сервомотора ЧВД, золотник, перемещаясь, вызывает соответственно движение сервомотора на открытие регулирующих клапанов ЦВД. Конус обратной связи, связанный со штоком сервомотора ЧВД, при своём движении изменяет подвод масла к камере под поршнем отсечного золотника, что обеспечивает установку золотника в первоначальное положение при каком-то новом положении регулирующих клапанов, соответствующем изменённой нагрузки турбины.
В случаи необходимости ограничения мощности достигается установкой шайбы ограничителя в положение, когда золотник № 1 РС не может спускаться ниже для набора нагрузки сверх установленной величины.
Работа на конденсационном режиме с отбором пара
Для перевода турбины на режим с отбором пара необходимо произвести подключение паровой импульсной линии соответствующего отбора к мембране мембранно-ленточной системы РД и включить в работу РД.
Включение производится воздействием маховичка на синхронизатор РД в сторону «Повышение». При этом перемещение конуса, жёстко связанного с соплом мембранно-ленточной системы РД, вызовет уменьшение слива масла из камеры над поршнем золотника РД. Перемещаясь, конус воздействует на золотник переключателя РД, который подключает импульсную линию отсечного золотника сервомотора ЧНД с этажом блока регуляторов.
Хода золотников подобраны как переключателя и конуса, что сперва камера над поршнем отсечного золотника сервомотора ЧНД соединяется с этажом ЧНД, а затем создаётся необходимое давление масла в камере над поршнем золотника РД. Конус следует перемещать до тех пор, пока золотник РД не стронется с верхнего упора. При этом давление в камере над поршнем золотника РД должно быть 6-8 атм, что будет означать включение регулятора давления в работу.
При этом режиме возможны следующие варианты работы системы регулирования:
- при изменении эл. нагрузки и неизменной тепловой нагрузки;
- при неизменной тепловой нагрузки и неизменной электрической;
- при одновременном изменении эл. и тепловой нагрузок.
При снижении эл. нагрузки (при работе на индивидуального потребителя) число оборотов ротора турбины возрастёт, соответственно увеличится давление масла импеллера, заставляя сильнее прогнуться мембрану и ленту РС, что вызовет слив масла из сопла РС, золотник РС Æ 65 пойдёт вниз, увеличиться расход масла из камеры над поршнем золотника № 1 РС, через тангенциальные окна своего поршня компенсирует изменение слива в сопле. при этом золотник № 1 РС поднимается вверх и увеличивает открытие сливных окон из этажей ЧВД и ЧНД блока регуляторов, связанных с камерами над отсечными золотниками соответствующих сервомоторов. Последние опускаясь вниз, прикрывают регулирующие клапаны и регулирующие диафрагмы. Расход пара через турбину и её мощность уменьшится при почти неизменном расходе пара в отбор. При работе ТГ в общую сеть, изменение эл. нагрузки производится синхронизатором (его подвижной буксой) с воздействием непосредственно на золотник № 1 РС.
Увеличение расхода пара в отбор вызывает снижение давление пара в камере отбора и в камере мембраны РД. При чём прогибы мембраны и ленты уменьшатся, прикрыв слив из сопла РД, золотник РД пойдёт вниз. перемещение золотника РД при этом увеличит слив из этажа ЧНД, что вызовет движение сервомотора ЧНД на прикрытие регулирующих диафрагм. Расход пара в отбор увеличится, эл. нагрузка изменится. При уменьшении расхода пара в отбор действие элементов системы регулирования происходит в обратном порядке.
При одновременном изменении эл. и тепловой нагрузок оба процесса протекают одновременно под действием регулятора скорости и регулятора давления.
Перевод турбины на режим работы по тепловому графику
Для перевода с режима с включённым отбором пара на режим работы по тепловому графику необходимо полностью закрыть регулирующие диафрагмы увеличением тепловой нагрузки или снижением эл. нагрузки. При этом должен загореться сигнал «Сервомотор ЧНД на упоре».
После этого ввести переключатель работы по тепловому графику дистанционно или вручную, перемещая его на верхний упор, одновременно выводя синхронизатор РС на «Убавить».
При введении золотника переключателя:
- Этаж ЧНД сообщается со сливом, что препятствует открытию сервомотора ЧНД, а следовательно поворотных диафрагм;
- Подключается дополнительный этаж ЧВД блока регуляторов, что усиливает воздействие регулятора давления на сервомотор ЧВД.
Открытие слива из этажа ЧВД дополнительно компенсируется подводом масла из напорного этажа через сверление в золотнике переключателя. Далее воздействуя на синхронизатор РС, вывести его в положение 15-20% нагрузки, поддерживая при этом давление в отборе неизменным с помощью регулятора давления.
В случае колебаний частоты сети, вызывающих изменение нагрузки, разрешается ввести ограничитель мощности, для чего с момента появления светового сигнала «работа на ограничителе мощности» ограничителем снять нагрузку 5-8 МВт.
Эта операция необходима для того, чтобы при нормальной работе РС был включён, а при сбросе нагрузки и повышении числа оборотов вступил в работу и закрывал регулирующие клапана.
В режиме противодавления увеличение тепловой нагрузки ведёт к падению давления пара в отборе и в камере мембраны регулятора давления. Изменение прогиба мембраны и жёстко связанной с ней ленты уменьшает слив масла через сопло регулятора из камеры над поршнем золотника РД. Золотник пойдёт вниз. При этом уменьшится слив масла из этажа ЧВД дополнительного соединения с камерой над поршнем отсечного золотника сервомотора. давление в этой камере увеличится, отсечной золотник поднимется вверх и переставит сервомотор, а следовательно и регулирующие клапана в новое положение, соответствующее увеличившейся тепловой нагрузке. При уменьшении тепловой нагрузки действие регулирования происходит в обратном порядке.
(Visited 4 361 times, 1 visits today)